What is PCB Assembly?
PCB assembly (PCBA) is the process of soldering electronic components onto a printed circuit board (PCB) to create a functional electronic device. This process involves several steps, including:
- Solder paste application
- Component placement
- Reflow soldering
- Inspection and testing
PCBA services are essential for businesses and individuals who require custom-made electronic devices, prototypes, or small series production runs.
Why Choose Professional PCBA Services?
Outsourcing your PCB assembly needs to professional services offers several advantages:
-
Expertise: PCBA service providers have skilled technicians and engineers with extensive experience in assembling various types of PCBs.
-
Quality: Professional PCBA services use state-of-the-art equipment and follow strict quality control procedures to ensure the highest quality of the assembLED PCBs.
-
Cost-effectiveness: Outsourcing PCBA can be more cost-effective than setting up an in-house assembly line, especially for small to medium-sized businesses.
-
Time-saving: PCBA service providers can often deliver assembled PCBs faster than in-house assembly, allowing you to bring your products to market more quickly.
How to Choose the Right PCBA Service Provider
When selecting a PCBA service provider, consider the following factors:
-
Experience: Look for a company with a proven track record in assembling PCBs similar to your project requirements.
-
Capabilities: Ensure that the service provider has the necessary equipment, expertise, and capacity to handle your project.
-
Quality certifications: Choose a PCBA service provider with relevant quality certifications, such as ISO 9001, IPC-A-610, or IPC-J-STD-001.
-
Customer support: Select a company that offers excellent customer support and clear communication throughout the assembly process.
-
Pricing: Compare prices from multiple service providers to ensure you get the best value for your money without compromising on quality.
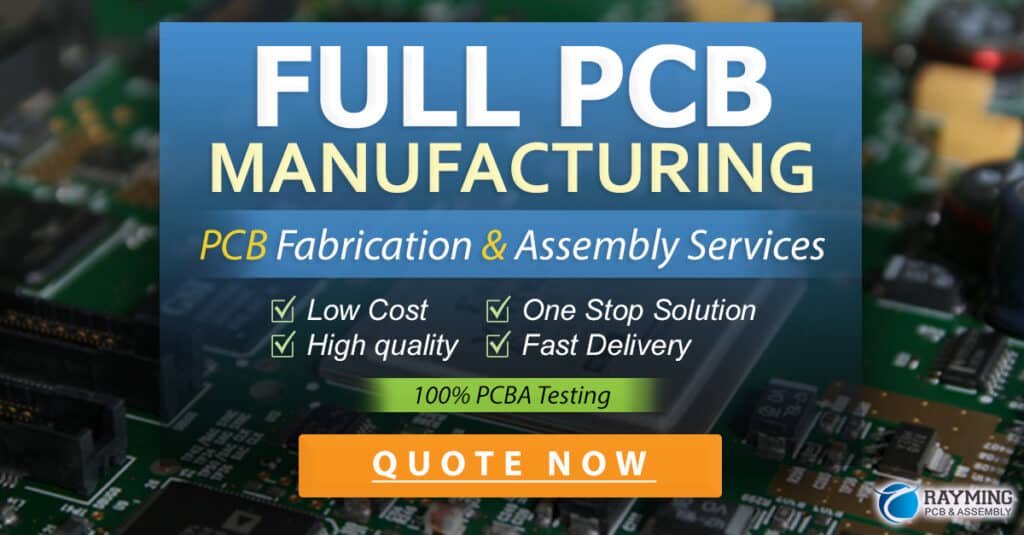
Preparing Your Design Files for PCBA
To ensure a smooth and successful PCB assembly process, prepare your design files accurately:
-
Gerber files: Provide complete and accurate Gerber files, which include information about the PCB Layers, drill holes, and solder mask.
-
Bill of Materials (BOM): Create a detailed BOM that lists all the components required for your PCB, including their quantities, part numbers, and manufacturers.
-
Assembly instructions: If your PCB requires specific assembly instructions, such as component orientation or special handling, include these in your documentation.
