What is Wave Soldering?
Wave soldering is a bulk soldering process that involves passing a PCB over a molten solder wave to solder the leads of through-hole components to the board. The process is highly automated and can solder hundreds of components onto a PCB in a matter of seconds.
The Wave Soldering Process
The wave soldering process consists of several steps:
- Flux application: A thin layer of flux is applied to the bottom side of the PCB to remove oxides and improve solder wettability.
- Preheating: The PCB is preheated to activate the flux and reduce thermal shock to the components during soldering.
- Solder wave contact: The PCB is passed over a wave of molten solder, which comes into contact with the leads of the through-hole components and the PCB’s solder pads.
- Cooling: The soldered PCB is cooled to allow the solder joints to solidify.
Advantages of Wave Soldering
Wave soldering offers several advantages over other soldering methods:
- High throughput: Wave soldering can solder hundreds of components onto a PCB in a matter of seconds, making it ideal for high-volume production.
- Consistency: The automated nature of wave soldering ensures consistent solder joint quality across all boards.
- Reliability: Wave soldered joints are strong and reliable, making them suitable for use in harsh environments.
- Cost-effective: Wave soldering is a cost-effective solution for mass production, as it reduces labor costs and increases production efficiency.
Types of Wave Soldering Machines
There are two main types of wave soldering machines:
- Conventional wave soldering machines: These machines feature a single solder wave and are suitable for soldering simple PCBs with low component density.
- Dual wave soldering machines: These machines feature two solder waves – a turbulent wave followed by a laminar wave. The turbulent wave ensures good solder penetration, while the laminar wave creates a smooth solder finish. Dual wave soldering machines are suitable for soldering complex PCBs with high component density.
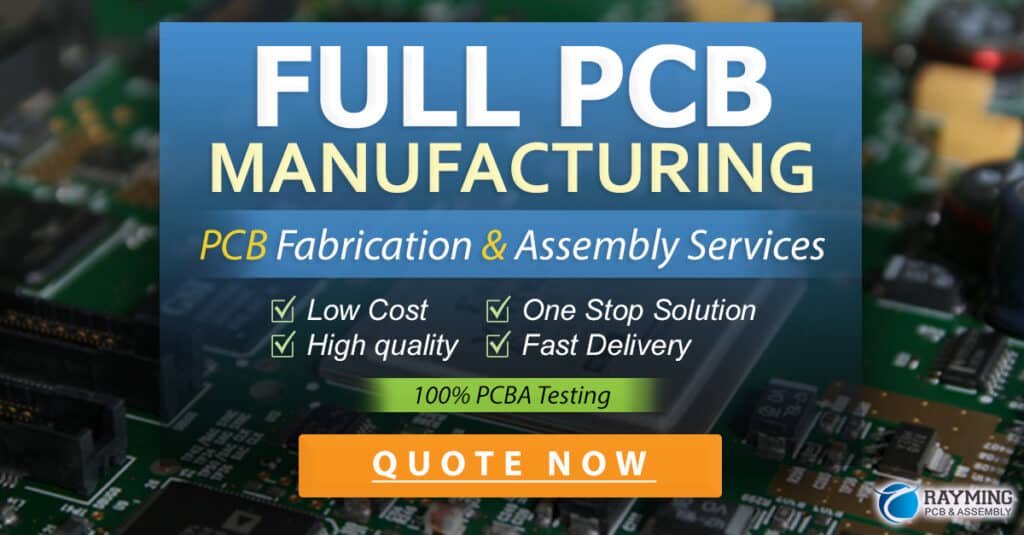
Wave Soldering Parameters
Several parameters must be carefully controlled to ensure optimal wave soldering results:
- Solder temperature: The solder temperature should be maintained within a specific range (typically 240-260°C) to ensure proper solder flow and wetting.
- Conveyor speed: The conveyor speed determines the contact time between the PCB and the solder wave. It should be adjusted based on the PCB’s complexity and the components’ thermal mass.
- Solder wave height: The solder wave height should be adjusted to ensure proper contact with the PCB and components without causing bridging or shadowing.
- Flux type and application: The flux type and application method should be selected based on the PCB’s surface finish and the components’ compatibility.
Wave Soldering Parameter Table
Parameter | Typical Range |
---|---|
Solder Temperature | 240-260°C |
Conveyor Speed | 0.5-2.0 m/min |
Solder Wave Height | 1-3 mm |
Flux Type | Rosin, water-soluble, no-clean |
Wave Soldering Defects and Troubleshooting
Despite its reliability, wave soldering can sometimes result in defects. Some common wave soldering defects include:
- Bridging: Solder bridges form between adjacent leads or pads due to excessive solder.
- Insufficient solder: Insufficient solder can result in weak or open solder joints.
- Solder balls: Solder balls can form due to excessive flux or incorrect solder wave parameters.
- Shadowing: Shadowing occurs when taller components block the solder wave from reaching smaller components.
To troubleshoot wave soldering defects, consider the following:
- Adjust the solder wave parameters (temperature, height, conveyor speed) to optimize solder flow and wetting.
- Review the PCB design for component placement and orientation to minimize shadowing and bridging.
- Ensure proper flux application and compatibility with the PCB surface finish and components.
- Regularly maintain and calibrate the wave soldering machine to ensure consistent performance.
Applications of Wave Soldering
Wave soldering is widely used in the electronics manufacturing industry for the production of:
- Consumer electronics (e.g., televisions, audio equipment)
- Automotive electronics (e.g., engine control units, infotainment systems)
- Industrial electronics (e.g., power supplies, control panels)
- Medical devices (e.g., patient monitors, diagnostic equipment)
- Aerospace and defense electronics (e.g., avionics, communication systems)
Frequently Asked Questions (FAQ)
1. Can wave soldering be used for surface mount components?
No, wave soldering is primarily used for through-hole components. Surface mount components are typically soldered using reflow soldering or selective soldering processes.
2. Is wave soldering suitable for double-sided PCBs?
Yes, wave soldering can be used for double-sided PCBs. However, special fixtures or pallets may be required to hold the components in place during the soldering process.
3. What is the difference between lead-based and lead-free solder in wave soldering?
Lead-based solder (Sn63Pb37) has a lower melting point and better wetting properties compared to lead-free solder (SAC305). However, due to environmental and health concerns, lead-free solder is becoming increasingly common in wave soldering applications.
4. How often should a wave soldering machine be maintained?
A wave soldering machine should be regularly maintained according to the manufacturer’s recommendations. This typically includes daily, weekly, and monthly maintenance tasks such as cleaning, inspection, and calibration.
5. Can wave soldering be used for high-mix, low-volume production?
While wave soldering is best suited for high-volume production, it can be used for high-mix, low-volume production with the use of selective soldering machines or manual soldering techniques for components that are not compatible with the wave soldering process.
Conclusion
Wave soldering is a reliable and efficient method for soldering through-hole components onto PCBs in high-volume production. By understanding the wave soldering process, its advantages, and its applications, electronics manufacturers can optimize their production processes and ensure the highest quality solder joints. With proper machine maintenance, parameter control, and defect troubleshooting, wave soldering can continue to play a vital role in the electronics manufacturing industry for years to come.
No responses yet