What is Reflow Soldering?
Reflow soldering is a process used in the manufacturing of electronic circuits, where components are mounted onto a printed circuit board (PCB) using a solder paste. The entire assembly is then heated in a reflow oven, causing the solder to melt and form a permanent connection between the components and the PCB. This process is widely used in the electronics industry due to its efficiency, reliability, and ability to handle high-volume production.
Advantages of Reflow Soldering
-
High-speed production: Reflow soldering allows for the simultaneous soldering of multiple components, significantly reducing the time required for assembly compared to manual soldering methods.
-
Consistency: The automated nature of reflow soldering ensures consistent solder joint quality across the entire PCB, minimizing the risk of human error.
-
Precision: Reflow soldering enables the use of smaller components and tighter spacing, as the solder paste is applied precisely using stencils or dispensing methods.
-
Flexibility: The process is suitable for a wide range of component types, including surface mount devices (SMDs) and through-hole components.
The Reflow Soldering Process
The reflow soldering process consists of several key stages:
1. PCB Preparation
Before the soldering process begins, the PCB must be properly designed and manufactured. This includes ensuring that the board has the correct pad sizes, spacing, and solder mask openings for the components being used.
2. Solder Paste Application
Solder paste, a mixture of tiny solder particles and flux, is applied to the PCB using a stencil or dispensing method. The stencil is a thin metal sheet with openings that correspond to the component pads on the PCB. The solder paste is spread across the stencil, filling the openings and depositing the paste onto the pads.
3. Component Placement
After the solder paste is applied, the components are placed onto the PCB using a pick-and-place machine or by hand. The machine uses vacuum nozzles to pick up the components from tape reels or trays and place them precisely on the solder paste-covered pads.
4. Reflow
The assembLED PCB is then placed in a reflow oven, which heats the board in a controlled manner. The reflow process typically follows a temperature profile that includes several stages:
-
Preheat: The PCB is gradually heated to activate the flux and remove any moisture from the solder paste.
-
Soak: The temperature is maintained at a stable level to allow the components and the PCB to reach a uniform temperature.
-
Reflow: The temperature is increased to the melting point of the solder, causing the solder particles to melt and form a permanent connection between the components and the PCB.
-
Cooling: The PCB is cooled down gradually to allow the solder joints to solidify and prevent thermal shock to the components.
5. Inspection and Testing
After the reflow process, the PCB undergoes visual inspection and electrical testing to ensure that all solder joints are properly formed and the circuit functions as intended. Automated optical inspection (AOI) systems and X-ray inspection may be used to detect any defects or issues.
Factors Affecting Reflow Soldering Quality
Several factors can impact the quality of the reflow soldering process:
1. Solder Paste Quality
The quality of the solder paste is crucial for achieving reliable solder joints. The paste must have the correct composition, particle size, and viscosity to ensure proper melting and wetting of the component leads and pads.
2. Stencil Design
The stencil used for applying the solder paste must be designed correctly to ensure the right amount of paste is deposited on each pad. Factors such as aperture size, shape, and thickness must be considered based on the component and PCB Design.
3. Component Placement Accuracy
Accurate placement of components is essential for proper solder joint formation. Misaligned or skewed components can lead to open circuits, shorts, or poor mechanical strength.
4. Reflow Temperature Profile
The reflow temperature profile must be carefully controlled to ensure that the solder melts and wets the components and pads properly without causing damage. The peak temperature, duration, and ramp rates must be optimized based on the solder paste and component specifications.
5. PCB and Component Cleanliness
Contaminants such as dirt, grease, or oxidation on the PCB or component leads can interfere with solder wetting and cause defects. Proper cleaning and handling procedures must be followed to maintain cleanliness throughout the assembly process.
