Introduction to PCB Soldering
Printed circuit board (PCB) assembly often requires manual soldering to attach components to the board. Soldering is the process of joining two or more metal items by melting and putting a filler metal (solder) into the joint, the filler metal having a lower melting point than the adjoining metal. Soldering is distinguished from welding by the base metals not melting during the joining process.
Manual soldering of PCBs requires skill, proper technique, and the right tools and materials to ensure reliable connections. This comprehensive guide will cover everything you need to know to successfully hand solder components onto a PCB.
Tools and Materials Needed for PCB Soldering
Before starting any PCB soldering work, it’s important to gather the necessary tools and materials. Here’s what you’ll need:
Soldering Iron
A soldering iron is the most essential tool for manual PCB soldering. Choose a soldering iron with adjustable temperature control and a power rating between 20-60 watts. Popular soldering iron types include:
- Pencil-style Soldering Irons
- Soldering stations with interchangeable tips
- Battery-powered cordless soldering irons
Soldering Iron Tips
Soldering iron tips come in various shapes and sizes for different soldering applications. Common tip shapes include chisel, conical, and bevel. Select a tip size appropriate for the component leads and PCB pads you’ll be soldering.
Solder
Solder is a fusible metal alloy used to create a permanent bond between the component leads and PCB pads. Leaded solder (63/37 tin-lead) is the most common type but lead-free solder alloys are required for ROHS compliance. Choose a solder diameter between 0.5-1.0mm for most PCB hand soldering.
Flux
Flux is a chemical cleaning agent that removes oxides from metal surfaces and prevents oxidation during soldering. Flux promotes solder wetting and helps create strong solder joints. Types of flux include:
- Rosin (R, RMA, RA)
- Water-soluble (OA)
- No-clean
Soldering Accessories
Other useful accessories for PCB soldering include:
- Brass sponge or wet sponge for cleaning tips
- Solder wick for removing excess solder
- Flux pen or bottle for applying flux
- Tweezers for handling small components
- Magnifying glass or microscope for inspecting joints
PCB Soldering Techniques
Tinning the Iron Tip
Before soldering, always tin the iron tip by applying a small amount of solder to the tip and wiping it on a damp sponge or brass wool. This protects the tip from oxidation and helps solder wet to it. Tin the tip whenever it starts to look dull or crusty.
Applying Flux
Apply flux to the component leads and PCB pads prior to soldering. Flux can be applied with a flux pen, bottle, or by dipping the leads in a tub of flux. Be sure to apply enough flux to cover the entire soldering area.
Soldering Components
Place the component onto the PCB, ensuring the leads go through the corresponding holes. Touch the soldering iron tip to both the component lead and PCB pad simultaneously. Apply solder to the opposite side of the lead, allowing the heat from the iron to melt the solder and flow it around the joint. Use just enough solder to create a concave fillet between the lead and pad. Avoid applying too much solder which can cause bridging between adjacent joints.
Inspection and Cleanup
Visually inspect each solder joint with a magnifying glass to ensure a proper fillet has formed and no solder bridges or cold joints are present. Clean the PCB as needed with isopropyl alcohol to remove flux residue.
