Understanding FR4 PCB Substrate
FR4 is a composite material composed of woven fiberglass cloth impregnated with an epoxy resin binder. The “FR” stands for “Flame Retardant,” indicating that the material has been treated to resist the spread of flames in case of a fire. The “4” represents the specific grade of the material, which is determined by its performance under various conditions, such as electrical insulation, mechanical strength, and thermal stability.
FR4 has several advantageous properties that make it an ideal choice for PCB substrates:
- High mechanical strength and dimensional stability
- Excellent electrical insulation properties
- Good thermal stability and resistance to high temperatures
- Resistance to moisture absorption
- Cost-effectiveness and ease of fabrication
Thickness of FR4 PCB Substrates
FR4 substrates are available in a wide range of thicknesses, typically ranging from 0.2 mm to 3.2 mm. The thickness of the substrate is an essential factor to consider when designing your PCB, as it can significantly impact the board’s performance, reliability, and manufacturing process. In general, FR4 substrates can be categorized into two main groups:
- Thin FR4 substrates: Typically less than 1.0 mm thick
- Thick FR4 substrates: Usually 1.0 mm or thicker
The choice between thin and thick FR4 substrates depends on various factors, such as the intended application, electrical requirements, mechanical constraints, and cost considerations.
Thin FR4 PCB Substrates
Thin FR4 substrates, usually less than 1.0 mm thick, are commonly used in applications where space is limited, and weight is a critical factor. Some of the advantages of using thin FR4 substrates include:
Advantages of Thin FR4 Substrates
-
Reduced weight and thickness: Thin FR4 substrates are ideal for applications where a compact and lightweight design is essential, such as in mobile devices, wearables, and aerospace systems.
-
Improved flexibility: Thinner substrates offer better flexibility, which can be advantageous in applications that require the PCB to conform to a specific shape or withstand moderate bending.
-
Enhanced thermal dissipation: In some cases, thin FR4 substrates can provide better thermal dissipation compared to thicker substrates, as the heat generated by components can be more easily transferred to the environment.
-
Lower material cost: Using thinner FR4 substrates can result in cost savings, as less material is required for manufacturing the PCB.
Disadvantages of Thin FR4 Substrates
-
Reduced mechanical strength: Thin FR4 substrates are more susceptible to mechanical stress and damage, especially during the manufacturing process and handling.
-
Increased warping and twisting: Thinner substrates are more prone to warping and twisting due to uneven thermal expansion and contraction during the soldering process.
-
Limitations in layer count: Thin FR4 substrates may not be suitable for complex designs that require a high number of layers, as the reduced thickness can limit the number of layers that can be accommodated.
-
Challenges in impedance control: Maintaining accurate impedance control can be more difficult with thin FR4 substrates, as the reduced thickness can make it harder to achieve the desired dielectric thickness and copper trace geometries.
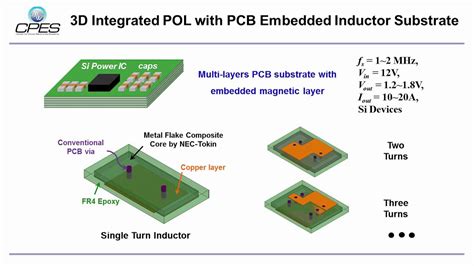
Thick FR4 PCB Substrates
Thick FR4 substrates, typically 1.0 mm or thicker, are commonly used in applications that demand high mechanical strength, stability, and reliability. Some of the advantages of using thick FR4 substrates include:
Advantages of Thick FR4 Substrates
-
Increased mechanical strength: Thick FR4 substrates provide better mechanical support and protection for components, making them more resistant to stress, impact, and vibration.
-
Improved dimensional stability: Thicker substrates are less prone to warping and twisting, ensuring better alignment and registration of layers during the manufacturing process.
-
Higher layer count capability: Thick FR4 substrates can accommodate a greater number of layers, making them suitable for complex designs with high interconnect density.
-
Enhanced thermal management: In some cases, thick FR4 substrates can provide better thermal management by allowing for the incorporation of thicker copper layers and larger heat-dissipating features.
Disadvantages of Thick FR4 Substrates
-
Increased weight and thickness: Thick FR4 substrates can result in a heavier and bulkier PCB, which may not be suitable for applications with stringent size and weight constraints.
-
Higher material cost: Using thicker FR4 substrates can increase the material cost of the PCB, as more material is required for manufacturing.
-
Reduced flexibility: Thicker substrates are generally less flexible than thinner ones, which can be a drawback in applications that require the PCB to conform to a specific shape or withstand bending.
-
Longer drilling and plating times: Thicker substrates may require longer drilling and plating times during the manufacturing process, which can increase production costs and lead times.
