Introduction to Hand-soldering techniques
Hand-soldering is a crucial skill in the field of Electronics Manufacturing and repair. It involves the manual application of solder to create electrical connections between components on a printed circuit board (PCB). Two commonly used hand-soldering techniques are point by point soldering and mini-Wave Soldering. In this article, we will explore these techniques in detail, discussing their advantages, disadvantages, and best practices for achieving optimal results.
Understanding Point by Point Soldering
What is Point by Point Soldering?
Point by point soldering, also known as touch soldering or pencil soldering, is a hand-soldering technique where the soldering iron tip is used to heat and apply solder to individual component leads and pads on a PCB. This technique requires precision and skill, as each connection is made individually.
Advantages of Point by Point Soldering
- Flexibility: Point by point soldering allows for precise control over each solder joint, making it suitable for complex PCB Designs and rework.
- Accessibility: This technique requires minimal equipment, primarily a soldering iron and solder, making it accessible for small-scale production and repairs.
- Versatility: Point by point soldering can be used on a wide range of component types and sizes, from through-hole to surface mount components.
Disadvantages of Point by Point Soldering
- Time-consuming: Soldering each connection individually can be a slow process, especially for large PCBs with numerous components.
- Skill-dependent: The quality of solder joints heavily relies on the operator’s skill and experience, leading to potential inconsistencies.
- Fatigue: Prolonged periods of point by point soldering can cause operator fatigue, which may affect the quality of work.
Best Practices for Point by Point Soldering
- Use the appropriate soldering iron tip size and shape for the component being soldered.
- Maintain a clean and well-tinned soldering iron tip to ensure efficient heat transfer.
- Apply solder to both the component lead and the PCB pad simultaneously to create a strong bond.
- Avoid applying excessive heat or solder, as this can damage components or create bridging between adjacent pads.
- Inspect each solder joint for quality, ensuring a shiny, concave appearance and proper wetting of the component lead and PCB pad.
Exploring Mini-wave Soldering
What is Mini-wave Soldering?
Mini-wave soldering is a hand-soldering technique that mimics the process of wave soldering on a smaller scale. It involves using a specialized soldering iron with a wave-shaped tip to apply solder to multiple component leads simultaneously. This technique is particularly useful for soldering surface mount components with fine pitch leads.
Advantages of Mini-wave Soldering
- Efficiency: Mini-wave soldering allows for the soldering of multiple component leads in a single pass, reducing the time required compared to point by point soldering.
- Consistency: The wave-shaped tip ensures a consistent amount of solder is applied to each lead, resulting in more uniform solder joints.
- Reduced bridging: The controlled flow of solder in mini-wave soldering reduces the risk of bridging between adjacent leads.
Disadvantages of Mini-wave Soldering
- Equipment cost: Mini-wave soldering requires specialized Soldering Irons with wave-shaped tips, which can be more expensive than traditional soldering irons.
- Learning curve: Operators need to develop the skill and technique to effectively use mini-wave soldering, which may require additional training.
- Limited accessibility: Mini-wave soldering is more commonly used in industrial settings and may not be as readily available for small-scale production or repairs.
Best Practices for Mini-wave Soldering
- Select the appropriate wave-shaped tip size based on the component pitch and PCB design.
- Preheat the PCB and components to reduce thermal shock and improve solder flow.
- Maintain a consistent speed and angle when moving the soldering iron across the component leads.
- Use a controlled amount of solder to prevent excessive buildup or bridging.
- Clean the soldering iron tip regularly to maintain optimal performance and solder flow.
