Overview of Electronics Manufacturing
Electronics manufacturing is the process of designing, producing, and assembling electronic devices and components. This industry encompasses a wide range of products, from consumer electronics like smartphones, laptops, and televisions to industrial equipment, medical devices, and automotive electronics. The global electronics manufacturing market is expected to reach $1.5 trillion by 2025, driven by the increasing demand for consumer electronics and the adoption of advanced technologies such as 5G, IoT, and artificial intelligence.
Key Stages in Electronics Manufacturing
The electronics manufacturing process typically involves several stages:
- Design and prototyping
- Component sourcing and procurement
- PCB fabrication and assembly
- Product assembly and testing
- Packaging and distribution
Each stage requires specialized skills, equipment, and processes to ensure the quality and reliability of the final product.
Design and Prototyping
The design and prototyping phase is crucial in electronics manufacturing. This stage involves creating a detailed design of the electronic device, including its schematic, layout, and mechanical structure. Engineers use computer-aided design (CAD) software to create 2D and 3D models of the product, which are then used to create prototypes for testing and validation.
CAD Software Used in Electronics Design
Some popular CAD software used in electronics design include:
Software | Developer | Key Features |
---|---|---|
Altium Designer | Altium | PCB design, 3D modeling, simulation |
Eagle | Autodesk | Schematic capture, PCB layout, library management |
KiCad | Open-source | Schematic capture, PCB layout, 3D modeling |
OrCAD | Cadence | Schematic capture, PCB layout, simulation |
Prototyping Techniques
Prototyping techniques used in electronics manufacturing include:
- 3D printing: Creates physical models of the product using additive manufacturing techniques
- CNC Machining: Uses computer-controlled machines to create precise mechanical components
- Breadboarding: Allows for quick and easy testing of electronic circuits without soldering
- PCB Prototyping: Fabricates small batches of printed circuit boards for testing and validation
Component Sourcing and Procurement
Once the design is finalized, the next step is to source and procure the necessary components for the electronic device. This involves identifying reliable suppliers, negotiating prices, and ensuring that the components meet the required specifications and quality standards.
Key Components in Electronics Manufacturing
Some of the key components used in electronics manufacturing include:
- Semiconductors (e.g., microprocessors, memory chips, and sensors)
- Passive components (e.g., resistors, capacitors, and inductors)
- Connectors and cables
- Displays and touchscreens
- Batteries and power management systems
Supply Chain Management
Effective supply chain management is critical in electronics manufacturing to ensure the timely delivery of components and minimize disruptions. Some best practices include:
- Diversifying suppliers to reduce risk and dependence on a single source
- Implementing just-in-time (JIT) inventory management to reduce storage costs and improve efficiency
- Using supply chain analytics to monitor and optimize performance
- Establishing strong relationships with key suppliers to ensure priority and support
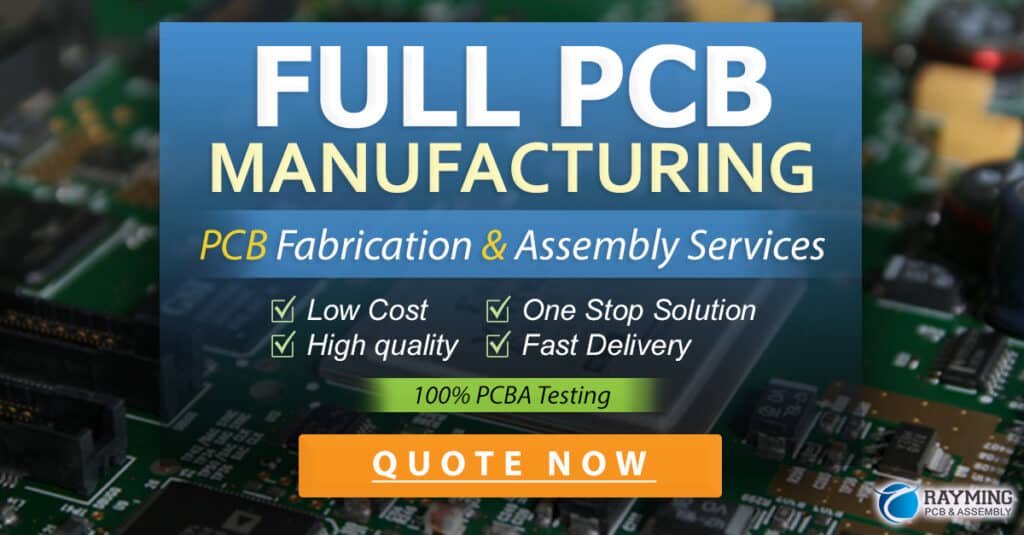
PCB Fabrication and Assembly
Printed circuit boards (PCBs) are the backbone of most electronic devices. PCB fabrication involves creating the physical board, while PCB Assembly involves soldering the components onto the board.
