Introduction to Layer Etching
Layer etching is a process used in the manufacturing of printed circuit boards (PCBs) and other electronic components. It involves the selective removal of specific layers of material from a substrate to create desired patterns or features. In this article, we will explore the concept of outer layer etching, its applications, techniques, and the advantages it offers in the production of high-quality electronic devices.
What is a PCB?
Before diving into the details of outer layer etching, let’s briefly discuss what a PCB is. A printed circuit board is a flat board made of insulating material, such as fiberglass or plastic, with conductive pathways printed or etched onto its surface. These pathways, known as traces, connect various electronic components mounted on the board, allowing for the flow of electrical signals and power.
PCBs are essential components in virtually all modern electronic devices, ranging from smartphones and computers to medical equipment and automotive systems. They provide a compact and efficient means of interconnecting electronic components, enabling the creation of complex circuits in a relatively small space.
The Role of Layer Etching in PCB Manufacturing
Layer etching plays a crucial role in the manufacturing process of PCBs. It allows for the precise removal of unwanted conductive material from the substrate, leaving behind the desired circuit pattern. This process is typically performed on the outer layers of a PCB, hence the term “outer layer etching.”
The outer layers of a PCB are the top and bottom surfaces of the board, which are exposed to the environment and often contain the majority of the components and connections. By selectively etching these layers, manufacturers can create the necessary conductive paths and pads for component placement and soldering.
Techniques for Outer Layer Etching
There are several techniques used for outer layer etching in PCB manufacturing. Each method has its own advantages and limitations, and the choice of technique depends on factors such as the desired feature size, material compatibility, and production volume. Let’s explore some of the most common outer layer etching techniques.
Subtractive Etching
Subtractive etching is the most widely used method for outer layer etching in PCB manufacturing. It involves the selective removal of unwanted conductive material from a fully covered substrate. The process typically follows these steps:
-
Photoresist Application: A photosensitive material, known as photoresist, is applied to the surface of the substrate. This material hardens when exposed to light.
-
Exposure: The photoresist-coated substrate is exposed to light through a photomask, which contains the desired circuit pattern. The areas of the photoresist that are exposed to light become hardened, while the unexposed areas remain soluble.
-
Development: The substrate is then subjected to a development process, where the unexposed photoresist is removed, leaving behind the hardened photoresist in the desired pattern.
-
Etching: The substrate is immersed in an etching solution, typically an acidic or alkaline solution, which selectively removes the exposed conductive material. The hardened photoresist acts as a protective mask, preventing the removal of the desired circuit pattern.
-
Stripping: Once the etching process is complete, the remaining photoresist is stripped away, revealing the final etched circuit pattern on the substrate.
Subtractive etching offers several advantages, including high precision, compatibility with a wide range of materials, and the ability to produce fine features. However, it does have some limitations, such as the potential for over-etching or undercutting of features, and the generation of waste materials from the etching process.
Additive Etching
Additive etching, also known as pattern plating or semi-additive process (SAP), is an alternative method for outer layer etching. Unlike subtractive etching, which removes unwanted material from a fully covered substrate, additive etching selectively deposits conductive material onto a bare substrate to form the desired circuit pattern. The process typically involves the following steps:
-
Seed Layer Deposition: A thin layer of conductive material, such as copper, is deposited onto the bare substrate. This seed layer serves as a foundation for the subsequent plating process.
-
Photoresist Application: A photoresist is applied to the seed layer and exposed to light through a photomask, similar to the subtractive etching process. The exposed areas of the photoresist become hardened, while the unexposed areas remain soluble.
-
Development: The unexposed photoresist is removed during the development process, exposing the seed layer in the desired circuit pattern.
-
Plating: The substrate is then subjected to an electroplating process, where additional conductive material is selectively deposited onto the exposed seed layer. This results in the buildup of the desired circuit pattern.
-
Photoresist Stripping: The remaining photoresist is stripped away, leaving behind the plated circuit pattern on the substrate.
-
Seed Layer Etching: Finally, the exposed seed layer is etched away, isolating the individual circuit features.
Additive etching offers several advantages over subtractive etching, including the ability to produce finer features, reduced material waste, and improved adhesion between the conductive material and the substrate. However, it does require additional processing steps and may have limitations in terms of material compatibility and production throughput.
Laser Etching
Laser etching is a relatively newer technique for outer layer etching in PCB manufacturing. It utilizes a high-power laser beam to selectively remove conductive material from the substrate. The process typically involves the following steps:
-
Laser Ablation: A focused laser beam is directed onto the substrate, selectively vaporizing or ablating the conductive material in the desired circuit pattern. The laser beam is controlled by a computer-aided design (CAD) file containing the circuit layout.
