Introduction to Metal Core PCB
A Metal Core PCB (MCPCB) is a type of printed circuit board that uses a metal substrate instead of the traditional FR-4 material. The metal substrate, usually aluminum, provides excellent thermal conductivity, allowing for efficient heat dissipation from the components mounted on the PCB. This makes MCPCBs ideal for applications that generate a significant amount of heat, such as high-power LEDs, power electronics, and automotive systems.
Advantages of Metal Core PCBs
- Enhanced thermal management
- Improved reliability and longevity
- Reduced size and weight
- Better mechanical stability
- Increased power density
Structure of a Metal Core PCB
A typical Metal Core PCB consists of three main layers:
- Dielectric layer
- Metal substrate (core)
- Copper circuit layer
Dielectric Layer
The dielectric layer is an electrically insulating material that separates the copper circuit layer from the metal substrate. It is typically made of a thermally conductive material, such as aluminum oxide or boron nitride, to ensure efficient heat transfer from the copper layer to the metal core.
Metal Substrate (Core)
The metal substrate, or core, is the main component of an MCPCB. It is usually made of aluminum, which offers excellent thermal conductivity, mechanical stability, and lightweight properties. Other metals, such as copper or steel, can also be used depending on the specific application requirements.
Copper Circuit Layer
The copper circuit layer is where the electronic components are mounted and interconnected. It is similar to the copper layer in a standard PCB, but it is thermally connected to the metal substrate through the dielectric layer. This allows heat generated by the components to be efficiently transferred to the metal core for dissipation.
Thermal Management with Metal Core PCBs
One of the primary reasons for using Metal Core PCBs is their superior thermal management capabilities. The metal substrate acts as a heat sink, quickly absorbing and spreading heat generated by the components on the PCB. This helps to maintain a lower operating temperature, which enhances the performance, reliability, and lifespan of the electronic devices.
Thermal Conductivity Comparison
Material | Thermal Conductivity (W/mK) |
---|---|
Aluminum | 205 – 250 |
Copper | 385 – 400 |
FR-4 | 0.3 – 0.4 |
As seen in the table above, aluminum and copper have significantly higher thermal conductivity compared to FR-4, the standard material used in traditional PCBs. This makes MCPCBs much more effective at dissipating heat.
Thermal Design Considerations
When designing a Metal Core PCB, several factors must be considered to optimize thermal performance:
- Dielectric layer thickness and material
- Metal substrate thickness and type
- Copper layer thickness and layout
- Component placement and power density
- External cooling methods (e.g., heatsinks, fans)
By carefully selecting materials and designing the PCB layout with thermal management in mind, engineers can create highly efficient and reliable electronic systems using Metal Core PCBs.
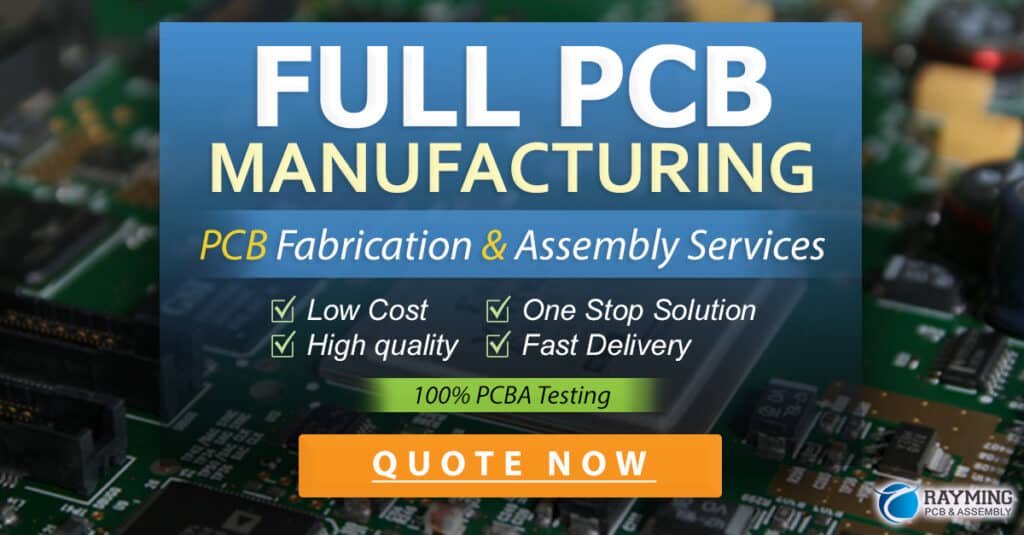
Applications of Metal Core PCBs
Metal Core PCBs find applications in various industries where thermal management is crucial. Some common applications include:
High-Power LED Lighting
MCPCBs are extensively used in high-power LED lighting systems, such as street lights, stadium lights, and automotive headlights. The metal core effectively dissipates heat generated by the LEDs, ensuring optimal performance and longer lifespan.
Power Electronics
Power electronic devices, such as motor drives, inverters, and power supplies, generate significant amounts of heat due to high current flow. MCPCBs help to manage this heat, preventing component failure and improving system reliability.
Automotive Electronics
In the automotive industry, MCPCBs are used in various applications, such as engine control units, LED headlights, and power steering systems. The metal core provides the necessary thermal management and mechanical stability to withstand the harsh operating conditions in vehicles.
