What is Electronic Manufacturing Technology?
Electronic Manufacturing Technology (EMT) refers to the set of processes, techniques, and tools used to design, develop, and manufacture electronic components, devices, and systems. EMT involves a wide range of activities, including:
- Circuit design and simulation
- Printed Circuit Board (PCB) design and fabrication
- Component selection and procurement
- Surface mount technology (SMT) and through-hole assembly
- Testing and quality control
- Packaging and shipping
EMT is a highly interdisciplinary field that combines knowledge from various domains, such as electrical engineering, materials science, computer science, and manufacturing engineering. The goal of EMT is to produce high-quality, reliable, and cost-effective electronic products that meet the needs of consumers and businesses.
Importance of Electronic Manufacturing Technology
Electronic Manufacturing Technology is essential for the growth and development of various industries, including:
- Consumer electronics
- Automotive
- Aerospace and defense
- Medical devices
- Industrial automation
- Telecommunications
- Energy and power systems
The importance of EMT can be attributed to several factors:
Enabling technological advancements
EMT plays a crucial role in enabling technological advancements by providing the means to manufacture new and innovative electronic products. As technology continues to evolve, EMT must adapt to meet the changing requirements of the industry, such as the need for smaller, faster, and more efficient electronic components.
Driving economic growth
The electronics industry is a significant contributor to the global economy, with an estimated market size of over $2 trillion. EMT is a key driver of this growth, as it enables the production of electronic products that are in high demand across various sectors. The growth of the electronics industry creates jobs, stimulates innovation, and contributes to overall economic development.
Enhancing product quality and reliability
EMT focuses on ensuring the quality and reliability of electronic products through rigorous testing and quality control processes. By adhering to strict quality standards and employing advanced manufacturing techniques, EMT helps to minimize defects, reduce product failures, and improve overall product performance.
Reducing costs and improving efficiency
EMT strives to optimize manufacturing processes and reduce costs through the use of automation, lean manufacturing principles, and continuous improvement initiatives. By streamlining production processes, minimizing waste, and improving efficiency, EMT helps to make electronic products more affordable and accessible to consumers.
Key Technologies in Electronic Manufacturing
Electronic Manufacturing Technology encompasses a wide range of technologies and processes, each playing a crucial role in the production of electronic products. Some of the key technologies in EMT include:
Surface Mount Technology (SMT)
Surface Mount Technology (SMT) is a method of assembling electronic components onto a printed circuit board (PCB) by soldering them directly onto the board’s surface. SMT has largely replaced through-hole technology in modern electronics manufacturing due to its numerous advantages, such as:
- Smaller component sizes and higher component density
- Faster assembly speeds and higher throughput
- Improved reliability and reduced defects
- Lower production costs
The SMT process typically involves the following steps:
- Solder paste application: A stencil is used to apply solder paste onto the PCB pads where components will be placed.
- Component placement: Automated pick-and-place machines accurately place components onto the PCB.
- Reflow soldering: The PCB is passed through a reflow oven, which melts the solder paste and creates a permanent connection between the components and the PCB.
- Inspection and testing: Automated optical inspection (AOI) systems and other testing methods are used to ensure the quality and functionality of the assembled PCB.
Through-Hole Technology (THT)
Through-Hole Technology (THT) is an older method of assembling electronic components onto a PCB by inserting the component leads through holes drilled in the board and soldering them on the opposite side. Although THT has largely been replaced by SMT in modern electronics manufacturing, it is still used for certain components that are not suitable for surface mounting, such as:
- Large or heavy components
- High-power components
- Connectors and sockets
- Components that require mechanical strength
The THT process typically involves the following steps:
- PCB Drilling: Holes are drilled into the PCB to accommodate component leads.
- Component insertion: Components are manually or automatically inserted into the drilled holes.
- Wave Soldering: The PCB is passed over a molten solder wave, which creates a connection between the component leads and the PCB.
- Inspection and testing: Visual inspection and functional testing are performed to ensure the quality and functionality of the assembled PCB.
Printed Circuit Board (PCB) Design and Fabrication
Printed Circuit Board (PCB) design and fabrication are essential aspects of Electronic Manufacturing Technology. PCBs are the backbone of electronic devices, providing the electrical interconnections and mechanical support for components. The PCB design and fabrication process typically involves the following steps:
- Schematic design: The electronic circuit is designed using schematic capture software, which defines the interconnections between components.
- PCB layout: The schematic is translated into a physical layout using PCB design software, which determines the placement of components and routing of traces on the board.
- PCB fabrication: The PCB layout is used to create a set of photomasks, which are used to transfer the circuit pattern onto copper-clad laminate boards through a photolithographic process. The boards are then etched, drilled, and plated to create the final PCB.
- PCB Assembly: Components are mounted onto the fabricated PCB using SMT or THT processes, as described earlier.
