Introduction to Automotive PCBs
Automotive Printed Circuit Boards (PCBs) are essential components in modern vehicles, enabling the functionality of various electronic systems. As the automotive industry continues to evolve, with a focus on electrification, autonomy, and connectivity, the demand for high-quality, reliable, and advanced automotive PCBs is on the rise. In this comprehensive article, we will delve into the latest trends, technologies, and challenges surrounding automotive PCBs in 2024.
The Growing Importance of Automotive PCBs
The automotive industry is undergoing a significant transformation, driven by the increasing adoption of electric vehicles (EVs), advanced driver assistance systems (ADAS), and connected car technologies. These advancements rely heavily on the performance and reliability of automotive PCBs, which serve as the backbone of a vehicle’s electronic systems.
Key Applications of Automotive PCBs
Automotive PCBs find applications in various systems within a vehicle, including:
- Powertrain control modules
- Infotainment systems
- ADAS sensors and control units
- Body control modules
- Lighting systems
- Battery management systems (BMS) in EVs
As vehicles become more sophisticated and feature-rich, the complexity and importance of automotive PCBs continue to grow.
Trends in Automotive PCB Design and Manufacturing
Miniaturization and High-Density Interconnect (HDI) PCBs
One of the key trends in automotive PCB design is miniaturization. As vehicle manufacturers strive to reduce weight, save space, and improve fuel efficiency, the demand for smaller and more compact electronic components has increased. High-Density Interconnect (HDI) PCBs, which feature finer traces, smaller vias, and higher layer counts, enable the integration of more functionality into smaller form factors.
Flexible and Rigid-Flex PCBs
Flexible and rigid-flex PCBs are gaining popularity in the automotive industry due to their ability to conform to complex shapes and withstand vibrations and mechanical stress. These PCBs offer several advantages over traditional rigid PCBs, such as:
- Improved reliability in harsh environments
- Reduced weight and space requirements
- Enhanced design flexibility
- Simplified assembly processes
Flexible and rigid-flex PCBs are particularly well-suited for applications like sensor integration, wiring harnesses, and in-vehicle displays.
Advanced Materials and Substrates
The demanding operating conditions in automotive environments, such as extreme temperatures, moisture, and vibrations, require the use of advanced materials and substrates in PCB manufacturing. Some of the materials gaining traction in the automotive industry include:
- High-Tg FR-4 laminates for improved thermal stability
- Polyimide (PI) and liquid crystal polymer (LCP) for Flexible PCBs
- Metal-core PCBs (MCPCBs) for enhanced thermal management
- Ceramic substrates for high-temperature applications
The selection of appropriate materials ensures the long-term reliability and performance of automotive PCBs.
Adoption of Industry 4.0 Technologies
The automotive PCB manufacturing industry is embracing Industry 4.0 technologies to improve efficiency, quality, and traceability. Some of the key technologies being implemented include:
- Industrial Internet of Things (IIoT) for real-time monitoring and data collection
- Artificial intelligence (AI) and machine learning (ML) for process optimization and predictive maintenance
- Robotics and automation for increased productivity and consistency
- Big data analytics for quality control and supply chain management
These technologies enable manufacturers to streamline their processes, reduce costs, and deliver high-quality automotive PCBs consistently.
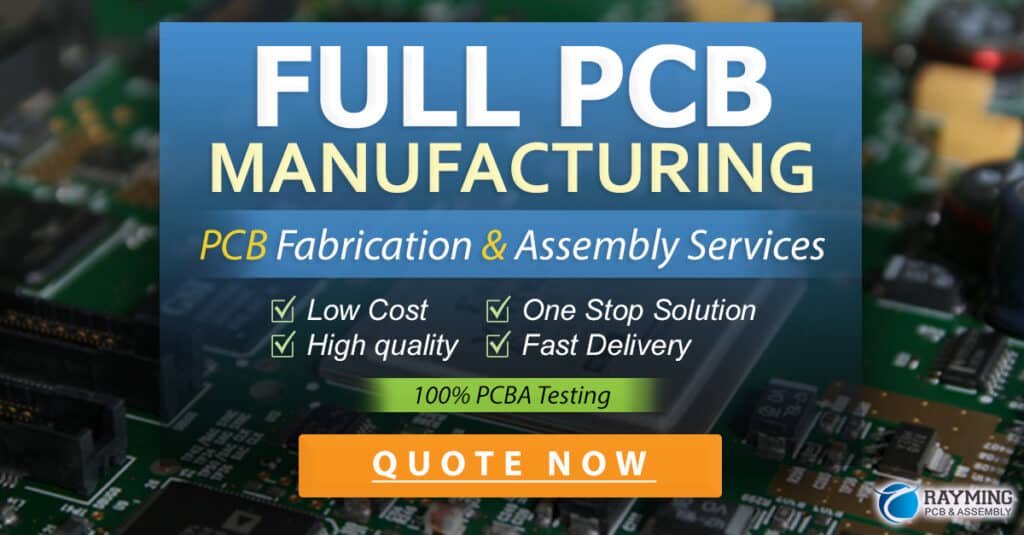
Challenges and Solutions in Automotive PCB Design and Manufacturing
Ensuring Reliability in Harsh Environments
One of the primary challenges in automotive PCB design and manufacturing is ensuring reliability in the harsh operating conditions encountered in vehicles. Automotive PCBs must withstand:
- Wide temperature ranges (-40°C to +125°C)
- Humidity and moisture exposure
- Vibrations and mechanical shocks
- Electromagnetic interference (EMI) and electromagnetic compatibility (EMC) issues
To address these challenges, PCB designers and manufacturers employ various techniques, such as:
- Selecting appropriate materials and coatings
- Implementing robust design practices, like thermal management and strain relief
- Conducting rigorous testing and qualification processes
- Adhering to industry standards and regulations, such as AEC-Q100 and ISO 26262
Managing Supply Chain Complexities
The automotive industry relies on a complex global supply chain, which can pose challenges for PCB manufacturers. Some of the key issues include:
- Ensuring the availability and quality of raw materials
- Managing lead times and inventory levels
- Navigating geopolitical risks and trade tensions
- Maintaining compliance with environmental and social responsibility standards
To mitigate these challenges, automotive PCB manufacturers are adopting supply chain management best practices, such as:
- Diversifying supplier base and sourcing strategies
- Implementing real-time supply chain visibility and risk monitoring
- Collaborating closely with customers and suppliers
- Investing in sustainable and ethical sourcing practices
Keeping Up with Rapidly Evolving Technologies
The automotive industry is characterized by rapid technological advancements, which can be challenging for PCB designers and manufacturers to keep pace with. Some of the emerging technologies that are shaping the future of automotive PCBs include:
- 5G connectivity and vehicle-to-everything (V2X) communication
- Autonomous driving and sensor fusion
- High-voltage systems for electric vehicles
- Wireless charging and power management
To stay competitive, automotive PCB manufacturers must continually invest in research and development, collaborate with industry partners, and adapt their processes to accommodate new technologies and requirements.
