Introduction to LED PCBs
Light-emitting diode (LED) printed circuit boards (PCBs) are essential components in various electronic devices, from consumer electronics to industrial applications. LED PCBs are designed to support and connect LED components while ensuring optimal performance and reliability. In this comprehensive guide, we will explore the process of LED PCB Assembly and discuss common defects and their analysis.
Key Components of LED PCBs
1. Substrate Material
The substrate material is the foundation of an LED PCB. Common substrate materials include:
- FR-4: A flame-retardant glass-reinforced epoxy laminate, widely used for its durability and cost-effectiveness.
- Aluminum: Used for its excellent thermal dissipation properties, especially in high-power LED applications.
- Ceramic: Offers superior thermal conductivity and dimensional stability, ideal for harsh environments.
2. Copper Layers
Copper layers are responsible for conducting electrical signals and dissipating heat. The number of layers and their thickness depend on the complexity and power requirements of the LED application.
3. Solder Mask
The solder mask is a protective layer applied over the copper traces, leaving only the exposed pads for soldering. It prevents short circuits and provides insulation between components.
4. Silkscreen
The silkscreen layer contains text, logos, and component identifiers, aiding in the assembly process and product branding.
LED PCB Assembly Process
1. Design and Fabrication
The LED PCB assembly process begins with the design and fabrication of the bare PCB. The design is created using electronic design automation (EDA) software, considering factors such as component placement, signal integrity, and thermal management.
2. Solder Paste Application
Solder paste, a mixture of tiny solder spheres and flux, is applied to the exposed pads on the PCB using a stencil or screen printing process. The stencil ensures precise solder paste placement and volume control.
3. Component Placement
LED components, along with other electronic components, are placed onto the PCB using automated pick-and-place machines. These machines use computer-aided design (CAD) data to accurately position components on the solder paste.
4. Reflow Soldering
The populated PCB is subjected to a reflow soldering process, where it passes through a carefully controlled temperature profile in a reflow oven. The solder paste melts, forming permanent electrical and mechanical connections between the components and the PCB.
5. Inspection and Testing
After the reflow soldering process, the assembled LED PCB undergoes visual inspection and automated optical inspection (AOI) to detect any defects or assembly issues. Functional testing is also performed to ensure the LED PCB meets the required specifications.
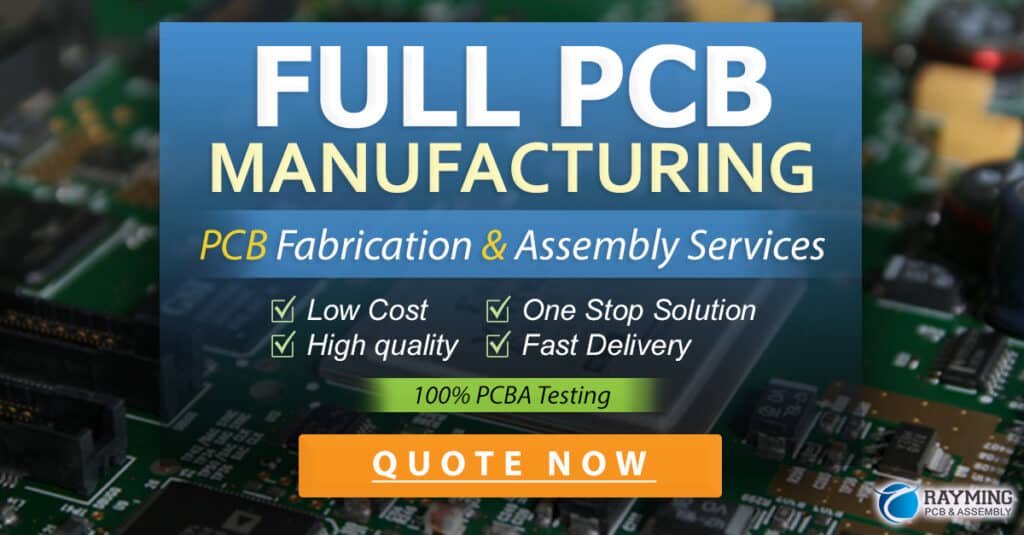
Common LED PCB Defects and Analysis
1. Solder Bridging
Solder bridging occurs when excess solder creates an unintended connection between two or more pads or traces. This defect can cause short circuits and affect the functionality of the LED PCB. Solder bridging can be caused by:
- Improper solder paste application
- Incorrect component placement
- Insufficient solder mask clearance
To analyze and prevent solder bridging, consider the following:
- Optimize stencil design and solder paste volume
- Ensure accurate component placement
- Maintain appropriate solder mask clearance
- Use AOI to detect solder bridging during inspection
2. Tombstoning
Tombstoning, also known as “chip standing” or “Manhattan effect,” is a defect where a surface-mount component, such as an LED or resistor, stands up on one end instead of lying flat on the PCB. This defect can be caused by:
- Uneven heating during the reflow process
- Imbalanced solder paste volume on component pads
- Misaligned component placement
To prevent tombstoning, consider the following:
- Ensure even heating during the reflow process
- Balance solder paste volume on component pads
- Use proper component placement techniques
- Optimize pad design and component selection
3. Insufficient Solder Joint
