Introduction to Flexible PCBs
Flexible printed circuit boards (PCBs) are a revolutionary technology that has transformed the electronics industry. Unlike traditional rigid PCBs, flexible PCBs are made from thin, flexible materials that can bend and fold to fit into tight spaces and conform to curved surfaces. This unique property makes them ideal for a wide range of applications, from wearable devices and medical implants to aerospace and automotive systems.
In this comprehensive article, we’ll explore everything you need to know about flexible PCBs, including their benefits, manufacturing process, design considerations, and common applications. Whether you’re an engineer, designer, or just curious about this innovative technology, this guide will provide you with valuable insights and practical knowledge.
Benefits of Flexible PCBs
Flexible PCBs offer several advantages over traditional rigid PCBs, making them an attractive choice for many applications. Here are some of the key benefits of using flexible PCBs:
Space Savings and Miniaturization
One of the primary advantages of flexible PCBs is their ability to fit into tight spaces and conform to irregular shapes. This allows designers to create more compact and miniaturized devices, which is especially important in applications where space is limited, such as wearables, medical devices, and portable electronics.
Improved Reliability and Durability
Flexible PCBs are highly durable and can withstand repeated bending and flexing without breaking or losing functionality. This makes them more reliable than rigid PCBs in applications where the device is subject to vibration, shock, or mechanical stress.
Reduced Weight and Thickness
Since flexible PCBs are made from thin, lightweight materials, they can significantly reduce the overall weight and thickness of electronic devices. This is particularly important in aerospace and automotive applications, where every gram counts.
Simplified Assembly and Manufacturing
Flexible PCBs can simplify the assembly process by eliminating the need for connectors and wires between different components. This reduces the number of parts required and minimizes the risk of assembly errors, leading to faster and more efficient manufacturing.
Enhanced Signal Integrity and EMI Shielding
Flexible PCBs can provide better signal integrity and electromagnetic interference (EMI) shielding compared to rigid PCBs. The close proximity of components and the ability to use shielding materials like copper or silver ink can help minimize signal noise and interference.
Manufacturing Process of Flexible PCBs
The manufacturing process of flexible PCBs is similar to that of rigid PCBs, but with some key differences to account for the unique properties of flexible materials. Here’s an overview of the typical manufacturing steps:
-
Material Selection: The first step is to choose the appropriate flexible substrate material, such as polyimide, polyester, or PEEK. The choice depends on factors like flexibility, temperature resistance, and chemical compatibility.
-
Circuit Design: The circuit layout is designed using CAD software, taking into account the specific requirements of the flexible PCB, such as bend radius, layer stack-up, and component placement.
-
Cutting and Drilling: The flexible substrate is cut to the desired size and shape using laser or mechanical cutting methods. Holes are drilled for component mounting and vias.
-
Copper Cladding: A thin layer of copper is laminated onto the flexible substrate using heat and pressure. The copper is then patterned and etched to create the circuit traces.
-
Soldermask and Silkscreen: A soldermask layer is applied to protect the copper traces from oxidation and short circuits. A silkscreen layer is added to label components and provide visual guides for assembly.
-
Component Assembly: Surface mount and through-hole components are attached to the flexible PCB using reflow soldering or conductive adhesives.
-
Coverlay and Stiffeners: A coverlay film is laminated over the assembled PCB to provide additional protection and insulation. Stiffeners may be added to certain areas to improve mechanical stability.
-
Testing and Inspection: The finished flexible PCB undergoes rigorous testing and inspection to ensure proper functionality, reliability, and compliance with industry standards.
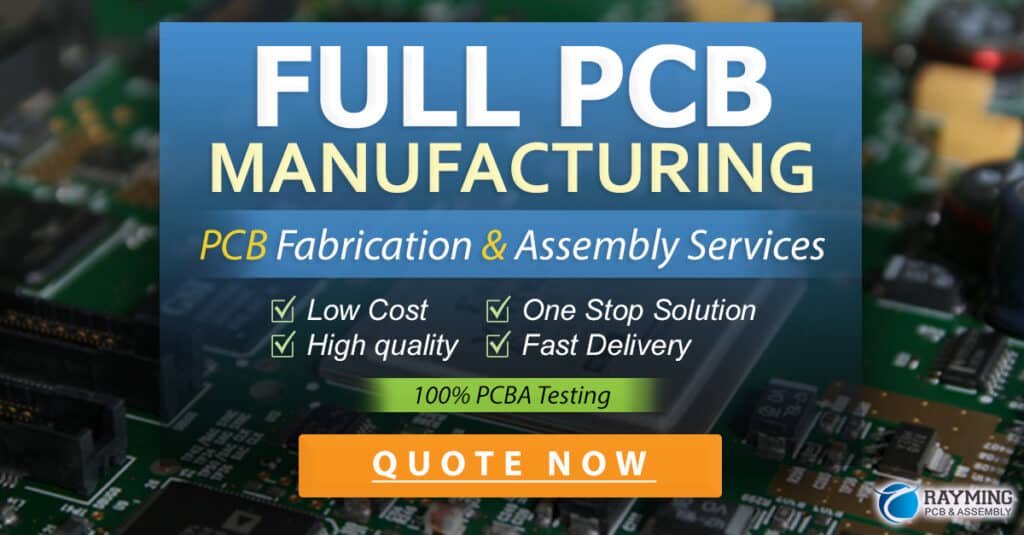
Design Considerations for Flexible PCBs
Designing flexible PCBs requires careful consideration of several factors to ensure optimal performance and reliability. Here are some key design considerations to keep in mind:
Bend Radius and Flexibility
The bend radius is a critical parameter in flexible PCB design, as it determines how tightly the board can be folded without causing damage or affecting functionality. The minimum bend radius depends on factors like substrate thickness, copper weight, and component placement. Designers must also consider the number of flex cycles required over the product’s lifetime.