Advancements in PCB technology, such as high-density interconnect (HDI) and flexible circuits, have enabled the development of more compact, lightweight, and high-performance electronic devices.
Automated Optical Inspection (AOI)
Automated Optical Inspection (AOI) is a technology used to automatically inspect assembLED PCBs for defects, such as:
- Component placement errors
- Solder joint defects
- Missing or incorrect components
- Short circuits or open connections
AOI systems use high-resolution cameras and advanced image processing algorithms to compare the assembled PCB to a reference image or design data. Any deviations from the expected results are flagged as potential defects for further investigation.
The benefits of using AOI in electronic manufacturing include:
- Improved quality control and reduced defect rates
- Faster inspection speeds compared to manual inspection
- Consistent and objective inspection results
- Early detection of process issues, allowing for timely corrective actions
Functional Testing
Functional testing is a crucial step in the electronic manufacturing process, ensuring that the assembled product meets its intended performance and quality requirements. Functional testing typically involves:
- Power-on testing: Verifying that the product powers up correctly and all basic functions are operational.
- In-circuit testing (ICT): Using a bed-of-nails fixture to access individual components on the PCB and test their functionality.
- Boundary scan testing: Utilizing built-in test circuitry (such as JTAG) to test the interconnections and functionality of digital components.
- System-level testing: Validating the overall performance and functionality of the complete product under various operating conditions.
Functional testing helps to identify and isolate defects that may not be detectable through visual inspection alone, ensuring that only high-quality products are released to the market.
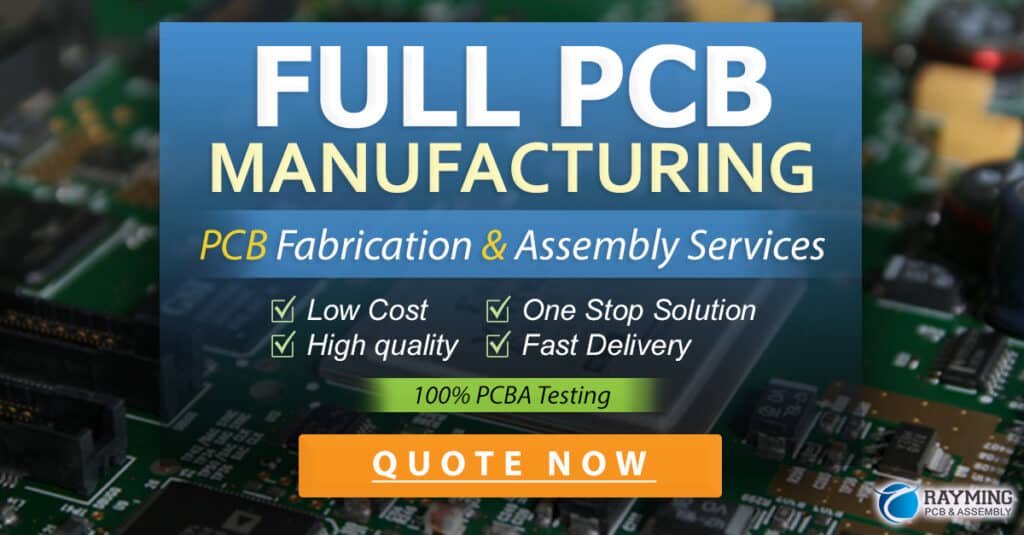
Trends and Future Prospects in Electronic Manufacturing Technology
Electronic Manufacturing Technology is constantly evolving to keep pace with the ever-changing demands of the electronics industry. Some of the key trends and future prospects in EMT include:
Miniaturization and Integration
The trend towards miniaturization and integration of electronic components and devices continues to drive advancements in EMT. As consumers demand smaller, lighter, and more powerful electronic products, manufacturers must adopt new technologies and processes to enable the production of highly integrated and compact systems.
Some of the key technologies enabling miniaturization and integration include:
- System-on-Chip (SoC): Integrating multiple functions (such as processors, memory, and peripherals) onto a single chip.
- Package-on-Package (PoP): Stacking multiple packaged chips on top of each other to create a compact, high-density module.
- 3D packaging: Using advanced packaging techniques, such as through-silicon vias (TSVs), to create 3D stacked chip structures.
Flexible and Wearable Electronics
The growing demand for flexible and wearable electronic devices, such as smartwatches, fitness trackers, and medical sensors, is driving the development of new materials and manufacturing processes in EMT.
Some of the key challenges and opportunities in this area include:
- Developing flexible and stretchable substrates and conductors that can withstand repeated bending and stretching.
- Integrating electronic components and sensors into textiles and other wearable materials.
- Designing and manufacturing thin, lightweight, and low-power electronic systems suitable for wearable applications.
Advancements in materials science, such as conductive polymers and nanomaterials, are expected to play a significant role in enabling the growth of flexible and wearable electronics.
