What is PCB Thickness Tolerance?
PCB thickness tolerance refers to the acceptable variation in the thickness of a printed circuit board (PCB) from the nominal or specified thickness. It is a crucial manufacturing parameter that affects the mechanical, electrical, and thermal properties of the PCB.
The thickness of a PCB is determined by the number of layers, the thickness of each layer, and the thickness of the dielectric material between the layers. The nominal thickness is the intended or designed thickness, while the actual thickness may vary due to manufacturing processes and material variations.
PCB thickness tolerance is typically expressed as a ± value, indicating the maximum allowable deviation from the nominal thickness. For example, a PCB with a nominal thickness of 1.6mm and a tolerance of ±10% would have an acceptable thickness range of 1.44mm to 1.76mm.
Why is PCB Thickness Tolerance Important?
PCB thickness tolerance is important for several reasons:
-
Mechanical Integrity: The thickness of a PCB affects its mechanical strength and rigidity. A PCB that is too thin may be prone to warping, bending, or cracking, especially during handling and assembly. A PCB that is too thick may not fit into the intended enclosure or may add unnecessary weight to the final product.
-
Electrical Performance: The thickness of a PCB affects its electrical properties, such as impedance, capacitance, and inductance. Variations in thickness can cause inconsistencies in these properties, leading to signal integrity issues, crosstalk, and electromagnetic interference (EMI).
-
Thermal Management: The thickness of a PCB also affects its Thermal Conductivity and heat dissipation capabilities. A thicker PCB may provide better thermal management, especially for high-power applications, while a thinner PCB may be more prone to overheating and thermal stress.
-
Manufacturing Feasibility: PCB thickness tolerance is important for manufacturing feasibility and yield. If the tolerance is too tight, it may be difficult or expensive to manufacture the PCB consistently. If the tolerance is too loose, it may result in a high rejection rate and waste of materials.
Factors Affecting PCB Thickness Tolerance
Several factors can affect the thickness tolerance of a PCB during manufacturing:
Material Thickness Variation
The thickness of the raw materials used in PCB manufacturing, such as Copper Foils, prepregs, and laminates, can vary from batch to batch or even within the same batch. These variations can accumulate and contribute to the overall thickness variation of the finished PCB.
Pressing and Lamination Process
The pressing and lamination process, where the layers of the PCB are bonded together under heat and pressure, can also affect the thickness tolerance. Uneven pressure distribution, temperature fluctuations, or incorrect pressing time can cause variations in the thickness of the finished PCB.
Etching and Plating Process
The etching and plating processes, used to create the conductive traces and vias on the PCB, can also affect the thickness tolerance. Over-etching or under-etching can change the thickness of the copper layers, while variations in the plating thickness can affect the overall thickness of the PCB.
Drilling and Routing Process
The drilling and routing processes, used to create holes and cut the PCB to its final shape, can also affect the thickness tolerance. Dull or worn-out drill bits or router bits can cause variations in the depth of the holes or the thickness of the routed edges.
Managing PCB Thickness Tolerance
To manage PCB thickness tolerance effectively, several strategies can be employed:
Design for Manufacturability (DFM)
Designing the PCB with manufacturability in mind can help minimize thickness variations. This includes:
- Specifying realistic thickness tolerances based on the capabilities of the manufacturing process and the requirements of the application.
- Avoiding unnecessary thickness changes or transitions within the same PCB.
- Using symmetrical stack-ups and balancing the Copper Distribution across layers to minimize warpage.
- Providing clear and unambiguous thickness specifications and requirements to the manufacturer.
Material Selection and Control
Selecting high-quality and consistent raw materials can help reduce thickness variations. This includes:
- Using materials from reputable suppliers with tight thickness tolerances and consistent quality.
- Verifying the thickness and quality of incoming materials through incoming inspection and testing.
- Storing materials properly to avoid moisture absorption, oxidation, or other degradation that can affect thickness.
