Understanding the Inner PCB Layer
Printed Circuit Boards (PCBs) are essential components in modern electronic devices. They provide a platform for mounting and interconnecting various electronic components, such as resistors, capacitors, and integrated circuits. While the Outer Layers of a PCB are visible and often contain the majority of the components, the inner layers play a crucial role in the overall functionality and performance of the board. In this article, we will delve into the inner layer of a PCB, exploring its purpose, composition, and manufacturing process.
What is an Inner PCB Layer?
An inner PCB layer, also known as an internal layer or buried layer, is a conductive layer located between the top and bottom layers of a multi-layer PCB. These layers are not visible from the outside and are sandwiched between the outer layers. The number of inner layers in a PCB can vary depending on the complexity and requirements of the design, ranging from two to several dozen layers.
The primary purpose of inner PCB layers is to provide additional routing paths for electrical signals and power distribution. By utilizing the inner layers, designers can create more complex and compact PCB designs, allowing for higher component density and improved signal integrity.
Composition of Inner PCB Layers
Inner PCB layers are typically made of copper, a highly conductive material that allows for efficient electrical signal transmission. The copper layer is laminated onto a dielectric substrate, such as FR-4, which provides insulation and mechanical support. The thickness of the copper layer can vary depending on the current carrying requirements and the desired impedance of the traces.
The dielectric substrate used for inner layers is usually thinner compared to the outer layers. This allows for closer spacing between the layers, enabling higher routing density and reducing the overall thickness of the PCB.
Manufacturing Process of Inner PCB Layers
The manufacturing process of inner PCB layers involves several steps to ensure precise and reliable fabrication. Here is an overview of the key steps involved:
-
Layer Stack-up Design: The first step is to design the layer stack-up, which defines the arrangement and thickness of the copper and dielectric layers. The stack-up design takes into account factors such as signal integrity, impedance control, and manufacturability.
-
Inner Layer Etching: Once the layer stack-up is finalized, the inner layers are etched using a photolithography process. The copper layer is coated with a photoresist material, and the desired circuit pattern is exposed using UV light through a photomask. The exposed areas are then chemically etched away, leaving the desired copper traces.
-
Lamination: After etching, the inner layers are laminated together with the dielectric substrate using heat and pressure. This process bonds the layers together, forming a solid and stable structure.
-
Drilling: Holes are drilled through the laminated layers to create vias, which are used to interconnect the different layers of the PCB. The drilling process is precisely controlled to ensure accurate hole placement and size.
-
Plating: The drilled holes are then plated with copper to create a conductive path between the layers. This process is known as through-hole plating and ensures reliable electrical connections.
-
Outer Layer Processing: Once the inner layers are fabricated and interconnected, the outer layers are added to the PCB. This involves applying a Copper Foil to the top and bottom surfaces, etching the desired circuit patterns, and applying a protective solder mask and silkscreen.
Benefits of Using Inner PCB Layers
Using inner layers in PCB design offers several advantages, including:
-
Increased Routing Density: Inner layers provide additional routing space, allowing for more complex and compact designs. This is particularly beneficial in high-density PCBs where a large number of components need to be interconnected within a limited area.
-
Improved Signal Integrity: By utilizing inner layers, designers can optimize the routing of critical signals, such as high-speed digital signals or sensitive analog signals. The inner layers provide shielding and isolation from external noise sources, reducing crosstalk and electromagnetic interference (EMI).
-
Enhanced Power Distribution: Inner layers can be used for power distribution, providing low-impedance paths for power and ground planes. This helps in minimizing voltage drops, reducing noise, and improving the overall power integrity of the PCB.
-
Reduced PCB Thickness: By using inner layers, designers can achieve higher routing density without increasing the overall thickness of the PCB. This is advantageous in applications where space is limited, such as in mobile devices or wearable electronics.
-
Cost-Effective for Complex Designs: While adding inner layers to a PCB increases the manufacturing cost, it can be a cost-effective solution for complex designs. The use of inner layers eliminates the need for multiple separate PCBs, reducing the overall assembly and integration costs.
Challenges and Considerations
While inner PCB layers offer numerous benefits, there are also challenges and considerations to keep in mind during the design and manufacturing process:
-
Layer Stack-up Design: Designing an optimal layer stack-up requires careful consideration of factors such as signal integrity, impedance control, and manufacturability. Designers need to ensure proper spacing between layers, match the dielectric constants of the materials, and consider the manufacturing capabilities of the PCB fabricator.
-
Signal Integrity Analysis: As PCBs become more complex and operate at higher frequencies, signal integrity analysis becomes crucial. Designers need to simulate and analyze the behavior of signals in the inner layers, considering factors such as crosstalk, impedance discontinuities, and signal reflections.
-
Thermal Management: Inner layers can contribute to the overall thermal performance of the PCB. Designers need to consider the thermal conductivity of the dielectric materials and the placement of power-dissipating components to ensure proper heat dissipation and avoid thermal issues.