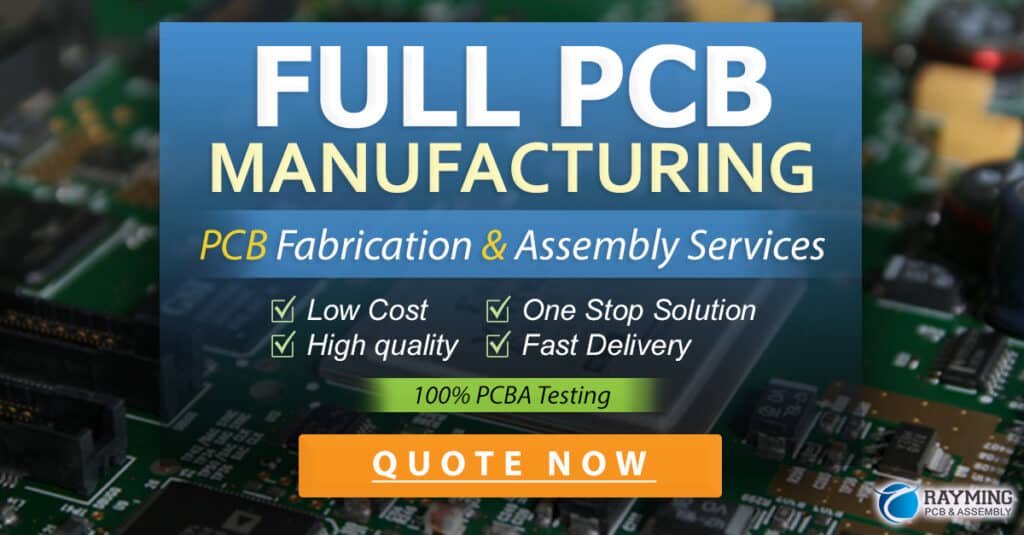
Choosing Between Thick and Thin FR4 Substrates
When deciding between thick and thin FR4 substrates for your PCB project, consider the following factors:
-
Application requirements: Evaluate the specific requirements of your application, such as size constraints, weight limitations, and environmental conditions.
-
Mechanical stability: Assess the need for mechanical strength and stability in your PCB. If your application involves high stress, impact, or vibration, a thicker FR4 substrate may be more suitable.
-
Layer count and complexity: Consider the complexity of your PCB design and the number of layers required. Complex designs with high layer counts may benefit from using a thicker FR4 substrate.
-
Thermal management: Analyze the thermal management requirements of your PCB. In some cases, a thicker substrate may provide better thermal dissipation, while in others, a thinner substrate may be more advantageous.
-
Cost considerations: Evaluate the cost implications of using thick or thin FR4 substrates. Thinner substrates may offer cost savings in terms of material, while thicker substrates may require higher material costs but could potentially save on manufacturing time and complexity.
-
Manufacturing capabilities: Consult with your PCB manufacturer to understand their capabilities and recommendations regarding thick and thin FR4 substrates. Some manufacturers may have specific guidelines or limitations based on their equipment and processes.
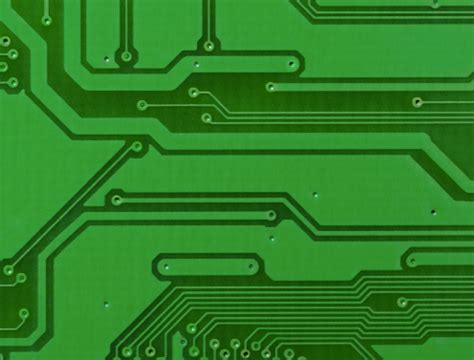
PCB Substrate Thickness Comparison
Thickness (mm) | Typical Applications | Advantages | Disadvantages |
---|---|---|---|
0.2 – 0.8 | Mobile devices, wearables, flexible PCBs | Lightweight, compact, flexible | Reduced mechanical strength, prone to warping |
0.8 – 1.6 | General-purpose PCBs, consumer electronics | Good balance of strength and thickness | Limited layer count, moderate thermal management |
1.6 – 3.2 | High-reliability systems, aerospace, military | High mechanical strength, stability, layer count | Increased weight and thickness, higher material cost |
Frequently Asked Questions (FAQ)
-
What is FR4, and why is it commonly used as a PCB substrate material?
FR4 is a flame-retardant, glass-reinforced epoxy laminate material. It is widely used as a PCB substrate due to its excellent electrical insulation properties, high mechanical strength, thermal stability, and cost-effectiveness. -
How does the thickness of the FR4 substrate affect the performance of a PCB?
The thickness of the FR4 substrate can impact various aspects of PCB performance, such as mechanical strength, dimensional stability, layer count capability, thermal management, and flexibility. Thicker substrates generally provide better mechanical support and stability, while thinner substrates offer reduced weight and increased flexibility. -
What are the typical thickness ranges for thin and thick FR4 substrates?
Thin FR4 substrates are typically less than 1.0 mm thick, while thick FR4 substrates are usually 1.0 mm or thicker. The exact thickness range can vary depending on the specific application and manufacturing capabilities. -
When should I choose a thin FR4 substrate for my PCB?
Thin FR4 substrates are suitable for applications that require a compact and lightweight design, such as mobile devices, wearables, and flexible PCBs. They can also offer benefits in terms of thermal dissipation and cost savings in some cases. -
What are the advantages of using a thick FR4 substrate for my PCB?
Thick FR4 substrates provide increased mechanical strength, improved dimensional stability, and the ability to accommodate a higher number of layers. They are often used in applications that demand high reliability, such as aerospace, military, and industrial systems.
Conclusion
Selecting the appropriate thickness of FR4 substrate for your PCB is a critical decision that can significantly impact the performance, reliability, and cost of your electronic device. Thin FR4 substrates offer advantages in terms of reduced weight, increased flexibility, and potential cost savings, while thick FR4 substrates provide better mechanical strength, stability, and the ability to accommodate more complex designs.
When choosing between thick and thin FR4 substrates, carefully consider your application requirements, mechanical stability needs, layer count and complexity, thermal management, cost implications, and manufacturing capabilities. By understanding the trade-offs and consulting with your PCB manufacturer, you can make an informed decision that ensures the optimal performance and reliability of your PCB.
No responses yet