Introduction to LED Grow Light PCBs
LED grow lights have revolutionized the indoor farming and horticulture industry by providing an efficient and customizable lighting solution for plant growth. At the heart of these innovative lighting systems are LED Grow Light PCBs (Printed Circuit Boards), which play a crucial role in the functionality and performance of the grow lights. In this comprehensive guide, we will delve into the world of LED Grow Light PCB manufacturing, exploring the key aspects, processes, and considerations involved in creating high-quality PCBs for LED grow lights.
Understanding the Basics of LED Grow Light PCBs
What are LED Grow Light PCBs?
LED Grow Light PCBs are specialized printed circuit boards designed specifically for use in LED grow light systems. These PCBs serve as the foundation for mounting and interconnecting the various electronic components, including the LED chips, drivers, and control circuitry. The PCB provides a stable and efficient platform for power distribution and heat dissipation, ensuring optimal performance of the LED grow light.
Key Components of LED Grow Light PCBs
An LED Grow Light PCB typically consists of the following key components:
- Substrate: The base material of the PCB, usually made of FR-4 or aluminum, which provides mechanical support and electrical insulation.
- Copper Layers: Thin layers of copper foil laminated onto the substrate, which form the conductive pathways for electrical signals and power distribution.
- Solder Mask: A protective coating applied over the copper layers, leaving only the exposed pads for component soldering.
- Silkscreen: A printed layer on top of the solder mask that provides text, logos, and component identifiers for easy assembly and troubleshooting.
- LED Chips: The light-emitting diodes that produce the specific wavelengths of light required for plant growth.
- LED Drivers: Electronic components that regulate the current and voltage supplied to the LED chips, ensuring stable and efficient operation.
- Control Circuitry: Additional electronic components, such as microcontrollers, sensors, and communication modules, that enable advanced features like dimming, spectrum control, and remote monitoring.
Designing LED Grow Light PCBs
Key Considerations for PCB Design
When designing an LED Grow Light PCB, several key factors must be considered to ensure optimal performance, reliability, and manufacturability:
- LED Selection: Choose LED chips with the appropriate wavelengths and intensities for the specific plant species and growth stages.
- Thermal Management: Design the PCB layout and choose materials that facilitate efficient heat dissipation to prevent overheating and ensure long-term reliability of the LEDs.
- Power Distribution: Ensure that the PCB traces are properly sized and routed to minimize voltage drop and provide uniform current distribution to all LED chips.
- Electromagnetic Compatibility (EMC): Incorporate appropriate EMC measures, such as ground planes and filtering components, to minimize electromagnetic interference and comply with regulatory standards.
- Manufacturability: Design the PCB with consideration for manufacturing processes, such as minimum trace widths, clearances, and hole sizes, to ensure high yields and cost-effectiveness.
PCB Layout and Routing Techniques
Proper PCB layout and routing are critical for achieving optimal performance and reliability in LED Grow Light PCBs. Some key techniques include:
- Shortest Path Routing: Minimize the length of traces between components to reduce resistance and inductance, which can cause signal degradation and EMI.
- Ground Planes: Incorporate solid ground planes on one or more layers of the PCB to provide a low-impedance return path for currents and shield against electromagnetic interference.
- Thermal Relief Pads: Use thermal relief pads for LED chips and other heat-generating components to improve solderability and thermal dissipation.
- Balanced Copper Distribution: Ensure a balanced distribution of copper on each layer of the PCB to minimize warping and improve thermal stability.
- Via Placement: Place vias strategically to provide efficient interconnections between layers while minimizing signal integrity issues and manufacturing challenges.