Sustainable and Eco-Friendly Manufacturing
As environmental concerns continue to grow, there is an increasing focus on sustainable and eco-friendly practices in electronic manufacturing. This includes:
- Designing products for recyclability and easy disassembly at end-of-life.
- Reducing the use of hazardous substances in electronic components and manufacturing processes.
- Implementing energy-efficient manufacturing processes and using renewable energy sources.
- Adopting circular economy principles, such as reuse, refurbishment, and recycling of electronic products and components.
Regulatory requirements, such as the Restriction of Hazardous Substances (RoHS) directive and the Waste Electrical and Electronic Equipment (WEEE) directive, are driving the adoption of sustainable practices in the electronics industry.
Industry 4.0 and Smart Manufacturing
Industry 4.0, also known as the Fourth Industrial Revolution, is transforming the way electronic products are designed, manufactured, and delivered. Industry 4.0 technologies, such as the Internet of Things (IoT), big data analytics, artificial intelligence (AI), and robotics, are enabling the development of smart manufacturing systems that are:
- Connected: Machines, sensors, and systems are interconnected, allowing for real-time data collection and communication.
- Intelligent: Data analytics and AI algorithms are used to optimize processes, predict maintenance needs, and make autonomous decisions.
- Flexible: Manufacturing systems can quickly adapt to changing product requirements and market demands.
- Efficient: Resources are used more efficiently, with reduced waste and improved quality.
The adoption of Industry 4.0 technologies in electronic manufacturing is expected to lead to significant improvements in productivity, quality, and cost-effectiveness, as well as enabling the development of new business models and services.
FAQs
1. What are the main differences between Surface Mount Technology (SMT) and Through-Hole Technology (THT)?
Surface Mount Technology (SMT) involves mounting components directly onto the surface of a PCB, while Through-Hole Technology (THT) involves inserting component leads through holes drilled in the PCB and soldering them on the opposite side. SMT allows for smaller component sizes, higher component density, and faster assembly speeds compared to THT. However, THT is still used for certain components that require mechanical strength or are not suitable for surface mounting.
2. What is the role of Automated Optical Inspection (AOI) in electronic manufacturing?
Automated Optical Inspection (AOI) is used to automatically detect defects in assembled PCBs, such as component placement errors, solder joint defects, and missing or incorrect components. AOI systems use high-resolution cameras and image processing algorithms to compare the assembled PCB to a reference image or design data. The use of AOI improves quality control, reduces defect rates, and enables faster inspection speeds compared to manual inspection.
3. How is the trend towards miniaturization and integration impacting electronic manufacturing?
The trend towards miniaturization and integration is driving the adoption of new technologies and processes in electronic manufacturing, such as System-on-Chip (SoC), Package-on-Package (PoP), and 3D packaging. These technologies enable the production of highly integrated and compact electronic systems, allowing manufacturers to meet the growing demand for smaller, lighter, and more powerful electronic products.
4. What are some of the key challenges in manufacturing flexible and wearable electronics?
Some of the key challenges in manufacturing flexible and wearable electronics include developing flexible and stretchable substrates and conductors that can withstand repeated bending and stretching, integrating electronic components and sensors into textiles and other wearable materials, and designing and manufacturing thin, lightweight, and low-power electronic systems suitable for wearable applications. Advancements in materials science, such as conductive polymers and nanomaterials, are expected to play a significant role in addressing these challenges.
5. How is Industry 4.0 transforming electronic manufacturing?
Industry 4.0 technologies, such as the Internet of Things (IoT), big data analytics, artificial intelligence (AI), and robotics, are enabling the development of smart manufacturing systems in electronic manufacturing. These systems are connected, intelligent, flexible, and efficient, leading to improvements in productivity, quality, and cost-effectiveness. Industry 4.0 is also enabling the development of new business models and services in the electronics industry.
Conclusion
Electronic Manufacturing Technology is a dynamic and rapidly evolving field that plays a crucial role in the production of a wide range of electronic products. From consumer electronics to industrial equipment and aerospace systems, EMT enables the development of new and innovative products that are driving technological advancements and economic growth.
Key technologies in EMT, such as Surface Mount Technology, Printed Circuit Board design and fabrication, Automated Optical Inspection, and functional testing, are essential for ensuring the quality, reliability, and cost-effectiveness of electronic products. As the electronics industry continues to evolve, EMT must adapt to meet the changing requirements and challenges, such as miniaturization, integration, flexibility, and sustainability.
The future of Electronic Manufacturing Technology is shaped by trends such as Industry 4.0, smart manufacturing, and the growing demand for flexible and wearable electronics. By embracing these trends and investing in research and development, the electronics industry can continue to drive innovation, create new opportunities, and contribute to the overall advancement of technology and society.
No responses yet