Introduction to Programmable Power Supplies
A programmable power supply unit (PSU) is a versatile tool that allows users to precisely control voltage and current output. Unlike traditional fixed-output power supplies, programmable PSUs can be adjusted and controlled through digital interfaces, making them ideal for a wide range of applications in electronics testing, development, and automation.
In this article, we will explore the basics of programmable power supply schematic circuits, their key components, and how they work together to provide accurate and adjustable power output.
Benefits of Using a Programmable PSU
- Flexibility: Programmable power supplies allow users to adjust voltage and current settings to suit their specific needs.
- Precision: With high-resolution digital control, programmable PSUs can deliver accurate and stable power output.
- Automation: Many programmable power supplies can be controlled remotely through digital interfaces, enabling automated testing and control systems.
- Protection: Advanced programmable PSUs often include built-in protection features, such as over-voltage, over-current, and short-Circuit Protection.
Key Components of a Programmable Power Supply Schematic
To understand how a programmable power supply works, it’s essential to familiarize yourself with the key components that make up its schematic circuit. These components work together to provide regulated, adjustable, and stable power output.
1. Power Transformer
The power transformer is responsible for stepping down the high-voltage AC input (e.g., 120V or 240V) to a lower AC voltage suitable for the power supply circuit. The transformer also provides electrical isolation between the input and output stages, enhancing safety.
2. Rectifier
The rectifier converts the stepped-down AC voltage from the transformer into a pulsating DC voltage. This is typically achieved using a full-wave bridge rectifier, which consists of four diodes arranged in a bridge configuration.
3. Filter Capacitors
Filter capacitors are used to smooth out the pulsating DC voltage from the rectifier, reducing ripple and providing a more stable DC voltage. The capacitance value is chosen based on the desired ripple level and the load current requirements.
4. Voltage Regulator
The voltage regulator is the heart of the programmable power supply. It takes the filtered DC voltage and regulates it to the desired output level. In a programmable PSU, the voltage regulator is typically a switching regulator, such as a buck converter or a Boost Converter, which can efficiently adjust the output voltage based on digital control signals.
5. Digital Control Interface
The digital control interface allows users to set and monitor the output voltage and current of the programmable PSU. This can be achieved through various means, such as:
- Front panel controls (buttons, knobs, and displays)
- Remote control via a computer or microcontroller (using protocols like USB, RS-232, or GPIB)
- Analog control signals (e.g., 0-5V or 0-10V)
The digital control interface communicates with the voltage regulator to adjust the output settings as needed.
6. Current Sensing and Limiting
To provide current limiting and protection, a programmable PSU includes current sensing and limiting circuitry. This typically involves a low-value shunt resistor in series with the load, which allows the control circuit to monitor the load current. If the current exceeds a set limit, the control circuit can reduce the output voltage or shut down the PSU to protect the connected devices.
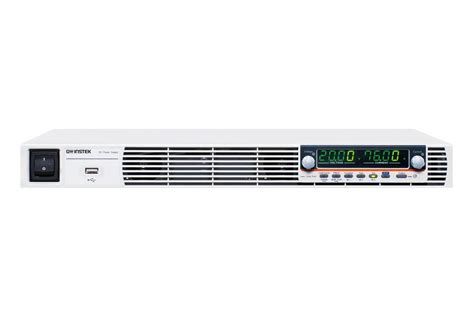
Programmable Power Supply Schematic Circuit Example
Now that we’ve covered the key components, let’s examine a simplified programmable power supply schematic circuit to see how these components work together.
[Insert a schematic diagram of a basic programmable PSU]
In this example, the AC input is stepped down by the power transformer and then rectified by the full-wave bridge rectifier. The rectified voltage is smoothed by the filter capacitors, resulting in a relatively stable DC voltage.
The DC voltage is then fed into a switching voltage regulator, such as a buck converter. The digital control interface, which can be a microcontroller or a dedicated PSU controller IC, communicates with the voltage regulator to set the desired output voltage.
The load current is monitored using a shunt resistor, and the control circuit adjusts the voltage regulator to maintain the set current limit. Additional protection features, such as over-voltage and short-circuit protection, can be implemented using comparators and control logic.
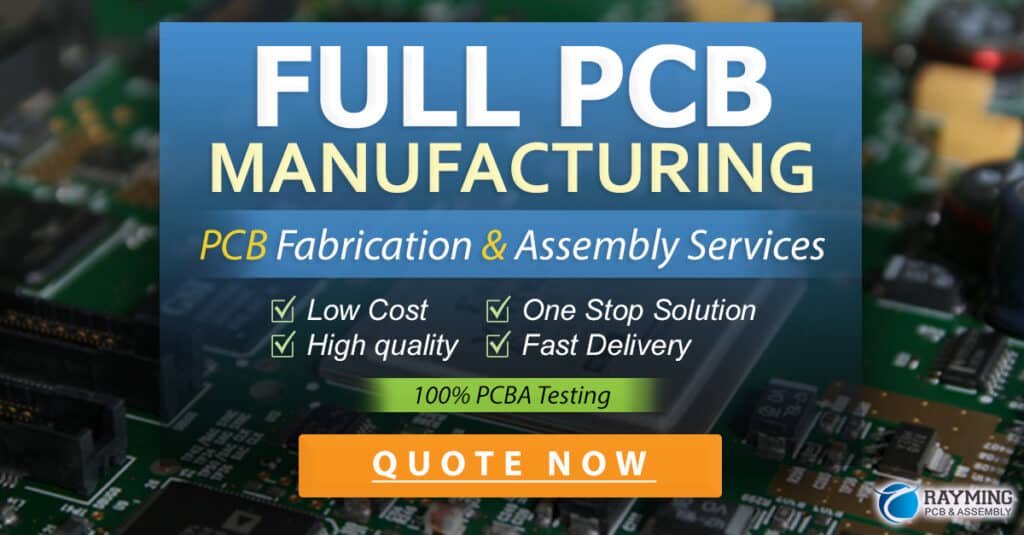
Designing a Programmable Power Supply
When designing a programmable power supply, several key factors must be considered to ensure optimal performance, efficiency, and safety.