-
CAD files: If available, provide the original CAD files (e.g., Altium, Eagle, or KiCad) to the PCBA service provider for reference.
The PCBA Process
Once you have chosen a PCBA service provider and submitted your design files, the assembly process typically follows these steps:
-
Design review: The PCBA service provider will review your design files to ensure they are complete, accurate, and suitable for assembly.
-
Component sourcing: The service provider will procure the necessary components based on your BOM.
-
PCB Fabrication: If not provided by you, the service provider will fabricate the bare PCBs according to your Gerber files.
-
Assembly: The PCBs will be assembled using the appropriate techniques, such as surface mount technology (SMT) or through-hole technology (THT).
-
Inspection and testing: The assembled PCBs will undergo various inspections and tests, such as automated optical inspection (AOI), X-ray inspection, and functional testing, to ensure quality and functionality.
-
Packaging and shipping: The assembled PCBs will be packaged and shipped to you according to your requirements.
Ordering Prototypes and Small Series
When ordering prototypes or small series, consider the following:
-
Minimum order quantity (MOQ): Some PCBA service providers may have a minimum order quantity for prototypes or small series. Ensure that the MOQ aligns with your needs.
-
Lead time: Prototype and small series orders may have longer lead times compared to mass production. Plan accordingly and communicate your timeline requirements with the service provider.
-
Design iterations: If you anticipate multiple design iterations, discuss this with your PCBA service provider to ensure they can accommodate your needs and provide quick turnaround times.
-
Testing requirements: Clearly communicate your testing requirements for prototypes and small series, as these may differ from mass production testing.
Frequently Asked Questions (FAQ)
1. What is the typical turnaround time for PCBA prototypes?
The turnaround time for PCBA prototypes can vary depending on the complexity of the design, component availability, and the service provider’s workload. Typically, prototype assembly can take anywhere from a few days to a few weeks.
2. Can I provide my own components for PCBA?
Yes, many PCBA service providers allow customers to provide their own components (known as consigned parts). However, ensure that you communicate this clearly with the service provider and provide accurate information about the components, including part numbers and quantities.
3. What is the difference between SMT and THT assembly?
Surface mount technology (SMT) involves placing components directly onto the surface of the PCB and soldering them using reflow soldering. Through-hole technology (THT) involves inserting component leads through holes in the PCB and soldering them on the opposite side. SMT is more common for modern electronics, while THT is used for larger components or when mechanical strength is required.
4. How can I ensure the quality of my assembled PCBs?
To ensure the quality of your assembled PCBs, choose a reputable PCBA service provider with relevant quality certifications and a proven track record. Clearly communicate your quality requirements and discuss the inspection and testing processes with the service provider.
5. What should I do if I receive assembled PCBs that do not meet my requirements?
If you receive assembled PCBs that do not meet your requirements, contact your PCBA service provider immediately. Provide clear documentation of the issues, including photos or videos if applicable. A reputable service provider will work with you to resolve the issue and provide a solution, such as rework, replacement, or refund, depending on the situation.
Conclusion
PCBA services are crucial for businesses and individuals who require custom-made electronic devices, prototypes, or small series production runs. By understanding the PCBA process, carefully selecting a service provider, and preparing accurate design files, you can ensure a successful and Cost-Effective PCB Assembly experience. Remember to communicate your requirements clearly and work closely with your chosen PCBA service provider throughout the process to achieve the best results.
Aspect | Consideration |
---|---|
Experience | Look for a company with a proven track record in assembling PCBs similar to your project requirements. |
Capabilities | Ensure that the service provider has the necessary equipment, expertise, and capacity to handle your project. |
Quality certifications | Choose a PCBA service provider with relevant quality certifications, such as ISO 9001, IPC-A-610, or IPC-J-STD-001. |
Customer support | Select a company that offers excellent customer support and clear communication throughout the assembly process. |
Pricing | Compare prices from multiple service providers to ensure you get the best value for your money without compromising on quality. |
By keeping these factors in mind when choosing a PCBA service provider, you can ensure a successful collaboration and high-quality assembled PCBs for your projects.
No responses yet