Understanding the Importance of a Bill of Materials in PCB Design
In the world of Printed Circuit Board (PCB) design, the Bill of Materials (BOM) is a crucial document that plays a significant role in the successful fabrication and assembly of a PCB. A well-crafted BOM ensures that all the necessary components are accounted for, ordered, and delivered in a timely manner, thereby streamlining the manufacturing process and minimizing the risk of errors or delays.
What is a Bill of Materials (BOM)?
A Bill of Materials, commonly referred to as a BOM, is a comprehensive list of all the components, materials, and sub-assemblies required to manufacture a product. In the context of PCB design, a BOM typically includes the following information for each component:
- Reference Designator
- Quantity
- Manufacturer Part Number
- Description
- Package Type
- Value
- Tolerance
- Supplier Information
Here’s an example of what a simple BOM might look like:
Reference Designator | Quantity | Manufacturer Part Number | Description | Package Type | Value | Tolerance | Supplier |
---|---|---|---|---|---|---|---|
C1, C2 | 2 | CAP-0805-X7R-50V-10UF | Capacitor | 0805 | 10uF | ±10% | Digi-Key |
R1, R2, R3 | 3 | RES-0603-1K-1% | Resistor | 0603 | 1kΩ | ±1% | Mouser |
U1 | 1 | IC-MCU-ATMEGA328P-AU | Microcontroller | TQFP-32 | – | – | Newark |
The Significance of a BOM in PCB Design
A well-maintained and accurate BOM is essential for several reasons:
-
Procurement: The BOM serves as a guide for the purchasing department to procure the necessary components from the specified suppliers. This helps ensure that the correct parts are ordered in the right quantities, minimizing the risk of Component Shortages or excess inventory.
-
Assembly: The manufacturing team relies on the BOM to assemble the PCB correctly. The reference designators and component descriptions provided in the BOM help the assemblers locate and place the components accurately on the board.
-
Quality Control: A complete and accurate BOM enables the quality control team to verify that the assembled PCB matches the intended design. This helps identify any missing, incorrect, or damaged components before the board proceeds to the next stage of production.
-
Revision Control: As a PCB design undergoes revisions and improvements, the BOM must be updated accordingly. Maintaining a revision history of the BOM helps track changes and ensures that the correct version of the board is being manufactured.
-
Cost Estimation: The BOM plays a vital role in estimating the cost of manufacturing a PCB. By listing all the required components and their quantities, the BOM enables accurate cost calculations, which are crucial for pricing the final product and determining profit margins.
Creating an Accurate BOM
To create an accurate and comprehensive BOM, follow these best practices:
-
Use a consistent naming convention: Establish a clear and consistent naming convention for all components, such as reference designators and manufacturer part numbers. This helps avoid confusion and ensures that all stakeholders can easily understand the BOM.
-
Include all necessary information: Ensure that the BOM contains all the essential information for each component, such as the reference designator, quantity, manufacturer part number, description, package type, value, tolerance, and supplier information.
-
Verify component availability: Before finalizing the BOM, check the availability of all components with the specified suppliers. This helps identify any potential supply chain issues or long lead times that could impact the manufacturing schedule.
-
Collaborate with the design team: Work closely with the PCB design team to ensure that the BOM accurately reflects the latest version of the schematic and layout. Any discrepancies between the BOM and the design files can lead to manufacturing errors and delays.
-
Perform regular audits: Conduct periodic audits of the BOM to verify its accuracy and completeness. This helps catch any errors or omissions early in the design process, reducing the risk of costly mistakes during manufacturing.
Integrating BOM Management with PCB Design Tools
Many modern PCB design tools offer built-in BOM management features that streamline the process of creating, updating, and sharing BOMs. These features typically include:
-
Automated BOM generation: PCB design tools can automatically generate a BOM based on the components used in the schematic and layout. This saves time and reduces the risk of manual errors.
-
Real-time updates: When changes are made to the schematic or layout, the BOM is automatically updated to reflect the latest component information. This ensures that the BOM always remains in sync with the design files.
-
Component libraries: PCB design tools often include extensive component libraries that contain detailed information about various components, such as manufacturer part numbers, package types, and footprints. These libraries can be used to populate the BOM quickly and accurately.
-
Collaboration and sharing: Many PCB design tools offer cloud-based collaboration features that allow team members to access and edit the BOM simultaneously. This enables real-time collaboration and ensures that everyone is working with the most up-to-date version of the BOM.
By leveraging these features, PCB designers can streamline the BOM management process, reduce the risk of errors, and improve overall design efficiency.
The Role of the BOM in Supply Chain Management
In addition to its importance in PCB design and manufacturing, the BOM plays a critical role in supply chain management. By providing a comprehensive list of all the required components, the BOM enables companies to:
-
Forecast demand: The BOM helps companies predict the demand for individual components based on the expected production volume of the final product. This information is crucial for planning inventory levels and avoiding stockouts or excess inventory.
-
Negotiate with suppliers: A well-structured BOM enables companies to negotiate better prices and terms with component suppliers. By consolidating the demand for similar components across multiple products, companies can leverage their purchasing power to secure more favorable deals.
