The Early Days of PCBs
The concept of the printed circuit board (PCB) dates back to the early 20th century. In 1903, German inventor Albert Hanson filed a patent for a crude form of PCB using flat foil conductors laminated to an insulating board. However, this early PCB was not widely adopted.
The modern PCB as we know it started to take shape in the 1930s and 1940s:
-
In 1936, Austrian engineer Paul Eisler invented the first operational printed circuit as part of a radio set while working in England.
-
During World War II, the United States developed the process of printing electrical circuits on an insulating base, advancing PCB manufacturing. PCBs played an important role in military technologies like proximity fuses in shells and mines.
-
The post-war era saw the gradual commercialization and widespread adoption of PCB technology. In 1948, the U.S. released the invention for commercial use. By 1950, the U.S. Army was working on “Auto-Sembly” technology with manufacturers to make PCBs more compact.
PCB Materials in the Early Years
The earliest PCBs used materials like Bakelite and Masonite for the insulating substrate:
Material | Properties |
---|---|
Bakelite | Phenolic resin, hard, brittle |
Masonite | Hardboard made of pressed-wood fibers |
However, these early substrate materials were eventually replaced by superior options like FR-4 fiberglass epoxy which is still widely used today for its good electrical insulation properties and mechanical strength.
The Rise of Through-Hole PCBs
In the 1950s and 1960s, through-hole construction became the dominant PCB Assembly technology. With through-hole mounting, component leads are inserted through drilled holes in the board and soldered to pads on the opposite side.
Through-Hole PCB Manufacturing Process
- Drilling holes in the substrate
- Plating the holes to form conductive barrels
- Screen printing solder paste on the pads
- Inserting components into holes
- Soldering components
Through-hole technology allowed for more complex, double-sided PCB designs compared to earlier single-sided boards where components could only be placed on one side. However, it had limitations in terms of component density and required manual assembly.
The Surface Mount Revolution
The 1980s saw the widespread adoption of surface-mount technology (SMT), which overtook through-hole as the primary PCB assembly method. With SMT, components are placed directly onto pads on the surface of the board without needing drilled holes.
Advantages of SMT over Through-Hole
- Smaller component footprints allowing for more compact designs
- Higher component density
- Faster and more automated assembly
- Lower cost
The introduction of SMT led to ever-smaller electronics and the proliferation of PCBs into countless devices and industries. Handheld gadgets like cellular phones and portable computers would not be possible without SMT PCBs.
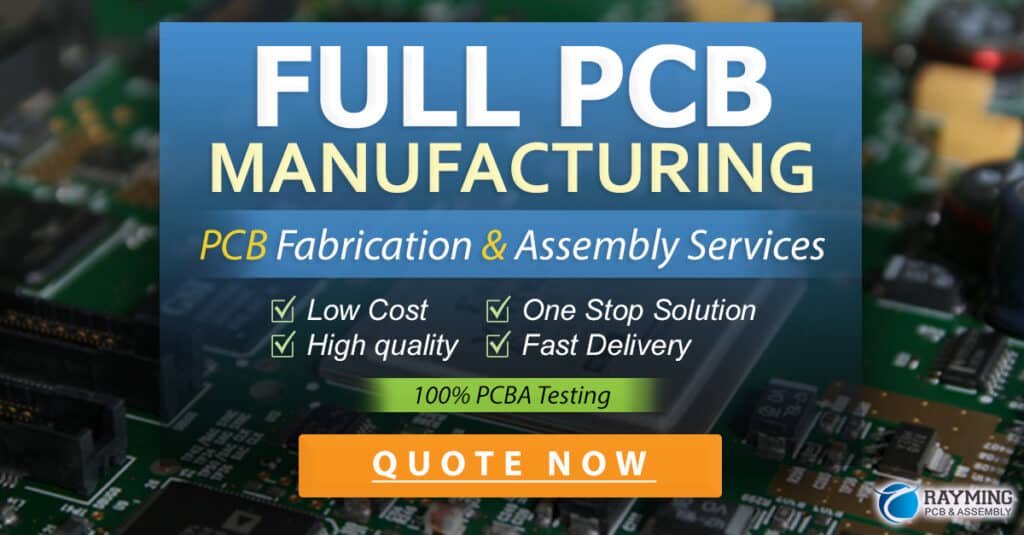
PCB Substrates and Lamination
A key development in PCB History was the copper-clad laminate. In this manufacturing process, a layer of copper foil is bonded to one or both sides of an insulating substrate, forming the basis for the conductive circuit pattern.
Common PCB Substrates Used Today
Substrate | Composition | Characteristics |
---|---|---|
FR-4 | Fiberglass and epoxy resin | Rigid, flame resistant, good insulation |
Polyimide | Polyimide film | Flexible, high heat resistance |
Teflon | PTFE fluoropolymer | Low dielectric constant, moisture resistant |
Ceramic | Ceramic material like alumina | Hard, brittle, high thermal conductivity |
The choice of laminate material depends on the specific electrical, mechanical, and environmental requirements of the end application. FR-4 fiberglass epoxy is the most common PCB substrate.
