Introduction to PCB Prototyping
Printed Circuit Board (PCB) prototyping is a crucial step in the development of electronic devices. It allows designers and engineers to test and validate their designs before mass production. PCB prototyping involves creating a small batch of boards to ensure that the design works as intended and meets all the necessary requirements. In this article, we will discuss the PCB Prototype manufacturing process in detail.
What is PCB Prototyping?
PCB prototyping is the process of creating a small number of printed circuit boards for testing and validation purposes. These prototypes are used to verify the functionality, reliability, and manufacturability of the design. PCB prototypes are typically made using the same materials and processes as the final production boards but in smaller quantities.
Why is PCB Prototyping Important?
PCB prototyping is essential for several reasons:
-
Design Verification: Prototyping allows designers to test their designs and make necessary changes before mass production. This helps to identify and fix any design flaws early in the development process, saving time and money.
-
Functionality Testing: Prototypes are used to test the functionality of the PCB design. This includes testing the board’s electrical properties, signal integrity, and thermal management.
-
Manufacturing Validation: PCB prototyping helps to validate the manufacturing process. It ensures that the design can be manufactured efficiently and cost-effectively.
-
Cost Savings: Prototyping helps to identify and fix design flaws early in the development process, which can save significant costs in the long run.
PCB Prototyping Methods
There are several methods for creating PCB prototypes, each with its own advantages and disadvantages. The choice of method depends on factors such as the complexity of the design, the required turnaround time, and the budget.
1. PCB Milling
PCB milling is a subtractive process that involves using a milling machine to remove copper from a blank PCB substrate. The milling machine uses a rotating cutting tool to etch the desired circuit pattern onto the board. PCB milling is suitable for simple designs with low quantity requirements.
Advantages of PCB Milling
- Fast turnaround time
- Low cost for small quantities
- Suitable for simple designs
Disadvantages of PCB Milling
- Limited to simple designs
- Not suitable for high-density designs
- Limited material options
2. PCB Etching
PCB etching is a chemical process that involves removing unwanted copper from a PCB substrate. The process starts with a copper-clad board that is coated with a photoresist layer. The desired circuit pattern is then transferred onto the photoresist layer using a photomask and UV light exposure. The exposed areas of the photoresist are then removed, leaving the copper exposed. The board is then immersed in an etchant solution, which removes the exposed copper, leaving only the desired circuit pattern.
Advantages of PCB Etching
- Suitable for complex designs
- Can produce high-density boards
- Relatively low cost
Disadvantages of PCB Etching
- Longer turnaround time compared to milling
- Requires chemical handling and disposal
- Limited material options
3. PCB Printing
PCB printing is an additive process that involves depositing conductive ink onto a substrate to create the desired circuit pattern. There are several types of PCB printing, including inkjet printing, aerosol jet printing, and screen printing.
Advantages of PCB Printing
- Suitable for flexible and stretchable substrates
- Can produce high-resolution features
- Environmentally friendly
Disadvantages of PCB Printing
- Limited material options
- Requires specialized equipment
- Higher cost compared to other methods
Comparison of PCB Prototyping Methods
Method | Advantages | Disadvantages |
---|---|---|
PCB Milling | Fast turnaround time, low cost for small quantities, suitable for simple designs | Limited to simple designs, not suitable for high-density designs, limited material options |
PCB Etching | Suitable for complex designs, can produce high-density boards, relatively low cost | Longer turnaround time compared to milling, requires chemical handling and disposal, limited material options |
PCB Printing | Suitable for flexible and stretchable substrates, can produce high-resolution features, environmentally friendly | Limited material options, requires specialized equipment, higher cost compared to other methods |
PCB Prototyping Process
The PCB prototyping process involves several steps, from design creation to final assembly. Let’s take a closer look at each step.
1. Design Creation
The first step in the PCB prototyping process is to create the PCB design using specialized software such as Altium, Eagle, or KiCad. The design includes the schematic, layout, and bill of materials (BOM).
2. Design Review
Once the design is complete, it undergoes a thorough review to ensure that it meets all the necessary requirements. This includes checking for design rule violations, manufacturability, and functionality.
3. Prototype Fabrication
After the design review, the prototype is fabricated using one of the methods discussed earlier (milling, etching, or printing). The fabrication process involves several sub-steps, such as drilling, plating, and solder mask application.
4. Component Sourcing
While the prototype is being fabricated, the components specified in the BOM are sourced from suppliers. This includes both off-the-shelf components and custom components.
5. Assembly
Once the prototype and components are ready, the board is assembled. This involves soldering the components onto the board using either through-hole or surface-mount technology.
6. Testing and Validation
The assembled prototype is then tested and validated to ensure that it meets all the necessary requirements. This includes functional testing, signal integrity testing, and environmental testing.
7. Design Iteration
Based on the testing and validation results, the design may need to be modified. This involves going back to the design creation step and making the necessary changes.
