Introduction to Voltage Regulators
A voltage regulator is an electronic circuit that maintains a constant voltage level at its output despite variations in load current or input voltage. Voltage regulators are essential components in many electronic systems, from small battery-powered devices to large industrial power supplies. They ensure that the voltage supplied to the load remains within a specified range, protecting sensitive components from damage due to overvoltage or undervoltage conditions.
In this article, we will explore the design of a 48v to 33v voltage regulator, discussing the various components, design considerations, and implementation details involved in creating an efficient and reliable regulator circuit.
Types of Voltage Regulators
There are two main types of voltage regulators: linear and switching.
Linear Voltage Regulators
Linear voltage regulators work by using a variable resistor to drop the excess voltage from the input to the desired output level. They are simple, inexpensive, and produce low noise, making them suitable for applications that require a clean, stable output voltage. However, linear regulators have several drawbacks, including low efficiency, high heat dissipation, and limited current handling capacity.
Switching Voltage Regulators
Switching voltage regulators, also known as switch-mode power supplies (SMPS), use a high-frequency switching element (usually a MOSFET or BJT) to convert the input voltage to the desired output level. They are more efficient than linear regulators, as they minimize power dissipation by rapidly switching between on and off states. Switching regulators can handle higher current loads and offer greater design flexibility, but they are more complex and generate more noise than linear regulators.
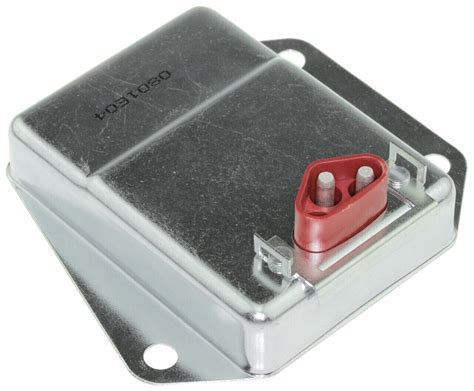
Designing a 48v to 33v Voltage Regulator
For our 48v to 33v voltage regulator project, we will design a switching regulator using a buck converter topology. A buck converter steps down the input voltage to a lower output voltage by controlling the duty cycle of the switching element.
Design Specifications
Before we begin the design process, let’s define the key specifications for our 48v to 33v voltage regulator:
Parameter | Value |
---|---|
Input Voltage Range | 45v – 51v |
Output Voltage | 33v |
Output Current (Max) | 5A |
Output Voltage Ripple | <100mV |
Efficiency (Min) | 90% |
Operating Temperature | -20°C to 85°C |
Component Selection
To design our buck converter, we need to select the appropriate components based on the design specifications. The main components include:
- Switching Controller IC
- Power MOSFET
- Inductor
- Output Capacitor
- Input Capacitor
- Diode
Switching Controller IC
The switching controller IC is the brain of the buck converter, responsible for generating the PWM signal that controls the power MOSFET. For our design, we will use the LM5116 switching controller from Texas Instruments, which is well-suited for high-voltage applications.
Power MOSFET
The power MOSFET acts as the switching element in the buck converter, alternately connecting and disconnecting the inductor to the input voltage. We will select an N-channel MOSFET with a voltage rating higher than our maximum input voltage (51v) and a current rating above our maximum output current (5A). The IRFB7430PbF from Infineon Technologies is a good choice for this application.
Inductor
The inductor in a buck converter stores energy during the on-time of the MOSFET and releases it to the load during the off-time. The inductor value is chosen based on the desired output voltage ripple and switching frequency. For our design, we will use a 47μH inductor with a current rating of at least 5A.
Output Capacitor
The output capacitor filters the output voltage and reduces the voltage ripple. We will select a low-ESR (Equivalent Series Resistance) capacitor with a voltage rating above our output voltage (33v). A 100μF aluminum electrolytic capacitor and a 10μF ceramic capacitor in parallel will provide adequate filtering and stability.
Input Capacitor
The input capacitor reduces the input voltage ripple and provides a stable supply to the buck converter. We will choose a low-ESR capacitor with a voltage rating above our maximum input voltage (51v). A 22μF ceramic capacitor will suffice for this purpose.
