Introduction to Double-Sided PCBs
Double-sided PCBs, also known as two-layer PCBs, are printed circuit boards that have conductive copper layers on both sides of the insulating substrate. These PCBs offer several advantages over Single-Sided PCBs, including higher component density, better signal integrity, and improved electromagnetic compatibility (EMC). In this article, we will explore the types of double-sided PCBs and their manufacturing process.
Types of Double-Sided PCBs
Double-sided PCBs can be categorized into two main types based on their interconnection method:
1. Through-Hole Double-Sided PCBs
Through-hole double-sided PCBs use conductive holes, called vias, to connect the copper layers on both sides of the board. Components are mounted on one side of the board, and their leads are inserted through the vias and soldered on the opposite side. This type of PCB is suitable for applications that require high reliability and mechanical stability, such as:
- Power electronics
- Automotive systems
- Industrial control equipment
2. Surface-Mount Double-Sided PCBs
Surface-mount double-sided PCBs utilize surface-mount technology (SMT) to attach components directly onto the copper pads on both sides of the board. This technology enables the use of smaller components and higher component density compared to through-hole mounting. Surface-mount double-sided PCBs are commonly used in:
- Consumer electronics
- Telecommunications equipment
- Medical devices
Double-Sided PCB Manufacturing Process
The manufacturing process for double-sided PCBs involves several steps, each requiring precision and accuracy to ensure the quality and reliability of the final product.
1. PCB Design and Artwork Creation
The first step in double-sided PCB manufacturing is to design the PCB layout using electronic design automation (EDA) software. The design includes the placement of components, routing of traces, and the creation of vias. Once the design is complete, the artwork files are generated for each layer of the PCB.
2. PCB Fabrication
The PCB fabrication process begins with the selection of the insulating substrate material, typically FR-4. The substrate is then coated with a thin layer of copper on both sides using a process called electroless copper deposition.
Next, the copper layers are patterned using a photolithography process. The artwork files are used to create photomasks, which are then used to selectively expose the photoresist-coated copper layers to UV light. The exposed areas of the photoresist are developed and removed, leaving behind the desired copper patterns.
The exposed copper is then etched away using a chemical etching process, typically with an acidic solution. The remaining photoresist is stripped off, revealing the final copper patterns on both sides of the substrate.
3. Drilling and Plating
After the copper patterns are formed, the PCB undergoes a drilling process to create the vias and component holes. The holes are then plated with copper to establish electrical connections between the layers.
4. Solder Mask Application
A solder mask, typically green in color, is applied to the PCB to protect the copper traces from oxidation and prevent solder bridges during the assembly process. The solder mask is selectively applied, leaving the pads and vias exposed for component mounting.
5. Silkscreen Printing
The final step in PCB fabrication is the application of the silkscreen layer. This layer contains text, logos, and component identifiers that aid in the assembly process and provide useful information for technicians and users.
6. PCB Assembly
Once the PCB fabrication is complete, the components are mounted onto the board using either through-hole or surface-mount technology. Through-hole components are inserted into the vias and soldered on the opposite side, while surface-mount components are placed directly onto the pads and soldered using a reflow oven.
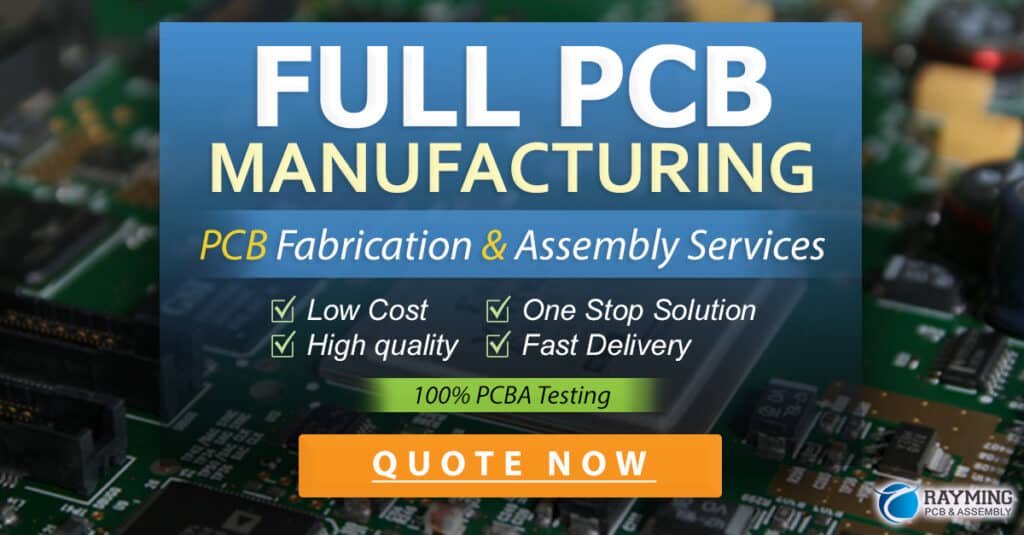
Advantages of Double-Sided PCBs
Double-sided PCBs offer several advantages over single-sided PCBs, including:
- Higher component density: Double-sided PCBs allow for more components to be placed on the same board area, reducing the overall size of the device.
