What is MCPCB“>MCPCB?
MCPCB stands for Metal Core Printed Circuit Board. It is a specialized type of PCB that uses a metal substrate, typically aluminum, as the base material instead of the traditional FR-4 fiberglass. The metal core provides excellent thermal conductivity, allowing heat to be efficiently dissipated from high-power components like LEDs and power semiconductors.
Advantages of MCPCB
- Enhanced thermal management
- Improved LED performance and lifespan
- Reduced size and weight
- Increased reliability
- Cost-effective solution
MCPCB Construction
An MCPCB consists of three main layers:
-
Metal Core: The base layer is made of a metal substrate, usually aluminum, which acts as a heat sink. The thickness of the metal core can vary depending on the thermal requirements of the application.
-
Dielectric Layer: A thin layer of dielectric material is applied on top of the metal core. This layer provides electrical insulation between the metal core and the copper traces. The dielectric material is typically a polymer with high thermal conductivity and excellent electrical insulation properties.
-
Copper Layer: The copper layer is the top layer of the MCPCB, where the electrical circuit is formed. The copper traces are etched on this layer, connecting the components and providing electrical pathways.
Comparison of MCPCB and Traditional PCB
Parameter | MCPCB | Traditional PCB (FR-4) |
---|---|---|
Thermal Conductivity | High (up to 8 W/mK) | Low (0.3 – 0.4 W/mK) |
Electrical Insulation | Good | Excellent |
Mechanical Strength | High | Moderate |
Weight | Heavier due to metal core | Lighter |
Cost | Higher than traditional PCB | Lower than MCPCB |
Applications | High-power LEDs, power electronics | General-purpose electronic circuits |
Thermal Management in MCPCB
The primary purpose of using an MCPCB is to efficiently dissipate heat generated by high-power components. The metal core acts as a heat spreader, quickly transferring heat away from the heat source and distributing it evenly across the board.
Thermal Vias
To further enhance thermal performance, thermal vias are often used in MCPCBs. Thermal vias are small holes drilled through the PCB, connecting the copper layer to the metal core. These vias provide a low-resistance thermal path, allowing heat to be conducted from the components to the metal core more efficiently.
Thermal Interface Materials (TIMs)
Thermal interface materials (TIMs) are used to improve the thermal contact between the components and the MCPCB. TIMs fill the air gaps and irregularities between the mating surfaces, reducing thermal resistance and enhancing heat transfer. Common TIMs used in MCPCBs include thermal greases, thermal pads, and phase change materials.
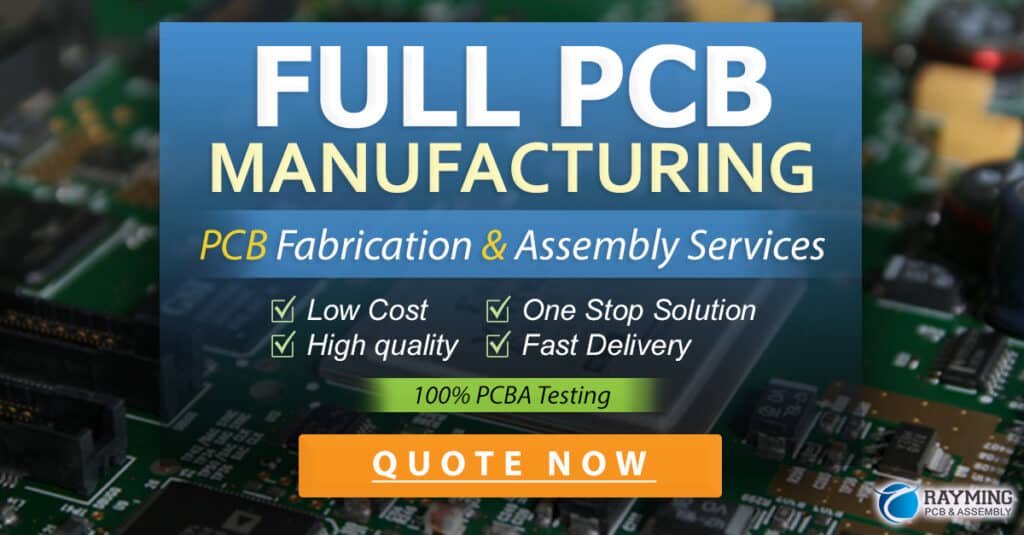
MCPCB Design Considerations
When designing an MCPCB, several factors need to be considered to ensure optimal performance and reliability.