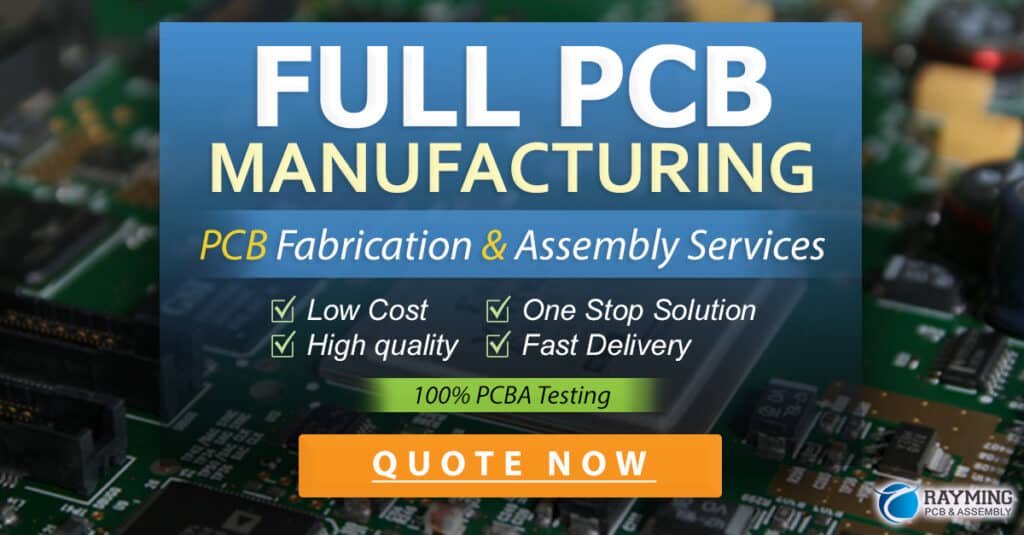
Manufacturing LED Grow Light PCBs
PCB Fabrication Process
The manufacturing process for LED Grow Light PCBs typically involves the following steps:
- Material Selection: Choose the appropriate substrate material, copper thickness, and solder mask based on the PCB design requirements.
- Imaging: Transfer the PCB design onto the copper-clad substrate using photolithography or direct imaging techniques.
- Etching: Remove the unwanted copper from the substrate using a chemical etching process, leaving only the desired conductive patterns.
- Lamination: Apply the solder mask and silkscreen layers to the etched PCB using screen printing or photoimaging techniques.
- Drilling: Drill holes in the PCB for through-hole components and vias using computer-controlled drilling machines.
- Surface Finishing: Apply a protective surface finish, such as HASL (Hot Air Solder Leveling) or ENIG (Electroless Nickel Immersion Gold), to the exposed copper pads to prevent oxidation and improve solderability.
- Electrical Testing: Perform automated optical inspection (AOI) and electrical testing to ensure the PCB meets the specified design requirements and is free of manufacturing defects.
Assembly and Testing
Once the LED Grow Light PCB is fabricated, it undergoes the following assembly and testing processes:
- SMT Assembly: Place and solder surface mount components, such as LED chips and drivers, onto the PCB using automated pick-and-place machines and reflow soldering.
- THT Assembly: Insert and solder through-hole components, such as connectors and large capacitors, onto the PCB using manual or automated insertion machines and wave soldering.
- Functional Testing: Perform comprehensive functional testing to ensure that the assembled LED Grow Light PCB operates as intended, including checks for light output, color accuracy, and power consumption.
- Burn-In Testing: Subject the assembLED PCBs to a burn-in period under controlled environmental conditions to identify any early failures or performance issues.
- Final Inspection: Conduct a final visual inspection and packaging of the assembled LED Grow Light PCBs before shipping to the customer.
Quality Control and Certifications
Quality Management Systems
To ensure consistent quality and reliability of LED Grow Light PCBs, manufacturers should implement robust quality management systems, such as:
- ISO 9001: A widely recognized standard for quality management systems that emphasizes continuous improvement, customer satisfaction, and risk management.
- IPC Standards: Industry-specific standards developed by the Association Connecting Electronics Industries (IPC) that provide guidelines for PCB design, fabrication, and assembly.
- Six Sigma: A data-driven approach to quality management that aims to minimize defects and variability in manufacturing processes.
Safety and Environmental Certifications
LED Grow Light PCBs must comply with various safety and environmental regulations to ensure safe operation and minimize ecological impact. Some key certifications include:
- UL 8750: A safety standard for LED equipment, including LED drivers and arrays, that specifies requirements for construction, testing, and marking.
- RoHS (Restriction of Hazardous Substances): A directive that restricts the use of certain hazardous substances, such as lead and mercury, in electronic and electrical products.