-
Manage lead times: The BOM helps companies identify components with long lead times and plan accordingly. By understanding the lead times for critical components, companies can optimize their production schedules and minimize the risk of delays.
-
Mitigate supply chain risks: A comprehensive BOM enables companies to identify potential supply chain risks, such as single-source components or components with a high risk of obsolescence. By proactively addressing these risks, companies can develop contingency plans and ensure a more resilient supply chain.
Common BOM Formats and Standards
BOMs can be created and shared in various formats, depending on the specific requirements of the organization and its supply chain partners. Some common BOM formats include:
-
Spreadsheets: Microsoft Excel and Google Sheets are widely used for creating and sharing BOMs. Spreadsheets offer a simple and flexible format that can be easily customized to include additional columns or calculations.
-
CSV (Comma-Separated Values): CSV files are plain text files that use commas to separate values. They are a common format for exchanging BOM data between different systems and can be easily imported into spreadsheets or databases.
-
XML (eXtensible Markup Language): XML is a structured format that uses tags to define the data elements in a BOM. XML files are human-readable and can be easily parsed by software applications, making them a popular choice for integrating BOM data with other systems.
-
IPC-2571 (Generic Requirements for Electronics Manufacturing Supply Chain Communication): IPC-2571 is an industry-standard format for exchanging BOM data between companies in the electronics manufacturing supply chain. It defines a common data model and file format for sharing BOM information, helping to ensure consistency and interoperability across different systems.
When choosing a BOM format, consider the following factors:
- Compatibility with your PCB design tools and other software systems
- Ease of use and collaboration with internal teams and external partners
- Scalability and ability to handle complex BOMs with a large number of components
- Compliance with industry standards and best practices
Best Practices for Managing BOMs
To effectively manage BOMs throughout the PCB design and manufacturing process, consider the following best practices:
-
Establish a clear BOM management process: Define a structured process for creating, updating, and sharing BOMs. This process should include roles and responsibilities, approval workflows, and version control mechanisms.
-
Use a centralized BOM repository: Store all BOMs in a centralized repository that is accessible to all relevant stakeholders. This helps ensure that everyone is working with the most up-to-date version of the BOM and reduces the risk of errors or inconsistencies.
-
Implement version control: Use version control to track changes to the BOM over time. This helps maintain a clear audit trail and enables teams to revert to previous versions if necessary.
-
Integrate BOM data with other systems: Integrate BOM data with other systems, such as ERP (Enterprise Resource Planning) or MRP (Material Requirements Planning) software. This helps ensure that BOM information is consistently used across the organization and enables better decision-making and planning.
-
Conduct regular BOM reviews: Schedule regular BOM reviews with cross-functional teams to verify the accuracy and completeness of the BOM. These reviews can help identify potential issues early in the design process and ensure that the BOM meets the requirements of all stakeholders.
By following these best practices, companies can improve the accuracy and efficiency of their BOM management processes, ultimately leading to better PCB design and manufacturing outcomes.
Frequently Asked Questions (FAQ)
1. What is the difference between a BOM and a parts list?
A BOM (Bill of Materials) is a comprehensive list of all the components, materials, and sub-assemblies required to manufacture a product. It includes detailed information about each component, such as the reference designator, quantity, manufacturer part number, and supplier information.
A parts list, on the other hand, is a simplified version of a BOM that typically only includes the component names, quantities, and sometimes the manufacturer part numbers. Parts lists are often used for quick reference or for sharing with external stakeholders who do not require the full level of detail provided in a BOM.
2. How do I handle component substitutions in a BOM?
Component substitutions can be managed in a BOM by:
- Clearly indicating the preferred component and any approved substitutes in the BOM.
- Including notes or comments to provide guidance on when and how to use substitute components.
- Updating the BOM whenever a substitution is made, and communicating the change to all relevant stakeholders.
- Maintaining a separate list of approved substitute components that can be referenced when needed.
It’s important to carefully evaluate any potential substitutions to ensure that they meet the required specifications and do not impact the overall performance or reliability of the PCB.
3. How do I ensure consistency between the BOM and the PCB design files?
To ensure consistency between the BOM and the PCB design files, follow these practices:
- Use automated BOM generation features in your PCB design tools to create the BOM directly from the schematic and layout.
- Regularly compare the BOM with the design files to identify and resolve any discrepancies.
- Implement version control for both the BOM and the design files, and ensure that they are always in sync.
- Establish clear communication channels between the design team and the BOM management team to facilitate collaboration and ensure that any changes are properly documented and reflected in both the BOM and the design files.
4. What should I do if a component in the BOM becomes obsolete?
If a component in the BOM becomes obsolete, take the following steps:
- Identify a suitable replacement component that meets the required specifications and is available from reliable suppliers.
- Update the BOM to include the new component, clearly indicating that it is a replacement for the obsolete part.
- Communicate the change to all relevant stakeholders, including the design team, purchasing department, and manufacturing partners.
