Introduction to Glass Transition Temperature
Glass transition temperature, commonly abbreviated as Tg, is a key property of polymer materials used in printed circuit boards (PCBs). It refers to the temperature range where a polymer transitions from a hard, glassy state to a soft, rubbery state.
Understanding Tg is crucial for PCB designers and manufacturers, as it impacts the performance, reliability, and processing of circuit boards. Operating a PCB above its glass transition temperature can lead to material softening, deformation, delamination, and reduced mechanical and electrical properties.
In this article, we will dive deep into glass transition temperature and its significance for PCB materials. We’ll cover:
- What happens at the glass transition
- Factors affecting Tg
- Tg of common PCB materials
- Measuring glass transition temperature
- Designing PCBs considering Tg
- Frequently asked questions about PCB glass transition temperature
By the end, you’ll have a solid grasp of this important concept and how to account for it when working with printed circuit boards.
What Happens at the Glass Transition?
Molecular Behavior
At the molecular level, polymers are made up of long chain-like molecules. These chains have some degree of flexibility and can move relative to each other. However, the extent of this motion depends on temperature.
Below the glass transition temperature, polymer chains have very limited motion. They are essentially “frozen” in place, locked into their positions by intermolecular forces. This gives the polymer a rigid, glassy character.
As temperature increases and approaches the glass transition, the polymer chains gain enough thermal energy to start moving more freely. They begin to slide past each other and rotate around their bonds. This marks the onset of the transition from glassy to rubbery behavior.
Above Tg, the polymer is in its rubbery state. Chains have a high degree of mobility and can easily deform under stress. The material becomes soft and flexible.
Changes in Properties
The glass transition is accompanied by significant changes in the polymer’s physical properties. These include:
-
Mechanical properties: Modulus (stiffness) and strength decrease dramatically as the polymer softens above Tg. Elongation and toughness may increase.
-
Thermal properties: Heat capacity and thermal expansion coefficient show a distinct change at Tg. The coefficient of thermal expansion (CTE) is typically much higher in the rubbery state.
-
Electrical properties: Dielectric constant and loss tangent may increase above Tg due to increased molecular motion.
-
Density: Specific volume increases more rapidly above Tg due to the increased free volume between mobile polymer chains.
The magnitude of these changes and the specific Tg temperature depend on the polymer type and its molecular structure. Let’s look at some of the key factors influencing glass transition temperature.
Factors Affecting Glass Transition Temperature
Molecular Weight
Polymers are made up of long chain-like molecules, and the length of these chains is described by molecular weight. Higher molecular weight means longer chains.
In general, Tg increases with increasing molecular weight. Longer chains have more intermolecular interactions and entanglements, which restrict motion and raise the temperature needed for the transition to rubbery behavior.
However, this effect is most pronounced at lower molecular weights. Once a critical molecular weight is reached, further increases have diminishing impact on Tg.
Crosslinking
Crosslinking refers to chemical bonds formed between polymer chains, creating a three-dimensional network. This is in contrast to linear or branched polymers where chains are not interconnected.
Crosslinking has a significant effect on glass transition temperature. Each crosslink acts as an anchor point restricting chain motion. More crosslinking results in a higher Tg.
In highly crosslinked polymers, like thermosetting resins used in PCBs, the glass transition is less distinct. The high degree of intermolecular bonding prevents the sharp transition to a rubbery state. Instead, properties change more gradually over a broader temperature range.
Chemical Structure
The specific chemical makeup of a polymer plays a major role in determining its Tg. Factors include:
-
Chain flexibility: Polymers with rigid, bulky side groups or aromatic rings in the backbone have higher Tg due to restricted chain motion. Flexible chains with freely rotating bonds have lower Tg.
-
Polarity: Polar groups like esters, amides, and hydroxyl groups form strong intermolecular attractions, raising Tg. Non-polar polymers have weaker interactions and lower Tg.