-
Manufacturing Limitations: The manufacturing process for inner layers has certain limitations that need to be considered during the design phase. Factors such as minimum trace width, spacing, and hole size should adhere to the manufacturing capabilities of the PCB fabricator to ensure successful fabrication.
-
Testing and Inspection: Testing and inspecting inner layers can be challenging since they are not directly accessible from the outside. Special techniques, such as X-ray inspection or electrical testing, may be required to verify the integrity and functionality of the inner layers.
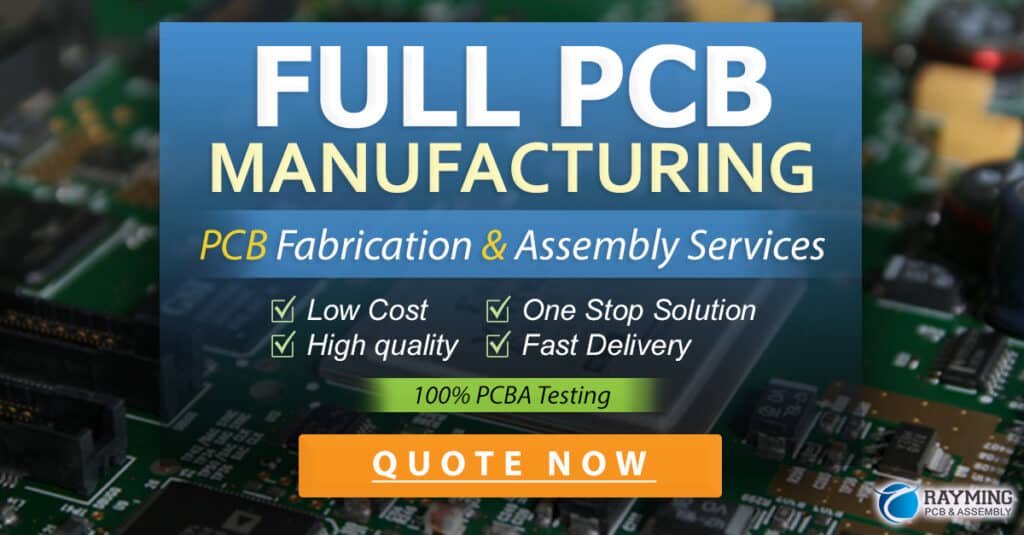
Frequently Asked Questions (FAQ)
-
What is the purpose of inner PCB layers?
Inner PCB layers provide additional routing paths for electrical signals and power distribution, allowing for more complex and compact PCB designs. They enable higher component density, improved signal integrity, and enhanced power distribution. -
How many inner layers can a PCB have?
The number of inner layers in a PCB can vary depending on the complexity and requirements of the design. PCBs can have anywhere from two to several dozen inner layers, with the most common configurations being four, six, or eight layers. -
What materials are used for inner PCB layers?
Inner PCB layers are typically made of copper, which is a highly conductive material. The copper layer is laminated onto a dielectric substrate, such as FR-4, which provides insulation and mechanical support. -
How are inner PCB layers interconnected?
Inner PCB layers are interconnected through vias, which are conductive paths that connect different layers of the PCB. Vias are created by drilling holes through the laminated layers and plating them with copper to establish electrical connections between the layers. -
Are there any challenges in designing and manufacturing inner PCB layers?
Yes, there are challenges and considerations to keep in mind when designing and manufacturing inner PCB layers. These include designing an optimal layer stack-up, conducting signal integrity analysis, managing thermal performance, adhering to manufacturing limitations, and testing and inspecting the inner layers.
Conclusion
Inner PCB layers play a crucial role in the functionality and performance of modern electronic devices. By providing additional routing paths and power distribution, inner layers enable more complex and compact PCB designs, improved signal integrity, and enhanced power management. Understanding the composition, manufacturing process, benefits, and challenges associated with inner PCB layers is essential for designers and engineers working on advanced PCB projects.
As technology continues to advance and electronic devices become more sophisticated, the importance of inner PCB layers will only grow. By leveraging the capabilities of inner layers and addressing the associated challenges, designers can create highly optimized and reliable PCBs that meet the demanding requirements of today’s electronic applications.
Layer Type | Description |
---|---|
Signal Layer | Used for routing electrical signals between components |
Power Layer | Provides power distribution to components on the PCB |
Ground Layer | Serves as a reference plane and provides shielding |
Mixed Layer | Combines signal routing and power/ground distribution |
Table: Common Types of Inner PCB Layers
Material | Dielectric Constant | Loss Tangent | Thermal Conductivity (W/mK) |
---|---|---|---|
FR-4 | 4.2 – 4.5 | 0.02 | 0.3 |
Rogers 4003C | 3.38 | 0.0027 | 0.71 |
Isola I-Tera | 3.45 | 0.0031 | 0.52 |
Nelco N4000-6 | 3.7 | 0.007 | 0.4 |
Table: Common Dielectric Materials for Inner PCB Layers
By understanding the intricacies of inner PCB layers and leveraging their capabilities, designers and engineers can create highly optimized and reliable PCBs that power the electronic devices of tomorrow.
No responses yet