Telecommunications
High-power RF amplifiers and base station equipment in the telecommunications industry rely on MCPCBs for efficient heat dissipation. This ensures stable operation and prevents signal degradation due to excessive heat.
Manufacturing Process of Metal Core PCBs
The manufacturing process of Metal Core PCBs differs slightly from that of standard PCBs due to the presence of the metal substrate. The main steps involved are:
- Substrate preparation
- Dielectric layer application
- Copper foil lamination
- Circuit pattern imaging and etching
- Soldermask and silkscreen application
- Surface finish application
- Drilling and routing
- Electrical testing and inspection
Substrate Preparation
The metal substrate, usually aluminum, is cleaned and treated to ensure good adhesion with the dielectric layer. This may involve surface roughening, anodizing, or applying a special coating.
Dielectric Layer Application
The dielectric layer is applied to the metal substrate using various methods, such as screen printing, roller coating, or lamination. The thickness and uniformity of the dielectric layer are critical for optimal thermal performance.
Copper Foil Lamination
A thin copper foil is laminated onto the dielectric layer using heat and pressure. The copper foil thickness can vary depending on the application requirements.
Circuit Pattern Imaging and Etching
The desired circuit pattern is transferred onto the copper foil using photolithography. The unwanted copper is then etched away, leaving the circuit pattern on the dielectric layer.
Soldermask and Silkscreen Application
A soldermask is applied to protect the copper traces from oxidation and prevent solder bridges during assembly. A silkscreen layer is added for component labeling and identification.
Surface Finish Application
A surface finish, such as HASL, ENIG, or OSP, is applied to the exposed copper areas to prevent oxidation and improve solderability.
Drilling and Routing
Holes are drilled through the MCPCB for component mounting and interconnections. The board is then routed to the desired shape and size.
Electrical Testing and Inspection
The finished MCPCB undergoes electrical testing and visual inspection to ensure proper functionality and quality before being shipped to the customer.
Challenges and Limitations of Metal Core PCBs
While Metal Core PCBs offer numerous benefits, there are some challenges and limitations to consider:
- Higher material and manufacturing costs compared to standard PCBs
- Limited design flexibility due to the presence of the metal substrate
- Potential for thermal expansion mismatch between the metal core and components
- Difficulty in achieving fine-pitch component placement and routing
- Limited availability of specialized materials and manufacturing processes
Despite these challenges, the advantages of MCPCBs in terms of thermal management and reliability often outweigh the drawbacks in applications where heat dissipation is a critical factor.
Future Trends in Metal Core PCB Technology
As electronic devices continue to become more powerful and compact, the demand for efficient thermal management solutions like Metal Core PCBs will continue to grow. Some future trends in MCPCB technology include:
- Development of advanced dielectric materials with higher thermal conductivity
- Adoption of newer metal substrates, such as copper or aluminum alloys
- Integration of embedded components and active cooling solutions
- Increased use of 3D printing technologies for rapid prototyping and customization
- Expansion into new application areas, such as renewable energy and aerospace
By staying at the forefront of these trends, manufacturers and designers can leverage the benefits of Metal Core PCBs to create innovative and high-performance electronic systems.
Frequently Asked Questions (FAQ)
-
What is the difference between a Metal Core PCB and a standard PCB?
A Metal Core PCB uses a metal substrate, usually aluminum, instead of the traditional FR-4 material used in standard PCBs. This metal core provides better thermal conductivity, allowing for more efficient heat dissipation from the components mounted on the PCB. -
What are the main advantages of using a Metal Core PCB?
The main advantages of using a Metal Core PCB include enhanced thermal management, improved reliability and longevity, reduced size and weight, better mechanical stability, and increased power density. -
What industries commonly use Metal Core PCBs?
Metal Core PCBs are commonly used in industries where thermal management is crucial, such as high-power LED lighting, power electronics, automotive electronics, and telecommunications. -
How does the manufacturing process of a Metal Core PCB differ from that of a standard PCB?
The manufacturing process of a Metal Core PCB involves additional steps, such as substrate preparation, dielectric layer application, and copper foil lamination, to accommodate the metal core. The etching, drilling, and finishing processes are similar to those used for standard PCBs. -
What are some challenges and limitations of using Metal Core PCBs?
Some challenges and limitations of using Metal Core PCBs include higher material and manufacturing costs, limited design flexibility, potential for thermal expansion mismatch, difficulty in achieving fine-pitch component placement and routing, and limited availability of specialized materials and manufacturing processes.
Conclusion
Metal Core PCBs have emerged as a critical solution for thermal management in modern electronic systems. By leveraging the high thermal conductivity of metal substrates, MCPCBs enable efficient heat dissipation, improved reliability, and increased power density. As electronic devices continue to push the boundaries of performance and miniaturization, the demand for advanced thermal management solutions like Metal Core PCBs will only continue to grow.
While there are challenges and limitations to consider when using MCPCBs, the benefits they offer in terms of thermal performance and system reliability often justify their use in applications where heat dissipation is a primary concern. As new materials, manufacturing processes, and design techniques are developed, Metal Core PCBs will likely play an increasingly important role in shaping the future of electronics across various industries.
No responses yet