-
Symmetry: Regularly repeating, symmetric structures allow tighter chain packing and less free volume, increasing Tg compared to asymmetric, irregularly shaped chains.
These structural features are inherent to each polymer type and can be modified by synthesis techniques and additives. Let’s look at some common PCB materials and their characteristic glass transition temperatures.
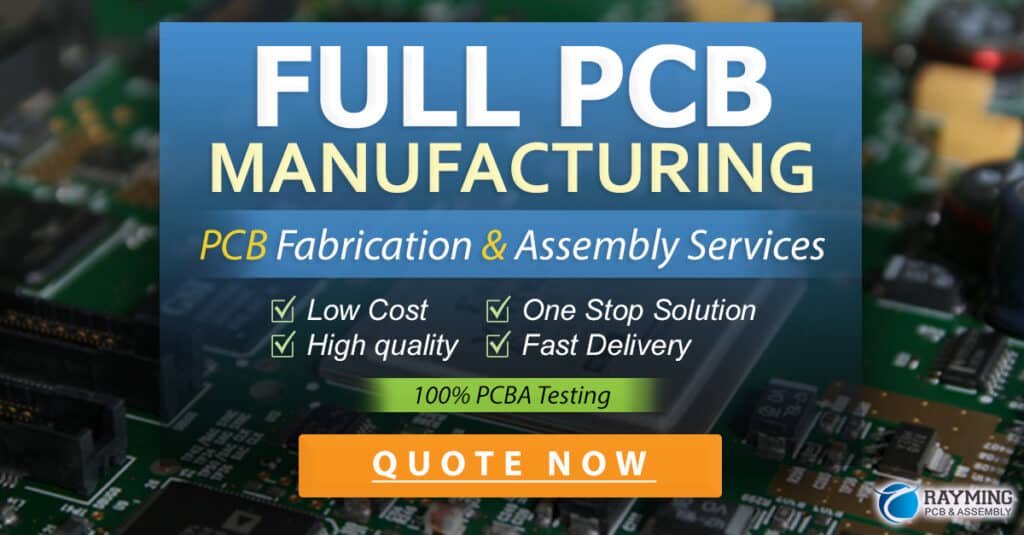
Glass Transition Temperatures of Common PCB Materials
Printed circuit boards employ a variety of polymeric materials, each with its own glass transition temperature range. Here are some of the most widely used:
FR-4 Laminate
FR-4 is the workhorse material of the PCB industry. It is a composite of woven fiberglass fabric impregnated with epoxy resin. The resin is a thermoset polymer that crosslinks during manufacturing to form a rigid, heat-resistant board.
Typical Tg values for FR-4 laminates range from 115°C to 180°C depending on the specific resin formulation and curing conditions. Standard FR-4 has a Tg around 135°C.
Polyimide
Polyimide (PI) is a high-performance polymer used in applications demanding excellent thermal stability, chemical resistance, and mechanical strength. It has a very high glass transition temperature, typically 250°C or higher.
PI’s high Tg makes it suitable for use in harsh environments and high-temperature electronics. However, it is more expensive and difficult to process than standard FR-4.
High-Tg FR-4
High-Tg FR-4 is a variant of standard FR-4 laminate with a glass transition temperature enhanced to 170°C or higher. This is achieved by using speciality epoxy resins and optimized curing cycles.
High-Tg FR-4 provides improved thermal performance and reliability compared to standard FR-4, while maintaining the ease of processing and lower cost than polyimide.
BT Epoxy
Bismaleimide-triazine (BT) epoxy is another high-performance PCB material. It offers a balance of high Tg (typically 180°C to 210°C), good processability, and moderate cost.
BT epoxy finds use in applications requiring thermal stability and high-density packaging, such as network infrastructure and Automotive Electronics.
