Introduction to PCB+Thickness”>PCB Thickness
Printed Circuit Board (PCB) thickness is a crucial factor in the design and manufacturing of electronic devices. It plays a significant role in determining the overall performance, reliability, and durability of the PCB. In this comprehensive article, we will delve into the intricacies of PCB thickness, exploring its importance, factors affecting it, and the various standards and considerations involved in choosing the right thickness for your PCB project.
Why PCB Thickness Matters
Mechanical Strength and Durability
One of the primary reasons PCB thickness is so important is its impact on the mechanical strength and durability of the board. Thicker PCBs are generally more robust and can withstand greater physical stress and vibrations. This is particularly crucial in applications where the PCB is subject to harsh environments or high levels of mechanical stress, such as in automotive, aerospace, or industrial settings.
Electrical Performance
PCB thickness also influences the electrical performance of the board. Thicker PCBs have lower electrical resistance, which can be beneficial for high-current applications. However, thicker boards may also have higher capacitance and inductance, which can affect signal integrity and high-frequency performance. Striking the right balance between thickness and electrical characteristics is essential for optimal PCB Design.
Thermal Management
The thickness of a PCB can also impact its thermal management capabilities. Thicker boards have a greater capacity to dissipate heat, which is critical in high-power applications or when dealing with components that generate significant amounts of heat. Adequate PCB thickness helps prevent overheating and ensures the long-term reliability of the electronic components.
Factors Affecting PCB Thickness
Number of Layers
One of the primary factors that determine PCB thickness is the number of layers in the board. As the number of layers increases, so does the overall thickness of the PCB. Each additional layer requires its own substrate material and Copper Foil, contributing to the total thickness. The table below shows the typical thickness ranges for different numbers of layers:
Number of Layers | Typical Thickness Range |
---|---|
1-2 | 0.4mm – 0.8mm |
4 | 0.8mm – 1.6mm |
6 | 1.2mm – 2.4mm |
8 | 1.6mm – 3.2mm |
10+ | 2.0mm – 4.0mm |
Copper Weight
The weight of the copper used in the PCB layers also affects the overall thickness. Copper weight is typically measured in ounces per square foot (oz/ft²). Common copper weights include 0.5 oz/ft², 1 oz/ft², and 2 oz/ft². Heavier copper weights result in thicker copper layers, which contribute to the total PCB thickness.
Substrate Material
The choice of substrate material also plays a role in determining PCB thickness. The most common substrate material is FR-4, a glass-reinforced epoxy laminate. Other materials, such as polyimide or PTFE, may be used for specific applications. The thickness of the substrate material varies depending on the manufacturer and the specific grade of the material.
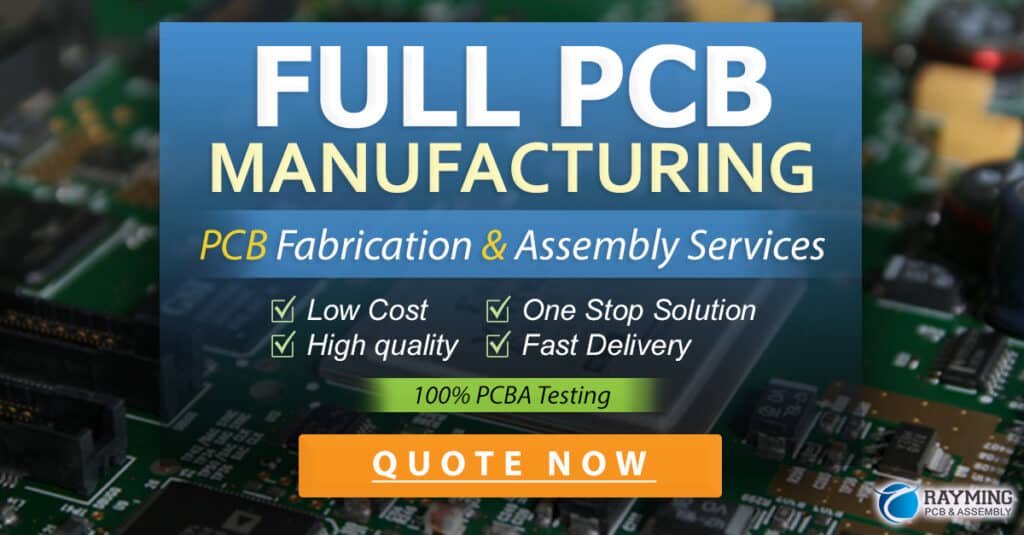
PCB Thickness Standards
IPC Standards
The IPC (Association Connecting Electronics Industries) is a global trade association that develops standards for the electronic interconnect industry. IPC standards provide guidelines for PCB design, manufacturing, and quality control. IPC-2221, IPC-6012, and IPC-4101 are some of the key standards that address PCB thickness.