PCB Fabrication Process
The PCB fabrication process typically involves the following steps:
- Creating the PCB layout using CAD software
- Printing the circuit pattern onto a copper-clad substrate
- Etching away the unwanted copper to create the circuit traces
- Drilling holes for through-hole components and vias
- Applying a solder mask and silkscreen for protection and labeling
- Cutting the board to the required size and shape
PCB Assembly Techniques
PCB assembly techniques used in electronics manufacturing include:
- Through-hole assembly: Components are inserted into drilled holes and soldered onto the board
- Surface-mount assembly: Components are placed directly onto the surface of the board and soldered using reflow or wave soldering techniques
- Mixed assembly: A combination of through-hole and surface-mount components are used
Automated PCB Assembly
Automated PCB assembly using pick-and-place machines and reflow ovens has greatly improved the speed, accuracy, and consistency of the assembly process. These machines use computer vision and precision robotics to place components onto the board, which is then passed through a reflow oven to melt the solder and form a permanent connection.
Product Assembly and Testing
After the PCBs are assembled, the next step is to integrate them with other components, such as the casing, display, and battery, to create the final product. This process involves careful planning and coordination to ensure that all components fit together seamlessly and function as intended.
Assembly Line Techniques
Assembly line techniques used in electronics manufacturing include:
- Manual assembly: Workers manually assemble the components using hand tools and jigs
- Semi-automated assembly: A combination of manual and automated processes are used, such as robotic arms for repetitive tasks
- Fully automated assembly: Entire assembly process is automated using robots and conveyor systems
Testing and Quality Control
Testing and quality control are critical in electronics manufacturing to ensure that the final product meets the required specifications and performance standards. Some common testing techniques include:
- In-circuit testing (ICT): Tests the functionality of individual components and circuits on the PCB
- Functional testing: Tests the overall functionality and performance of the assembled product
- Burn-in testing: Subjects the product to elevated temperatures and voltages to identify early failures and improve reliability
- Automated optical inspection (AOI): Uses computer vision to inspect the PCB for defects and component placement errors
Packaging and Distribution
The final stage in electronics manufacturing is packaging and distribution. This involves designing and producing the packaging materials, such as boxes, manuals, and labels, and shipping the products to customers or retailers.
Packaging Design Considerations
Some key considerations in packaging design for electronics include:
- Protection: Packaging should protect the product from damage during shipping and handling
- Branding: Packaging should reflect the brand identity and attract customers
- Sustainability: Packaging should be environmentally friendly and recyclable where possible
- Regulatory compliance: Packaging should meet relevant safety and labeling requirements
Distribution Channels
Distribution channels for electronics products include:
- Direct sales: Selling directly to end customers through e-commerce or company-owned stores
- Retail partners: Selling through third-party retailers, such as electronics stores or online marketplaces
- Distributors: Selling through intermediaries who then resell to end customers or smaller retailers
- Original equipment manufacturers (OEMs): Selling to other companies who incorporate the product into their own offerings
Frequently Asked Questions (FAQ)
- What is the difference between through-hole and surface-mount PCB assembly?
-
Through-hole assembly involves inserting component leads through drilled holes in the PCB and soldering them on the opposite side, while surface-mount assembly involves placing components directly onto the surface of the PCB and soldering them using reflow or wave soldering techniques.
-
What are some common challenges in electronics manufacturing?
-
Some common challenges include managing complex supply chains, ensuring consistent quality control, keeping up with rapidly changing technologies and customer demands, and complying with various regulatory requirements.
-
How has automation impacted electronics manufacturing?
-
Automation has greatly improved the speed, accuracy, and consistency of various processes in electronics manufacturing, such as PCB assembly, testing, and packaging. It has also reduced labor costs and increased overall efficiency.
-
What are some key considerations when selecting an electronics manufacturing partner?
-
Some key considerations include their technical capabilities, quality control processes, supply chain management, flexibility and scalability, and overall cost and value proposition. It is also important to consider their location, communication, and cultural fit.
-
What are some emerging trends in electronics manufacturing?
- Some emerging trends include the adoption of Industry 4.0 technologies such as IoT, AI, and robotics, the increasing use of 3D printing and additive manufacturing, the growing demand for miniaturization and wearable devices, and the focus on sustainability and circular economy principles.
No responses yet