- REACH (Registration, Evaluation, Authorization, and Restriction of Chemicals): A regulation that aims to improve the protection of human health and the environment from the risks posed by chemicals used in manufacturing.
Advancements and Future Trends
Emerging Technologies in LED Grow Light PCBs
As the demand for more efficient and customizable LED grow light solutions continues to grow, several emerging technologies are shaping the future of LED Grow Light PCB manufacturing:
- COB (Chip-on-Board) Technology: A packaging technique that mounts multiple LED chips directly onto the PCB, enabling higher light output and better thermal management.
- Flexible PCBs: The use of flexible substrates, such as polyimide or PEEK, allows for the creation of bendable and conformable LED Grow Light PCBs that can adapt to various form factors and applications.
- Smart Lighting Control: The integration of wireless communication modules, such as Bluetooth or Wi-Fi, enables remote monitoring and control of LED grow lights through smartphones or web-based platforms.
- Spectral Tuning: The development of multi-channel LED drivers and advanced control algorithms allows for precise tuning of the light spectrum to optimize plant growth and yields.
Sustainable Manufacturing Practices
As environmental sustainability becomes an increasingly important consideration, LED Grow Light PCB manufacturers are adopting eco-friendly practices, such as:
- Lead-Free Soldering: The use of lead-free solder alloys, such as SAC (Tin-Silver-Copper), to reduce the environmental impact of PCB Assembly.
- Waste Reduction: Implementing waste reduction strategies, such as recycling of PCB substrates and solvents, to minimize the environmental footprint of the manufacturing process.
- Energy Efficiency: Optimizing manufacturing processes and equipment to reduce energy consumption and carbon emissions.
- Green Packaging: Using biodegradable and recyclable materials for packaging and shipping of LED Grow Light PCBs.
FAQ
-
What are the benefits of using LED Grow Light PCBs compared to traditional lighting solutions?
LED Grow Light PCBs offer several advantages over traditional lighting solutions, such as higher energy efficiency, longer lifespan, customizable light spectra, and reduced heat generation, making them an ideal choice for indoor plant growth applications. -
How do I choose the right LED Grow Light PCB for my specific application?
When selecting an LED Grow Light PCB, consider factors such as the plant species, growth stage, desired light intensity and spectrum, coverage area, and power requirements. Consult with LED Grow Light PCB manufacturers or horticulture experts to determine the most suitable solution for your needs. -
What is the typical lifespan of an LED Grow Light PCB?
The lifespan of an LED Grow Light PCB depends on factors such as the quality of components, thermal management, and operating conditions. High-quality LED Grow Light PCBs can last up to 50,000 hours or more, providing a long-term, reliable lighting solution for indoor plant growth. -
How can I ensure the quality and reliability of LED Grow Light PCBs?
To ensure the quality and reliability of LED Grow Light PCBs, choose manufacturers that adhere to strict quality management systems, such as ISO 9001 and IPC standards. Look for PCBs that have undergone rigorous testing and have obtained relevant safety and environmental certifications, such as UL 8750 and RoHS. -
What are the future trends in LED Grow Light PCB manufacturing?
The future of LED Grow Light PCB manufacturing is driven by advancements in technologies such as COB packaging, flexible PCBs, smart lighting control, and spectral tuning. Additionally, manufacturers are increasingly adopting sustainable practices, such as lead-free soldering and waste reduction, to minimize the environmental impact of PCB production.
Conclusion
LED Grow Light PCBs have emerged as a game-changer in the indoor farming and horticulture industry, offering a highly efficient, customizable, and reliable lighting solution for plant growth. By understanding the key aspects of LED Grow Light PCB manufacturing, from design considerations and fabrication processes to quality control and certifications, growers and horticulture professionals can make informed decisions when selecting and implementing LED grow light systems.
As the demand for sustainable and innovative plant growth solutions continues to rise, LED Grow Light PCB manufacturers are pushing the boundaries of technology and eco-friendly practices. By staying at the forefront of these advancements, the industry can continue to develop cutting-edge LED grow light solutions that optimize plant growth, reduce environmental impact, and shape the future of indoor farming.
No responses yet