Advantages of SMDs
SMDs offer several advantages over through-hole components:
-
Miniaturization: SMDs are significantly smaller than their through-hole counterparts, allowing for more compact PCB Designs and smaller electronic devices.
-
Higher component density: With SMDs, more components can be placed on a single PCB, enabling more complex circuits and functionality in a smaller space.
-
Reduced weight: As SMDs are smaller and require less material, they contribute to an overall reduction in the weight of electronic devices.
-
Improved performance: SMDs have shorter lead lengths, which reduces parasitic inductance and capacitance, resulting in better high-frequency performance and signal integrity.
-
Automated assembly: SMDs are well-suited for automated pick-and-place assembly processes, which increases production speed and reduces manufacturing costs.
SMD Packages and Sizes
SMDs come in various package types and sizes to accommodate different component types and PCB layout requirements. Some common SMD packages include:
Package | Description | Typical Components |
---|---|---|
0201 | 0.02″ x 0.01″ (0.5mm x 0.25mm) | Resistors, capacitors |
0402 | 0.04″ x 0.02″ (1.0mm x 0.5mm) | Resistors, capacitors |
0603 | 0.06″ x 0.03″ (1.6mm x 0.8mm) | Resistors, capacitors |
0805 | 0.08″ x 0.05″ (2.0mm x 1.25mm) | Resistors, capacitors |
1206 | 0.12″ x 0.06″ (3.2mm x 1.6mm) | Resistors, capacitors |
SOT-23 | Small Outline Transistor | Transistors, diodes |
SOIC | Small Outline Integrated Circuit | Integrated circuits |
QFN | Quad Flat No-leads | Integrated circuits |
BGA | Ball Grid Array | Integrated circuits, microprocessors |
The choice of package depends on factors such as component availability, PCB space constraints, and the required power dissipation and thermal characteristics.
SMD Assembly Process
The SMD assembly process typically involves the following steps:
-
Solder paste application: A thin layer of solder paste is applied to the PCB pads using a stencil or solder paste printer.
-
Component placement: SMDs are picked and placed onto the PCB using an automated pick-and-place machine or by hand for low-volume or prototype assembly.
-
Reflow Soldering: The PCB with placed components is passed through a reflow oven, where the solder paste melts and forms a permanent electrical and mechanical connection between the component terminals and PCB pads.
-
Inspection: The assembLED PCB undergoes visual and automated optical inspection (AOI) to ensure proper component placement and solder joint quality.
-
Rework and repair: Any defects identified during inspection are reworked or repaired using specialized tools and techniques.
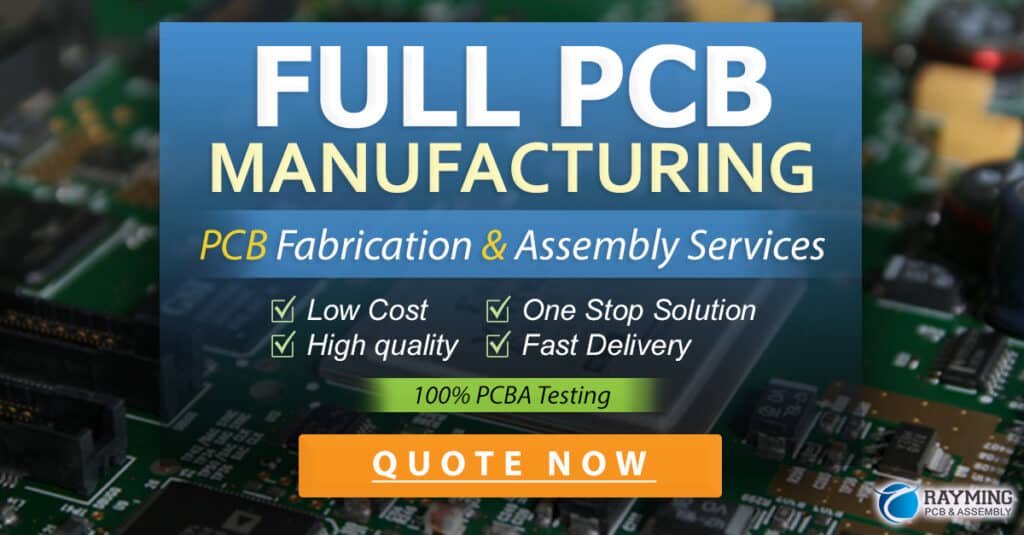
SMD Soldering Techniques
There are two primary methods for soldering SMDs:
-
Reflow soldering: This is the most common method for SMD assembly, as described in the previous section. Reflow soldering is well-suited for high-volume production and ensures consistent solder joint quality.
-
Hand soldering: For low-volume production, prototyping, or repair work, SMDs can be hand-soldered using a fine-tipped soldering iron and tweezers. Proper technique and tools are essential to avoid damage to the components or PCB.