Dielectric Layer Thickness
The thickness of the dielectric layer plays a crucial role in the thermal performance of the MCPCB. A thinner dielectric layer offers better thermal conductivity but may compromise electrical insulation. On the other hand, a thicker dielectric layer provides better electrical insulation but may hinder heat transfer. The appropriate thickness should be chosen based on the specific requirements of the application.
Copper Thickness
The thickness of the copper layer affects the current-carrying capacity and the thermal performance of the MCPCB. Thicker copper traces can handle higher currents and provide better heat spreading. However, increasing the copper thickness also increases the overall cost of the MCPCB.
Thermal Vias Placement
The placement and density of thermal vias are critical for effective heat dissipation. Thermal vias should be strategically placed near the heat-generating components to provide the shortest thermal path to the metal core. The number and size of thermal vias should be optimized based on the thermal requirements and the available board space.
Component Placement
Proper component placement is essential for optimal thermal management in MCPCBs. High-power components should be placed close to the metal core and thermal vias to minimize the thermal resistance. Components with similar thermal characteristics should be grouped together to avoid hot spots and ensure even heat distribution.
LED Applications of MCPCB
MCPCBs are widely used in LED lighting applications due to their excellent thermal management capabilities. LEDs generate a significant amount of heat during operation, which can negatively impact their performance, efficiency, and lifespan. By using MCPCBs, the heat generated by LEDs can be effectively dissipated, resulting in several benefits.
Improved LED Performance
MCPCBs help maintain lower junction temperatures in LEDs, which translates to several performance improvements:
-
Higher Luminous Efficiency: As the junction temperature decreases, the luminous efficiency of LEDs increases. This means that LEDs can produce more light output for the same amount of power input.
-
Enhanced Color Consistency: High junction temperatures can cause color shifts in LEDs. By keeping the temperature stable, MCPCBs help maintain consistent color output over time.
-
Increased Lifespan: Elevated temperatures accelerate the degradation of LEDs, leading to premature failure. By dissipating heat effectively, MCPCBs can significantly extend the lifespan of LEDs.
Compact LED Modules
MCPCBs enable the design of compact and high-density LED modules. The metal core allows for efficient heat dissipation, eliminating the need for bulky external heat sinks. This results in smaller and more lightweight LED fixtures, which is particularly advantageous in applications with limited space or weight constraints.
Cost-Effective Thermal Solution
Using MCPCBs for LED applications can be a cost-effective thermal management solution compared to traditional methods. By integrating the heat dissipation capabilities into the PCB itself, the need for additional heat sinks or cooling mechanisms is reduced. This simplifies the overall system design and lowers manufacturing and assembly costs.
MCPCB Manufacturing Process
The manufacturing process of MCPCBs involves several steps:
-
Metal Core Preparation: The aluminum substrate is cleaned and surface-treated to ensure proper adhesion of the dielectric layer.
-
Dielectric Layer Application: The dielectric layer is applied onto the metal core using techniques such as lamination, screen printing, or powder coating. The dielectric material is cured and hardened to form a stable insulating layer.
-
Copper Foil Lamination: A copper foil is laminated onto the dielectric layer using heat and pressure. The copper foil thickness can vary depending on the desired current-carrying capacity and thermal performance.
-
Circuit Patterning: The copper layer is patterned using photolithography and etching processes to create the desired circuit layout. This involves applying a photoresist, exposing it to UV light through a patterned mask, and etching away the unwanted copper.
-
Drill and Plating: Holes are drilled through the MCPCB for component mounting and thermal vias. The holes are then plated with copper to establish electrical connections and enhance thermal conductivity.
-
Surface Finishing: A surface finish, such as HASL (Hot Air Solder Leveling), ENIG (Electroless Nickel Immersion Gold), or OSP (Organic Solderability Preservative), is applied to the copper traces to protect them from oxidation and improve solderability.
-
Solder Mask Application: A solder mask is applied to the MCPCB to insulate and protect the copper traces. Openings are left in the solder mask for component pads and exposed copper areas.
-
Silkscreen Printing: Silkscreen printing is used to add component designators, logos, and other markings on the MCPCB for easy identification and assembly.
-
Singulation: The manufactured panel is cut into individual MCPCBs using methods like routing, punching, or V-scoring.
MCPCB Testing and Quality Control
To ensure the quality and reliability of MCPCBs, several testing and inspection procedures are carried out during and after the manufacturing process.
Visual Inspection
Visual inspection is performed at various stages of the manufacturing process to identify any visible defects or anomalies. This includes checking for proper alignment of layers, uniform dielectric coverage, and accurate patterning of the copper traces.