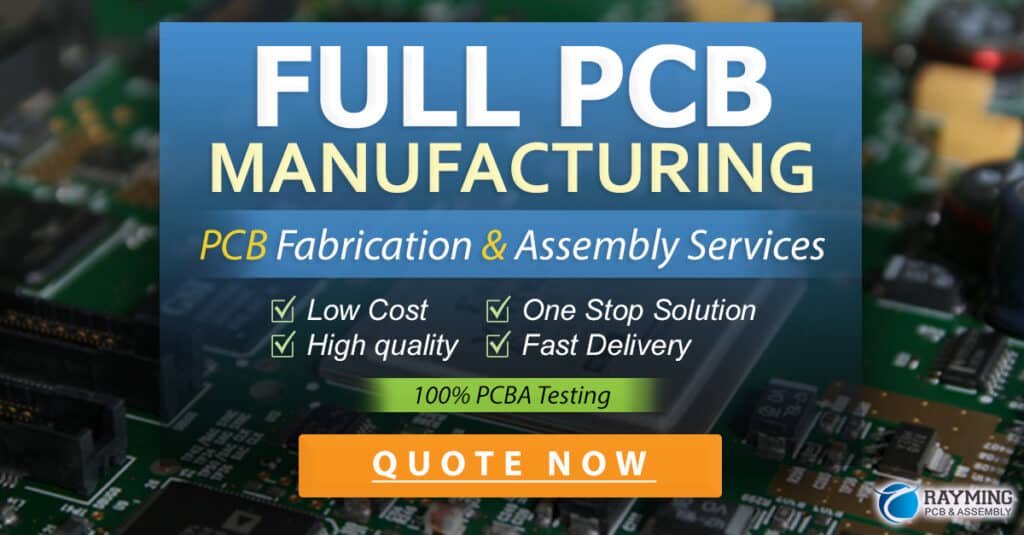
Common Reflow Soldering Defects
Despite the advantages of reflow soldering, several types of defects can occur during the process:
-
Bridging: Solder bridges form between adjacent pads or pins, causing short circuits.
-
Tombstoning: Small, lightweight components may stand up on one end due to uneven heating or surface tension, resulting in an open circuit.
-
Insufficient or excessive solder: Too little solder can lead to weak joints, while too much solder can cause shorts or impede the placement of nearby components.
-
Solder balls: Small solder spheres may form and scatter across the PCB, potentially causing shorts.
-
Component shifting: Components may move or rotate during the reflow process, leading to misalignment or poor connections.
Proper process control, regular maintenance, and continuous monitoring can help minimize the occurrence of these defects.
Reflow Soldering Equipment
Several types of equipment are used in the reflow soldering process:
1. Stencil Printer
A stencil printer is used to apply the solder paste to the PCB. It consists of a frame to hold the stencil, a squeegee to spread the paste, and a mechanism to align the PCB with the stencil.
2. Pick-and-Place Machine
Pick-and-place machines are used to automatically place components onto the PCB. They use vacuum nozzles to pick up components from tape reels or trays and place them precisely on the solder paste-covered pads.
3. Reflow Oven
Reflow ovens are used to heat the PCB and melt the solder paste. They can be convection-based, using hot air circulation, or infrared-based, using radiant heat. Modern reflow ovens often incorporate multiple heating zones and cooling systems to achieve the desired temperature profile.
4. Inspection Systems
Automated optical inspection (AOI) systems and X-ray inspection machines are used to detect defects and ensure the quality of the soldered assembly. AOI systems use cameras and image processing algorithms to identify surface-level defects, while X-ray inspection allows for the detection of hidden defects, such as voids or insufficient solder penetration.
Reflow Soldering Standards and Guidelines
Several industry standards and guidelines exist to ensure the quality and reliability of reflow soldered assemblies:
- IPC-A-610: Acceptability of Electronic Assemblies
- IPC-J-STD-001: Requirements for Soldered Electrical and Electronic Assemblies
- IPC-7530: Guidelines for Temperature Profiling for Mass Soldering Processes (Reflow & Wave)
These standards provide criteria for evaluating the quality of solder joints, specifying the acceptable levels of defects, and outlining best practices for process control and inspection.