Here is a summary table of glass transition temperatures for these common PCB materials:
Material | Typical Tg Range (°C) |
---|---|
Standard FR-4 | 115 – 135 |
High-Tg FR-4 | 170 – 180 |
Polyimide (PI) | 250+ |
BT Epoxy | 180 – 210 |
It’s important to note that these are representative values and actual Tg can vary based on specific resin chemistry, manufacturing processes, and test methods. Speaking of testing, let’s look at how glass transition temperature is measured.
Measuring Glass Transition Temperature
There are several techniques used to measure the glass transition temperature of polymers and PCB materials. The most common are:
Differential Scanning Calorimetry (DSC)
DSC is a thermal analysis technique that measures heat flow into or out of a sample as a function of temperature. It can detect the changes in heat capacity that occur at the glass transition.
In a DSC experiment, a small sample (typically a few milligrams) is placed in an aluminum pan and heated at a controlled rate, usually 10-20°C per minute. An empty reference pan is heated simultaneously. The differential heat flow between the sample and reference is measured.
At the glass transition, the sample’s heat capacity increases as it gains molecular mobility. This appears as a step change in the DSC heat flow curve. The midpoint of this step is taken as the Tg value.
DSC is the most widely used method for measuring Tg due to its simplicity, speed, and small sample size. However, it may not give a clear transition for some highly crosslinked or composite materials.
Dynamic Mechanical Analysis (DMA)
DMA measures the mechanical properties of a material as a function of temperature. It is particularly sensitive to the changes in modulus and damping that occur at the glass transition.
In DMA, a sample is subjected to a small oscillatory stress and the resulting strain is measured. This allows the calculation of the storage modulus (stiffness) and loss modulus (damping). These properties are measured while the sample is heated at a controlled rate, typically 1-5°C per minute.
At the glass transition, the storage modulus decreases sharply as the material softens. The loss modulus goes through a peak as molecular motion increases and then dissipates energy through friction.
The temperature of the peak in loss modulus is often reported as the DMA Tg. The onset of the storage modulus drop can also be used.
DMA provides more information than DSC, showing changes in both thermal and mechanical properties. It is useful for measuring Tg in composites and high-performance materials. However, it requires larger samples and more complex fixturing than DSC.
Thermomechanical Analysis (TMA)
TMA measures the dimensional changes of a sample as a function of temperature. It can detect the softening and expansion that occur at the glass transition.
In TMA, a small probe rests on the sample with a controlled force. As the sample is heated, changes in its thickness are measured by the displacement of the probe. The heating rate is typically 5-10°C per minute.
At the glass transition, the sample’s coefficient of thermal expansion increases markedly. This appears as a change in slope of the TMA thickness versus temperature curve. The intersection of the extrapolated pre- and post-transition slopes is reported as the Tg.
TMA is a simple method well-suited for measuring the Tg of films and coatings. It is also sensitive to the expansion changes in highly filled or reinforced materials. However, it does not provide as much information as DSC or DMA.
Each of these techniques has its strengths and limitations. In practice, Tg values from different methods may not always agree due to the different heating rates and property changes being measured. It’s important to specify the test method and conditions when reporting Tg values.
Designing PCBs Considering Glass Transition Temperature
Understanding and designing for the glass transition is crucial for producing reliable, high-performance PCBs. Here are some key considerations:
Material Selection
The most fundamental decision is choosing a PCB material with a Tg appropriate for the application. The operating temperature of the device should be comfortably below the material’s Tg to avoid softening and degradation.
For standard consumer electronics, FR-4 with a Tg of 135°C is usually sufficient. More demanding applications may require high-Tg FR-4, polyimide, or other speciality materials.
It’s also important to consider the processing temperatures the PCB will be exposed to during assembly and rework. The Tg should be high enough to withstand soldering and other thermal processes without deformation.
Thermal Management
Even if the nominal operating temperature is below Tg, localized heating from power components or inadequate cooling can cause the PCB to exceed its limit. Thermal simulations should be used to identify hot spots and ensure the board stays within its thermal budget.
Proper thermal management techniques, such as using Thermal Vias, heatsinks, and fans, can help dissipate heat and maintain a safe operating temperature.
