Introduction to Core PCB
A printed circuit board (PCB) is a fundamental component of modern electronic devices, serving as the backbone that connects and supports various electronic components. At the heart of a PCB lies its core, a crucial element that determines the board’s overall performance, durability, and reliability. In this article, we will delve into the concept of a core PCB, exploring its composition, types, manufacturing process, and the key factors to consider when selecting the right core material for your PCB project.
What is a Core PCB?
A core PCB, also known as the substrate, is the central layer of a printed circuit board. It is typically made of a dielectric material, such as fiberglass or epoxy resin, which provides a stable and insulating foundation for the copper traces and other components that make up the PCB. The core acts as a support structure, ensuring the proper placement and connectivity of the electronic components while also dissipating heat and minimizing electromagnetic interference (EMI).
Composition of a Core PCB
The most common material used for PCB cores is FR-4, a flame-retardant composite made of woven fiberglass cloth impregnated with an epoxy resin. FR-4 offers excellent mechanical and electrical properties, making it suitable for a wide range of applications. Other core materials include:
- CEM-1 and CEM-3: Composite epoxy materials with lower cost and performance compared to FR-4
- Polyimide: A high-temperature resistant material for demanding applications
- PTFE (Teflon): A low-dielectric constant material for high-frequency applications
- Aluminum: Used for metal-core PCBs (MCPCBs) to enhance heat dissipation
Types of Core PCB
PCBs can be classified based on the number of layers and the presence of a core:
- Single-layer PCB: Consists of a single conductive layer on one side of the core material
- Double-layer PCB: Features conductive layers on both sides of the core
- Multi-layer PCB: Comprises multiple conductive layers separated by insulating layers, with the core material in the center
Additionally, PCBs can be categorized based on the presence of a core:
- Rigid PCB: Has a solid, inflexible core material
- Flexible PCB: Uses a flexible core material, such as polyimide, allowing the PCB to bend and conform to various shapes
- Rigid-Flex PCB: Combines rigid and flexible sections in a single board
Manufacturing Process of a Core PCB
The manufacturing process of a core PCB involves several key steps:
-
Material Selection: Choose the appropriate core material based on the PCB’s requirements, such as thermal, electrical, and mechanical properties.
-
Lamination: Layer the core material with Copper Foils on one or both sides, applying heat and pressure to bond them together.
-
Drilling: Create holes in the laminated board for component placement and interconnections.
-
Plating: Deposit a thin layer of copper onto the drilled holes to establish electrical connections between layers.
-
Etching: Remove unwanted copper from the board’s surface, leaving only the desired circuit pattern.
-
Solder Mask Application: Apply a protective coating to the board’s surface to prevent short circuits and improve solderability.
-
Silkscreen Printing: Add text, logos, and component identifiers to the board’s surface for easy assembly and troubleshooting.
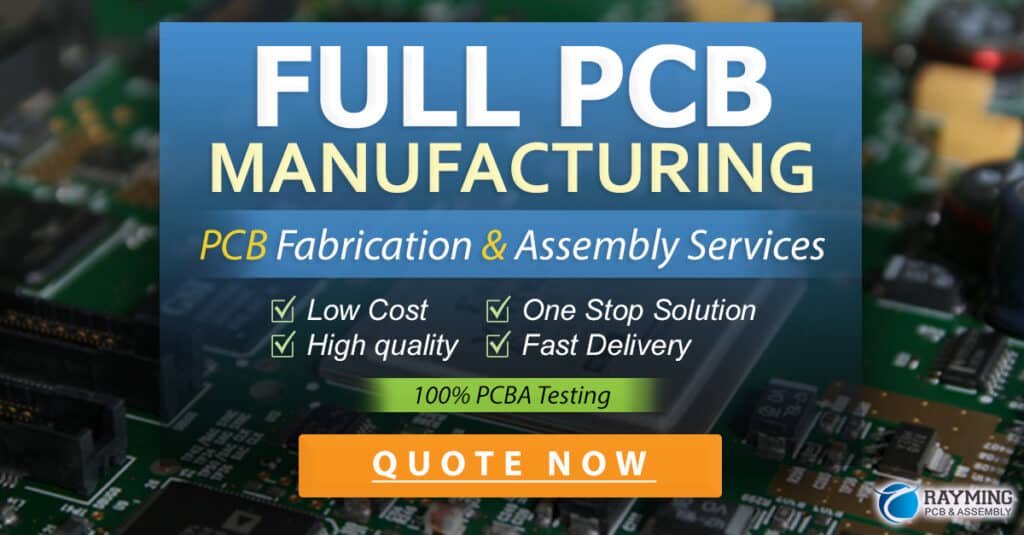
Factors to Consider When Selecting a Core PCB Material
When choosing the right core material for your PCB project, consider the following factors:
-
Dielectric Constant (Dk): A material’s ability to store electrical energy, which affects signal propagation speed and impedance.
