Introduction to Aluminum PCB
Printed Circuit Boards (PCBs) are an essential component in modern electronics, providing a platform for electrical components to be mounted and connected. Traditionally, PCBs are made using a substrate material such as FR-4, which is a glass-reinforced epoxy laminate. However, in recent years, aluminum has emerged as an alternative substrate material for PCBs, offering unique properties and advantages over traditional materials.
Aluminum PCBs, also known as Metal Core PCBs (MCPCBs), are a type of PCB that uses an aluminum alloy as the base material instead of the more common FR-4. The aluminum base provides excellent thermal conductivity, making it ideal for applications that generate significant amounts of heat, such as high-power LEDs, power electronics, and automotive systems.
Advantages of Aluminum PCB
-
Enhanced Thermal Management: Aluminum has a high thermal conductivity, which allows it to efficiently dissipate heat away from electronic components. This property is particularly useful in applications that generate a lot of heat, as it helps to prevent components from overheating and failing prematurely.
-
Improved Mechanical Stability: Aluminum PCBs offer superior mechanical stability compared to traditional FR-4 PCBs. The aluminum base provides a rigid and sturdy foundation, reducing the risk of board warpage and improving the overall durability of the PCB.
-
Lightweight and Compact: Aluminum PCBs are often thinner and lighter than their FR-4 counterparts, making them suitable for applications where weight and space are critical factors, such as in aerospace and portable electronics.
-
Cost-Effective: While aluminum PCBs may have a higher initial cost compared to FR-4 PCBs, they can be more cost-effective in the long run. The enhanced thermal management and improved durability of aluminum PCBs can lead to longer product lifetimes and reduced maintenance costs.
Structure of Aluminum PCB
An aluminum PCB typically consists of three main layers: the aluminum base, a dielectric layer, and a copper circuit layer.
Aluminum Base Layer
The aluminum base layer serves as the foundation of the PCB and provides the primary thermal management properties. The most commonly used aluminum alloys for PCBs are 5052 and 6061, which offer a good balance of thermal conductivity, mechanical strength, and corrosion resistance.
The thickness of the aluminum base layer can vary depending on the specific application and thermal requirements. Typical thicknesses range from 0.8mm to 3.2mm, with thicker bases providing better thermal dissipation but also increasing the overall weight and size of the PCB.
Dielectric Layer
The dielectric layer is a thin, electrically insulating material that separates the aluminum base from the copper circuit layer. Its primary purpose is to prevent electrical shorts between the conductive layers while allowing efficient heat transfer from the copper to the aluminum.
Common dielectric materials used in aluminum PCBs include:
-
Epoxy Resin: A polymer material that offers good electrical insulation and thermal conductivity. It is often used in combination with ceramic fillers to enhance its thermal properties.
-
Polyimide: A high-performance polymer known for its excellent thermal stability, mechanical strength, and electrical insulation properties. Polyimide is often used in applications that require high reliability and durability.
-
Ceramic: Ceramic materials, such as alumina or beryllia, offer excellent thermal conductivity and electrical insulation. However, they are more brittle and expensive compared to polymer-based dielectrics.
The dielectric layer is typically applied to the aluminum base using a lamination process, which involves high temperature and pressure to ensure a strong bond between the layers.
Copper Circuit Layer
The copper circuit layer is where the actual electronic circuits are formed. It is made of a thin layer of copper foil that is laminated onto the dielectric layer. The copper foil is then etched to create the desired circuit patterns, which can include traces, pads, and vias.
The thickness of the copper foil can vary depending on the current carrying requirements of the circuit. Common thicknesses range from 0.5oz to 4oz (17μm to 140μm), with thicker foils providing higher current carrying capacity but also increasing the overall thickness of the PCB.
Layer | Material | Thickness Range |
---|---|---|
Aluminum Base | 5052, 6061 Aluminum Alloy | 0.8mm – 3.2mm |
Dielectric | Epoxy Resin, Polyimide, Ceramic | 50μm – 200μm |
Copper Circuit | Copper Foil | 17μm – 140μm (0.5oz – 4oz) |
Heat Conductivity of Aluminum PCB
One of the main advantages of aluminum PCBs is their excellent thermal conductivity, which allows them to efficiently dissipate heat away from electronic components. The thermal conductivity of an aluminum PCB depends on several factors, including the aluminum alloy used, the thickness of the base layer, and the properties of the dielectric material.