Diode
The diode in a buck converter provides a path for the inductor current to flow when the MOSFET is off. We will use a Schottky diode with a voltage rating higher than our maximum input voltage (51v) and a current rating above our maximum output current (5A). The SS34 Schottky diode from Vishay is a suitable choice.
Circuit Design and Calculations
With the components selected, we can now proceed to design the buck converter circuit and perform the necessary calculations.
Duty Cycle Calculation
The duty cycle (D) of the buck converter is the ratio of the output voltage to the input voltage:
D = V_out / V_in
For our 48v to 33v converter, the nominal duty cycle is:
D = 33v / 48v = 0.6875 or 68.75%
Inductor Current Ripple Calculation
The inductor current ripple (ΔI_L) is the amount by which the inductor current varies during each switching cycle. It is determined by the inductor value (L), switching frequency (f_sw), and voltage difference between the input and output:
ΔI_L = (V_in – V_out) × D / (f_sw × L)
Assuming a switching frequency of 200kHz, the inductor current ripple is:
ΔI_L = (48v – 33v) × 0.6875 / (200kHz × 47μH) = 0.22A
Output Voltage Ripple Calculation
The output voltage ripple (ΔV_out) is the amount by which the output voltage varies due to the inductor current ripple. It is determined by the inductor current ripple, output capacitor value (C_out), and switching frequency:
ΔV_out = ΔI_L / (8 × f_sw × C_out)
With a 100μF output capacitor and a 10μF ceramic capacitor in parallel (C_out = 110μF), the output voltage ripple is:
ΔV_out = 0.22A / (8 × 200kHz × 110μF) = 12.5mV
This meets our design specification of less than 100mV output voltage ripple.
PCB Layout Considerations
Proper PCB layout is crucial for the optimal performance and reliability of the buck converter. Some key layout considerations include:
- Minimizing the loop area of the high-frequency current path (input capacitor, MOSFET, and diode) to reduce electromagnetic interference (EMI).
- Placing the input and output capacitors close to the switching controller IC and MOSFET to minimize trace inductance.
- Using wide traces for high-current paths to minimize resistive losses and voltage drops.
- Providing adequate copper area for heat dissipation, especially for the MOSFET and diode.
- Separating the analog and digital ground planes to reduce noise coupling.
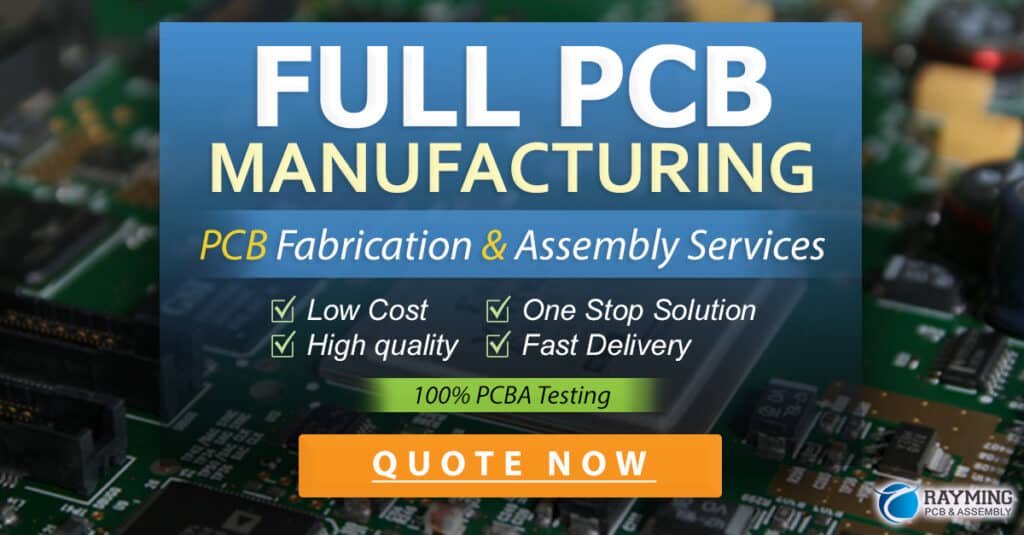
Testing and Verification
After assembling the buck converter circuit, it is essential to test and verify its performance to ensure that it meets the design specifications. Some key tests include:
- Measuring the output voltage and ripple under various load conditions.
