What is SMT Assembly?
Surface-mount technology (SMT) assembly is a method used in electronic circuit board manufacturing where components are mounted directly onto the surface of a printed circuit board (PCB). This technique has largely replaced the through-hole technology assembly method for many applications due to its numerous advantages.
SMT assembly involves placing surface-mount devices (SMDs) onto pads or lands on the PCB surface. The components are then soldered to the board using a reflow soldering process. SMDs are much smaller than their through-hole counterparts, allowing for higher component density and more compact designs.
Advantages of SMT Assembly
- Increased component density
- Smaller PCB sizes
- Reduced manufacturing costs
- Improved performance and reliability
- Faster assembly process
SMT Assembly Process
The SMT assembly process consists of several steps, each of which is crucial to ensuring a high-quality final product.
1. Solder Paste Application
The first step in SMT assembly is applying solder paste to the PCB. Solder paste is a mixture of tiny solder balls suspended in a flux medium. The paste is applied to the PCB using a stencil printing process, where a stencil with openings corresponding to the component pads is placed over the board. The solder paste is then spread across the stencil, filling the openings and depositing the paste onto the pads.
2. Component Placement
After the solder paste is applied, the surface-mount components are placed onto the board. This is typically done using automated pick-and-place machines, which use vacuum nozzles to pick up the components from tape reels or trays and place them precisely onto the solder paste-covered pads.
Modern pick-and-place machines are highly accurate and can place thousands of components per hour, greatly increasing the speed and efficiency of the assembly process compared to manual placement.
3. Reflow Soldering
Once all the components are placed, the PCB undergoes a reflow soldering process. The board is passed through a reflow oven, which heats the solder paste to its melting point. As the solder melts, it forms a permanent electrical and mechanical connection between the components and the PCB pads.
The reflow soldering process is carefully controlled to ensure proper solder joint formation and to prevent component damage due to excessive heat exposure.
4. Inspection and Testing
After the reflow soldering process, the assembled PCBs are inspected and tested to ensure quality and functionality. Common inspection methods include:
- Visual inspection
- Automated optical inspection (AOI)
- X-ray inspection
Functional testing is also performed to verify that the assembled board operates as intended.
SMT Component Types
SMT components come in various package types, each with its own characteristics and advantages. Some common SMT component package types include:
- Chip components (resistors, capacitors)
- Small outline packages (SOPs)
- Quad flat packages (QFPs)
- Ball grid arrays (BGAs)
- Land grid arrays (LGAs)
The choice of package type depends on factors such as component function, pin count, thermal requirements, and available PCB space.
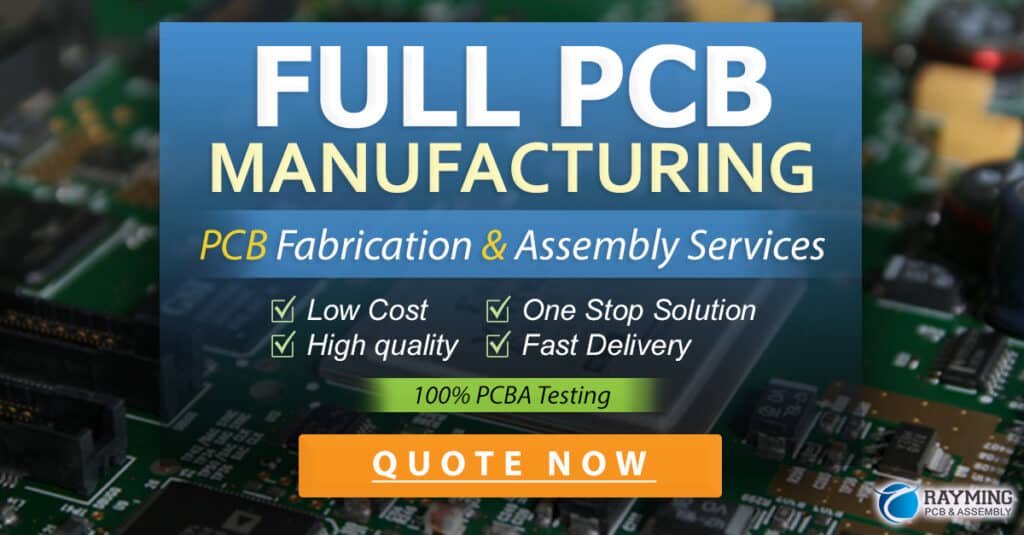
Designing for SMT Assembly
When designing a PCB for SMT assembly, several considerations must be taken into account to ensure a smooth and efficient manufacturing process:
1. Component Selection
Choose SMT components that are compatible with the assembly process and meet the design requirements. Consider factors such as package type, size, pitch, and thermal characteristics.