Thermal Conductivity of Aluminum Alloys
The thermal conductivity of aluminum alloys used in PCBs can vary depending on their composition and manufacturing process. The most common aluminum alloys used in PCBs are:
-
5052 Aluminum Alloy: This alloy has a thermal conductivity of around 138 W/mK (Watts per meter-Kelvin), which is about 60% that of pure aluminum. It offers a good balance of thermal conductivity, mechanical strength, and corrosion resistance.
-
6061 Aluminum Alloy: This alloy has a slightly higher thermal conductivity than 5052, at around 167 W/mK. It also offers excellent mechanical properties and corrosion resistance, making it a popular choice for high-performance applications.
For comparison, the thermal conductivity of FR-4, the most common material used in traditional PCBs, is only around 0.3 W/mK, which is about 460 times lower than 5052 aluminum alloy.
Effect of Base Layer Thickness on Thermal Conductivity
The thickness of the aluminum base layer can have a significant impact on the overall thermal conductivity of the PCB. Thicker base layers provide more cross-sectional area for heat to flow through, resulting in better thermal dissipation.
However, increasing the base layer thickness also increases the overall weight and size of the PCB, which may not be desirable in certain applications. Therefore, the optimal base layer thickness should be determined based on the specific thermal requirements and design constraints of the application.
Thermal Conductivity of Dielectric Materials
The dielectric layer in an aluminum PCB also plays a role in its thermal conductivity. While the primary purpose of the dielectric is to provide electrical insulation, it also acts as a thermal interface between the aluminum base and the copper circuit layer.
The thermal conductivity of common dielectric materials used in aluminum PCBs are:
- Epoxy Resin: 0.2 – 2.0 W/mK (depending on the filler material and composition)
- Polyimide: 0.1 – 0.5 W/mK
- Ceramic (Alumina): 20 – 30 W/mK
- Ceramic (Beryllia): 200 – 300 W/mK
While ceramic dielectrics offer the highest thermal conductivity, they are also more expensive and brittle compared to polymer-based dielectrics. Epoxy resin with ceramic fillers is a popular choice for aluminum PCBs, as it offers a good balance of thermal conductivity, mechanical properties, and cost.
Material | Thermal Conductivity (W/mK) |
---|---|
5052 Aluminum Alloy | 138 |
6061 Aluminum Alloy | 167 |
FR-4 (Traditional PCB) | 0.3 |
Epoxy Resin (Dielectric) | 0.2 – 2.0 |
Polyimide (Dielectric) | 0.1 – 0.5 |
Alumina Ceramic (Dielectric) | 20 – 30 |
Beryllia Ceramic (Dielectric) | 200 – 300 |
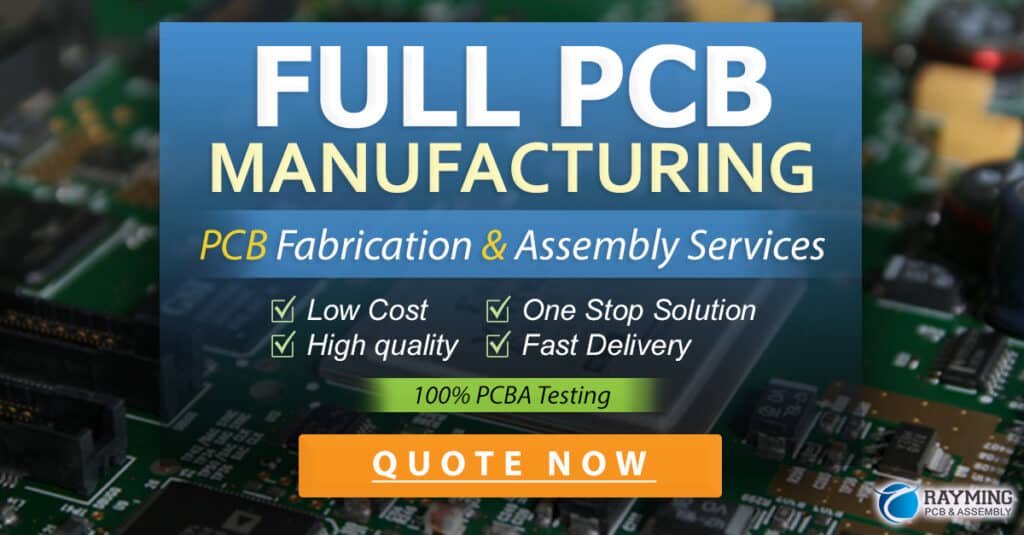
Applications of Aluminum PCB
Aluminum PCBs are used in a wide range of applications where thermal management is a critical factor. Some common applications include:
High-Power LED Lighting
High-power LEDs generate a significant amount of heat during operation, which can lead to reduced light output, color shift, and premature failure if not properly managed. Aluminum PCBs provide an efficient thermal path to dissipate heat away from the LEDs, ensuring stable performance and long lifetimes.