Insufficient solder joints occur when there is not enough solder to create a reliable connection between the component and the PCB. This defect can lead to poor electrical conductivity, reduced mechanical strength, and premature failure. Causes of insufficient solder joints include:
- Inadequate solder paste volume
- Improper reflow temperature profile
- Contaminated or oxidized component leads or PCB pads
To address insufficient solder joints, consider the following:
- Optimize solder paste volume and stencil design
- Adjust reflow temperature profile
- Ensure cleanliness of components and PCB pads
- Use X-ray inspection to detect hidden solder joint issues
4. LED Polarity Mismatch
LED polarity mismatch occurs when an LED is soldered onto the PCB with the anode and cathode reversed. This defect prevents the LED from functioning correctly and can cause damage to the LED or other components. Causes of LED polarity mismatch include:
- Incorrect component placement
- Unclear or missing polarity markings on the PCB or LED
- Human error during manual assembly
To prevent LED polarity mismatch, consider the following:
- Use clear and consistent polarity markings on the PCB and LED
- Implement automated optical inspection (AOI) to detect polarity issues
- Provide proper training for manual assembly operators
- Use polarized component footprints when possible
5. Thermal Management Issues
Thermal management is crucial for LED PCBs, as excessive heat can reduce LED performance, cause color shifts, and shorten the lifespan of the LED. Thermal management issues can arise from:
- Inadequate PCB substrate material selection
- Poor thermal interface material (TIM) application
- Insufficient heat sinking or cooling solutions
- High LED power density
To address thermal management issues, consider the following:
- Select appropriate PCB Substrate Materials with good thermal conductivity
- Use thermal interface materials (TIMs) to improve heat transfer
- Implement adequate heat sinking or cooling solutions
- Optimize LED power density and layout for better heat dissipation
- Use thermal simulation tools to predict and optimize thermal performance
Conclusion
Understanding the LED PCB assembly process and common defects is essential for designing, manufacturing, and troubleshooting LED-based electronic devices. By following best practices in design, assembly, and inspection, manufacturers can minimize defects and ensure the production of high-quality, reliable LED PCBs.
Frequently Asked Questions (FAQ)
1. What are the advantages of using Aluminum PCBs for LED applications?
Aluminum PCBs offer excellent thermal dissipation properties, making them suitable for high-power LED applications. They can effectively transfer heat away from the LEDs, improving performance and longevity. Additionally, aluminum PCBs provide good mechanical stability and are lightweight compared to other metal-core PCBs.
2. How can I choose the right solder paste for my LED PCB assembly process?
When selecting a solder paste for LED PCB assembly, consider factors such as:
- Melting temperature: Ensure the solder paste’s melting temperature is compatible with the reflow profile and the components used.
- Particle size: Choose a solder paste with the appropriate particle size for the PCB’s pitch and component sizes.
- Flux type: Select a flux type (e.g., no-clean, water-soluble, or rosin-based) based on the PCB’s cleaning requirements and environmental considerations.
- Viscosity: Ensure the solder paste has the right viscosity for the application method (e.g., stencil printing or dispensing).
Consult with your solder paste supplier or manufacturer for specific recommendations based on your LED PCB assembly needs.
3. What is the purpose of the silkscreen layer on an LED PCB?
The silkscreen layer on an LED PCB serves several purposes:
- Component identification: It provides text and symbols to identify components, their values, and their orientations, aiding in the assembly process and future maintenance.
- Branding: The silkscreen layer can include logos, product names, or company information for branding purposes.
- Assembly instructions: It may contain instructions or guidelines for assembling the PCB, such as connector pinouts or switch positions.
