Introduction to Metal PCBs
Metal core printed circuit boards (MCPCBs) are a specialized type of PCB that uses a metal substrate instead of the traditional FR-4 material. The metal substrate, usually aluminum, provides excellent thermal conductivity, allowing for better heat dissipation from electronic components. This makes metal PCBs an ideal choice for applications that generate a significant amount of heat, such as high-power LEDs, power electronics, and automotive systems.
Key Features of Metal PCBs
- Thermal conductivity: Metal PCBs offer superior thermal conductivity compared to traditional PCBs, enabling efficient heat dissipation.
- Durability: The metal substrate provides increased durability and mechanical strength, making metal PCBs resistant to vibration and shock.
- Lightweight: Aluminum, the most common metal substrate, is lightweight, making metal PCBs suitable for weight-sensitive applications.
- Design flexibility: Metal PCBs can be manufactured in various shapes and sizes to accommodate different design requirements.
Thermal Management Benefits
One of the primary advantages of metal PCBs is their excellent thermal management capabilities. The metal substrate acts as a heat sink, efficiently conducting heat away from electronic components and distributing it evenly across the board. This helps to prevent hotspots and reduces the risk of component failure due to thermal stress.
Comparison of Thermal Conductivity
Material | Thermal Conductivity (W/mK) |
---|---|
Aluminum | 205 |
Copper | 401 |
FR-4 | 0.3 |
As shown in the table above, aluminum and copper, the most common metal substrates used in metal PCBs, have significantly higher thermal conductivity than FR-4, the standard material used in traditional PCBs. This high thermal conductivity enables metal PCBs to dissipate heat more effectively, improving the overall thermal performance of the electronic system.
Thermal Management Techniques
In addition to the inherent thermal conductivity of the metal substrate, several techniques can be employed to further enhance the thermal management capabilities of metal PCBs:
- Thermal vias: These are small holes drilled through the PCB that allow heat to be conducted from the top layer to the metal substrate.
- Thermal interface materials (TIMs): TIMs, such as thermal greases or thermal pads, can be used to improve the thermal contact between the electronic components and the metal substrate.
- Heat spreaders: Additional heat spreaders, such as metal plates or heat pipes, can be attached to the metal PCB to further increase heat dissipation.
By implementing these thermal management techniques, designers can optimize the thermal performance of metal PCBs and ensure that electronic components operate within their specified temperature ranges.
Mechanical Strength and Durability
Another significant advantage of metal PCBs is their enhanced mechanical strength and durability compared to traditional PCBs. The metal substrate provides a rigid backbone that can withstand higher levels of vibration and shock, making metal PCBs suitable for applications that require robust performance in harsh environments.
Vibration and Shock Resistance
Metal PCBs offer superior resistance to vibration and shock compared to traditional PCBs. The metal substrate’s rigidity helps to minimize flexing and bending, which can cause component failure or solder joint cracking. This makes metal PCBs an ideal choice for applications that are subject to high levels of vibration or shock, such as:
- Automotive electronics
- Aerospace systems
- Industrial machinery
- Military equipment
Impact on Product Lifetime
The enhanced mechanical strength and durability of metal PCBs can significantly impact the overall lifetime of the electronic product. By minimizing the risk of component failure due to vibration or shock, metal PCBs can help to extend the product’s lifespan, reducing maintenance costs and increasing reliability.
Furthermore, the improved thermal management capabilities of metal PCBs also contribute to increased product lifetime. By preventing components from overheating, metal PCBs reduce the risk of thermal-related failures, which can significantly extend the product’s lifespan.
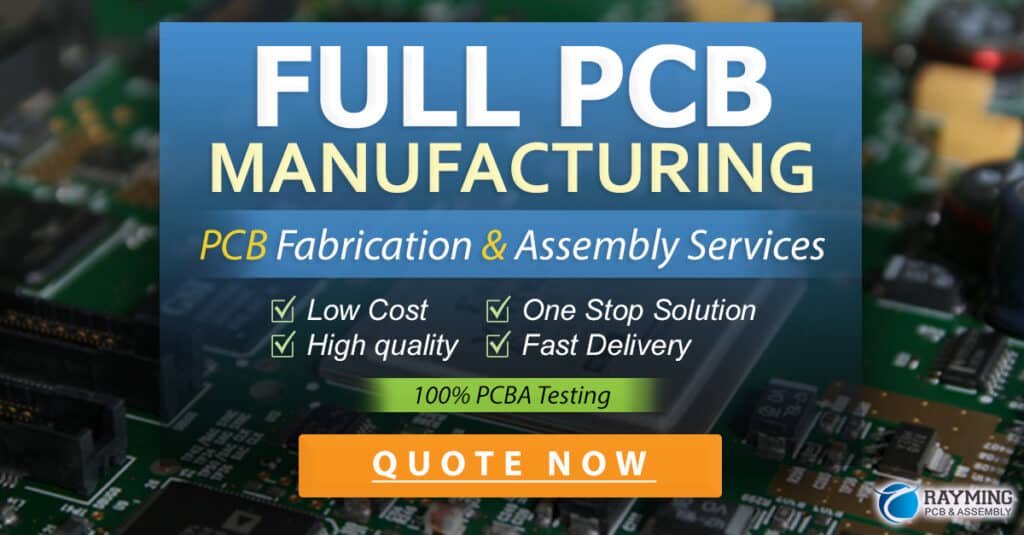
Lightweight Design Advantages
In addition to their thermal and mechanical benefits, metal PCBs offer the advantage of being lightweight, particularly when aluminum is used as the substrate material. This makes metal PCBs an attractive option for weight-sensitive applications, such as aerospace systems or portable electronics.
