Introduction to Gerber Files
Gerber files are a standard file format used in the printed circuit board (PCB) industry to describe the layout and design of a PCB. They are named after the Gerber Scientific Instrument Company, which developed the format in the 1960s. Gerber files are essential for PCB Fabrication as they contain all the necessary information required to manufacture a PCB, including the copper layers, solder mask, silkscreen, and drill data.
Types of Gerber Files
There are two main types of Gerber files:
- Standard Gerber (RS-274-D)
- Extended Gerber (RS-274X)
Standard Gerber files, also known as RS-274-D, are the original Gerber file format. They are simple ASCII text files that describe the PCB Layout using a series of commands and coordinates. Standard Gerber files have limitations, such as the inability to specify the aperture shape and size, which can lead to ambiguity and errors in PCB fabrication.
Extended Gerber files, also known as RS-274X or Gerber X, were introduced to address the limitations of Standard Gerber files. They include additional commands and attributes that allow for more precise and unambiguous PCB layout description. Extended Gerber files are the most widely used Gerber file format in the PCB industry today.
What is Gerber X2?
Gerber X2 is an extension of the Extended Gerber (RS-274X) file format. It was developed by Ucamco, the company that now owns the Gerber file format, to further enhance the capabilities of Gerber files and streamline the PCB fabrication process. Gerber X2 adds new features and attributes to the Extended Gerber format, making it more intelligent and efficient.
Key Features of Gerber X2
-
Embedded Aperture Definitions: In Extended Gerber, aperture definitions are typically stored in a separate file called an aperture list. Gerber X2 allows aperture definitions to be embedded directly within the Gerber file, eliminating the need for a separate aperture list file and reducing the chances of errors.
-
Attribute Metadata: Gerber X2 introduces attribute metadata, which allows additional information to be associated with specific features in the PCB layout. This metadata can include information such as component designators, pad functions, and net names, making the Gerber file more informative and easier to interpret.
-
Standardized Attributes: Gerber X2 defines a set of standardized attributes that can be used to convey common PCB design information, such as the layer type, copper weight, and solder mask color. This standardization helps to ensure consistency and reduces the potential for misinterpretation.
-
Nested Step and Repeat: Step and repeat is a feature that allows a section of the PCB layout to be replicated multiple times. Gerber X2 introduces nested step and repeat, which enables the creation of complex hierarchical designs with multiple levels of repetition, simplifying the PCB layout process.
-
Improved Precision: Gerber X2 supports higher precision coordinates and sizes, allowing for more accurate representation of the PCB layout. This is particularly important for high-density designs with fine features and tight tolerances.
Differences between Gerber and Gerber X2
While Gerber X2 is an extension of the Extended Gerber format, there are several key differences between the two:
-
Aperture Definitions: In Extended Gerber, aperture definitions are stored in a separate aperture list file, while in Gerber X2, they can be embedded directly within the Gerber file itself.
-
Attribute Metadata: Gerber X2 introduces attribute metadata, which is not available in Extended Gerber. This metadata allows additional information to be associated with specific features in the PCB layout, making the Gerber file more informative and easier to interpret.
-
Standardized Attributes: Gerber X2 defines a set of standardized attributes for conveying common PCB design information, which is not present in Extended Gerber.
-
Nested Step and Repeat: Gerber X2 supports nested step and repeat, allowing for the creation of complex hierarchical designs, while Extended Gerber only supports simple step and repeat.
-
Precision: Gerber X2 supports higher precision coordinates and sizes compared to Extended Gerber, enabling more accurate representation of the PCB layout.
Feature | Extended Gerber (RS-274X) | Gerber X2 |
---|---|---|
Aperture Definitions | Separate aperture list file | Embedded within Gerber file |
Attribute Metadata | Not available | Supported |
Standardized Attributes | Not defined | Defined and supported |
Nested Step and Repeat | Not supported | Supported |
Precision | Lower precision | Higher precision |
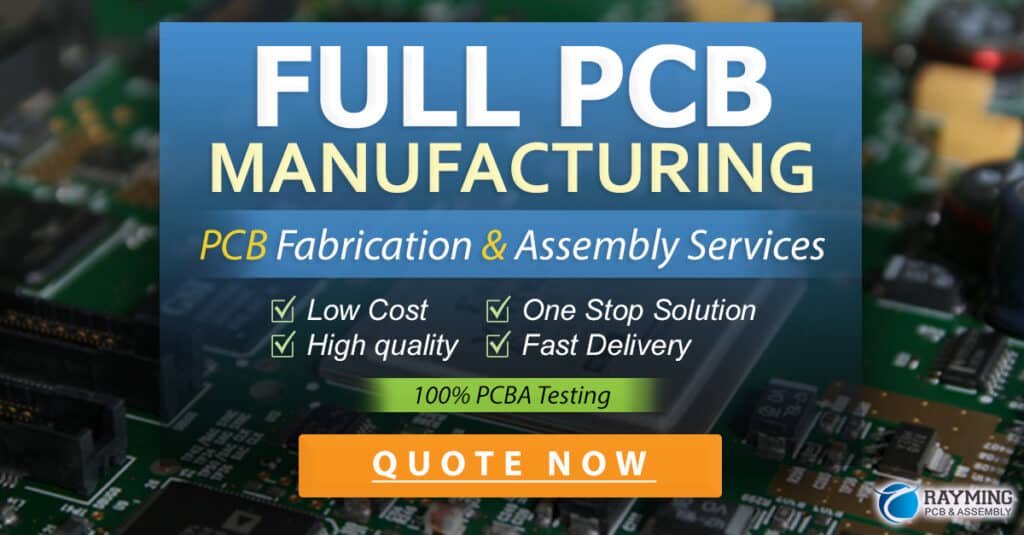
Benefits of using Gerber X2
Adopting Gerber X2 offers several benefits for PCB designers and manufacturers:
-
Improved Efficiency: By embedding aperture definitions and attribute metadata directly within the Gerber file, Gerber X2 eliminates the need for separate files and reduces the chances of errors and inconsistencies. This streamlines the PCB fabrication process and improves overall efficiency.