-
Dissipation Factor (Df): The measure of a material’s power loss due to heat generation, which impacts signal integrity and power efficiency.
-
Thermal Conductivity: The material’s ability to transfer heat away from components, crucial for high-power applications.
-
Coefficient of Thermal Expansion (CTE): The rate at which a material expands or contracts with temperature changes, which can cause stress and warping if not properly managed.
-
Mechanical Strength: The material’s ability to withstand physical stress and maintain its shape during manufacturing and use.
-
Cost: The overall expense of the core material, which can vary significantly depending on its properties and availability.
Core Material | Dk | Df | Thermal Conductivity (W/mK) | CTE (ppm/°C) | Relative Cost |
---|---|---|---|---|---|
FR-4 | 4.5 | 0.02 | 0.3 | 14 | Low |
CEM-1 | 4.7 | 0.03 | 0.2 | 15 | Very Low |
CEM-3 | 4.5 | 0.02 | 0.3 | 14 | Low |
Polyimide | 3.5 | 0.002 | 0.2 | 12 | High |
PTFE | 2.1 | 0.0004 | 0.2 | 60 | Very High |
Aluminum | – | – | 150 | 23 | Moderate |
Frequently Asked Questions (FAQ)
-
Q: What is the most common core material used in PCBs?
A: FR-4, a composite of woven fiberglass and epoxy resin, is the most widely used core material in PCBs due to its excellent balance of electrical, mechanical, and thermal properties. -
Q: Can the core material affect the signal integrity of a PCB?
A: Yes, the core material’s dielectric constant (Dk) and dissipation factor (Df) can significantly impact signal propagation speed, impedance, and power loss, ultimately affecting the PCB’s overall signal integrity. -
Q: What are the advantages of using a metal-core PCB (MCPCB)?
A: MCPCBs, which use a metal (typically aluminum) core, offer superior thermal conductivity compared to traditional FR-4 cores. This allows for better heat dissipation, making MCPCBs ideal for high-power applications or devices that generate significant heat. -
Q: How does the core material influence the manufacturing process of a PCB?
A: The choice of core material can affect various aspects of the PCB manufacturing process, such as lamination parameters (temperature and pressure), drilling speeds, and etching chemistry. Some materials, like polyimide or PTFE, may require specialized equipment or processes, which can increase production time and cost. -
Q: Can the core material be changed after the PCB has been manufactured?
A: No, once a PCB has been manufactured, the core material cannot be easily changed without significant rework or redesign. It is crucial to select the appropriate core material during the design phase to ensure the PCB meets all the necessary performance requirements.
Conclusion
Understanding the core of a PCB is essential for designing and manufacturing reliable, high-performance electronic devices. The core material serves as the foundation of the PCB, providing mechanical support, insulation, and a platform for the copper traces and components. By carefully considering factors such as dielectric constant, thermal conductivity, and mechanical strength, engineers can select the optimal core material for their specific application, ensuring the PCB meets all the necessary performance requirements while balancing cost and manufacturability.
As technology advances and new materials emerge, the choice of core materials for PCBs will continue to expand, offering designers and manufacturers greater flexibility and opportunities for innovation. By staying informed about the latest developments in core PCB materials and manufacturing processes, engineers can create cutting-edge electronic devices that push the boundaries of performance, reliability, and sustainability.
No responses yet