Choose the Right PCB Material
Selecting the appropriate PCB material is crucial for the performance and durability of your custom PCB. The most common PCB materials include:
Material | Description | Applications |
---|---|---|
FR-4 | Flame-retardant, glass-reinforced epoxy laminate | General-purpose, high-volume production |
Polyimide | High-temperature resistance, flexible | Aerospace, military, medical devices |
Aluminum | Excellent thermal conductivity | High-power LEDs, power electronics |
Rogers | Low dielectric loss, stable at high frequencies | RF and microwave applications |
Consider your application’s specific requirements, such as temperature range, dielectric constant, and mechanical properties, when choosing the PCB material.
Determine the Appropriate Layer Stack-up
The number of layers in your custom PCB directly affects its functionality, size, and cost. When deciding on the layer stack-up, consider the following:
- Signal integrity: More layers allow for better signal routing and reduced crosstalk.
- Power distribution: Dedicated power and ground planes provide stable power distribution and reduce noise.
- Electromagnetic compatibility (EMC): Proper layer arrangement and grounding techniques minimize electromagnetic interference (EMI).
A typical 4-layer PCB Stack-up might look like this:
Layer | Purpose |
---|---|
Top | Signal routing, components |
Inner 1 | Ground plane |
Inner 2 | Power plane |
Bottom | Signal routing, components |
Work closely with your PCB manufacturer to determine the optimal layer stack-up for your custom PCB.
Optimize Component Placement and Routing
Proper component placement and routing are essential for PCB performance, manufacturability, and assembly. Follow these guidelines:
- Group related components together to minimize signal path lengths and improve signal integrity.
- Provide adequate spacing between components for manufacturability and assembly.
- Route critical signals first, such as high-speed signals, clock lines, and sensitive analog signals.
- Use appropriate via sizes and spacing to ensure reliable connections between layers.
- Adhere to your manufacturer’s design rules and guidelines for minimum trace widths, spacing, and hole sizes.
Utilize PCB design software with automatic design rule checking (DRC) to validate your layout against the manufacturer’s specifications.
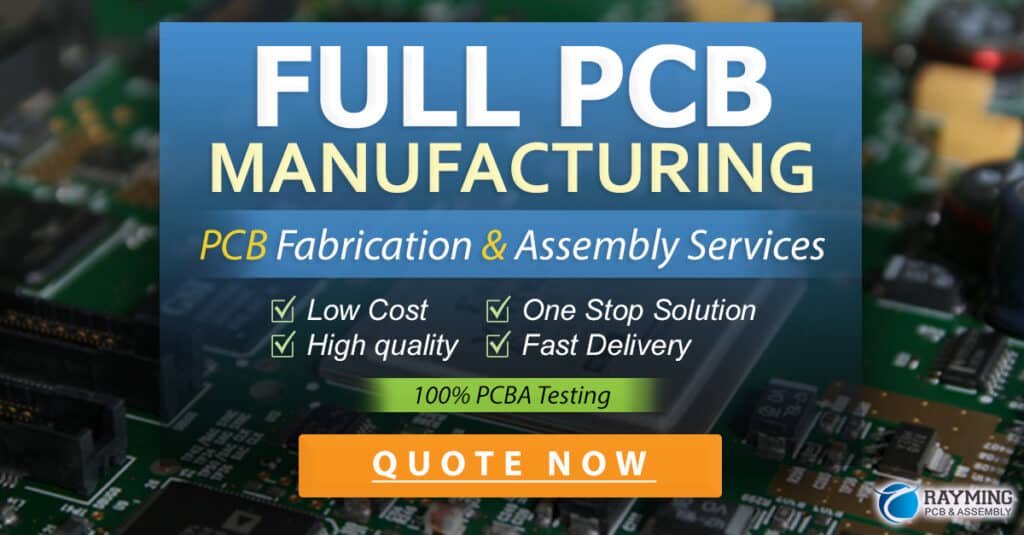
Select the Appropriate Surface Finish
The surface finish on your custom PCB serves several purposes, including protecting exposed copper, enhancing solderability, and providing a reliable contact surface. Common surface finishes include:
- Hot Air Solder Leveling (HASL): Economical, widely used, and suitable for most applications.
- Electroless Nickel Immersion Gold (ENIG): Flat surface, excellent solderability, and long shelf life.
- Immersion Silver (IAg): Cost-effective, good solderability, and suitable for high-frequency applications.
- Immersion Tin (ISn): Affordable, good solderability, and RoHS compliant.
Choose the surface finish based on your application’s requirements, budget, and the assembly process.
Consider Controlled Impedance
For high-speed digital and RF applications, controlling the impedance of transmission lines is critical for maintaining signal integrity. Factors that affect impedance include:
- Trace width and thickness
- Dielectric constant of the PCB material
- Proximity to reference planes (ground or power)
To achieve controlled impedance, work with your PCB manufacturer to:
- Specify the target impedance value and tolerance.
- Provide the necessary information, such as layer stack-up and material properties.
- Request a time-domain reflectometry (TDR) test to verify the actual impedance values.
Controlled impedance adds complexity and cost to the PCB manufacturing process, so it should only be used when necessary.
Collaborate with Your PCB Manufacturer
Engaging with your PCB manufacturer early in the design process can help you make informed decisions and avoid potential issues. A reputable manufacturer can provide valuable insights on:
- Design for manufacturability (DFM) recommendations
- Material selection and availability
- Cost-saving opportunities
- Lead times and production scheduling
Foster a strong working relationship with your PCB manufacturer to ensure the success of your custom PCB project.
Frequently Asked Questions (FAQ)
- What is the minimum feature size for custom PCBs?
-
The minimum feature size depends on the PCB manufacturer’s capabilities. Typically, the minimum trace width and spacing range from 3 to 6 mils (0.075 to 0.15 mm) for standard PCBs, while advanced processes can achieve 1 to 2 mils (0.025 to 0.05 mm).
-
How long does it take to manufacture custom PCBs?
-
Lead times vary based on the complexity of the design, the manufacturer’s workload, and the selected service level. Standard lead times range from 1 to 3 weeks, while expedited services can reduce the lead time to a few days.
-
What is the cost of custom PCB Printing?
-
The cost of custom PCB printing depends on several factors, including the board size, layer count, material, surface finish, quantity, and turnaround time. Work with your PCB manufacturer to obtain a detailed quote based on your specific requirements.
-
Can I combine different surface finishes on the same PCB?
-
Yes, it is possible to have different surface finishes on the same PCB, such as ENIG on connectors and HASL on the rest of the board. However, this may increase the complexity and cost of the manufacturing process.
-
How can I ensure my custom PCB design is ready for manufacturing?
- To ensure your PCB design is ready for manufacturing, follow the manufacturer’s design guidelines, use DRC tools to validate your layout, and request a design review from the manufacturer before finalizing your design files.
In conclusion, paying special attention to these six aspects of custom PCB printing – material selection, layer stack-up, component placement and routing, surface finish, controlled impedance, and manufacturer collaboration – will help you create high-quality, reliable, and cost-effective PCBs for your projects. By carefully considering each factor and working closely with your PCB manufacturer, you can optimize your custom PCB design and ensure a smooth manufacturing process.
No responses yet