Understanding Thermal Conductivity in PCBs
Thermal conductivity is a critical property of printed circuit boards (PCBs) that determines how effectively heat is dissipated from electronic components. It is measured in watts per meter-kelvin (W/mK) and represents the rate at which heat is conducted through a material. In PCBs, thermal conductivity plays a crucial role in ensuring the reliability and longevity of electronic devices by preventing overheating and thermal damage.
Factors Affecting Thermal Conductivity in PCBs
Several factors influence the thermal conductivity of PCBs, including:
-
Material composition: The choice of materials used in PCB construction, such as the substrate, copper layers, and solder mask, directly impacts thermal conductivity.
-
Thickness: The thickness of the PCB and its layers affects heat dissipation. Thicker boards generally have better thermal conductivity than thinner ones.
-
Copper weight: The amount of copper used in the PCB Layers influences thermal conductivity. Higher copper weights improve heat dissipation.
-
Via density: Vias are small holes that connect different layers of a PCB. A higher via density enhances thermal conductivity by providing more pathways for heat to dissipate.
Common PCB Materials and Their Thermal Conductivity
PCBs can be manufactured using various materials, each with unique thermal conductivity properties. Here are some common PCB materials and their typical thermal conductivity values:
Material | Thermal Conductivity (W/mK) |
---|---|
FR-4 | 0.3 – 0.4 |
Aluminum | 120 – 237 |
Copper | 385 – 401 |
Polyimide | 0.1 – 0.4 |
Ceramic | 20 – 50 |
FR-4
FR-4 is the most widely used PCB material, consisting of a glass-reinforced epoxy laminate. It has a relatively low thermal conductivity, ranging from 0.3 to 0.4 W/mK. Despite its limited heat dissipation capabilities, FR-4 is popular due to its low cost, good electrical insulation, and mechanical stability.
Aluminum
Aluminum PCBs offer excellent thermal conductivity, with values ranging from 120 to 237 W/mK. They are often used in high-power applications where efficient heat dissipation is crucial. Aluminum PCBs are lightweight, durable, and provide good electrical insulation when anodized.
Copper
Copper is an exceptional thermal conductor, with thermal conductivity values ranging from 385 to 401 W/mK. It is commonly used in PCB layers to facilitate heat dissipation. However, using copper as the primary PCB substrate is uncommon due to its high cost and weight.
Polyimide
Polyimide PCBs have thermal conductivity values similar to FR-4, ranging from 0.1 to 0.4 W/mK. They are known for their excellent thermal stability, high temperature resistance, and flexibility. Polyimide PCBs are often used in applications that require resilience to harsh environments.
Ceramic
Ceramic PCBs offer good thermal conductivity, with values ranging from 20 to 50 W/mK. They are well-suited for high-temperature applications and provide excellent electrical insulation. Ceramic PCBs are also known for their dimensional stability and resistance to chemical and physical stress.
Enhancing Thermal Conductivity in PCBs
To improve the thermal conductivity of PCBs and ensure efficient heat dissipation, several techniques can be employed:
-
Using high-conductivity materials: Selecting PCB materials with inherently high thermal conductivity, such as aluminum or ceramic, can significantly enhance heat dissipation.
-
Increasing copper weight: Using thicker copper layers or increasing the copper weight in the PCB can improve thermal conductivity by providing more pathways for heat transfer.
-
Optimizing via placement: Strategic placement of vias, especially thermal vias, can facilitate better heat dissipation by creating efficient heat transfer channels between layers.
-
Incorporating thermal management features: Adding features like heat sinks, thermal pads, or heat spreaders can help dissipate heat more effectively from critical components.
-
Using thermal interface materials: Applying thermal interface materials, such as thermal grease or Thermal Adhesives, between components and the PCB can improve heat transfer and reduce thermal resistance.