Electrical Testing
Electrical testing is conducted to verify the continuity and insulation resistance of the MCPCB. This involves using automated testing equipment to check for short circuits, open circuits, and other electrical faults. High-voltage testing may also be performed to ensure adequate dielectric strength between the copper layer and the metal core.
Thermal Resistance Measurement
Thermal resistance measurement is crucial for evaluating the thermal performance of MCPCBs. The thermal resistance between the heat source (e.g., LED) and the metal core is measured using specialized equipment. This measurement helps validate the effectiveness of the thermal design and ensures that the MCPCB meets the required thermal specifications.
Microsectioning Analysis
Microsectioning analysis involves cross-sectioning a sample of the MCPCB and examining it under a microscope. This technique allows for detailed evaluation of the layer thicknesses, dielectric coverage, copper plating quality, and thermal via integrity. Microsectioning analysis helps identify any internal defects or deviations from the design specifications.
MCPCB Assembly Considerations
When assembling components on MCPCBs, certain considerations should be taken into account to ensure proper thermal management and reliable performance.
Soldering Techniques
Soldering components onto MCPCBs requires careful temperature control to avoid damaging the dielectric layer or the components. Reflow soldering is commonly used for surface-mount components, while Wave Soldering or hand soldering can be employed for through-hole components. It is important to follow the recommended soldering profiles and use compatible solder alloys to achieve reliable solder joints.
Thermal Interface Material Application
Applying thermal interface materials (TIMs) between the components and the MCPCB is crucial for efficient heat transfer. The TIM should be applied in a thin, uniform layer to minimize thermal resistance. Proper surface preparation, such as cleaning and degreasing, should be performed before applying the TIM to ensure good adhesion and thermal contact.
Mechanical Considerations
MCPCBs have different mechanical properties compared to traditional FR-4 PCBs. The metal core provides added rigidity and strength, but it also makes the MCPCB more susceptible to bending and warping. Proper handling and mounting techniques should be employed to avoid excessive mechanical stress on the board. Using appropriate fasteners and mounting hardware can help distribute the mechanical load evenly and prevent damage to the MCPCB.
FAQ
-
What are the advantages of using MCPCB over traditional PCB?
MCPCBs offer several advantages over traditional PCBs, including enhanced thermal management, improved LED performance and lifespan, reduced size and weight, increased reliability, and cost-effectiveness for high-power applications. -
How does the metal core in MCPCB help with thermal management?
The metal core in MCPCB acts as a heat spreader, quickly transferring heat away from the heat-generating components and distributing it evenly across the board. This helps maintain lower junction temperatures, leading to improved performance and reliability. -
What are thermal vias, and how do they enhance thermal performance in MCPCBs?
Thermal vias are small holes drilled through the MCPCB, connecting the copper layer to the metal core. They provide a low-resistance thermal path, allowing heat to be conducted from the components to the metal core more efficiently, thus enhancing the overall thermal performance of the MCPCB. -
What factors should be considered when designing an MCPCB?
When designing an MCPCB, several factors should be considered, including the dielectric layer thickness, copper thickness, thermal via placement, and component placement. These factors impact the thermal performance, electrical insulation, and overall reliability of the MCPCB. -
How does using MCPCB benefit LED applications?
Using MCPCBs in LED applications provides several benefits, such as improved LED performance, enhanced color consistency, increased lifespan, compact LED module design, and cost-effective thermal management. MCPCBs help dissipate heat efficiently, maintaining lower junction temperatures, which is crucial for optimal LED performance and longevity.
Conclusion
Metal Core PCBs (MCPCBs) have emerged as a vital solution for thermal management in high-power applications, particularly in LED lighting. By combining the electrical functionality of a traditional PCB with the thermal dissipation capabilities of a metal substrate, MCPCBs offer a compact, reliable, and cost-effective approach to managing heat.
The use of MCPCBs has revolutionized LED lighting design, enabling the development of high-performance, long-lasting, and energy-efficient LED systems. With their excellent thermal conductivity, MCPCBs help maintain lower junction temperatures, improve luminous efficiency, enhance color consistency, and extend the lifespan of LEDs.
As the demand for high-power electronics and advanced lighting solutions continues to grow, MCPCBs will play an increasingly important role in thermal management. By understanding the construction, design considerations, manufacturing processes, and assembly techniques associated with MCPCBs, engineers and manufacturers can harness their potential to create innovative and reliable products that meet the evolving needs of various industries.
No responses yet