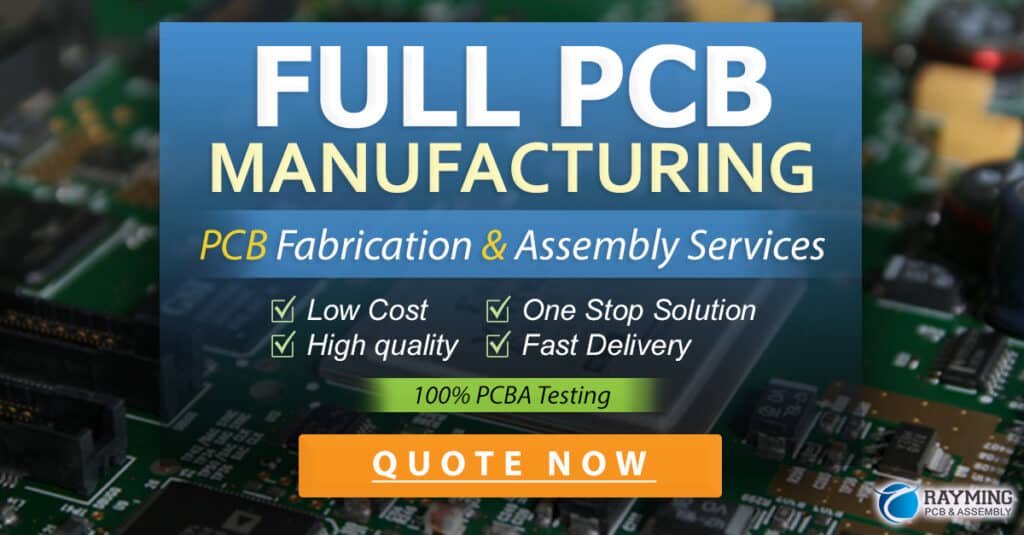
PCB Prototype Manufacturing Considerations
When manufacturing PCB prototypes, there are several considerations to keep in mind to ensure a successful outcome.
1. Material Selection
The choice of PCB material depends on factors such as the operating environment, frequency, and power requirements. Common PCB materials include FR-4, Rogers, and polyimide.
2. Layer Stack-up
The layer stack-up refers to the arrangement of copper layers and dielectric materials in the PCB. The layer stack-up affects the board’s electrical properties, signal integrity, and manufacturability.
3. Trace Width and Spacing
The trace width and spacing determine the board’s current carrying capacity and signal integrity. Smaller trace widths and spacing allow for higher density designs but may be more challenging to manufacture.
4. Via Size and Placement
Vias are used to connect traces between layers in the PCB. The size and placement of vias affect the board’s electrical properties and manufacturability.
5. Solder Mask and Silkscreen
The solder mask and silkscreen layers protect the board and provide labeling for components. The choice of solder mask and silkscreen colors can affect the board’s aesthetics and readability.
PCB Prototyping Best Practices
To ensure a successful PCB prototyping process, it’s essential to follow best practices.
1. Use a Checklist
Create a checklist of all the necessary steps and requirements for the PCB prototyping process. This helps to ensure that nothing is overlooked and that the process runs smoothly.
2. Communicate with Manufacturers
Communicate clearly with PCB manufacturers about your requirements and expectations. Provide detailed documentation, including the schematic, layout, and BOM.
3. Plan for Testing
Plan for testing and validation early in the development process. This includes identifying the necessary testing equipment and procedures.
4. Use Version Control
Use version control software to track changes to the PCB design. This helps to ensure that everyone is working with the latest version of the design.
5. Document Everything
Document everything related to the PCB prototyping process, including design decisions, testing results, and manufacturer communications. This helps to ensure that knowledge is retained and can be referenced in the future.
Frequently Asked Questions (FAQ)
1. How long does PCB prototyping take?
The turnaround time for PCB prototyping depends on the complexity of the design and the chosen manufacturing method. PCB milling can have a turnaround time as short as 24 hours, while etching and printing can take several days.
2. How much does PCB prototyping cost?
The cost of PCB prototyping depends on factors such as the design complexity, quantity, and chosen manufacturing method. PCB milling is typically the lowest cost option for small quantities, while etching and printing can be more cost-effective for larger quantities.
3. What is the minimum quantity for PCB prototyping?
The minimum quantity for PCB prototyping depends on the manufacturer and the chosen manufacturing method. Some manufacturers offer low minimum quantities, such as 5 or 10 boards, while others may require a minimum of 100 boards.
4. Can I use any components for PCB prototyping?
The choice of components for PCB prototyping depends on the design requirements and the chosen manufacturing method. Some manufacturing methods may have limitations on the types of components that can be used.
5. What is the difference between PCB prototyping and production?
PCB prototyping involves creating a small number of boards for testing and validation purposes, while production involves mass-producing boards for commercial use. PCB prototyping typically uses the same materials and processes as production but in smaller quantities.
Conclusion
PCB prototyping is a critical step in the development of electronic devices. It allows designers and engineers to test and validate their designs before mass production, saving time and money in the long run. There are several methods for creating PCB prototypes, each with its own advantages and disadvantages. The choice of method depends on factors such as the complexity of the design, the required turnaround time, and the budget. By following best practices and carefully considering manufacturing considerations, designers can ensure a successful PCB prototyping process.
No responses yet