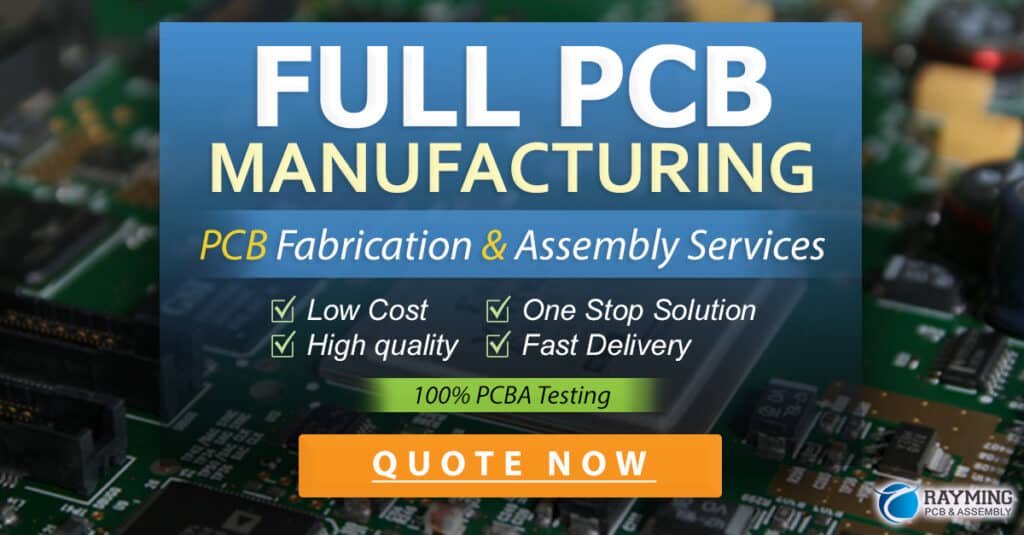
Thermal Conductivity Testing Methods for PCBs
To ensure that PCBs meet the required thermal conductivity specifications, various testing methods can be employed:
-
Infrared thermography: This non-contact method uses an infrared camera to capture thermal images of the PCB, allowing for the identification of hot spots and temperature gradients.
-
Thermocouple measurement: Thermocouples are placed at specific points on the PCB to measure temperature directly. This method provides accurate temperature readings but requires physical contact with the board.
-
Thermal simulation: Computer-aided design (CAD) software can be used to simulate the thermal behavior of a PCB under different operating conditions. This allows for the optimization of the PCB design before manufacturing.
-
Thermal resistance testing: This method involves applying a known amount of power to a component and measuring the temperature rise. The thermal resistance can then be calculated, providing insight into the PCB’s heat dissipation capabilities.
Frequently Asked Questions (FAQ)
-
What is the importance of thermal conductivity in PCBs?
Thermal conductivity is essential in PCBs because it determines how effectively heat is dissipated from electronic components. Poor thermal conductivity can lead to overheating, reduced performance, and decreased reliability of electronic devices. -
Which PCB material has the highest thermal conductivity?
Among common PCB materials, copper has the highest thermal conductivity, ranging from 385 to 401 W/mK. However, copper is rarely used as the primary PCB substrate due to its high cost and weight. -
Can the thermal conductivity of a PCB be improved after manufacturing?
While the inherent thermal conductivity of a PCB is determined by its material composition and design, some post-manufacturing techniques can enhance heat dissipation. These include adding thermal management features like heat sinks or thermal pads and applying thermal interface materials between components and the PCB. -
How does the thickness of a PCB affect its thermal conductivity?
Thicker PCBs generally have better thermal conductivity compared to thinner ones. This is because thicker boards provide more material for heat to dissipate through, allowing for more efficient heat transfer. -
What role do vias play in the thermal conductivity of a PCB?
Vias, especially thermal vias, play a crucial role in enhancing the thermal conductivity of a PCB. They create pathways for heat to transfer between layers, allowing for more efficient heat dissipation. A higher via density can significantly improve the overall thermal conductivity of a PCB.
Conclusion
Thermal conductivity is a critical property of PCBs that directly impacts the performance, reliability, and longevity of electronic devices. Understanding the factors that influence thermal conductivity, such as material composition, thickness, copper weight, and via density, is essential for designing PCBs that effectively dissipate heat.
By selecting appropriate materials, optimizing design features, and employing thermal management techniques, engineers can enhance the thermal conductivity of PCBs and ensure that electronic components operate within their specified temperature ranges. Regular testing and monitoring of thermal conductivity using methods like infrared thermography, thermocouple measurement, thermal simulation, and thermal resistance testing can help identify potential issues and validate the effectiveness of heat dissipation strategies.
As electronic devices continue to become more compact and powerful, the importance of thermal conductivity in PCBs will only continue to grow. By staying informed about the latest materials, design techniques, and testing methods, engineers can create PCBs that meet the ever-increasing demands for reliable, high-performance electronics while effectively managing heat dissipation challenges.
No responses yet