Understanding Component Orientation
Definition and Significance
Component orientation describes the specific way in which electronic components are placed and aligned on a PCB. It involves the physical positioning of components relative to the board’s surface and other components. The orientation of components is crucial because it affects several aspects of the PCB design and manufacturing process, including:
- Functionality: Proper component orientation ensures that the components are connected correctly and function as intended within the circuit.
- Manufacturability: The orientation of components impacts the ease and efficiency of the assembly process, as well as the ability to perform automated placement and soldering.
- Reliability: Correct component orientation contributes to the overall reliability of the electronic device by minimizing stress on components and preventing issues such as short circuits or mechanical interference.
Factors Influencing Component Orientation
Several factors influence the choice of component orientation in PCB design:
- PCB Layout: The overall layout of the PCB, including the placement of other components, traces, and connectors, may dictate the orientation of certain components to optimize space utilization and signal integrity.
- Component package: The package type of the component, such as through-hole or surface mount, determines the available orientation options and the required footprint on the PCB.
- Mechanical considerations: The physical size, shape, and height of components may affect their orientation to ensure proper clearance and avoid interference with other components or enclosures.
- Thermal management: The orientation of components that generate significant heat, such as power regulators or processors, may be optimized to facilitate efficient heat dissipation.
- Manufacturing constraints: The capabilities and limitations of the manufacturing process, including the placement machines and soldering techniques, may influence the preferred orientation of components.
Common Component Orientation Types
Through-Hole Components
Through-hole components have leads that are inserted into drilled holes on the PCB and soldered on the opposite side. The orientation of through-hole components is typically determined by the lead configuration and the corresponding hole pattern on the PCB.
- Vertical orientation: Components are placed perpendicular to the PCB surface, with leads extending through the holes. This orientation is common for larger components or those requiring mechanical stability.
- Horizontal orientation: Components are placed parallel to the PCB surface, with leads bent at a right angle to fit into the holes. This orientation is often used for components with a low profile or when space is limited.
Surface Mount Components
Surface mount components are directly soldered onto pads on the PCB surface without requiring drilled holes. The orientation of surface mount components is critical for automated assembly processes and can vary based on the component package.
- Chip components: Chip resistors, capacitors, and inductors have a simple rectangular package with terminations on opposite ends. They are typically oriented with the longer side parallel to the PCB surface.
- Gull-wing leads: Components with gull-wing leads, such as QFP (Quad Flat Pack) and SOP (Small Outline Package), have leads that extend from the sides of the package and bend downward. The orientation is usually dictated by the lead configuration and the corresponding pad layout on the PCB.
- J-lead packages: Components with J-lead packages, such as SOJ (Small Outline J-lead) and PLCC (Plastic Leaded Chip Carrier), have leads that extend from the sides of the package and bend inward underneath the component. The orientation is determined by the lead configuration and the matching pad layout.
- BGA (Ball Grid Array): BGA components have an array of solder balls on the underside of the package. The orientation of BGA components is critical for proper alignment with the corresponding pad array on the PCB.
Best Practices for Component Orientation
To ensure optimal functionality, manufacturability, and reliability of PCBs, consider the following best practices when determining component orientation:
- Adhere to manufacturer recommendations: Consult the component manufacturer’s datasheet and application notes for recommended orientation guidelines specific to each component.
- Consider assembly processes: Choose component orientations that facilitate automated placement and soldering processes, minimizing the need for manual intervention or special handling.
- Optimize for signal integrity: Orient components in a way that minimizes the length of critical signal paths and reduces crosstalk or interference between components.
- Ensure proper clearance: Verify that the chosen orientation provides sufficient clearance between components, preventing physical interference or short circuits.
- Accommodate thermal management: Position components that generate significant heat in an orientation that promotes efficient heat dissipation, such as aligning them with Thermal Pads or exposed copper areas.
- Maintain consistency: Strive for consistent orientation of similar components throughout the PCB design to enhance readability and ease of assembly.
- Collaborate with manufacturing partners: Engage with PCB Fabrication and assembly partners early in the design process to ensure that the chosen component orientations are compatible with their manufacturing capabilities and guidelines.