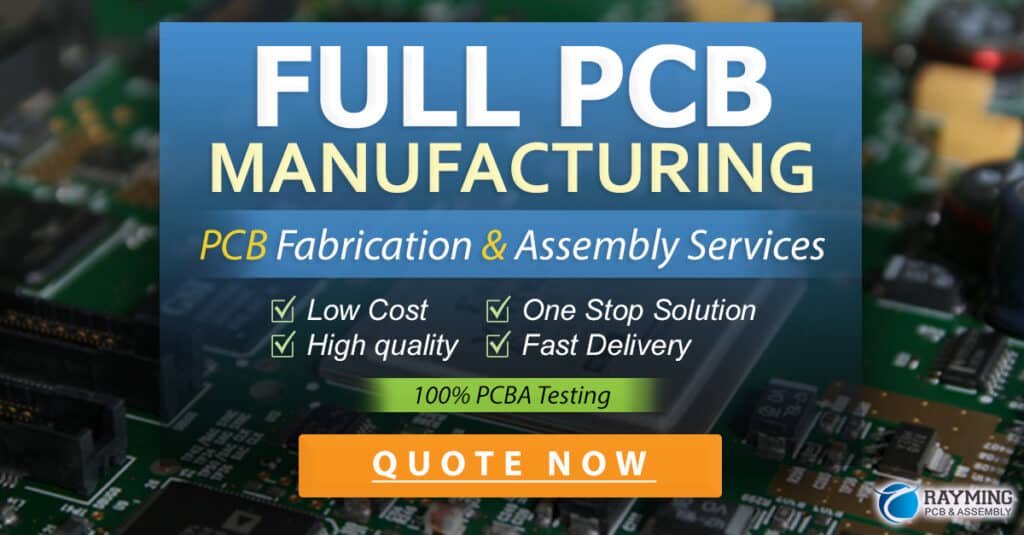
Comparing Point by Point and Mini-wave Soldering
Aspect | Point by Point Soldering | Mini-wave Soldering |
---|---|---|
Precision | High | Moderate |
Speed | Slow | Fast |
Consistency | Operator-dependent | More consistent |
Equipment Cost | Low | High |
Learning Curve | Moderate | High |
Accessibility | High | Moderate |
Versatility | High | Moderate |
Factors to Consider When Choosing a Hand-soldering Technique
When deciding between point by point soldering and mini-wave soldering, several factors should be considered:
- PCB complexity: For complex PCB designs with closely spaced components, point by point soldering may offer more precision and control.
- Production scale: Mini-wave soldering can be more efficient for larger production runs, while point by point soldering is suitable for small-scale production and repairs.
- Component types: Point by point soldering is versatile and can handle a wide range of component types, while mini-wave soldering is primarily used for surface mount components with fine pitch leads.
- Operator skill: Point by point soldering relies heavily on operator skill, while mini-wave soldering requires specific training but can provide more consistent results.
- Budget: Mini-wave soldering equipment can be more expensive than traditional soldering irons used for point by point soldering.
Frequently Asked Questions (FAQ)
-
Q: What is the main difference between point by point soldering and mini-wave soldering?
A: Point by point soldering involves soldering each component lead individually, while mini-wave soldering uses a wave-shaped tip to solder multiple leads simultaneously. -
Q: Which hand-soldering technique is faster?
A: Mini-wave soldering is generally faster than point by point soldering, as it allows for soldering multiple component leads in a single pass. -
Q: Can both through-hole and surface mount components be soldered using point by point soldering?
A: Yes, point by point soldering is versatile and can be used for both through-hole and surface mount components. -
Q: Is mini-wave soldering suitable for complex PCB designs?
A: Mini-wave soldering may not offer the same level of precision as point by point soldering for complex PCB designs with closely spaced components. -
Q: Which hand-soldering technique is more affordable in terms of equipment cost?
A: Point by point soldering requires minimal equipment, primarily a soldering iron and solder, making it more affordable compared to mini-wave soldering, which requires specialized soldering irons with wave-shaped tips.
Conclusion
Hand-soldering is an essential skill in electronics manufacturing and repair, and choosing the right technique depends on various factors such as PCB complexity, production scale, component types, operator skill, and budget. Point by point soldering offers precision, versatility, and accessibility, while mini-wave soldering provides efficiency, consistency, and reduced bridging. By understanding the advantages, disadvantages, and best practices of each technique, operators can make informed decisions and achieve optimal results in their hand-soldering projects.
No responses yet