Introduction to SolderPastePrep
Solder paste is a crucial component in the surface mount technology (SMT) assembly process. It is a mixture of tiny solder particles suspended in a flux medium, which is applied to the printed circuit board (PCB) pads before component placement. The quality and consistency of the solder paste deposition heavily influence the reliability and performance of the final assembled product. Therefore, proper solder paste data preparation is essential to ensure optimal printing results and minimize defects.
In this article, we will delve into the various aspects of solder paste data preparation, including the importance of paste properties, stencil design, printer setup, and process control. By understanding and implementing best practices in SolderPastePrep, manufacturers can improve their SMT Assembly yields and product quality.
Understanding Solder Paste Properties
Composition and Particle Size Distribution
Solder paste consists of two main components: solder alloy particles and flux. The solder alloy particles are typically made of tin-lead (SnPb) or lead-free alloys such as tin-silver-copper (SAC). The particle size distribution (PSD) of the solder paste is a critical factor that affects its printing and reflow performance. A well-controlled PSD ensures consistent paste deposition and minimizes defects such as bridging, solder balling, and Insufficient Solder joints.
Solder Paste Type | Alloy Composition | Particle Size Range |
---|---|---|
SnPb | Tin-Lead (63/37) | 25-45 μm |
SAC305 | Sn96.5/Ag3.0/Cu0.5 | 25-45 μm |
SAC387 | Sn95.5/Ag3.8/Cu0.7 | 25-45 μm |
Rheology and Viscosity
Solder paste rheology refers to its flow characteristics under applied stress. The viscosity of the solder paste determines its ability to be printed through the stencil apertures and maintain its shape on the PCB pads. Solder paste manufacturers often provide rheology data, including viscosity, thixotropic index, and yield stress, to help users optimize their printing process.
Rheology Parameter | Description | Recommended Range |
---|---|---|
Viscosity | Resistance to flow under applied stress | 150-200 Pa·s |
Thixotropic Index | Ratio of viscosity at low and high shear rates | 1.5-2.5 |
Yield Stress | Minimum stress required to initiate flow | 200-400 Pa |
Stencil Design Considerations
Aperture Size and Shape
The stencil aperture size and shape directly influence the volume and geometry of the solder paste deposited on the PCB pads. Aperture dimensions should be optimized based on the component footprint, pad size, and desired solder joint height. Common aperture shapes include square, rectangular, and circular. In some cases, custom aperture shapes may be necessary to accommodate unique component geometries or to control solder paste deposition in specific areas.
Stencil Thickness and Material
Stencil thickness is another critical factor in determining the volume of solder paste deposited. Thicker stencils generally result in higher solder paste volumes, which can be beneficial for larger components or those with higher stand-off heights. However, thicker stencils may also increase the risk of bridging and other printing defects. Common stencil thicknesses range from 100 to 150 μm for standard SMT assemblies.
Stencil material selection also plays a role in printing performance and durability. Stainless steel is the most common material due to its strength, stability, and ease of cleaning. For fine-pitch applications or those requiring high-precision printing, electroformed nickel stencils or laser-cut stencils may be preferred.
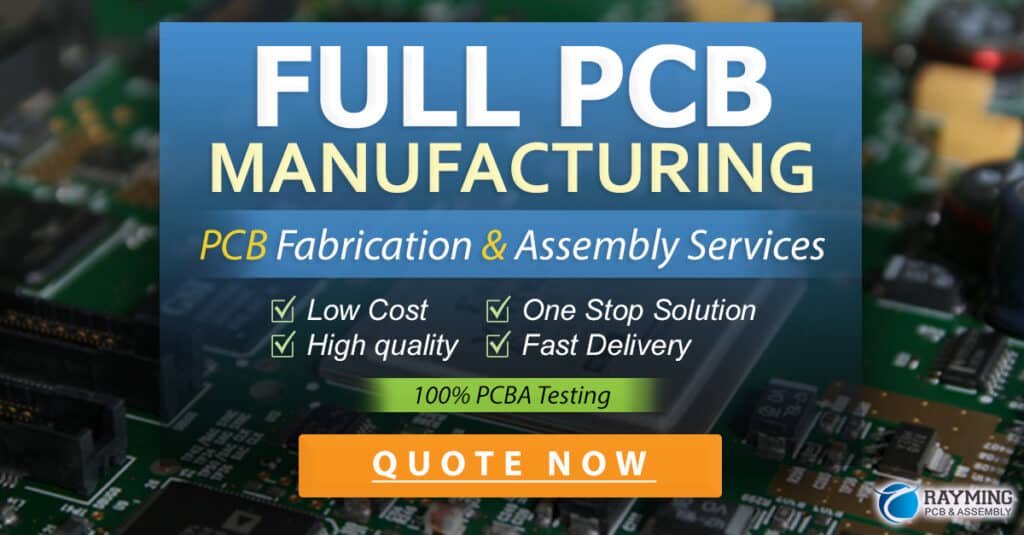
Printer Setup and Process Control
Squeegee Pressure and Speed
Proper squeegee pressure and speed settings are essential for consistent solder paste deposition. Excessive pressure can cause scooping or bleeding of the paste, while insufficient pressure may result in incomplete aperture filling. Squeegee speed affects the shear rate applied to the solder paste, which influences its flow behavior. Optimal pressure and speed settings should be determined through experimentation and analysis of print quality.