-
Cleaning: After laser ablation, the substrate is cleaned to remove any debris or residue generated during the etching process.
Laser etching offers several advantages, including high precision, fast processing times, and the ability to produce fine features. It also eliminates the need for photoresists and etching solutions, reducing material waste and environmental impact. However, laser etching may have limitations in terms of material compatibility and the potential for thermal damage to the substrate.
Applications of Outer Layer Etching
Outer layer etching finds applications in various aspects of PCB manufacturing and electronic component production. Some of the key applications include:
Circuit Patterning
The primary application of outer layer etching is the creation of conductive circuit patterns on PCBs. By selectively removing unwanted conductive material, manufacturers can create the necessary traces, pads, and interconnects that form the backbone of an electronic circuit.
Component Footprints
Outer layer etching is also used to create component footprints on PCBs. These footprints are the specific patterns and pads designed to accommodate the mounting and soldering of electronic components, such as resistors, capacitors, and integrated circuits (ICs). Precise etching ensures accurate component placement and reliable electrical connections.
Solder Mask Openings
Solder mask is a protective layer applied to the surface of a PCB, covering the areas that do not require soldering. Outer layer etching is used to create openings in the solder mask, exposing the underlying pads and traces where components will be soldered. These openings, known as solder mask openings (SMOs), are critical for ensuring proper soldering and preventing short circuits.
Text and Symbols
Outer layer etching can also be used to create text, symbols, and logos on the surface of a PCB. This is typically done for identification, branding, or informational purposes. By selectively etching these elements onto the outer layers, manufacturers can provide clear and durable markings on the PCB.
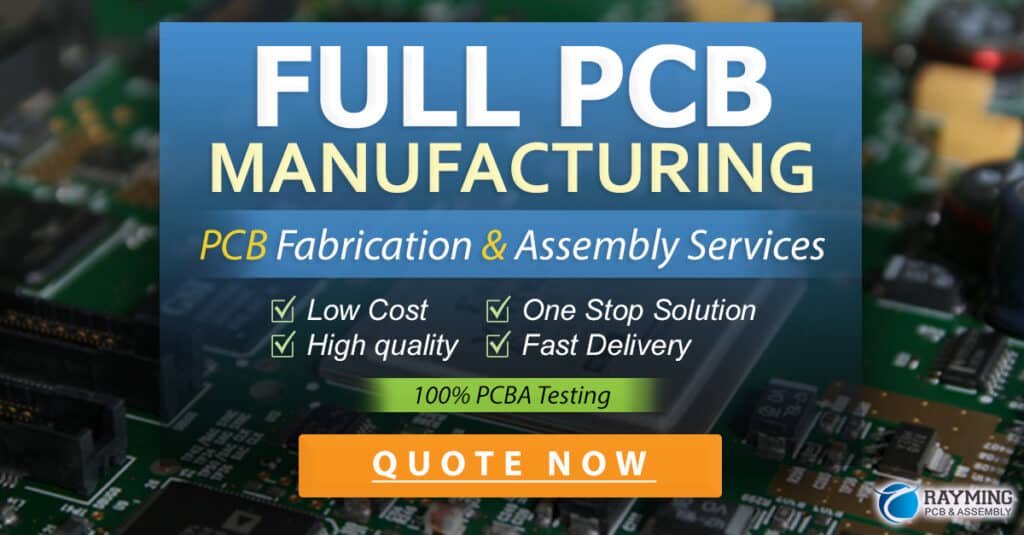
Advantages of Outer Layer Etching
Outer layer etching offers several advantages in the manufacturing of PCBs and electronic components:
High Precision
Outer layer etching techniques, such as subtractive etching and laser etching, enable the creation of highly precise circuit patterns and features. This precision is essential for producing high-density PCBs with fine pitch traces and small component footprints.
Consistency and Repeatability
Etching processes, when properly controlled, offer excellent consistency and repeatability. This means that the etched features will be uniform across multiple PCBs, ensuring reliable performance and compatibility with automated assembly processes.
Design Flexibility
Outer layer etching allows for the creation of complex and intricate circuit designs. With the ability to etch fine features and accommodate various component footprints, designers have greater flexibility in optimizing circuit layouts and maximizing functionality within a given board size.
Cost-Effectiveness
Etching techniques, particularly subtractive etching, are well-established and cost-effective for mass production of PCBs. The process can be easily scaled up to meet high-volume manufacturing requirements while maintaining consistent quality and reliability.