- Verifying the efficiency of the converter across the input voltage and load current range.
- Checking the thermal performance of the circuit under maximum load and ambient temperature conditions.
- Conducting EMI testing to ensure compliance with relevant standards.
Any deviations from the expected performance should be investigated and corrected before finalizing the design.
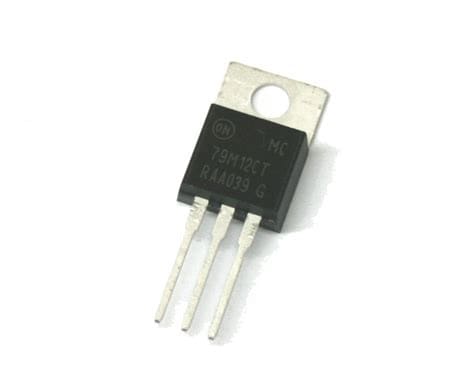
Applications of 48v to 33v Voltage Regulators
48v to 33v voltage regulators find applications in various industries and systems, such as:
- Telecommunications equipment
- Industrial control systems
- Automotive electronics
- Renewable energy systems (e.g., solar and wind power)
- Battery-powered devices
In these applications, the voltage regulator ensures a stable and reliable power supply for the connected loads, enhancing system performance and longevity.
Frequently Asked Questions (FAQ)
1. What is the efficiency of the 48v to 33v buck converter?
The efficiency of the buck converter depends on various factors, such as the input voltage, load current, and component selection. With proper design and component choice, efficiencies of 90% or higher can be achieved. In our example, we specified a minimum efficiency of 90%.
2. Can I use a linear voltage regulator for a 48v to 33v conversion?
While it is possible to use a linear voltage regulator for a 48v to 33v conversion, it is not recommended due to the high power dissipation and low efficiency. The power dissipated by the linear regulator would be (48v – 33v) × I_load, which can be significant at higher load currents. A switching regulator, like the buck converter, is a more efficient choice for this voltage conversion.
3. What is the purpose of the input and output capacitors in the buck converter?
The input capacitor reduces the input voltage ripple and provides a stable supply to the buck converter, while the output capacitor filters the output voltage and reduces the voltage ripple. These capacitors help to ensure a clean and stable power supply for the connected load.
4. How do I select the appropriate inductor value for the buck converter?
The inductor value is chosen based on the desired output voltage ripple, switching frequency, and the voltage difference between the input and output. A higher inductor value will result in lower output voltage ripple but may increase the physical size and cost of the inductor. The inductor current rating should also be higher than the maximum load current to prevent saturation.
5. What are the advantages of using a switching regulator over a linear regulator?
Switching regulators offer several advantages over linear regulators, including:
- Higher efficiency, especially for large voltage drops and high load currents.
- Lower heat dissipation, as power is not continuously dissipated in the regulator.
- Greater design flexibility, as they can be configured for step-up (boost), step-down (buck), or inverting operation.
- Smaller size and lighter weight for a given power level, due to the reduced heat sinking requirements.
However, switching regulators are more complex and generate more noise than linear regulators, requiring careful design and layout to minimize EMI.
Conclusion
Designing a reliable and efficient 48v to 33v voltage regulator requires careful consideration of the system requirements, component selection, and PCB layout. By following the design steps outlined in this article and selecting appropriate components, such as the LM5116 switching controller, IRFB7430PbF MOSFET, and SS34 Schottky diode, you can create a robust buck converter that meets the specified performance criteria.
Remember to conduct thorough testing and verification to ensure that the voltage regulator performs as expected under various operating conditions. By understanding the principles and best practices of voltage regulator design, you can create power solutions that are optimized for your specific application, ensuring the stability, reliability, and longevity of your electronic systems.
No responses yet