Why PCB Environmental Control is Critical
Printed circuit boards (PCBs) are the foundation of virtually all modern electronic devices. Proper PCB environmental control in the manufacturing process is essential to ensure high quality, reliability and performance of the final products. Two key environmental factors that must be tightly controlled are light and moisture.
Excess light exposure, especially to UV light, can prematurely cure and harden photoresists and solder masks, leading to manufacturing defects. Moisture in the air and on surfaces can cause oxidation, corrosion, warping, delamination and other moisture-related PCB failure modes. Careful control of light and humidity levels in the PCB factory environment is critical.
Risks of Light Exposure in PCB Manufacturing
UV Light Curing of Photoresists and Solder Masks
Many PCB manufacturing processes use photoimageable coatings like photoresists for etching patterns and solder masks for protecting conductive traces. These polymer coatings are applied in liquid form and then hardened by exposure to ultraviolet (UV) light. The UV light causes cross-linking of the polymers, curing them into a permanent solid coating.
However, any unintended or excess UV light exposure will prematurely begin the curing process. This can lead to a host of PCB defects and failures, including:
- Loss of fine feature resolution
- Inconsistent hardening and durability of coatings
- Poor adhesion of photoresists and solder masks
- Inability to properly develop and strip away unexposed areas
Therefore, it’s critical to shield PCBs from ambient UV light exposure except during the specific curing steps. This is achieved by:
- Using UV-blocking filters on windows and lighting
- Fully enclosing UV curing equipment
- Handling PCBs under yellow safelights that don’t emit UV
Preventing Operator Eye Damage
Excess UV light exposure is also a safety hazard for PCB manufacturing workers. High intensity UV lamps used for curing can cause eye damage and increase risk of cataracts. UV-blocking protective eyewear is required for operators working around curing equipment.
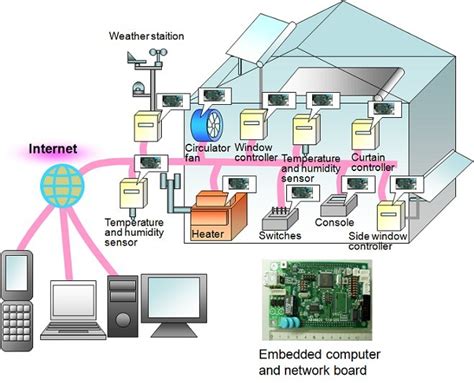
Risks of Moisture in PCB Manufacturing
Oxidation and Corrosion
One of the biggest risks of moisture in PCB manufacturing is promoting oxidation and corrosion of metals. Copper traces, solder joints, and other metal surfaces on the PCB can corrode when exposed to moisture and oxygen in the air. Some key factors include:
- Relative humidity (RH) levels
- Presence of ionic contaminants
- Applied voltage bias (in use)
- Temperature
Higher moisture accelerates the corrosion reactions. Ionic contamination from PCB processes, handling, and environment can worsen corrosion by increasing conductivity. Applied voltage bias drives electrochemical corrosion. Higher temperatures speed up reaction kinetics.
Corroded metals can cause both catastrophic and latent PCB failures. Shorts, opens, and current leakage are common issues. Corrosion products also weaken solder joints. So it’s critical to maintain low humidity in the PCB factory environment.
PCB Material Instability
Many PCB Substrate and laminate materials are hygroscopic, readily absorbing and holding moisture from the air. Common PCB materials like FR-4 are organic composites of woven fiberglass cloth impregnated with epoxy resin. Both the fiber reinforcement and the polymer matrix can take up moisture.
Absorption of moisture causes PCB materials to swell and distort. If the moisture content is high enough, rapid heating (like during soldering) will vaporize the water and cause measling, blistering, and delamination of the board. Moisture also degrades the dielectric properties and increases losses for high frequency PCBs.
So it’s important to control moisture exposure throughout PCB manufacturing, storage, and transport. Humid environments will require baking PCBs to drive off moisture before thermal processes like soldering. Sealed moisture barrier bags with desiccants are used to keep PCBs dry in storage and shipping.