1. Input Voltage Range
Determine the input voltage range that the power supply should accept. Common input voltages include 120V AC (North America) and 240V AC (Europe and other regions). The power transformer and rectifier should be selected to handle the expected input voltage range.
2. Output Voltage and Current Range
Specify the desired output voltage and current range for the programmable PSU. This will depend on the intended application and the devices that will be powered by the supply. The voltage regulator and current limiting circuitry should be designed to accommodate the required output range.
3. Regulation and Ripple
Consider the required voltage regulation and ripple specifications. Voltage regulation refers to the power supply’s ability to maintain a constant output voltage under varying load conditions. Ripple is the residual AC voltage superimposed on the DC output. Lower ripple and tighter regulation are desirable for most applications.
4. Efficiency
Efficiency is a critical factor in Power supply design, as it determines the amount of power wasted as heat. Higher efficiency translates to less heat generation, reduced cooling requirements, and lower operating costs. The choice of voltage regulator topology (e.g., buck, boost, or flyback) and the selection of components with low losses can help maximize efficiency.
5. Protection Features
Incorporate appropriate protection features to safeguard the power supply and connected devices from damage. Common protection features include:
- Over-voltage protection (OVP): Shuts down the PSU if the output voltage exceeds a set limit.
- Over-current protection (OCP): Limits the output current to a safe level to prevent damage to the PSU or load.
- Short-circuit protection (SCP): Detects and prevents damage from short circuits on the output.
- Thermal protection: Shuts down the PSU if the internal temperature exceeds a safe limit.
6. Digital Control Interface
Select a suitable digital control interface for the programmable PSU. This can range from simple front panel controls to advanced remote control interfaces like USB, RS-232, or GPIB. The choice of interface will depend on the intended application and the level of automation required.
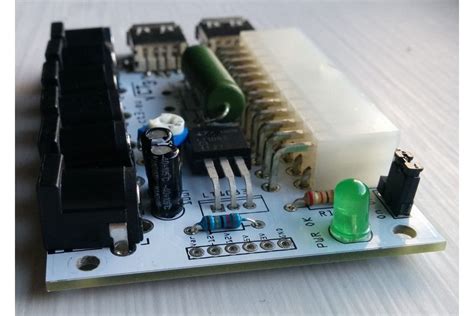
Applications of Programmable Power Supplies
Programmable power supplies find use in a wide range of applications across various industries. Some common applications include:
- Electronics Testing and Development
- Power supply for testing electronic circuits and components
- Simulating various power conditions to evaluate device performance
-
Automated testing using programmable voltage and current profiles
-
Battery Charging and Management
- Controlled charging of various battery types (e.g., Li-ion, NiMH, Lead-acid)
- Battery conditioning and testing
-
Battery management systems (BMS) for electric vehicles and energy storage
-
Industrial Automation
- Powering industrial control systems and sensors
- Process control and monitoring
-
Automated test equipment (ATE) for manufacturing
-
Research and Scientific Instrumentation
- Powering scientific instruments and lab equipment
- Precise control of experimental conditions
-
High-voltage and high-current applications (e.g., electrochemistry, plasma research)
-
Telecommunications and Networking
- Powering communication equipment (e.g., base stations, routers, switches)
- Backup power systems for uninterrupted operation
- Power over Ethernet (PoE) applications
Frequently Asked Questions (FAQ)
-
What is the difference between a programmable power supply and a fixed-output power supply?
A programmable power supply allows users to adjust the output voltage and current through digital control interfaces, while a fixed-output power supply has a predetermined, non-adjustable output. -
Can a programmable power supply be controlled remotely?
Yes, many programmable power supplies can be controlled remotely using digital interfaces like USB, RS-232, or GPIB. This enables automated testing and control systems. -
What is the purpose of current limiting in a programmable power supply?
Current limiting protects the power supply and connected devices from damage by preventing the load current from exceeding a set limit. If the current exceeds the limit, the power supply reduces the output voltage or shuts down to prevent overcurrent conditions. -
How does a programmable power supply maintain a constant output voltage?
A programmable power supply uses a voltage regulator, typically a switching regulator like a buck or boost converter, to maintain a constant output voltage. The regulator continuously adjusts its output to compensate for changes in load current or input voltage, ensuring a stable output voltage. -
What factors should be considered when selecting a programmable power supply?
When selecting a programmable power supply, consider factors such as the required input voltage range, output voltage and current range, regulation and ripple specifications, efficiency, protection features, and the desired digital control interface. The power supply should be chosen based on the specific requirements of the intended application.
Conclusion
Programmable power supplies are essential tools for a wide range of applications, offering precise control, flexibility, and automation capabilities. By understanding the key components and design considerations of programmable power supply schematic circuits, engineers and technicians can effectively select, use, and troubleshoot these versatile devices.
As technology advances, programmable power supplies continue to evolve, offering higher efficiency, better regulation, and more advanced control features. By staying informed about the latest developments in programmable PSU technology, users can take advantage of these improvements to optimize their power supply solutions for their specific applications.
No responses yet