What is Thermal Adhesive?
Thermal adhesive, also known as thermal bonding adhesive or thermal interface material (TIM), is a specialized type of adhesive designed to facilitate efficient heat transfer between electronic components and heat sinks or other cooling solutions. These adhesives are formulated to provide excellent thermal conductivity while maintaining strong adhesive properties.
Key Properties of Thermal Adhesives
-
Thermal Conductivity: Thermal adhesives possess high thermal conductivity, allowing them to effectively transfer heat from the electronic component to the heat sink. The thermal conductivity is measured in watts per meter-kelvin (W/mK), and higher values indicate better heat transfer capabilities.
-
Adhesive Strength: Thermal adhesives must exhibit strong adhesive properties to ensure a secure bond between the electronic component and the heat sink. The adhesive strength is critical for maintaining the integrity of the assembly and preventing detachment under various environmental conditions.
-
Electrical Insulation: In many applications, thermal adhesives need to provide electrical insulation to prevent short circuits or electrical interference. Some thermal adhesives are formulated with electrically insulating materials to offer both thermal conductivity and electrical insulation simultaneously.
-
Temperature Stability: Electronic devices often operate in a wide range of temperatures, and thermal adhesives must maintain their properties and performance across this temperature range. Thermal adhesives with good temperature stability ensure reliable performance even in extreme conditions.
Applications of Thermal Adhesives
Thermal adhesives find extensive use in various electronic applications, including:
-
Power Electronics: In power electronic devices, such as power converters, inverters, and motor drives, thermal adhesives are used to attach power semiconductor devices (e.g., MOSFETs, IGBTs) to heat sinks for efficient heat dissipation.
-
Automotive Electronics: Thermal adhesives are employed in automotive electronic systems, including engine control units (ECUs), power modules, and sensors, to ensure reliable operation in harsh automotive environments.
-
Consumer Electronics: Thermal adhesives are used in consumer electronic devices, such as smartphones, tablets, and laptops, to dissipate heat generated by processors, graphics chips, and other high-performance components.
-
LED Lighting: In LED lighting applications, thermal adhesives play a crucial role in transferring heat from the LED package to the heat sink, ensuring optimal thermal management and prolonging the lifespan of the LED.
-
Telecommunications: Thermal adhesives are utilized in telecommunications equipment, such as base stations, routers, and switches, to maintain proper cooling and prevent overheating of critical components.
Types of Thermal Adhesives
Thermal adhesives can be categorized based on their composition and curing mechanism. Let’s explore some common types of thermal adhesives:
Epoxy-Based Thermal Adhesives
Epoxy-based thermal adhesives are widely used due to their excellent adhesion, high thermal conductivity, and good chemical resistance. They consist of an epoxy resin and a hardener, which react to form a strong and durable bond. Epoxy thermal adhesives can be filled with thermally conductive materials, such as aluminum oxide, boron nitride, or silver, to enhance their thermal conductivity.
Silicone-Based Thermal Adhesives
Silicone-based thermal adhesives offer excellent flexibility, temperature stability, and moisture resistance. They are commonly used in applications where the electronic components are subjected to thermal cycling or mechanical stress. Silicone thermal adhesives can be filled with thermally conductive particles to improve their thermal performance.
Acrylic-Based Thermal Adhesives
Acrylic-based thermal adhesives provide good adhesion, fast curing, and easy dispensing. They are often used in applications where quick assembly and high throughput are required. Acrylic thermal adhesives can be formulated with thermally conductive fillers to achieve the desired thermal conductivity.
Polyurethane-Based Thermal Adhesives
Polyurethane-based thermal adhesives offer a balance of good adhesion, flexibility, and thermal conductivity. They are suitable for applications where the electronic components experience moderate thermal and mechanical stresses. Polyurethane thermal adhesives can be filled with thermally conductive materials to enhance their thermal performance.
Phase Change Materials (PCMs)
Phase change materials (PCMs) are a special class of thermal interface materials that change from a solid to a liquid state at a specific temperature. They are designed to fill the microscopic gaps and irregularities between the electronic component and the heat sink, providing excellent thermal contact. PCMs offer low thermal resistance and good wetting properties, making them suitable for applications with high heat flux densities.
Selecting the Right Thermal Adhesive
Choosing the appropriate thermal adhesive for a specific application requires careful consideration of several factors:
-
Thermal Conductivity: Select a thermal adhesive with a thermal conductivity that meets the heat dissipation requirements of the electronic component. Higher thermal conductivity is generally preferred for applications with high heat generation.
-
Adhesive Strength: Consider the required adhesive strength based on the environmental conditions and mechanical stresses the Electronic Assembly will encounter. Ensure that the thermal adhesive provides sufficient adhesion to maintain the integrity of the bond.
-
Operating Temperature Range: Choose a thermal adhesive that can withstand the expected operating temperature range of the electronic device. The adhesive should maintain its properties and performance across the specified temperature range.
-
Electrical Insulation: If electrical insulation is required, select a thermal adhesive that offers both thermal conductivity and electrical insulation. Some thermal adhesives are specifically formulated to provide this combination of properties.
-
Curing Mechanism: Consider the curing mechanism of the thermal adhesive based on the manufacturing process and assembly requirements. Some adhesives require heat curing, while others can cure at room temperature or with exposure to UV light.
-
Dispensing and Application: Evaluate the dispensing and application methods compatible with the chosen thermal adhesive. Some adhesives are suitable for automated dispensing, while others may require manual application. Consider the viscosity, pot life, and working time of the adhesive.
-
Reworkability: In some cases, the ability to rework or remove the thermal adhesive may be important. Consider the reworkability of the adhesive if there is a possibility of component replacement or repair in the future.