- Aesthetic appeal: A well-designed silkscreen layer can enhance the overall appearance of the LED PCB.
4. How can I troubleshoot LED polarity mismatch issues during the assembly process?
To troubleshoot LED polarity mismatch issues during the assembly process, follow these steps:
-
Inspect the PCB layout: Verify that the PCB layout has clear and consistent polarity markings for the LED footprints. Ensure that the anode and cathode pads are correctly labeled.
-
Check the component orientation: Visually inspect the LED components to confirm that they are placed on the PCB with the correct orientation. The anode and cathode leads should match the corresponding pads on the PCB.
-
Use AOI: Implement automated optical inspection (AOI) to detect polarity mismatches. AOI systems can compare the assembled PCB to the expected layout and identify any discrepancies in component orientation.
-
Perform functional testing: Conduct functional tests on the assembled LED PCB to verify that the LEDs are operating correctly. If an LED does not illuminate, it may indicate a polarity mismatch.
-
Rework and replace: If a polarity mismatch is detected, carefully desolder the affected LED and replace it with a new one, ensuring the correct orientation during the rework process.
5. What are some best practices for optimizing the reflow soldering process for LED PCBs?
To optimize the reflow soldering process for LED PCBs, consider the following best practices:
-
Use the appropriate reflow profile: Develop a reflow temperature profile that is suitable for the solder paste and components used. The profile should include proper preheat, soak, reflow, and cooling stages to ensure good solder joint formation and minimize thermal stress on the components.
-
Control the peak temperature: Ensure that the peak temperature during the reflow process does not exceed the maximum temperature ratings of the LED components and the PCB substrate. Excessive temperatures can cause damage to the LEDs and affect their performance.
-
Minimize temperature gradients: Strive for even heating across the PCB to minimize temperature gradients. Uneven heating can lead to defects such as tombstoning or insufficient solder joints. Consider using a convection reflow oven with good air circulation and temperature control.
-
Optimize the conveyor speed: Adjust the conveyor speed of the reflow oven to ensure that the PCB spends the appropriate amount of time in each stage of the reflow profile. A speed that is too fast may result in insufficient heating, while a speed that is too slow may cause overheating or damage to the components.
-
Monitor and maintain the reflow oven: Regularly monitor and calibrate the reflow oven to ensure consistent performance. Clean the oven periodically to remove any flux residue or contaminants that may affect the reflow process.
-
Use nitrogen atmosphere (if applicable): For high-reliability LED PCBs, consider using a nitrogen atmosphere during the reflow process. Nitrogen helps to reduce oxidation and improve solder joint quality, especially for lead-free solder alloys.
Defect Type | Causes | Prevention |
---|---|---|
Solder Bridging | – Improper solder paste application – Incorrect component placement – Insufficient solder mask clearance |
– Optimize stencil design and solder paste volume – Ensure accurate component placement – Maintain appropriate solder mask clearance – Use AOI to detect solder bridging during inspection |
Tombstoning | – Uneven heating during the reflow process – Imbalanced solder paste volume on component pads – Misaligned component placement |
– Ensure even heating during the reflow process – Balance solder paste volume on component pads – Use proper component placement techniques – Optimize pad design and component selection |
Insufficient Solder Joint | – Inadequate solder paste volume – Improper reflow temperature profile – Contaminated or oxidized component leads or PCB pads |
– Optimize solder paste volume and stencil design – Adjust reflow temperature profile – Ensure cleanliness of components and PCB pads – Use X-ray inspection to detect hidden solder joint issues |
LED Polarity Mismatch | – Incorrect component placement – Unclear or missing polarity markings on the PCB or LED – Human error during manual assembly |
– Use clear and consistent polarity markings on the PCB and LED – Implement automated optical inspection (AOI) to detect polarity issues – Provide proper training for manual assembly operators – Use polarized component footprints when possible |
Thermal Management Issues | – Inadequate PCB substrate material selection – Poor thermal interface material (TIM) application – Insufficient heat sinking or cooling solutions – High LED power density |
– Select appropriate PCB substrate materials with good thermal conductivity – Use thermal interface materials (TIMs) to improve heat transfer – Implement adequate heat sinking or cooling solutions – Optimize LED power density and layout for better heat dissipation – Use thermal simulation tools to predict and optimize thermal performance |
By understanding the causes and implementing the appropriate prevention measures for each type of defect, manufacturers can significantly improve the quality and reliability of their LED PCBs.
No responses yet