Understanding the Importance of Copper Distribution in PCB Design
Copper distribution is a critical aspect of printed circuit board (PCB) design that directly impacts the performance, reliability, and manufacturability of electronic devices. The proper layout and distribution of copper on a PCB panel ensure effective signal transmission, heat dissipation, and mechanical stability. This article delves into the intricacies of copper distribution, exploring its significance, design considerations, and best practices for optimizing PCB Performance.
The Role of Copper in PCBs
Copper is the primary conductive material used in PCBs due to its excellent electrical conductivity, thermal conductivity, and relatively low cost. In a typical PCB, copper is used to create conductive traces, planes, and vias that interconnect electronic components and facilitate signal transmission. The thickness and width of copper traces determine their current-carrying capacity and resistance, which are crucial factors in PCB design.
Factors Affecting Copper Distribution
Several factors influence the distribution of copper on a PCB panel:
-
Signal Integrity: Proper copper distribution is essential for maintaining signal integrity. The width, spacing, and length of copper traces must be carefully designed to minimize signal reflections, crosstalk, and electromagnetic interference (EMI).
-
Power Distribution: Copper planes and traces distribute power to various components on the PCB. The thickness and width of these copper features must be sufficient to handle the required current without excessive voltage drop or heat generation.
-
Thermal Management: Copper’s high thermal conductivity helps dissipate heat generated by electronic components. Adequate copper coverage and proper placement of thermal vias can prevent hot spots and ensure efficient heat transfer to the PCB’s surface.
-
Manufacturing Constraints: PCB manufacturers have specific requirements and limitations regarding copper distribution. Minimum trace width, spacing, and hole size must be considered to ensure manufacturability and reduce production costs.
Designing for Optimal Copper Distribution
Trace Width and Spacing
The width and spacing of copper traces are critical parameters in PCB design. Trace width determines the current-carrying capacity and resistance of the trace, while spacing affects signal integrity and EMI performance. The following table provides general guidelines for trace width and spacing based on the copper thickness and signal frequency:
Copper Thickness (oz) | Trace Width (mm) | Trace Spacing (mm) | Maximum Frequency (MHz) |
---|---|---|---|
0.5 | 0.15 | 0.15 | 100 |
1.0 | 0.20 | 0.20 | 500 |
2.0 | 0.30 | 0.30 | 1000 |
Note: These values are approximate and may vary based on specific design requirements and manufacturing capabilities.
Power and Ground Planes
Power and ground planes are large copper areas that provide a low-impedance path for power distribution and serve as a reference for signal traces. The use of planes offers several advantages:
- Reduced impedance and voltage drop
- Improved signal integrity and EMI performance
- Enhanced heat dissipation
When designing power and ground planes, consider the following:
- Use separate planes for different voltage levels to prevent noise coupling
- Maintain adequate clearance between planes and signal traces to minimize capacitive coupling
- Utilize appropriate decoupling capacitors near power pins to suppress high-frequency noise
Via Placement and Optimization
Vias are conductive holes that connect different layers of a multi-layer PCB. Proper via placement and optimization are crucial for maintaining signal integrity and minimizing signal reflections. Consider the following guidelines:
- Place vias as close to the signal source or destination as possible to reduce trace length and impedance discontinuities
- Use appropriate via sizes and pad diameters based on the signal frequency and current requirements
- Employ via stitching techniques to create low-impedance paths for high-speed signals and to minimize EMI
Thermal Management Techniques
Effective thermal management is essential for ensuring the long-term reliability and performance of electronic devices. Copper distribution plays a vital role in heat dissipation. Consider the following techniques:
-
Copper Pours: Use large copper pours on unused areas of the PCB to increase the overall copper coverage and improve heat dissipation.
-
Thermal Vias: Place thermal vias near heat-generating components to provide a low-resistance path for heat transfer to the PCB’s surface or dedicated heatsinks.
-
Heatsinks and Thermal Interface Materials: Attach heatsinks to high-power components and use thermal interface materials (TIMs) to enhance heat transfer between the component and the heatsink.