- Test and validate the new component to ensure that it performs as expected and does not introduce any compatibility issues.
- Update any affected design files, such as schematics and layouts, to reflect the component change.
It’s important to proactively monitor the lifecycle status of components in the BOM and plan for potential obsolescence to minimize disruptions to the PCB design and manufacturing process.
5. How can I optimize my BOM for cost reduction?
To optimize your BOM for cost reduction, consider the following strategies:
- Standardize components: Use standard, readily available components whenever possible to leverage economies of scale and reduce procurement costs.
- Consolidate suppliers: Reduce the number of suppliers and consolidate purchases to negotiate better prices and terms.
- Evaluate alternative components: Consider using alternative components that offer similar performance at a lower cost.
- Optimize component quantities: Analyze the BOM to identify opportunities to reduce the number of components or consolidate similar components to minimize waste and excess inventory.
- Leverage volume discounts: Take advantage of volume discounts by combining the demand for similar components across multiple products or projects.
- Design for manufacturability: Collaborate with the design team to optimize the PCB design for manufacturability, which can help reduce assembly costs and minimize the risk of defects.
By continuously reviewing and optimizing the BOM, companies can identify opportunities to reduce costs while maintaining the quality and reliability of their PCB designs.
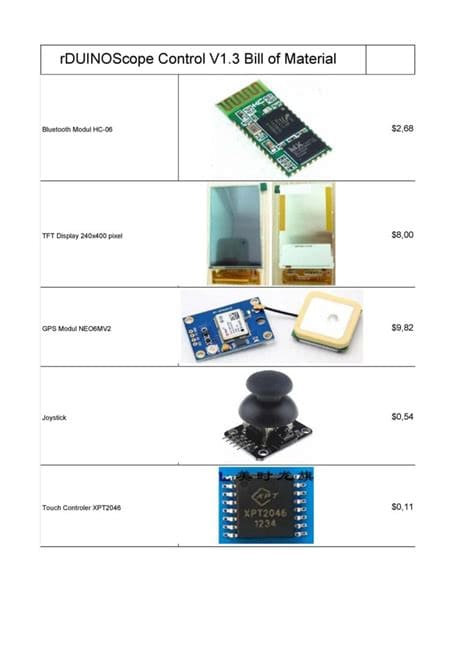
Conclusion
In conclusion, a Bill of Materials (BOM) is a critical document in PCB design that plays a vital role in ensuring the successful fabrication and assembly of a PCB. By providing a comprehensive list of all the required components, a well-crafted BOM streamlines the procurement, assembly, and quality control processes, ultimately leading to more efficient and cost-effective PCB manufacturing.
To create and maintain accurate and effective BOMs, it’s essential to follow best practices such as using consistent naming conventions, collaborating closely with the design team, and leveraging the features of modern PCB design tools. By integrating BOM management with supply chain planning and continuously optimizing the BOM for cost reduction, companies can improve their overall PCB design and manufacturing outcomes.
As PCB designs become increasingly complex and supply chains become more global, the importance of effective BOM management will only continue to grow. By staying up-to-date with the latest tools, techniques, and best practices for BOM management, PCB designers and manufacturers can position themselves for success in an ever-evolving industry.
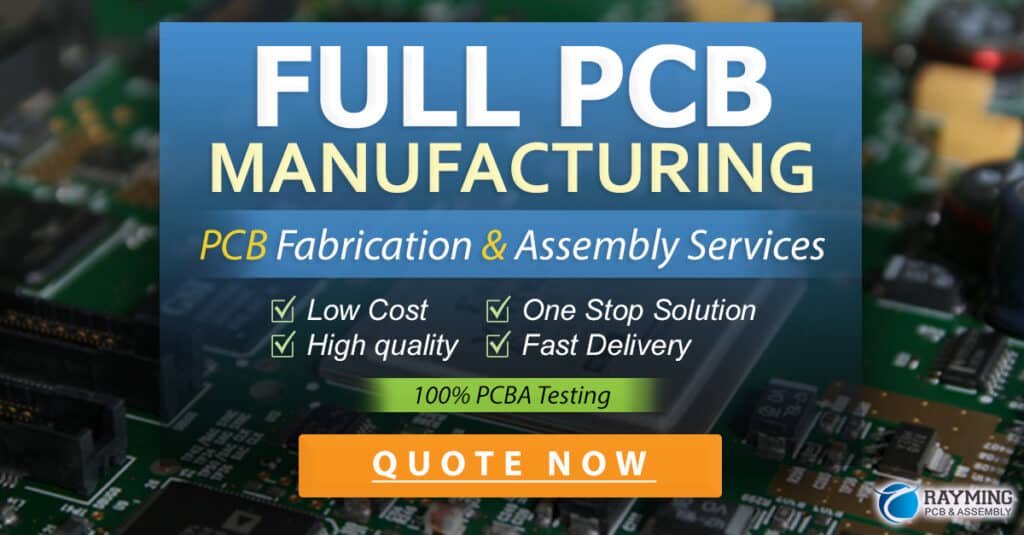
No responses yet