Reflow Soldering in Different Industries
Reflow soldering is used in various industries that rely on electronic assemblies:
- Consumer electronics: Smartphones, tablets, laptops, and home appliances
- Automotive: Engine control units, sensors, infotainment systems, and advanced driver assistance systems (ADAS)
- Aerospace and defense: Avionics, communication systems, and military equipment
- Medical devices: Diagnostic equipment, monitoring systems, and implantable devices
- Industrial automation: Control systems, sensors, and power electronics
Each industry may have specific requirements and challenges related to reflow soldering, such as high reliability, miniaturization, or harsh operating environments.
Troubleshooting Reflow Soldering Issues
When issues arise during the reflow soldering process, several troubleshooting steps can be taken:
-
Review the reflow temperature profile: Ensure that the temperature profile is optimized for the solder paste and components being used. Adjust the peak temperature, ramp rates, or dwell times as needed.
-
Check the solder paste: Verify that the solder paste is within its shelf life and has been stored properly. Inspect the paste for signs of drying, separation, or contamination.
-
Inspect the stencil: Check the stencil for damage, wear, or clogging of the apertures. Clean or replace the stencil as necessary.
-
Verify component placement: Ensure that the components are placed accurately and securely on the pads. Check for any misalignment, skewing, or lifting of components.
-
Assess the PCB condition: Inspect the PCB for any damage, contamination, or oxidation that may interfere with solder wetting. Clean the PCB if required.
-
Analyze the defects: Use visual inspection, AOI, or X-ray inspection to identify the types and locations of defects. Determine the root causes and implement corrective actions.
By systematically addressing these factors, most reflow soldering issues can be resolved, and the process can be optimized for consistent, high-quality results.
Frequently Asked Questions (FAQ)
- What is the difference between reflow soldering and wave soldering?
-
Reflow soldering is used primarily for surface mount components and involves applying solder paste, placing components, and heating the entire assembly in a reflow oven. Wave soldering, on the other hand, is used for through-hole components and involves passing the PCB over a molten solder wave to create the solder joints.
-
Can reflow soldering be used for through-hole components?
-
While reflow soldering is primarily used for surface mount components, it can also be used for certain through-hole components with appropriate preparation. This may involve using special solder paste formulations or pre-forming the component leads to ensure proper solder wetting.
-
What is the purpose of flux in solder paste?
-
Flux in solder paste serves several purposes: it cleans the surfaces of the components and PCB pads, removes oxidation, and promotes solder wetting. The flux also helps to prevent re-oxidation during the reflow process and improves the flow characteristics of the molten solder.
-
How can voids in solder joints be minimized during reflow soldering?
-
Voids can be minimized by optimizing the reflow temperature profile, ensuring proper solder paste application, and using solder paste with an appropriate composition and particle size. Additionally, using vacuum reflow soldering equipment or implementing a controlled cooling rate can help reduce the formation of voids.
-
What is the role of nitrogen in reflow soldering?
- Nitrogen is sometimes used in reflow soldering to create an inert atmosphere in the oven. This helps to reduce oxidation of the solder and component surfaces during the reflow process, leading to improved solder joint quality and reliability. Nitrogen can also help to minimize the formation of solder balls and other defects.
Reflow Soldering Comparison | Advantages | Disadvantages |
---|---|---|
Reflow Soldering | – High-speed production – Consistency – Precision – Flexibility |
– Higher initial equipment cost – Requires careful process control – Limited to certain component types |
Wave Soldering | – Suitable for through-hole components – Lower equipment cost – Faster for high-volume production of simple boards |
– Not suitable for most surface mount components – Less precise than reflow soldering – Higher risk of thermal damage to components |
In conclusion, reflow soldering is a crucial process in the manufacturing of electronic assemblies, offering numerous advantages such as high-speed production, consistency, precision, and flexibility. By understanding the process, controlling the key factors, and utilizing appropriate equipment and guidelines, manufacturers can achieve high-quality solder joints and reliable electronic products. As the electronics industry continues to evolve, with increasing demand for miniaturization and higher performance, reflow soldering will remain an essential technique for creating robust and efficient electronic assemblies.
No responses yet