When hand-soldering SMDs, it is important to:
- Use a soldering iron with a fine tip (e.g., chisel or conical) and temperature control
- Apply flux to improve solder flow and prevent oxidation
- Preheat the PCB and components to minimize thermal shock
- Use tweezers or a vacuum pickup tool to position and hold components
- Apply solder sparingly and avoid bridging adjacent pads or terminals
SMD Rework and Repair
Despite advancements in SMD assembly processes, defects can still occur, necessitating rework or repair. Common SMD defects include:
- Tombstoning: When one end of a component lifts off the PCB pad during reflow soldering
- Bridging: Unintended solder connections between adjacent pads or terminals
- Poor solder joints: Insufficient, excessive, or inconsistent solder coverage
- Misaligned or missing components
To rework or repair SMDs, technicians use specialized tools such as:
- Hot air rework stations: For heating and removing SMDs without damaging the PCB
- Soldering irons with fine tips: For precise soldering and desoldering
- Tweezers and vacuum pickup tools: For handling and positioning small components
- Solder wick and flux: For removing excess solder and improving solder flow
Proper training and experience are essential for successful SMD rework and repair to minimize the risk of further damage to the components or PCB.
SMD Component Handling and Storage
SMDs are sensitive to moisture, static electricity, and mechanical stress, so proper handling and storage are crucial to maintain their integrity and reliability. Some best practices include:
-
Moisture-sensitive device (MSD) handling: Many SMDs are moisture-sensitive and require special handling to prevent damage during reflow soldering. MSDs should be stored in moisture-barrier bags with desiccants and humidity indicator cards, and they must be baked before assembly if exposed to excessive moisture.
-
Electrostatic discharge (ESD) protection: SMDs can be damaged by static electricity, so ESD protection measures should be implemented throughout the manufacturing process. These include using grounded workstations, wrist straps, and ESD-safe packaging materials.
-
Proper storage: SMDs should be stored in a clean, dry, and temperature-controlled environment to prevent oxidation, corrosion, and mechanical damage. Components should be kept in their original packaging until ready for use, and excess components should be returned to storage promptly.
-
Inventory management: Implementing a well-organized inventory management system helps ensure that components are used within their shelf life and that stock levels are maintained to prevent production delays.
Designing for SMD Assembly
When designing PCBs for SMD assembly, engineers must consider several factors to ensure manufacturability, reliability, and cost-effectiveness. Some key design considerations include:
-
Component selection: Choose SMD packages that are readily available, have a proven track record of reliability, and are compatible with the intended assembly process.
-
PCB layout: Design the PCB layout with SMD assembly in mind, providing adequate pad sizes, spacing, and clearances for automated pick-and-place and reflow soldering processes.
-
Solder mask and paste stencils: Ensure that the solder mask and paste stencil designs are optimized for the selected SMD packages and assembly process, minimizing the risk of defects such as bridging or insufficient solder coverage.
-
Assembly process compatibility: Consider the capabilities and limitations of the intended assembly process when designing the PCB, such as maximum component placement speed, reflow oven profiles, and inspection requirements.
-
Design for manufacturing (DFM) analysis: Perform DFM analysis to identify and resolve potential manufacturability issues early in the design process, reducing the risk of delays and costly rework during production.
By carefully considering these factors and collaborating closely with the manufacturing team, designers can create PCBs that are optimized for SMD assembly and ensure a smooth transition from design to production.
Frequently Asked Questions (FAQ)
- What is the difference between SMD and through-hole components?
-
SMDs are mounted directly onto the surface of a PCB, while through-hole components have leads that are inserted into holes drilled in the PCB and soldered on the opposite side.
-
Can SMDs be soldered by hand?
-
Yes, SMDs can be hand-soldered using a fine-tipped soldering iron and tweezers, although this method is more suitable for low-volume production, prototyping, or repair work. High-volume production typically relies on automated reflow soldering processes.
-
What are the most common SMD packages?
-
Some of the most common SMD packages include 0402, 0603, and 0805 for resistors and capacitors, SOT-23 for transistors and diodes, and SOIC, QFN, and BGA for integrated circuits and microprocessors.
-
How can I prevent damage to SMDs during handling and storage?
-
To prevent damage to SMDs, follow proper handling and storage practices, such as using moisture-barrier bags for moisture-sensitive devices, implementing ESD protection measures, and storing components in a clean, dry, and temperature-controlled environment.
-
What should I consider when designing PCBs for SMD assembly?
- When designing PCBs for SMD assembly, consider factors such as component selection, PCB layout, solder mask and paste stencil design, assembly process compatibility, and design for manufacturing (DFM) analysis to ensure manufacturability, reliability, and cost-effectiveness.
Conclusion
Surface Mount Devices (SMDs) have transformed the electronics industry by enabling the production of smaller, lighter, and more complex electronic devices. By understanding the advantages, assembly processes, soldering techniques, and design considerations associated with SMDs, engineers and technicians can effectively work with these components to create innovative and reliable products. As electronic devices continue to evolve and demand for miniaturization grows, SMDs will remain an essential part of the electronics manufacturing landscape.
No responses yet