Process Control and Monitoring
Implementing strict process controls and monitoring can help maintain consistent thickness throughout manufacturing. This includes:
- Establishing and following standard operating procedures (SOPs) for each manufacturing process step.
- Monitoring process parameters such as temperature, pressure, time, and speed, and adjusting them as necessary to maintain consistency.
- Using statistical process control (SPC) techniques to monitor thickness variations and identify trends or anomalies.
- Conducting regular maintenance and calibration of equipment to ensure accurate and repeatable performance.
Inspection and Testing
Performing regular inspection and testing can help catch thickness variations early and prevent defective PCBs from reaching the customer. This includes:
- Conducting visual inspection of the PCB surface and edges for any visible thickness variations or defects.
- Using thickness gauges or micrometers to measure the thickness of the PCB at multiple points and compare it to the specified tolerance.
- Performing microsectioning or cross-sectioning analysis to examine the internal structure and thickness of the PCB layers.
- Conducting electrical testing to verify that the PCB meets the required performance specifications and tolerances.
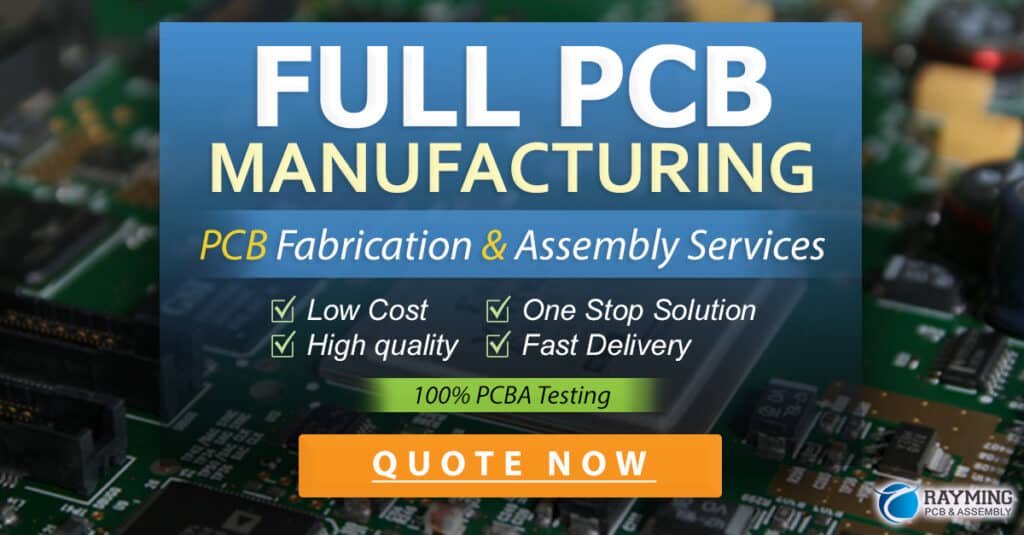
PCB Thickness Tolerance Standards and Specifications
Several industry standards and specifications provide guidance on PCB thickness tolerances:
IPC-6012
IPC-6012, “Qualification and Performance Specification for Rigid Printed Boards,” is a widely used standard that specifies the requirements for PCB thickness tolerances based on the PCB class and the nominal thickness. For example:
Class | Nominal Thickness (mm) | Tolerance (mm) |
---|---|---|
1, 2 | ≤ 1.57 | ± 0.17 |
1, 2 | > 1.57 | ± 10% |
3 | All | ± 10% |
IPC-2221
IPC-2221, “Generic Standard on Printed Board Design,” provides general guidelines for PCB design, including recommendations for thickness tolerances based on the number of layers and the manufacturing process. For example:
Number of Layers | Thickness Tolerance |
---|---|
1 – 4 | ± 10% |
5 – 8 | ± 10% |
9 – 20 | ± 10% |
MIL-PRF-55110
MIL-PRF-55110, “Printed Wiring Board, Rigid, General Specification For,” is a military standard that specifies the requirements for PCB thickness tolerances for military and aerospace applications. It defines thickness tolerances based on the PCB type and the nominal thickness. For example:
Type | Nominal Thickness (mm) | Tolerance (mm) |
---|---|---|
1, 2 | ≤ 2.36 | ± 0.23 |
1, 2 | > 2.36 | ± 10% |
3 | All | ± 10% |
Frequently Asked Questions (FAQ)