The table below summarizes common thermal management techniques and their effectiveness:
Technique | Effectiveness | Application |
---|---|---|
Copper Pours | Moderate | General heat dissipation |
Thermal Vias | High | Localized heat transfer |
Heatsinks | High | High-power components |
Thermal Interface Materials | High | Enhancing heat transfer efficiency |
Manufacturing Considerations
Copper Balancing
Copper balancing is the process of equalizing the amount of copper on each layer of a multi-layer PCB to prevent warping and ensure consistent etching. Unbalanced copper distribution can lead to manufacturing defects and affect the PCB’s mechanical stability. To achieve proper copper balancing:
- Distribute copper evenly across all layers
- Add copper fills or dummy traces in sparse areas
- Use the same copper thickness for all layers
Panelization and Routing
Panelization is the process of arranging multiple PCBs on a single panel for efficient manufacturing. Proper panelization and routing techniques optimize copper distribution and minimize waste. Consider the following:
- Use uniform copper distribution across the panel to ensure consistent etching and plating
- Maintain adequate spacing between individual PCBs to allow for proper routing and depanelization
- Employ mouse bites or v-grooves for easy depanelization without damaging the PCBs
Design for Manufacturing (DFM)
Design for Manufacturing (DFM) is a methodology that incorporates manufacturing considerations into the PCB design process to improve yield, reduce costs, and ensure product quality. DFM guidelines related to copper distribution include:
- Adhering to the manufacturer’s minimum trace width and spacing requirements
- Avoiding acute angles and sharp corners in copper traces to prevent acid traps during etching
- Using teardrop-shaped pad-to-trace connections to enhance mechanical strength and reduce stress concentrations
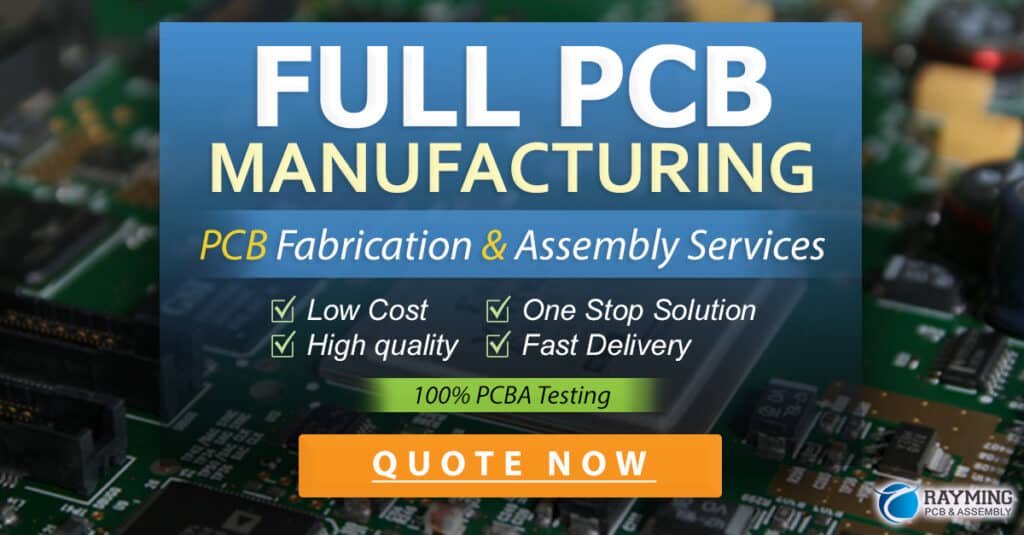
Frequently Asked Questions (FAQ)
1. What is the minimum trace width and spacing for a typical PCB?
The minimum trace width and spacing depend on the PCB manufacturer’s capabilities and the specific design requirements. Common minimum values range from 0.1 mm to 0.2 mm for trace width and spacing. However, it’s essential to consult with the manufacturer and adhere to their guidelines to ensure manufacturability and reliability.
2. How does copper thickness affect current-carrying capacity?
The current-carrying capacity of a copper trace increases with its thickness. Thicker copper traces have lower resistance and can handle higher currents without excessive heating. The standard copper thicknesses used in PCBs are 0.5 oz (17.5 μm), 1 oz (35 μm), and 2 oz (70 μm). Doubling the copper thickness allows the trace to carry approximately twice the current.
3. What is the purpose of copper pours on a PCB?
Copper pours, also known as copper fills or ground planes, serve multiple purposes on a PCB:
- They provide a low-impedance return path for signals, reducing loop area and minimizing EMI
- They increase the overall copper coverage, aiding in heat dissipation and improving thermal performance
- They enhance the mechanical stability of the PCB by balancing copper distribution and reducing warping
4. How can I optimize copper distribution for high-speed signals?
To optimize copper distribution for high-speed signals, consider the following techniques:
- Use controlled impedance traces with well-defined width and spacing to maintain signal integrity
- Employ ground planes adjacent to high-speed signal layers to provide a consistent reference and minimize crosstalk
- Place decoupling capacitors close to power pins to suppress high-frequency noise and maintain power integrity
- Use via stitching and ground vias to create low-impedance return paths and minimize signal reflections
5. What are the consequences of unbalanced copper distribution in a multi-layer PCB?
Unbalanced copper distribution in a multi-layer PCB can lead to several issues:
- Warping: Uneven copper distribution can cause the PCB to warp during the manufacturing process, resulting in mechanical stress and potential reliability issues
- Inconsistent etching: Unbalanced copper can lead to inconsistent etching rates, affecting the uniformity and accuracy of trace widths and spacing
- Reduced mechanical strength: Non-uniform copper distribution can weaken the overall mechanical strength of the PCB, making it more susceptible to damage during assembly and operation
Conclusion
Copper distribution is a fundamental aspect of PCB design that directly impacts the performance, reliability, and manufacturability of electronic devices. By understanding the principles of copper distribution and applying best practices in trace design, power distribution, thermal management, and manufacturing considerations, designers can create high-quality PCBs that meet the demanding requirements of modern electronics.
Effective copper distribution requires a balance between signal integrity, power delivery, thermal management, and manufacturing constraints. Designers must carefully consider factors such as trace width and spacing, power and ground planes, via placement, and thermal management techniques to optimize PCB performance. Additionally, adhering to manufacturing guidelines and employing DFM principles ensures the producibility and reliability of the final product.
As technology advances and electronic devices become more complex, the importance of proper copper distribution will only continue to grow. By staying informed about the latest design techniques and collaborating closely with PCB manufacturers, designers can navigate the challenges of copper distribution and create innovative, high-performance electronic products that push the boundaries of what is possible.
No responses yet