Future Outlook for Automotive PCBs
The automotive PCB market is poised for significant growth in the coming years, driven by the increasing adoption of electric vehicles, ADAS, and connected car technologies. According to market research reports, the global automotive PCB market is expected to reach USD 14.8 billion by 2025, growing at a CAGR of 6.7% from 2020 to 2025.
Year | Market Size (USD Billion) |
---|---|
2020 | 10.2 |
2021 | 10.9 |
2022 | 11.6 |
2023 | 12.4 |
2024 | 13.2 |
2025 | 14.8 |
Source: MarketsandMarkets Analysis
As the automotive industry continues to evolve, PCB manufacturers will need to adapt to new challenges and opportunities. Some of the key areas of focus for the future of automotive PCBs include:
- Developing advanced materials and manufacturing processes for improved performance and reliability
- Integrating more functionality and intelligence into PCBs, such as embedded sensors and processors
- Enabling faster data transmission and processing for autonomous driving and connected car applications
- Collaborating closely with automotive OEMs and Tier 1 suppliers to co-develop innovative solutions
- Investing in sustainable and eco-friendly practices to reduce environmental impact
By addressing these challenges and embracing new technologies, automotive PCB manufacturers can position themselves for success in the dynamic and rapidly evolving automotive industry.
Frequently Asked Questions (FAQ)
-
Q: What are the key differences between automotive PCBs and standard PCBs?
A: Automotive PCBs are designed to withstand harsh operating conditions, such as extreme temperatures, vibrations, and moisture. They also must comply with stringent industry standards and regulations for safety and reliability. In contrast, standard PCBs may not be subject to the same level of environmental and regulatory requirements. -
Q: How are automotive PCBs tested for reliability and durability?
A: Automotive PCBs undergo rigorous testing and qualification processes to ensure they meet the required performance and reliability standards. Some of the common tests include thermal cycling, vibration and shock testing, humidity exposure, and electromagnetic compatibility (EMC) testing. These tests are conducted in accordance with industry standards, such as AEC-Q100 and IPC-6012. -
Q: What are the challenges in designing and manufacturing high-density interconnect (HDI) PCBs for automotive applications?
A: The main challenges in designing and manufacturing HDI PCBs for automotive applications include maintaining signal integrity, managing thermal dissipation, and ensuring mechanical reliability. HDI PCBs feature finer traces and smaller vias, which can be more susceptible to signal integrity issues and manufacturing defects. Designers must carefully optimize the layout and select appropriate materials to mitigate these challenges. -
Q: How are automotive PCB manufacturers addressing the need for sustainable and eco-friendly practices?
A: Automotive PCB manufacturers are adopting various sustainable practices, such as using lead-free and halogen-free materials, implementing energy-efficient manufacturing processes, and reducing waste and emissions. They are also investing in recycling and end-of-life management programs to minimize the environmental impact of their products. -
Q: What are the key considerations when selecting an automotive PCB manufacturer?
A: When selecting an automotive PCB manufacturer, key considerations include their experience and expertise in the automotive industry, compliance with relevant quality and safety standards (e.g., IATF 16949, ISO 26262), manufacturing capabilities and capacity, supply chain management, and customer support. It is also essential to evaluate their ability to innovate and adapt to new technologies and requirements.
Conclusion
Automotive PCBs play a crucial role in enabling the functionality, safety, and performance of modern vehicles. As the automotive industry undergoes a transformative shift towards electrification, autonomy, and connectivity, the demand for advanced and reliable automotive PCBs will continue to grow. PCB designers and manufacturers must stay at the forefront of technological advancements, while also addressing challenges related to reliability, supply chain management, and sustainability.
By embracing innovative design and manufacturing practices, collaborating closely with industry partners, and investing in research and development, automotive PCB manufacturers can capitalize on the opportunities presented by the evolving automotive landscape. As we look ahead to 2024 and beyond, the future of automotive PCBs is filled with exciting possibilities, driving the development of safer, smarter, and more sustainable vehicles.
No responses yet