Parameter | Recommended Range |
---|---|
Squeegee Pressure | 0.2-0.4 kg/cm |
Squeegee Speed | 20-50 mm/s |
Print Alignment and Gasketing
Accurate alignment between the stencil and PCB is crucial for ensuring precise solder paste deposition. Modern solder paste printers incorporate vision systems and fiducial recognition to automate the alignment process. Proper gasketing between the stencil and PCB is also necessary to prevent paste bleed-out and maintain consistent print quality. Regular cleaning and inspection of the printer, stencil, and tooling can help maintain optimal alignment and gasketing.
Environmental Control
Solder paste is sensitive to environmental conditions such as temperature and humidity. Excessive humidity can cause solder paste slumping and scooping, while low humidity may lead to premature drying of the paste. Temperature variations can affect the paste’s viscosity and flow properties. Maintaining a controlled environment with a temperature range of 20-25°C and a relative humidity of 40-60% is recommended for optimal solder paste performance.
Process Monitoring and Quality Control
Solder Paste Inspection (SPI)
Solder paste inspection (SPI) systems are used to assess the quality of the printed solder paste deposits. These systems use 2D or 3D imaging techniques to measure the volume, height, and area of the solder paste deposits and compare them to predefined acceptance criteria. SPI data can be used to identify printing defects, monitor process stability, and provide feedback for process optimization.
Defect Analysis and Troubleshooting
Despite best efforts in solder paste data preparation and process control, defects may still occur. Common solder paste printing defects include:
- Bridging: Unintended connection between adjacent pads due to excessive solder paste deposition
- Solder balling: Formation of small solder balls around the printed deposits
- Insufficient solder: Inadequate solder paste volume on the pads, leading to weak or open solder joints
Defect analysis involves identifying the root causes of these issues and implementing corrective actions. Troubleshooting may involve adjusting stencil design, printer settings, or solder paste properties to eliminate or minimize the occurrence of defects.
Frequently Asked Questions (FAQ)
- What is the recommended solder paste particle size for fine-pitch components?
-
For fine-pitch components with lead spacings of 0.5 mm or less, a particle size range of 25-45 μm is typically recommended. This ensures good printability and reduces the risk of bridging between adjacent pads.
-
How often should I clean my solder paste printer?
-
Solder paste printers should be cleaned regularly to maintain print quality and prevent contamination. The frequency of cleaning depends on factors such as production volume, paste type, and environmental conditions. As a general guideline, cleaning should be performed at least once per shift or every 4-8 hours of continuous operation.
-
Can I reuse solder paste that has been left out for an extended period?
-
Solder paste has a limited shelf life and should be used within the manufacturer’s recommended time frame. If the paste has been left out for an extended period or has been exposed to excessive temperature or humidity, it may have degraded properties and should not be reused. Always store solder paste in a controlled environment and use fresh paste for best results.
-
What is the optimal stencil thickness for my application?
-
The optimal stencil thickness depends on factors such as component size, pad geometry, and desired solder joint height. As a general rule, a stencil thickness of 100-150 μm is suitable for most standard SMT assemblies. For larger components or those with higher stand-off heights, thicker stencils (up to 200 μm) may be necessary. It is recommended to consult with your stencil supplier or process engineer to determine the best thickness for your specific application.
-
How can I optimize my solder paste printing process?
- Optimizing the solder paste printing process involves a combination of factors, including:
- Selecting the appropriate solder paste type and particle size for your application
- Designing stencils with optimal aperture sizes and shapes
- Setting up the printer with proper squeegee pressure, speed, and alignment
- Maintaining a controlled environment with stable temperature and humidity
- Implementing regular cleaning and maintenance procedures
- Monitoring print quality using SPI systems and conducting defect analysis
- Continuously reviewing and adjusting process parameters based on data and feedback
By following best practices in solder paste data preparation and process control, manufacturers can achieve consistent, high-quality solder paste printing results and minimize defects in their SMT assembly process.
Conclusion
Solder paste data preparation is a critical aspect of the SMT assembly process that directly impacts the quality and reliability of the final product. By understanding the properties of solder paste, designing optimal stencils, setting up printers correctly, and implementing robust process control measures, manufacturers can ensure consistent and defect-free solder paste deposition.
Effective SolderPastePrep involves a systematic approach that considers the interplay between paste properties, stencil design, printer setup, and environmental factors. Regular monitoring, inspection, and defect analysis are essential for identifying and correcting issues promptly and maintaining process stability.
As the electronics industry continues to evolve, with ever-increasing demands for miniaturization and performance, the importance of solder paste data preparation will only grow. By staying up-to-date with best practices, emerging technologies, and industry standards, manufacturers can position themselves to meet these challenges and deliver high-quality, reliable products to their customers.
No responses yet