Challenges and Considerations
While outer layer etching offers numerous benefits, there are also some challenges and considerations to keep in mind:
Material Compatibility
Not all substrate materials are compatible with every etching technique. Some materials may be more prone to undercutting, over-etching, or thermal damage during the etching process. It is important to select the appropriate etching method based on the specifIC Substrate material and desired feature sizes.
Feature Size Limitations
Each etching technique has its own limitations in terms of the minimum feature size that can be reliably produced. Subtractive etching, for example, may have limitations in creating very fine pitch traces or small via holes. Designers need to consider these limitations when creating circuit layouts and selecting the appropriate etching method.
Environmental Concerns
Some etching processes, particularly those involving chemical solutions, can generate hazardous waste materials. Proper handling, treatment, and disposal of these waste products are essential to minimize environmental impact and comply with regulatory requirements.
Process Control and Optimization
To achieve consistent and reliable results, outer layer etching processes require careful control and optimization. Factors such as etch rates, solution concentrations, temperature, and exposure times must be closely monitored and adjusted to ensure the desired outcomes. Ongoing process control and quality assurance measures are necessary to maintain high-quality etching results.
Frequently Asked Questions (FAQs)
-
What is the difference between outer layer etching and inner layer etching?
Outer layer etching refers to the etching process performed on the top and bottom surfaces of a PCB, which are exposed to the environment and typically contain the majority of components and connections. Inner layer etching, on the other hand, refers to the etching of internal layers within a multi-layer PCB, which are not directly accessible from the surface. -
Can outer layer etching be used for Flexible PCBs?
Yes, outer layer etching can be used for flexible PCBs, which are made from flexible substrate materials such as polyimide or polyester. However, the etching process may need to be adapted to accommodate the specific properties and challenges of flexible substrates, such as their tendency to stretch or deform during processing. -
What is the minimum feature size achievable with outer layer etching?
The minimum feature size achievable with outer layer etching depends on the specific etching technique used. Subtractive etching can typically produce feature sizes down to around 50-100 microns, while additive etching and laser etching can achieve finer features, potentially down to 25 microns or less. However, the actual achievable feature size may also depend on factors such as the substrate material, etching parameters, and process control. -
How does outer layer etching impact the electrical performance of a PCB?
Outer layer etching can have a significant impact on the electrical performance of a PCB. The precision and quality of the etched features directly affect the signal integrity, Impedance Control, and overall functionality of the circuit. Poorly etched traces or inconsistent feature sizes can lead to signal reflections, crosstalk, and other issues that degrade electrical performance. Proper etching process control and adherence to design guidelines are essential for ensuring optimal electrical characteristics. -
What are the safety considerations when performing outer layer etching?
Outer layer etching processes, particularly those involving chemical solutions, can pose safety risks if not handled properly. Etching solutions may contain corrosive or toxic chemicals that can cause skin irritation, respiratory issues, or other health hazards. Proper personal protective equipment (PPE), such as gloves, goggles, and respiratory protection, should be worn when handling these materials. Adequate ventilation and proper storage and disposal of chemicals are also essential. Laser etching processes may involve high-power laser beams that can cause eye damage or burns, so appropriate safety measures and training are necessary.
Conclusion
Outer layer etching is a critical process in the manufacturing of PCBs and electronic components. It enables the creation of precise and reliable conductive patterns on the surfaces of substrates, forming the foundation for interconnecting electronic components and enabling the functionality of modern electronic devices.
Through techniques such as subtractive etching, additive etching, and laser etching, manufacturers can selectively remove or deposit conductive materials to create the desired circuit features. Each technique offers its own advantages and limitations, and the choice of method depends on factors such as the substrate material, desired feature sizes, and production requirements.
Outer layer etching finds applications in various aspects of PCB manufacturing, including circuit patterning, component footprints, solder mask openings, and text and symbols. It offers benefits such as high precision, consistency, design flexibility, and cost-effectiveness.
However, outer layer etching also presents challenges and considerations, such as material compatibility, feature size limitations, environmental concerns, and the need for careful process control and optimization. Manufacturers must address these challenges to ensure high-quality and reliable etching results.
As electronic devices continue to advance and become more complex, the importance of outer layer etching in PCB manufacturing will only continue to grow. Ongoing research and development in etching techniques, materials, and process control will be crucial for meeting the evolving demands of the electronics industry and enabling the creation of innovative and high-performance electronic products.
No responses yet