Introduction to PCB Outer Layers
A Printed Circuit Board (PCB) is a fundamental component in modern electronics, serving as the backbone for interconnecting electronic components. PCBs consist of multiple layers, with the outer layers playing a crucial role in the overall functionality and performance of the board. In this article, we will delve into the intricacies of PCB outer layers, exploring their significance, manufacturing processes, and key considerations for designers and engineers.
The Significance of Outer Layers in PCBs
The outer layers of a PCB, also known as the top and bottom layers, serve several critical functions:
-
Component Placement: The outer layers provide a surface for mounting electronic components, such as integrated circuits (ICs), resistors, capacitors, and connectors. These components are soldered onto the exposed copper pads on the outer layers, ensuring secure electrical connections.
-
Interconnections: The outer layers contain copper traces that interconnect the various components on the board. These traces are carefully designed to ensure proper signal routing, minimizing interference and maintaining signal integrity.
-
Protection: The outer layers act as a protective barrier for the internal layers of the PCB. They shield the sensitive inner layers from environmental factors such as moisture, dust, and mechanical stress.
-
Aesthetics and Identification: The outer layers often feature silkscreen printing, which includes text, logos, and component identifiers. This helps in the assembly process and provides a professional appearance to the finished product.
Manufacturing Process of PCB Outer Layers
The manufacturing of PCB outer layers involves several key steps:
1. Copper Foil Lamination
The process begins with the lamination of a thin layer of copper foil onto the base substrate material, typically FR-4 (a glass-reinforced epoxy laminate). The copper foil is bonded to the substrate using heat and pressure, creating a solid and uniform surface.
2. Photoresist Application
A photoresist, a light-sensitive material, is applied to the copper surface. This photoresist will later be used to transfer the desired circuit pattern onto the copper layer.
3. Exposure and Development
The photoresist-coated copper layer is exposed to UV light through a photomask, which contains the circuit pattern. The exposed areas of the photoresist become soluble and are removed during the development process, leaving behind the desired circuit pattern on the copper layer.
4. Etching
The exposed copper areas are etched away using a chemical solution, typically ferric chloride or ammonium persulfate. This process removes the unwanted copper, leaving only the desired circuit traces on the outer layer.
5. Photoresist Removal and Surface Finish
After etching, the remaining photoresist is removed, revealing the final copper circuit pattern. A surface finish, such as HASL (Hot Air Solder Leveling), ENIG (Electroless Nickel Immersion Gold), or OSP (Organic Solderability Preservative), is applied to protect the exposed copper and enhance solderability.
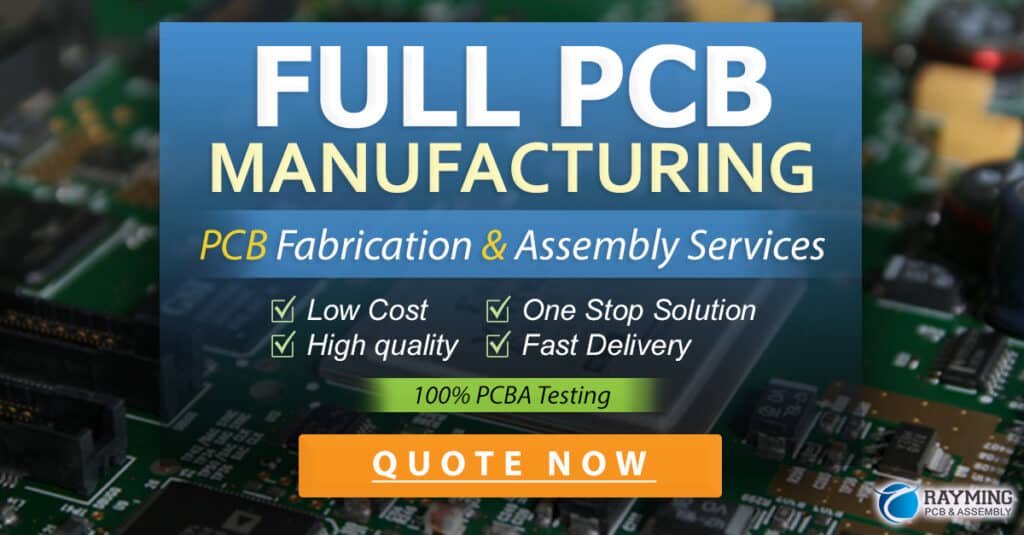
Design Considerations for Outer Layers
When designing the outer layers of a PCB, several key factors must be considered:
-
Trace Width and Spacing: The width and spacing of the copper traces on the outer layers must be carefully calculated based on the electrical requirements, such as current carrying capacity and Impedance Control. Proper trace sizing ensures reliable signal transmission and prevents issues like signal integrity problems or excessive heat generation.