Coefficient of Thermal Expansion (CTE)
The CTE mismatch between the PCB and its components can lead to mechanical stress and reliability issues, especially during thermal cycling. This is particularly critical at the glass transition, where the PCB’s CTE changes significantly.
Designers should choose PCB and component materials with closely matched CTEs to minimize stress. For example, using high-Tg FR-4 can provide a better CTE match to ceramic chip packages than standard FR-4.
Via and Pad Design
At elevated temperatures, the PCB material around vias and pads can soften and deform, leading to pad cratering, via cracking, and other defects. This is more likely to occur if the via or pad size is too large relative to the PCB thickness.
Designers should follow guidelines for minimum via and pad sizes and spacing to ensure the PCB can withstand the stresses of thermal cycling. Techniques like via-in-pad and microvia can also help improve reliability.
Conformal Coating
Applying a conformal coating to the assembLED PCB can provide an extra layer of protection against thermal and mechanical stress. The coating can help redistribute stresses and prevent delamination or cracking of the PCB material.
However, the coating material must also be chosen with its Tg in mind. A coating with a Tg lower than the PCB can soften and lose its protective properties at elevated temperatures.
By carefully considering the glass transition temperature in PCB design and material selection, engineers can ensure their boards will maintain their structural and functional integrity over the full range of operating conditions.
Frequently Asked Questions About PCB Glass Transition Temperature
What is the glass transition temperature (Tg) of FR-4?
Standard FR-4 laminate has a glass transition temperature around 135°C. However, the exact value can range from 115°C to 180°C depending on the specific resin formulation and manufacturing process. High-Tg FR-4 variants are available with Tg values of 170°C or higher.
What happens if a PCB exceeds its glass transition temperature?
Operating a PCB above its Tg can lead to a variety of problems. The board material will soften and lose its mechanical strength, potentially leading to warping, delamination, and pad cratering. The softened material is also more susceptible to thermal expansion mismatches, which can cause via and pad cracking. Electrical properties like dielectric constant and loss tangent may also degrade above Tg.
How does glass transition temperature affect PCB Assembly?
The Tg of the PCB material must be high enough to withstand the temperatures encountered during assembly processes like soldering. If the board softens during soldering, it can lead to misalignment, pad lifting, and other defects. Standard lead-free Soldering Temperatures are around 260°C, so the PCB material should have a Tg of at least 170°C to provide a safe margin.
Can the glass transition temperature of a PCB change over time?
The Tg of a PCB material can potentially decrease over time due to aging and environmental factors. Exposure to high temperatures, humidity, and chemical agents can degrade the polymer structure and lower its Tg. This is one reason why it’s important to design with a margin of safety between the operating temperature and the material’s initial Tg.
How do I choose the right PCB material based on glass transition temperature?
The key is to select a material with a Tg comfortably above the maximum expected operating temperature of the device. For most consumer electronics, standard FR-4 with a Tg around 135°C is sufficient. More demanding applications like automotive, aerospace, or high-power electronics may require high-Tg materials like polyimide or BT epoxy. It’s also important to consider the processing temperatures the board will be exposed to during assembly and rework. Consultation with your PCB fabricator can help select the best material for your specific application.
Conclusion
Glass transition temperature is a critical property for printed circuit board materials. It marks the temperature at which the polymer structure softens and properties like strength, stiffness, and expansion change significantly.
Operating a PCB above its Tg can lead to a host of reliability issues. Therefore, it’s crucial for designers to understand Tg, how it’s measured, and how it impacts PCB performance.
By selecting materials with appropriate Tg values, using proper thermal management and design techniques, and controlling processing conditions, engineers can ensure their PCBs will maintain their integrity and functionality over the full range of operating environments.
With this knowledge, you’re well-equipped to make informed decisions about glass transition temperature in your PCB designs. Keep learning, keep designing, and keep pushing the boundaries of what’s possible with printed circuit boards.
No responses yet