Advances in Multilayer PCBs
While double-sided PCBs became common with through-hole technology, the development of multilayer PCBs further increased circuit density and complexity. Multilayer boards consist of alternating layers of conducting copper and insulating substrates bonded together.
Multilayer PCB Manufacturing Process
- Printing and etching inner layer circuits
- Aligning and laminating layers together under heat and pressure
- Drilling holes through all layers
- Plating holes to interconnect layers
- Printing and etching outer layer circuits
Multilayer PCBs with 4, 6, 8 or more layers became increasingly common in the 1990s and 2000s for complex consumer electronics as well as high-density applications like telecommunications and aerospace systems. Modern multilayer PCB Fabrication facilities can produce boards with 50+ layers for the most advanced technologies.
Environmental Concerns and Regulations
As PCBs became ubiquitous, there was growing awareness of their environmental impact, particularly when it came to disposal of old electronics. PCBs can contain hazardous materials like lead, cadmium, and brominated flame retardants.
Significant regulations related to PCBs include:
-
The European Union’s Restriction of Hazardous Substances (RoHS) Directive, first adopted in 2003, restricted the use of certain hazardous materials in electronics, most notably lead. This spurred the development of lead-free solder alloys and components.
-
The Waste Electrical and Electronic Equipment (WEEE) Directive, also introduced in Europe in 2003, set collection, recycling and recovery targets for electrical goods to address the growing problem of e-waste.
These types of regulations have driven a trend towards “green” electronics and more environmentally friendly PCB materials and manufacturing processes. However, e-waste remains a global challenge as our consumption of PCB-based devices continues to grow.
The Future of PCBs
As electronics continue to advance, so does PCB technology. Some key trends shaping the future of PCBs include:
Miniaturization and High Density Interconnect (HDI)
The demand for ever-smaller and more powerful electronics is driving the development of HDI PCBs with finer lines and spaces, smaller vias, and higher layer counts. Advanced technologies like smartphones, wearables, and Internet of Things (IoT) devices rely on highly miniaturized PCBs.
Flexible and Stretchable PCBs
Flexible PCBs made of thin, pliable materials are seeing growing use in applications like wearable electronics, medical devices, and automotive systems. Stretchable PCBs that can conform to irregular shapes are an emerging technology for applications like soft robotics and on-skin electronics.
3D Printing of PCBs
Additive manufacturing techniques like 3D printing are being explored as a way to fabricate PCBs with unique form factors and embedded components. While still in the early stages, 3D-printed electronics have the potential to enable new design possibilities and faster prototyping.
Sustainable PCB Materials and Processes
There is ongoing research into more sustainable PCB materials and manufacturing processes to reduce environmental impact. This includes bio-based materials, recycled plastics, and alternative chemicals for plating and etching. The goal is to create a circular economy for electronics where PCBs can be more easily recycled and reused.
Frequently Asked Questions
1. What is a printed circuit board (PCB)?
A printed circuit board (PCB) is a flat board made of insulating material with conductive tracks, pads and other features etched from copper sheets laminated onto the substrate. It mechanically supports and electrically connects electronic components using conductive pathways.
2. What are the main differences between through-hole and surface-mount PCBs?
Through-hole PCBs have components with leads that are inserted into drilled holes in the board and soldered to pads on the opposite side. Surface-mount PCBs have components placed directly onto pads on the surface of the board without needing holes. Surface-mount allows for smaller components, higher density, and more automated assembly compared to through-hole.
3. What materials are PCBs typically made from?
The most common base material for rigid PCBs is FR-4, a glass-reinforced epoxy laminate. Flexible PCBs use pliable substrates like polyimide. The conductive traces are typically made of copper. Solder mask and silkscreen are applied to the outer layers for insulation and labeling.
4. How are multilayer PCBs manufactured?
Multilayer PCBs are made by laminating together multiple double-sided boards with insulating layers in between. The individual layers are aligned and bonded under heat and pressure. Holes are then drilled through the board and plated to interconnect the layers. Finally, the outer layers are printed and etched.
5. What environmental regulations apply to PCBs?
Key regulations include the European Union’s RoHS (Restriction of Hazardous Substances) Directive which restricts the use of certain hazardous materials in electronics, and the WEEE (Waste Electrical and Electronic Equipment) Directive which sets targets for collection, recycling and recovery of e-waste. Many countries have similar laws to control the environmental impact of PCBs.
Conclusion
The printed circuit board has come a long way from its origins in the early 20th century. PCB technology has continuously evolved to enable the incredible advancements in electronics we have seen over the past century, from early radios and computers to today’s smartphones, laptops, and IoT devices.
As electronics become ever more integrated into our lives, PCBs will continue to play a critical role. The future of PCBs will be shaped by trends like miniaturization, new materials, and sustainability. By understanding the history and importance of this foundational technology, we can appreciate the complex interconnected world that PCBs have created.
No responses yet