1. What is the typical thickness tolerance for a standard 1.6mm PCB?
A: For a standard 1.6mm PCB, the typical thickness tolerance is ±10% according to IPC-6012 Class 2. This means the acceptable thickness range is 1.44mm to 1.76mm.
2. Can I specify a tighter thickness tolerance for my PCB?
A: Yes, you can specify a tighter thickness tolerance for your PCB, but it may increase the manufacturing cost and lead time. Tighter tolerances may require more precise materials, processes, and controls, which can be more expensive and time-consuming. It’s important to discuss your requirements with your PCB Manufacturer and find a balance between tolerance, cost, and feasibility.
3. What happens if the PCB thickness is out of tolerance?
A: If the PCB thickness is out of tolerance, it may affect the mechanical, electrical, and thermal performance of the PCB. Depending on the severity and the application, out-of-tolerance PCBs may be rejected, reworked, or used with deviations. In some cases, out-of-tolerance PCBs may cause assembly issues, reliability problems, or even failures in the field.
4. How can I measure the thickness of my PCB?
A: You can measure the thickness of your PCB using various methods, such as:
- Using a digital caliper or micrometer to measure the thickness at multiple points along the edges and compare it to the specified tolerance.
- Using a thickness gauge or a coordinate measuring machine (CMM) to measure the thickness across the surface of the PCB.
- Performing a microsection or cross-section analysis to measure the thickness of individual layers and the overall thickness of the PCB.
It’s important to use calibrated and accurate measurement tools and follow the appropriate measurement procedures to ensure reliable results.
5. How does PCB thickness affect the impedance of controlled impedance traces?
A: PCB thickness is one of the factors that affect the impedance of controlled impedance traces, along with trace width, trace spacing, and dielectric constant of the substrate material. In general, a thicker dielectric layer between the trace and the reference plane will result in a higher characteristic impedance, while a thinner dielectric layer will result in a lower characteristic impedance.
For example, for a microstrip trace on a PCB with a dielectric constant of 4.0, the characteristic impedance can be approximated by the following formula:
Z0 = 87 / √(εr + 1.41) * ln(5.98 * h / (0.8 * w + t))
Where:
– Z0 is the characteristic impedance in ohms
– εr is the dielectric constant of the substrate material
– h is the thickness of the dielectric layer in mils
– w is the width of the trace in mils
– t is the thickness of the trace in mils
As you can see, the thickness of the dielectric layer (h) has a direct impact on the characteristic impedance. If the PCB thickness is out of tolerance, it can cause variations in the impedance of controlled impedance traces, leading to signal integrity issues and performance degradation.
To minimize the impact of thickness variations on impedance, it’s important to:
- Specify the nominal thickness and tolerance of the PCB based on the impedance requirements and the manufacturing capabilities.
- Use a symmetrical stack-up and maintain a consistent dielectric thickness between the trace and the reference plane.
- Design the controlled impedance traces with sufficient margin and tolerance to accommodate minor thickness variations.
- Work closely with the PCB manufacturer to ensure that the PCB thickness and impedance are within the specified tolerances and meet the performance requirements.
In summary, PCB thickness tolerance is a critical aspect of PCB manufacturing that affects the mechanical, electrical, and thermal performance of the final product. By understanding the factors that affect thickness tolerance, implementing appropriate design and manufacturing strategies, and following industry standards and best practices, designers and manufacturers can ensure that PCBs meet the required thickness specifications and perform reliably in the intended application.
No responses yet