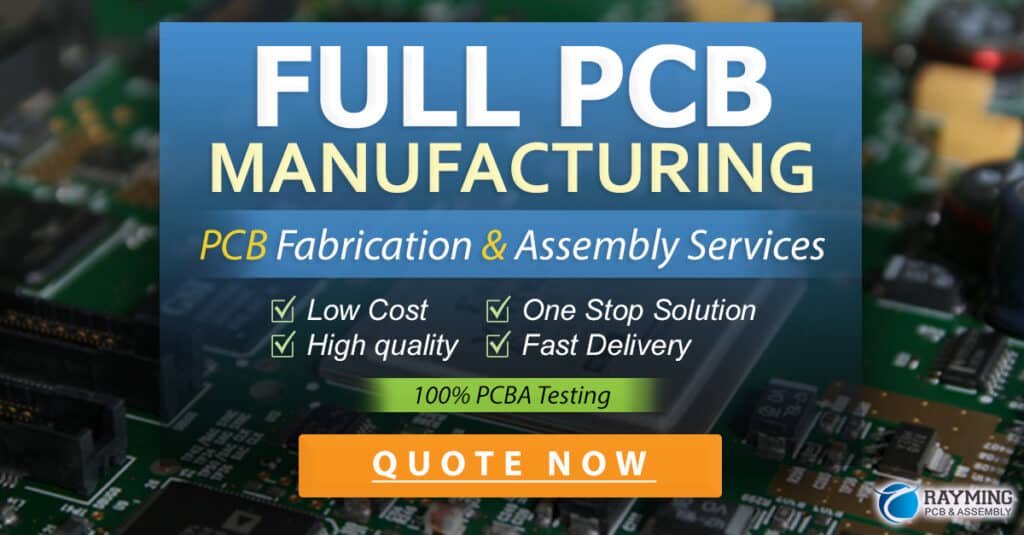
Frequently Asked Questions (FAQ)
1. What happens if a component is placed in the wrong orientation on a PCB?
Incorrect component orientation can lead to various issues, such as:
– Malfunction or complete failure of the circuit due to incorrect connections.
– Short circuits or physical interference between components.
– Difficulty in assembly or soldering processes, leading to poor quality or damaged components.
– Reduced reliability and increased risk of failure over time.
2. Can the orientation of a component affect its performance?
Yes, the orientation of a component can impact its performance in certain cases. For example:
– Orientation can affect the thermal dissipation of components that generate significant heat, leading to overheating if not properly aligned with cooling features.
– Orientation can influence the signal integrity of high-speed or sensitive components, as improper placement may introduce noise or crosstalk.
– Certain components, such as polarized capacitors or diodes, have specific orientation requirements for proper functioning.
3. How do I determine the correct orientation for a component?
To determine the correct orientation for a component, follow these steps:
1. Consult the component manufacturer’s datasheet and application notes for specific orientation guidelines.
2. Review the PCB layout and consider factors such as pad configuration, adjacent components, and signal routing.
3. Verify that the chosen orientation aligns with the capabilities and constraints of the manufacturing process.
4. Seek guidance from experienced PCB designers or manufacturing partners if unsure about the optimal orientation.
4. Can I change the orientation of a component after the PCB has been manufactured?
Changing the orientation of a component after PCB manufacturing is generally not recommended and can be challenging. It may involve desoldering the component, potentially damaging the PCB or the component itself. In some cases, minor adjustments may be possible, but it is always best to ensure correct orientation during the design and assembly stages.
5. Are there any tools or software that can help with determining component orientation?
Yes, various PCB design software packages offer tools and features to assist with component orientation:
– 3D visualization: Many PCB design tools provide 3D rendering capabilities that allow designers to visualize component placement and orientation in a virtual environment.
– Design rule checks (DRC): DRC tools can validate component orientation against predefined rules and guidelines, flagging any violations or potential issues.
– Component libraries: PCB design software often includes extensive component libraries with recommended footprints and orientation information for common components.
– Collaborative features: Some PCB design platforms enable collaboration with manufacturing partners, allowing for seamless communication and feedback on component orientation and other design aspects.
Conclusion
Component orientation is a critical aspect of PCB design and manufacturing that directly impacts the functionality, reliability, and manufacturability of electronic devices. By understanding the different types of component orientations and following best practices, designers can ensure optimal performance and successful assembly of their PCBs.
When determining component orientation, it is essential to consider factors such as PCB layout, component package, mechanical constraints, thermal management, and manufacturing capabilities. Adhering to manufacturer guidelines, collaborating with manufacturing partners, and leveraging PCB design software tools can greatly facilitate the process of selecting the appropriate orientation for each component.
By paying close attention to component orientation throughout the design and manufacturing workflow, electronics professionals can create high-quality, reliable, and efficiently manufacturable PCBs that meet the ever-increasing demands of modern electronic devices.
No responses yet