-
Enhanced Communication: The standardized attributes and attribute metadata in Gerber X2 provide a clear and unambiguous way to convey PCB design intent. This enhanced communication between designers and manufacturers helps to avoid misinterpretations and ensures that the manufactured PCB matches the designer’s intent.
-
Increased Design Flexibility: The nested step and repeat feature in Gerber X2 allows for the creation of complex hierarchical designs with ease. This increased design flexibility enables designers to create more intricate and compact PCB layouts.
-
Higher Accuracy: With support for higher precision coordinates and sizes, Gerber X2 enables more accurate representation of the PCB layout. This is particularly important for high-density designs with fine features and tight tolerances, where even small inaccuracies can lead to manufacturing issues.
-
Future-proofing: As PCB designs continue to become more complex and compact, the enhanced capabilities of Gerber X2 ensure that the format remains relevant and capable of handling future design requirements.
Transition to Gerber X2
While Gerber X2 offers numerous benefits, transitioning from Extended Gerber to Gerber X2 requires some adjustments in the PCB design and fabrication workflow.
-
Software Updates: To support Gerber X2, PCB design software and Computer-Aided Manufacturing (CAM) systems may require updates or upgrades. Designers and manufacturers should ensure that their software tools are compatible with Gerber X2 before making the transition.
-
Education and Training: Designers and manufacturers may need to educate themselves on the new features and attributes introduced in Gerber X2. This may involve training sessions, workshops, or self-study to become familiar with the format and its capabilities.
-
Adaptation of Workflow: The transition to Gerber X2 may require some changes in the existing PCB design and fabrication workflow. Designers and manufacturers should review their current processes and make necessary adjustments to accommodate the new format and its features.
-
Collaboration with Partners: To ensure a smooth transition, it is essential to collaborate with supply chain partners, such as PCB fabricators and assembly houses. Clear communication and coordination with these partners will help to identify any potential issues and ensure that all stakeholders are prepared for the transition to Gerber X2.
FAQs
-
Q: Is Gerber X2 backward compatible with Extended Gerber?
A: Yes, Gerber X2 is backward compatible with Extended Gerber. PCB fabricators that support Extended Gerber can still process Gerber X2 files, although they may not be able to take advantage of the new features and attributes introduced in Gerber X2. -
Q: Do I need to update my PCB design software to use Gerber X2?
A: It depends on your current PCB design software. Many modern PCB design tools already support Gerber X2. However, if you are using an older version or a software package that does not support Gerber X2, you may need to update or upgrade your software. -
Q: Can I mix Extended Gerber and Gerber X2 files in the same PCB project?
A: While it is technically possible to mix Extended Gerber and Gerber X2 files in the same project, it is not recommended. To take full advantage of the benefits offered by Gerber X2, it is best to use Gerber X2 for all files associated with a given PCB project. -
Q: Will adopting Gerber X2 increase the cost of PCB fabrication?
A: In most cases, adopting Gerber X2 will not increase the cost of PCB fabrication. Many PCB fabricators already support Gerber X2, and the enhanced capabilities of the format can potentially lead to cost savings by reducing errors and improving efficiency. -
Q: Is Gerber X2 the latest version of the Gerber format?
A: As of 2021, Gerber X2 is the most recent version of the Gerber format. However, the Gerber format continues to evolve, and future extensions or updates may be introduced to address new challenges and requirements in PCB design and fabrication.
Conclusion
Gerber X2 is an extension of the Extended Gerber file format that introduces new features and attributes to enhance the capabilities of Gerber files and streamline the PCB fabrication process. By embedding aperture definitions, adding attribute metadata, defining standardized attributes, supporting nested step and repeat, and improving precision, Gerber X2 offers numerous benefits for PCB designers and manufacturers.
While transitioning from Extended Gerber to Gerber X2 requires some adjustments in the PCB design and fabrication workflow, the long-term advantages of adopting Gerber X2 make it a worthwhile investment. As PCB designs continue to become more complex and compact, Gerber X2 ensures that the Gerber format remains relevant and capable of meeting future design requirements.
By understanding the differences between Gerber and Gerber X2 files and the benefits of adopting Gerber X2, PCB designers and manufacturers can make informed decisions about incorporating this advanced format into their workflow, ultimately leading to improved efficiency, enhanced communication, and higher-quality PCB fabrication.
No responses yet