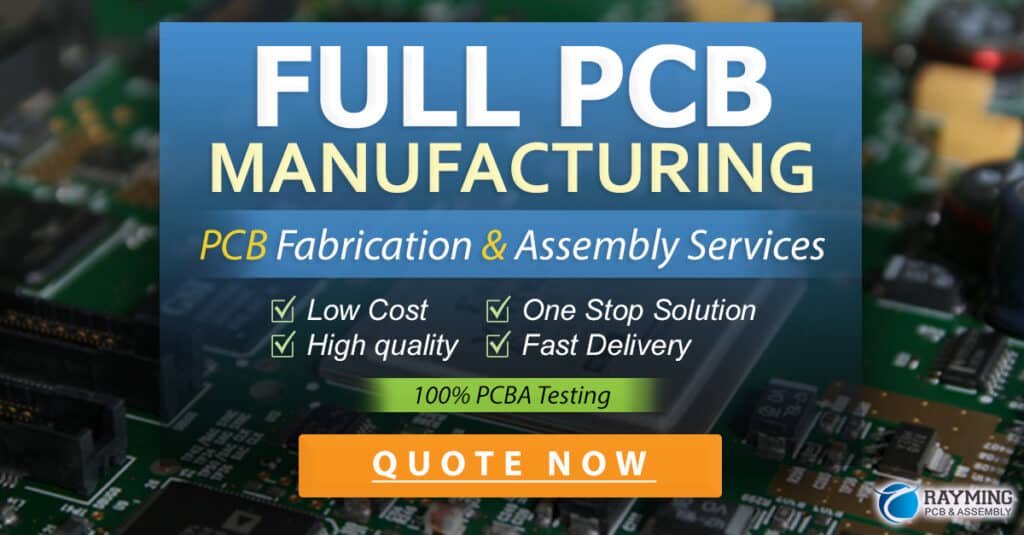
Controlling Light in the PCB Factory
UV-Blocking Filters
Ambient lighting in PCB manufacturing areas should use UV-blocking filters to minimize stray UV light that could prematurely cure photoresists or solder masks. Fluorescent lamps naturally emit some near-UV, and UV energy is present in natural daylight coming through windows.
Special sleeves or films applied to fluorescent lamps can filter out UV emissions. For windows, UV-blocking films and coatings on the glass are used. Alternatively, windows in the PCB production area can simply be covered with opaque barriers.
Safelighting
Often PCBs need to be visually inspected or handled by operators during photoresist and solder mask processing steps. This is done under yellow “safelights” that illuminate the work area without emitting UV wavelengths that could affect the polymers.
Safelights use specific wavelengths, often in the yellow region around 580 nm, that don’t overlap with the UV sensitivity spectrum of the photoimageable coatings being used. This allows operators to safely work with the PCBs while still protecting them from ambient UV.
Enclosed UV Curing
The high intensity UV lamps used for intentionally curing photoresists and solder masks are fully enclosed. The PCBs are transported into a light-tight chamber where they are exposed to the UV light source for a controlled time. This ensures that the UV exposure only occurs when and where intended in the process.
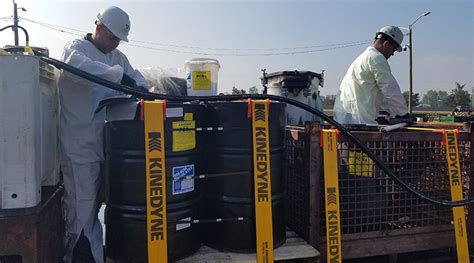
Controlling Moisture in the PCB Factory
Humidity Control
The most important factor in controlling moisture in PCB manufacturing is humidity control. Relative humidity (RH) is a measure of the amount of moisture held in the air compared to the maximum possible at that temperature. At 100% RH, the air is fully saturated, while 0% RH air is completely dry.
For general PCB manufacturing and assembly, the recommended relative humidity range is 30-50% RH. This provides a good balance, dry enough to prevent most moisture-related issues but not so dry as to promote electrostatic discharge (ESD) problems.