Layer Stack-up and Material Selection
The layer stack-up of a flexible PCB can have a significant impact on its performance and reliability. Designers must carefully choose the number and arrangement of conductive, dielectric, and adhesive layers based on the specific requirements of the application. The choice of substrate material is also crucial, as it affects properties like flexibility, temperature resistance, and chemical compatibility.
Component Placement and Routing
Component placement and routing are more challenging in flexible PCBs due to the need to accommodate bending and flexing. Designers must ensure that components are placed in areas with minimal stress and that traces are routed to avoid sharp bends or kinks. The use of strain relief features, such as curved traces or accordion-style folds, can help improve reliability.
Shielding and Grounding
Proper shielding and grounding are essential for minimizing signal noise and interference in flexible PCBs. Designers can use techniques like copper shielding, conductive adhesives, and grounding planes to provide effective EMI protection. The choice of shielding material and method depends on factors like frequency range, shielding effectiveness, and cost.
Manufacturing and Assembly Considerations
Designers must also consider the manufacturing and assembly processes when designing flexible PCBs. This includes factors like minimum feature sizes, tolerances, and design for manufacturability (DFM) guidelines. Close collaboration with the manufacturing team can help ensure that the design is optimized for production and assembly.
Common Applications of Flexible PCBs
Flexible PCBs are used in a wide range of industries and applications due to their unique properties and benefits. Here are some of the most common applications of flexible PCBs:
Application | Description |
---|---|
Wearable Devices | Flexible PCBs are ideal for wearable devices like smartwatches, fitness trackers, and medical monitors, as they can conform to the shape of the body and withstand repeated flexing. |
Medical Implants | Flexible PCBs are used in medical implants like pacemakers, cochlear implants, and neurostimulators, where they must fit into tight spaces and operate reliably for long periods. |
Aerospace and Defense | Flexible PCBs are used in aerospace and defense applications like satellites, missiles, and avionics systems, where weight reduction and reliability are critical. |
Automotive Electronics | Flexible PCBs are used in automotive applications like infotainment systems, instrument clusters, and sensors, where they must withstand harsh environments and vibration. |
Consumer Electronics | Flexible PCBs are used in consumer electronics like smartphones, tablets, and laptops, where they enable thinner and more compact designs. |
Industrial Automation | Flexible PCBs are used in industrial automation applications like robotics, motion control, and machine vision, where they must operate reliably in harsh environments. |
FAQ
What is the difference between flexible and Rigid-Flex PCBs?
Flexible PCBs are made entirely from flexible materials and can bend and fold freely. Rigid-flex PCBs, on the other hand, are a hybrid of flexible and rigid sections, where the flexible portions connect the rigid sections. Rigid-flex PCBs offer the benefits of both technologies, such as improved reliability and reduced assembly costs.
Can flexible PCBs be repaired?
Repairing flexible PCBs can be challenging due to their delicate nature and the difficulty of accessing components. In most cases, it is more cost-effective to replace the entire board rather than attempt a repair. However, some specialized techniques, such as micro-soldering or conductive adhesives, can be used for minor repairs.
How long do flexible PCBs last?
The lifespan of a flexible PCB depends on several factors, such as the materials used, the operating environment, and the number of flex cycles. With proper design and manufacturing, flexible PCBs can last for millions of flex cycles and operate reliably for many years. However, like any electronic component, they will eventually wear out and need to be replaced.
Are flexible PCBs more expensive than rigid PCBs?
In general, flexible PCBs are more expensive than rigid PCBs due to the specialized materials, manufacturing processes, and design considerations involved. However, the total cost of ownership can be lower for flexible PCBs in certain applications, as they can reduce assembly costs, improve reliability, and enable more compact designs.
Can flexible PCBs be used in high-temperature environments?
Yes, flexible PCBs can be designed to operate in high-temperature environments by using specialized substrate materials like polyimide or PEEK, which have high glass transition temperatures and excellent thermal stability. However, designers must also consider factors like component selection, solder joint reliability, and thermal management to ensure reliable operation at elevated temperatures.
Conclusion
Flexible PCBs are a game-changing technology that offers numerous benefits over traditional rigid PCBs, including space savings, improved reliability, reduced weight, simplified assembly, and enhanced signal integrity. By understanding the manufacturing process, design considerations, and common applications of flexible PCBs, engineers and designers can leverage this innovative technology to create more advanced and reliable electronic devices.
As the demand for smaller, lighter, and more flexible electronics continues to grow, flexible PCBs will play an increasingly important role in shaping the future of the industry. With ongoing research and development in materials science, manufacturing techniques, and design tools, we can expect to see even more exciting applications and Breakthroughs in the years to come.
No responses yet