2. PCB Layout
Design the PCB layout with SMT assembly in mind. Ensure adequate spacing between components, provide proper pad sizes and shapes, and follow recommended design guidelines for solder joint reliability.
3. Stencil Design
Create a stencil design that ensures proper solder paste deposition on the component pads. Consider factors such as aperture size, shape, and pitch.
4. Manufacturing Feasibility
Collaborate with the SMT assembly provider to ensure that the design is manufacturable and optimized for the assembly process. Consider design for manufacturability (DFM) guidelines and incorporate feedback from the assembly team.
Benefits of Outsourcing SMT Assembly
Outsourcing SMT assembly to a specialized provider offers several benefits for electronics manufacturers:
- Access to advanced equipment and expertise
- Reduced capital investment in assembly equipment
- Faster time-to-market
- Scalability and flexibility in production volumes
- Improved product quality and reliability
When selecting an SMT assembly provider, consider factors such as experience, capabilities, quality control processes, and customer support.
Frequently Asked Questions (FAQ)
1. What is the difference between SMT and through-hole assembly?
SMT assembly involves mounting components directly onto the surface of the PCB, while through-hole assembly requires inserting component leads through holes in the board and soldering them on the opposite side. SMT assembly allows for smaller components, higher density, and faster assembly compared to through-hole.
2. Can SMT and through-hole components be used on the same PCB?
Yes, it is possible to use both SMT and through-hole components on the same PCB. This is known as a mixed-technology assembly. However, the assembly process becomes more complex and may require additional steps, such as wave soldering for through-hole components.
3. What is the smallest component size that can be used in SMT assembly?
The smallest SMT component size commonly used is 01005 (0.4mm x 0.2mm). However, the feasibility of using such small components depends on the capabilities of the SMT assembly provider and the specific design requirements.
4. How does the reflow soldering process work?
Reflow soldering involves applying heat to the PCB assembly to melt the solder paste and form permanent solder joints between the components and the board. The process typically involves a controlled temperature profile, with stages such as preheating, soak, reflow, and cooling.
5. What are some common defects in SMT assembly?
Common defects in SMT assembly include:
- Tombstoning (component standing on one end)
- Bridging (solder connecting adjacent pads)
- Insufficient or excessive solder
- Component misalignment or skewing
- Solder balls or splatter
Proper process control, inspection, and quality assurance measures help minimize the occurrence of these defects.
Defect | Description | Causes | Prevention |
---|---|---|---|
Tombstoning | Component standing on one end | Uneven heating, component imbalance | Proper pad design, balanced solder paste |
Bridging | Solder connecting adjacent pads | Excessive solder paste, improper stencil design | Optimize stencil apertures, control paste volume |
Insufficient/Excessive Solder | Too little or too much solder on joints | Incorrect solder paste volume, stencil issues | Adjust stencil design, control paste deposition |
Component Misalignment | Component not properly aligned with pads | Improper pick-and-place settings, component packaging issues | Optimize placement parameters, use high-quality components |
Solder Balls/Splatter | Small solder spheres or splatter on PCB | Excessive solder paste, improper reflow profile | Control solder paste volume, optimize reflow process |
Conclusion
SMT assembly is a crucial process in modern electronics manufacturing, offering numerous advantages over traditional through-hole assembly. By understanding the SMT assembly process, component types, design considerations, and benefits of outsourcing, electronics manufacturers can optimize their PCB designs and streamline their production processes.
Partnering with an experienced SMT assembly provider can help ensure high-quality, reliable, and cost-effective results while allowing manufacturers to focus on their core competencies and bring innovative products to market faster.
No responses yet