Some key elements of humidity control in the PCB factory include:
- Humidity sensors to continuously monitor RH levels
- Dehumidification to remove excess moisture from the air
- Humidification to add moisture if RH drops too low
- Insulation and sealing of the PCB production area from outside humid air
- Humidity-controlled storage for materials and PCBs
The specific humidity control setpoints will depend on the PCB types, materials, and processes being used in the facility. IPC standards offer guidance on acceptable ranges.
Dealing with Moisture Sensitive Devices
Even if humidity is well-controlled in the PCB factory, some components are inherently sensitive to moisture exposure. Many semiconductors and other electronic components are moisture-sensitive devices (MSDs).
MSDs absorb moisture from the air, so they are shipped dry in moisture barrier bags with desiccants inside and humidity indicator cards to monitor moisture exposure. Each MSD has a moisture sensitivity level (MSL) rating that specifies the maximum time it can be exposed to ambient humidity before it must be dried out again.
When building PCB assemblies that contain MSDs, special moisture-sensitive handling and storage procedures are required:
- MSDs must be dry baked before use if exposed too long
- Exposure times during PCB Assembly must be limited
- Partially assembled PCBs with MSDs must be stored in dry cabinets or nitrogen boxes
- Baking ovens must be available in the factory to dry MSDs as needed
Following the J-STD-033 handling standard for MSDs is important to prevent moisture-related component failures in PCB assemblies.
FAQ
What are the ideal humidity and temperature levels for a PCB factory?
For general PCB manufacturing, 30-50% RH and 68-77°F (20-25°C) are the recommended ranges for humidity and temperature in the production environment. The specific ideal ranges may vary depending on the exact PCB technology and processes being used.
How can I measure the humidity in my PCB factory?
Humidity sensors, also known as hygrometers, are used to measure and monitor relative humidity. These instruments use various methods to detect moisture in the air, such as capacitance changes or resistivity of a material. For monitoring a PCB factory, robust industrial-grade humidity sensors with digital output are often used. These can connect to a building management system or local alarm to maintain the humidity in the desired range.
What type of UV blocking sleeves are used on fluorescent lamps for PCB manufacturing?
UV-blocking sleeves for fluorescent lamps are typically made of polycarbonate or acrylic plastic that is transparent to visible light but blocks the transmission of UV-A and UV-B wavelengths. These attach to the outside of the fluorescent bulb. Some fluorescent lamps are also available with the UV-blocking material applied directly to the inside of the bulb glass.
How long will a desiccant bag last in an MSD bag?
The lifespan of a desiccant in a moisture barrier bag depends on the type and amount of desiccant, bag size, bag seal quality, and external humidity levels. For a well-sealed bag in a humidity-controlled environment, desiccants can be effective for months to years. Humidity indicator cards (HICs) should be used to monitor the interior humidity of the bag. If the HIC shows humidity has breached a critical level, the desiccant has been exhausted and must be regenerated or replaced to continue protecting the contents.
What is the recommended baking procedure for a moisture-sensitive PCB?
Refer to J-STD-033 for the detailed baking procedures for MSDs. In general, baking is done at 125°C for 6-24 hours, with the specific time depending on the MSL rating and thickness of the device. The bake time must be sufficient to reduce the moisture content to a safe level, but not so long as to cause thermal damage. Desiccant or dry nitrogen storage cabinets can also be used for lower MSL devices.
Conclusion
In summary, careful control of light and moisture is essential for high quality, reliable PCB manufacturing. UV exposure must be limited to prevent premature curing of photoimageable coatings. Humidity must be kept low to avoid oxidation, corrosion, material instability, and problems with moisture-sensitive devices.
Effective PCB environmental control includes using UV-blocking filters on lighting, yellow safelighting, and enclosed UV curing equipment to limit stray UV exposure. Humidity control requires monitoring and regulating RH in the PCB production environment, as well as properly storing and handling moisture-sensitive PCBs and components.
By understanding and controlling these key environmental factors, PCB manufacturers can optimize their processes, reduce defects and failures, and ultimately produce higher quality, more reliable electronic products. Investing in the necessary equipment and facilities for proper PCB environmental control is well worth the cost for any serious electronics manufacturer.
No responses yet