- Better signal integrity: The use of vias and shorter traces in double-sided PCBs minimizes signal distortion and crosstalk, improving signal integrity.
- Improved EMC: Double-sided PCBs with proper grounding and shielding techniques can significantly reduce electromagnetic interference (EMI) and improve electromagnetic compatibility (EMC).
- Enhanced thermal management: Double-sided PCBs can dissipate heat more effectively by utilizing both sides of the board for heat-generating components and copper pours.
- Cost-effective: Although double-sided PCBs are more expensive than single-sided PCBs, they offer a better cost-to-performance ratio for more complex designs.
Challenges in Double-Sided PCB Manufacturing
Despite the many advantages of double-sided PCBs, there are some challenges associated with their manufacturing process:
- Alignment: Ensuring proper alignment between the layers during the photolithography and drilling processes is crucial for maintaining the electrical integrity of the PCB.
- Via reliability: The reliability of vias can be a concern, especially in applications with high thermal stress or mechanical strain. Proper via design and filling techniques can help mitigate these issues.
- Solder joint quality: Achieving consistent and reliable solder joints on both sides of the board can be challenging, particularly for through-hole components. Proper process control and inspection are necessary to ensure solder joint quality.
Future Trends in Double-Sided PCB Manufacturing
As technology advances, the demand for more compact, high-performance electronic devices continues to grow. To meet these demands, double-sided PCB manufacturing is evolving with new materials, processes, and technologies:
- Advanced substrate materials: The development of high-performance substrate materials, such as polyimide and ceramic, enables double-sided PCBs to operate in more demanding environments with higher temperatures and mechanical stresses.
- Embedded components: The integration of passive components, such as resistors and capacitors, within the PCB substrate itself, further increases component density and reduces the overall size of the device.
- High-density interconnect (HDI): HDI technology involves the use of microvias and fine-pitch traces to create highly compact and dense PCB designs. This technology is becoming increasingly popular in applications such as smartphones, wearables, and medical devices.
- Additive manufacturing: The use of additive manufacturing techniques, such as 3D printing, in PCB fabrication allows for the creation of complex, three-dimensional PCB Structures with embedded components and unique geometries.
FAQ
1. What is the difference between a single-sided and a double-sided PCB?
A single-sided PCB has conductive copper traces on only one side of the insulating substrate, while a double-sided PCB has copper traces on both sides of the substrate. Double-sided PCBs offer higher component density, better signal integrity, and improved EMC compared to single-sided PCBs.
2. Can double-sided PCBs be used for high-frequency applications?
Yes, double-sided PCBs can be used for high-frequency applications. However, proper design techniques, such as controlled impedance routing, shielding, and grounding, must be employed to ensure signal integrity and minimize EMI at high frequencies.
3. What is the purpose of vias in double-sided PCBs?
Vias are conductive holes that connect the copper layers on both sides of a double-sided PCB. They are used to route signals between layers, establish electrical connections for through-hole components, and provide thermal paths for heat dissipation.
4. How does the manufacturing process differ for through-hole and surface-mount double-sided PCBs?
The main difference in the manufacturing process for through-hole and surface-mount double-sided PCBs lies in the component mounting and soldering stages. Through-hole components are inserted into vias and soldered on the opposite side of the board, while surface-mount components are placed directly onto pads and soldered using a reflow oven.
5. What are the key considerations when designing a double-sided PCB?
When designing a double-sided PCB, some key considerations include:
- Component placement and routing: Optimizing component placement and routing to minimize signal path lengths, reduce crosstalk, and improve manufacturability.
- Via design: Selecting the appropriate via size, type, and location to ensure reliable electrical connections and minimize signal integrity issues.
- Power and ground planes: Incorporating power and ground planes to provide low-impedance power distribution and reduce EMI.
- Thermal management: Designing the PCB to effectively dissipate heat generated by components, using techniques such as copper pours and thermal vias.
- Manufacturing constraints: Considering the limitations and capabilities of the PCB manufacturing process, such as minimum trace widths, spacing, and hole sizes.
Conclusion
Double-sided PCBs are essential components in modern electronic devices, offering higher component density, better signal integrity, and improved EMC compared to single-sided PCBs. The manufacturing process for double-sided PCBs involves several critical steps, including PCB design, fabrication, drilling, plating, and assembly.
As technology continues to advance, double-sided PCB manufacturing is evolving to meet the demands for more compact, high-performance electronic devices. The use of advanced substrate materials, embedded components, HDI technology, and additive manufacturing techniques is driving innovation in the PCB industry.
By understanding the types, manufacturing process, advantages, and challenges of double-sided PCBs, designers and engineers can make informed decisions when developing electronic products that meet the ever-increasing demands of the market.
No responses yet