Aluminum Substrate
Aluminum is the most common metal substrate used in metal PCBs due to its combination of high thermal conductivity, mechanical strength, and lightweight properties. With a density of 2.7 g/cm³, aluminum is significantly lighter than copper (8.96 g/cm³) and even FR-4 (1.85 g/cm³), the standard material used in traditional PCBs.
Weight Comparison
Material | Density (g/cm³) | Relative Weight (compared to FR-4) |
---|---|---|
Aluminum | 2.7 | 1.46 |
Copper | 8.96 | 4.84 |
FR-4 | 1.85 | 1.00 |
As shown in the table above, aluminum is only 1.46 times heavier than FR-4, while copper is nearly five times heavier. This makes aluminum an ideal substrate material for metal PCBs in weight-sensitive applications, as it provides the necessary thermal and mechanical benefits without adding significant weight to the overall system.
Benefits for Weight-Sensitive Applications
The lightweight nature of aluminum-based metal PCBs offers several benefits for weight-sensitive applications:
- Reduced overall system weight: By using metal PCBs instead of traditional PCBs, designers can reduce the overall weight of the electronic system, which is crucial for applications such as aerospace systems or drones.
- Improved fuel efficiency: In automotive applications, reducing the weight of electronic components can lead to improved fuel efficiency and reduced emissions.
- Enhanced portability: For portable electronics, such as laptops or mobile devices, using lightweight metal PCBs can help to reduce the overall device weight, making them more comfortable to carry and use.
Design Flexibility
Metal PCBs offer a high degree of design flexibility, allowing designers to create boards in various shapes and sizes to accommodate different application requirements. This flexibility enables the optimization of board layout and component placement, leading to improved system performance and reduced manufacturing costs.
Customizable Shapes and Sizes
Metal PCBs can be manufactured in a wide range of shapes and sizes, including:
- Rectangular boards
- Circular boards
- Irregular shapes
- Cutouts and openings
This customization allows designers to create metal PCBs that fit perfectly within the available space in the electronic system, optimizing the use of space and minimizing the overall system size.
Multilayer Designs
In addition to customizable shapes and sizes, metal PCBs can also be manufactured in multilayer designs. By combining multiple layers of insulating material and metal substrates, designers can create complex board layouts that accommodate a high density of electronic components.
Multilayer metal PCBs offer several advantages:
- Increased circuit density: Multilayer designs allow for a higher density of electronic components, enabling more compact and efficient system designs.
- Improved signal integrity: By using dedicated layers for power and ground planes, multilayer metal PCBs can help to reduce electromagnetic interference (EMI) and improve signal integrity.
- Enhanced thermal management: Multilayer metal PCBs can incorporate additional metal layers to further enhance heat dissipation and thermal management.
Applications of Metal PCBs
Metal PCBs are used in a wide range of applications that require efficient thermal management, mechanical strength, and lightweight design. Some of the most common applications include:
- High-power LED lighting
- Automotive electronics
- Power electronics
- Aerospace systems
- Industrial control systems
- Medical devices
- Military and defense equipment
In each of these applications, the unique properties of metal PCBs help to ensure reliable performance, extended product lifetime, and optimized system design.
FAQ
1. What is the difference between Metal Core PCBs and traditional PCBs?
Metal core PCBs use a metal substrate, usually aluminum, instead of the traditional FR-4 material. This metal substrate provides superior thermal conductivity, mechanical strength, and lightweight properties compared to FR-4.
2. Can metal PCBs be used in high-frequency applications?
While metal PCBs offer excellent thermal and mechanical properties, they may not be the best choice for high-frequency applications. The metal substrate can cause signal integrity issues due to its high electrical conductivity. For high-frequency applications, traditional PCBs with low-loss dielectric materials are typically preferred.
3. How are components attached to metal PCBs?
Components are attached to metal PCBs using standard soldering techniques, such as reflow soldering or wave soldering. However, it is essential to consider the thermal expansion differences between the metal substrate and the components when designing the solder joints to ensure reliable connections.
4. Can metal PCBs be manufactured with different metal substrates?
Yes, while aluminum is the most common metal substrate used in metal PCBs, other metals such as copper or steel can also be used depending on the specific application requirements.
5. Are metal PCBs more expensive than traditional PCBs?
In general, metal PCBs are more expensive than traditional PCBs due to the additional materials and manufacturing processes involved. However, the increased cost is often justified by the improved thermal management, mechanical strength, and lightweight properties that metal PCBs offer, particularly in applications where these factors are critical to system performance and reliability.
Conclusion
Metal core printed circuit boards offer a range of advantages over traditional PCBs, including superior thermal management, enhanced mechanical strength and durability, lightweight design, and increased design flexibility. By leveraging these benefits, designers can create electronic systems that are more reliable, efficient, and optimized for specific application requirements.
As the demand for high-performance electronics continues to grow across various industries, metal PCBs are poised to play an increasingly important role in enabling the development of advanced technologies. From automotive electronics to aerospace systems and beyond, metal PCBs provide a robust and versatile solution for a wide range of applications.
As designers continue to push the boundaries of electronic system performance, it is clear that metal PCBs will remain an essential tool in their arsenal, offering the thermal, mechanical, and design advantages needed to meet the ever-increasing demands of modern electronics.
No responses yet