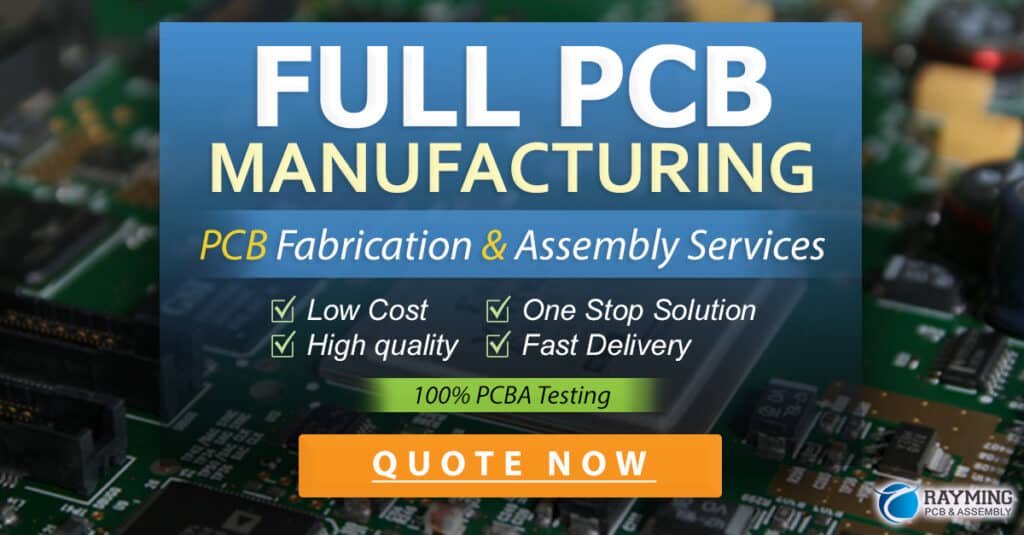
Best Practices for Using Thermal Adhesives
To ensure optimal performance and reliability when using thermal adhesives, follow these best practices:
-
Surface Preparation: Clean and degrease the surfaces of the electronic component and heat sink before applying the thermal adhesive. Remove any contaminants, such as dust, oil, or oxidation, to ensure good adhesion.
-
Dispensing and Application: Use the appropriate dispensing equipment and techniques recommended by the adhesive manufacturer. Apply the adhesive evenly and in the specified thickness to achieve the desired thermal and mechanical properties.
-
Curing Process: Follow the curing instructions provided by the adhesive manufacturer. Some adhesives require elevated temperatures for curing, while others can cure at room temperature. Ensure that the curing conditions are met to achieve optimal bond strength and thermal performance.
-
Storage and Handling: Store thermal adhesives in the recommended conditions, typically in a cool and dry place. Follow the manufacturer’s guidelines for storage temperature and shelf life. Handle the adhesives with care, avoiding contamination and excessive exposure to air or moisture.
-
Quality Control: Implement quality control measures to ensure consistent application and performance of the thermal adhesive. Conduct regular inspections and testing to verify the bond strength, thermal conductivity, and other critical parameters.
Frequently Asked Questions (FAQ)
-
What is the difference between thermal adhesive and thermal grease?
Thermal adhesive is a bonding material that provides both thermal conductivity and adhesion, while thermal grease is a non-bonding thermal interface material that fills the gaps between surfaces to enhance heat transfer. -
Can thermal adhesives be used on all types of electronic components?
Thermal adhesives are suitable for most electronic components, but it’s important to consider the specific requirements of each component, such as temperature range, material compatibility, and electrical insulation needs. -
How do I choose the right thermal adhesive for my application?
When selecting a thermal adhesive, consider factors such as thermal conductivity, adhesive strength, operating temperature range, electrical insulation requirements, curing mechanism, and dispensing method. Consult with the adhesive manufacturer or a technical expert to determine the most suitable option. -
Are thermal adhesives electrically conductive?
Some thermal adhesives are formulated to be electrically insulating, while others may have some level of electrical conductivity. It’s important to choose a thermal adhesive that meets the electrical insulation requirements of the specific application. -
Can thermal adhesives be removed or reworked?
The ability to remove or rework thermal adhesives depends on the specific formulation and curing mechanism. Some adhesives may allow for rework, while others form a permanent bond. Consider the reworkability requirements of the application when selecting a thermal adhesive.
Conclusion
Thermal adhesives play a critical role in the assembly and performance of electronic devices. By providing efficient heat transfer and strong adhesion, thermal adhesives ensure the reliable operation and longevity of electronic components. Understanding the properties, types, and selection criteria of thermal adhesives is essential for engineers and manufacturers in the electronics industry.
When choosing a thermal adhesive, consider factors such as thermal conductivity, adhesive strength, operating temperature range, electrical insulation, and curing mechanism. Following best practices for surface preparation, dispensing, curing, and quality control is crucial for achieving optimal results.
As electronic devices continue to become more advanced and generate higher heat loads, the development and innovation in thermal adhesives will play a vital role in enabling effective thermal management solutions. By staying informed about the latest advancements in thermal adhesive technology, engineers and manufacturers can design and produce electronic devices that meet the ever-increasing demands for performance, reliability, and efficiency.
Property | Description |
---|---|
Thermal Conductivity | Ability to transfer heat efficiently, measured in W/mK |
Adhesive Strength | Strength of the bond between surfaces |
Electrical Insulation | Ability to prevent electrical current flow |
Temperature Stability | Maintaining properties over a wide temperature range |
Curing Mechanism | Method of curing (heat, room temperature, UV) |
Dispensing and Application | Ease of applying the adhesive evenly |
Reworkability | Ability to remove or rework the adhesive if needed |
By carefully considering these properties and following best practices, engineers and manufacturers can select the optimal thermal adhesive for their specific electronic applications, ensuring reliable performance and long-term durability.
No responses yet