Power Electronics
Power electronic devices, such as motor drives, inverters, and switch-mode power supplies, often deal with high currents and voltages, which can result in substantial heat generation. Aluminum PCBs help to effectively dissipate this heat, preventing component overheating and improving system reliability.
Automotive Electronics
The harsh environment in automotive applications, combined with the increasing use of high-power electronic systems, makes thermal management a critical challenge. Aluminum PCBs are used in various automotive applications, such as LED headlights, engine control units, and power converters, to ensure reliable operation under demanding conditions.
Aerospace and Defense
In aerospace and defense applications, weight and space are often at a premium, while reliability is of utmost importance. Aluminum PCBs offer a lightweight and compact solution for thermal management, making them suitable for use in avionics, radar systems, and satellite electronics.
Medical Devices
Medical devices, such as imaging equipment and surgical instruments, often require compact and reliable electronics that can operate in sensitive environments. Aluminum PCBs provide efficient thermal management in a small form factor, ensuring the stable performance of medical devices.
Frequently Asked Questions (FAQ)
1. What is the difference between an aluminum PCB and a traditional FR-4 PCB?
The main difference between an aluminum PCB and a traditional FR-4 PCB is the base material. Aluminum PCBs use an aluminum alloy as the base, while FR-4 PCBs use a glass-reinforced epoxy laminate. The aluminum base provides significantly higher thermal conductivity compared to FR-4, making aluminum PCBs better suited for applications that require efficient heat dissipation.
2. Can aluminum PCBs be used for high-frequency applications?
Aluminum PCBs can be used for high-frequency applications, but they may require special design considerations. The aluminum base can act as a ground plane, which can affect the impedance and signal integrity of high-frequency circuits. Proper layout techniques, such as the use of ground planes and controlled impedance traces, can help to mitigate these issues.
3. Are aluminum PCBs more expensive than traditional PCBs?
Aluminum PCBs can be more expensive than traditional FR-4 PCBs due to the higher cost of the aluminum base material and the specialized manufacturing processes required. However, the improved thermal management and durability of aluminum PCBs can lead to cost savings in the long run, particularly in applications where reliability and longevity are critical factors.
4. How are components mounted on aluminum PCBs?
Components can be mounted on aluminum PCBs using standard surface mount (SMT) or through-hole (THT) techniques. However, special consideration must be given to the thermal expansion mismatch between the components and the aluminum base. Thermal interface materials, such as Thermal Adhesives or thermal pads, are often used to improve heat transfer and reduce mechanical stress on the components.
5. Can aluminum PCBs be recycled?
Yes, aluminum PCBs can be recycled. The aluminum base can be easily separated from the other materials and recycled using standard aluminum recycling processes. The copper and other metals in the circuit layer can also be recovered and recycled. Recycling aluminum PCBs helps to reduce electronic waste and conserve valuable resources.
Conclusion
Aluminum PCBs offer a unique solution for applications that require efficient thermal management and reliable performance in demanding environments. By leveraging the high thermal conductivity of aluminum alloys, these PCBs can effectively dissipate heat away from electronic components, ensuring stable operation and extended lifetimes.
The structure of an aluminum PCB, consisting of an aluminum base, dielectric layer, and copper circuit layer, provides a robust and lightweight platform for electronic circuits. The choice of materials and thicknesses can be optimized based on the specific thermal and mechanical requirements of the application.
As electronic systems continue to push the boundaries of power density and performance, aluminum PCBs are likely to play an increasingly important role in enabling the next generation of technologies. From high-power LEDs and power electronics to automotive and aerospace systems, aluminum PCBs offer a reliable and efficient solution for managing thermal challenges in a wide range of applications.
No responses yet