- IPC-2221: Generic Standard on Printed Board Design
- IPC-6012: Qualification and Performance Specification for Rigid Printed Boards
- IPC-4101: Specification for Base Materials for Rigid and Multilayer Printed Boards
These standards specify the allowable thickness ranges, tolerances, and other requirements for different classes of PCBs based on their intended application and performance level.
Industry-Specific Standards
In addition to IPC standards, various industries may have their own specific standards or requirements for PCB thickness. For example:
- Automotive: AEC-Q100 (Stress Test Qualification for Integrated Circuits)
- Medical: ISO 13485 (Medical Devices – Quality Management Systems)
- Military: MIL-PRF-31032 (Printed Circuit Board/Printed Wiring Board, General Specification For)
These industry-specific standards ensure that PCBs meet the unique demands and reliability requirements of their respective applications.
Choosing the Right PCB Thickness
Design Considerations
When selecting the appropriate PCB thickness for your project, several design considerations come into play:
-
Mechanical Requirements: Consider the mechanical stresses and environmental conditions the PCB will be subjected to. Thicker boards may be necessary for applications with high vibration or impact levels.
-
Electrical Requirements: Evaluate the electrical performance needs of your design. High-current or high-frequency applications may require specific thickness considerations to ensure optimal signal integrity and power delivery.
-
Component Placement: The thickness of the PCB should accommodate the mounting and placement of components. Ensure that the chosen thickness allows for proper component fit and clearance.
-
Manufacturing Constraints: Consult with your PCB manufacturer to understand any limitations or constraints related to PCB thickness. Some manufacturing processes may have specific thickness requirements or limitations.
Cost Implications
PCB thickness also has cost implications. Generally, thicker PCBs are more expensive to manufacture due to the increased material usage and processing time. However, it’s important to balance cost with the necessary performance and reliability requirements. In some cases, investing in a thicker PCB can lead to long-term cost savings by improving product durability and reducing field failures.
FAQ
-
Q: What is the most common PCB thickness?
A: The most common PCB thickness is 1.6mm (0.063 inches). This thickness is widely used in many applications and offers a good balance between mechanical strength and cost. -
Q: Can I use different thicknesses for different layers in a Multilayer PCB?
A: Yes, it is possible to use different thicknesses for different layers in a multilayer PCB. This is known as a “hybrid” or “asymmetric” stackup. However, it requires careful design and manufacturing considerations to ensure proper layer registration and reliability. -
Q: How does PCB thickness affect impedance control?
A: PCB thickness plays a role in impedance control. Thicker dielectric layers between copper layers can help maintain consistent impedance values. The thickness of the copper layers themselves also influences impedance. Careful design and material selection are necessary to achieve the desired impedance characteristics. -
Q: Are there any limitations on how thick a PCB can be?
A: While there is no absolute limit on PCB thickness, practical considerations come into play. Extremely thick PCBs may face manufacturing challenges, such as difficulty in drilling through-holes or maintaining layer registration. Additionally, thick PCBs may have limitations in terms of flexibility and weight. -
Q: How can I determine the appropriate PCB thickness for my project?
A: Determining the appropriate PCB thickness involves considering various factors such as mechanical requirements, electrical performance, component placement, and manufacturing constraints. It’s recommended to consult with experienced PCB designers and manufacturers who can provide guidance based on your specific project requirements.
Conclusion
PCB thickness is a critical aspect of PCB design and manufacturing. It influences the mechanical strength, electrical performance, and thermal management of the board. Understanding the factors that affect PCB thickness, such as the number of layers, copper weight, and substrate material, is essential for making informed design decisions.
Industry standards, such as those developed by IPC, provide guidelines and specifications for PCB thickness based on different application requirements. Additionally, industry-specific standards may impose further requirements to ensure the reliability and performance of PCBs in specific sectors.
When choosing the appropriate PCB thickness for your project, consider the design requirements, cost implications, and manufacturing constraints. Striking the right balance between these factors is key to achieving a reliable, high-performing PCB that meets the needs of your application.
By understanding the complex story of PCB thickness, designers and manufacturers can make informed decisions that optimize the performance, reliability, and cost-effectiveness of their electronic products. As technology continues to advance, staying up-to-date with the latest trends, standards, and best practices in PCB thickness will be crucial for success in the ever-evolving world of electronics.
No responses yet