-
Component Placement: The placement of components on the outer layers should be optimized for manufacturability, signal integrity, and thermal management. Proper component placement minimizes signal path lengths, reduces crosstalk, and facilitates efficient heat dissipation.
-
Via Placement: Vias, which are small holes drilled through the PCB Layers to establish electrical connections between layers, must be strategically placed on the outer layers. Via placement should consider signal integrity, manufacturability, and reliability factors.
-
Copper Pour and Grounding: Copper pour, also known as ground planes or power planes, are large areas of copper on the outer layers that provide a low-impedance path for ground or power connections. Proper copper pour design helps in reducing electromagnetic interference (EMI) and improving signal integrity.
-
Silkscreen and Labeling: The silkscreen layer on the outer layers should include clear and legible component identifiers, polarity markers, and any necessary instructions for assembly or debugging. Proper labeling helps in minimizing assembly errors and facilitates easier troubleshooting.
FAQs
-
Q: What is the difference between the top and bottom outer layers of a PCB?
A: The top and bottom outer layers of a PCB serve similar functions but may have different component placements and routing requirements based on the specific design. The top layer typically accommodates components that require user interaction or visibility, while the bottom layer may have components that are less frequently accessed or can be hidden from view. -
Q: Can the outer layers of a PCB have different thicknesses?
A: Yes, the outer layers of a PCB can have different copper thicknesses based on the electrical and mechanical requirements of the design. Thicker copper layers are often used for high-current or high-power applications, while thinner layers are suitable for signal routing and lower-power components. -
Q: What is the purpose of solder mask on the outer layers?
A: Solder mask is a protective coating applied to the outer layers of a PCB, covering the copper traces while leaving the pads exposed. The solder mask helps prevent accidental short circuits during soldering, protects the copper from oxidation and corrosion, and provides electrical insulation between adjacent traces. -
Q: How do vias connect the outer layers to the inner layers of a PCB?
A: Vias are small holes drilled through the PCB layers and plated with conductive material, typically copper. They establish electrical connections between the outer layers and the inner layers of the board. Vias allow signals and power to be routed vertically through the PCB, enabling more complex routing and interconnections between components on different layers. -
Q: What are the common surface finishes applied to the outer layers of a PCB?
A: The most common surface finishes for PCB outer layers include: - HASL (Hot Air Solder Leveling): A tin-lead alloy is applied to the exposed copper pads, providing good solderability and protection against oxidation.
- ENIG (Electroless Nickel Immersion Gold): A thin layer of nickel is plated onto the copper, followed by a layer of gold. ENIG offers excellent solderability, corrosion resistance, and a flat surface finish.
- OSP (Organic Solderability Preservative): A thin, organic compound is applied to the copper, protecting it from oxidation and enhancing solderability. OSP is a cost-effective and environmentally friendly option.
Conclusion
The outer layers of a PCB play a vital role in the overall functionality, reliability, and performance of electronic devices. Understanding the significance of outer layers, their manufacturing processes, and the key design considerations is crucial for engineers and designers working on PCB projects. By carefully designing and optimizing the outer layers, designers can ensure proper signal integrity, efficient heat dissipation, and reliable component connections. As technology advances and electronic devices become more complex, the importance of well-designed outer layers in PCBs will only continue to grow.
No responses yet