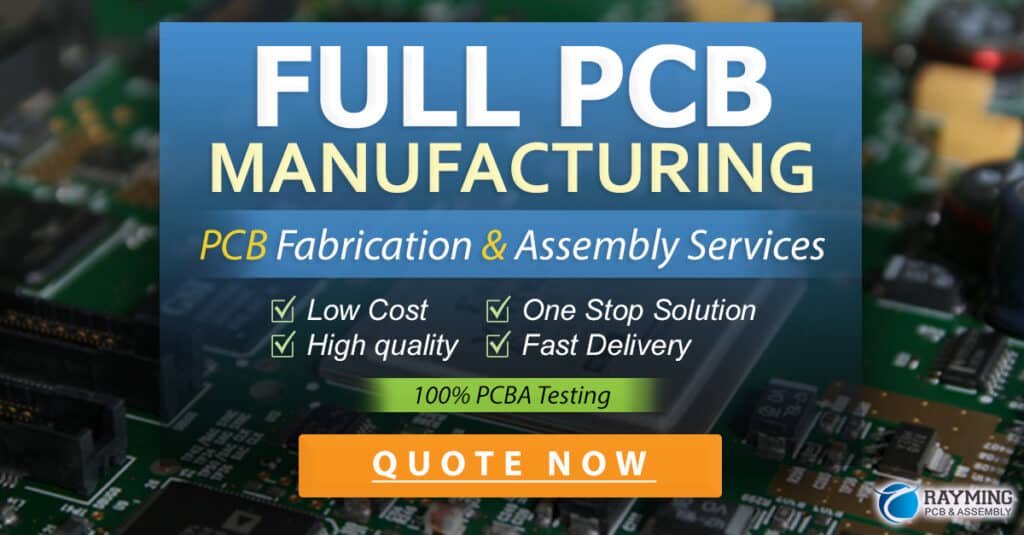
Soldering Different Component Types
Through-Hole (THT) Components
Through-hole components have long leads that are inserted through holes drilled in the PCB. Follow these steps when soldering THT parts:
- Bend the leads at a 90-degree angle to hold the part in place.
- Apply flux to leads and pads.
- Heat both lead and pad with iron and apply solder until a concave fillet forms.
- Trim excess lead length with flush cutters.
Surface Mount (SMT) Components
Surface mount components are soldered to pads on the surface of the PCB. Techniques for soldering common SMT packages include:
Chip Components (Resistors, Capacitors, Diodes)
- Apply solder paste or flux to one pad.
- Position the component on the pads using tweezers.
- Touch the iron to the lead and pad and apply solder to the other side to reflow paste and form a fillet.
- Repeat for the other lead.
SOT/SOP ICs
- Apply solder paste or flux to one row of pads.
- Align IC pins with pads and place down, holding in place with tweezers.
- Touch iron to pin and pad and apply solder to form fillet on first pin.
- Solder remaining pins.
- Repeat steps for other side of IC.
QFP/TQFP ICs
- Apply solder paste or flux to corner pads.
- Align IC and place down, holding with tweezers.
- Tack solder two corner pins to hold IC in place.
- Solder remaining pins, using a fine tipped iron to avoid bridging.
- Remove any solder bridges with solder wick.
Soldering Tips and Tricks
- Always use a clean, tinned iron tip for best results.
- Match the tip size and shape to the component being soldered.
- Use quality solder designed for electronics with a rosin core.
- Apply an appropriate amount of solder. Too little solder can result in a poor connection while too much can cause bridging. A proper solder joint should have a concave fillet between the lead and pad.
- Keep the iron tip in contact with the joint just long enough for the solder to melt and wet to the surfaces. Avoid excessive heat which can damage components and lift pads.
- Clean the PCB with isopropyl alcohol when finished to remove flux residue which can be corrosive over time.
- Practice proper safety including using a fume extractor in well ventilated area and avoiding contact with hot surfaces.
Visual Guide to Good vs Bad Solder Joints
Use this visual reference to help identify the characteristics of an acceptable solder joint versus common soldering defects:
Good Solder Joint | Cold or Dull Joint | Excessive Solder | Insufficient Solder |
---|---|---|---|
Concave fillet | Convex shape | Large rounded fillet | Flat or no fillet |
Shiny appearance | Grainy, dull surface | Obscures component lead | Lead still visible |
Wetting to all surfaces | Gaps or voids present | Solder spikes or peaks | Gaps between solder and lead or pad |
PCB Soldering FAQs
Q1: What type of solder should I use for PCB soldering?
A1: A solder wire with a diameter between 0.5-1.0mm and a rosin flux core is recommended for most PCB soldering. Leaded 63/37 tin-lead solder is commonly used but lead-free solder may be required for ROHS compliance.
Q2: What wattage soldering iron is best for PCB work?
A2: A soldering iron between 20-60 watts is suitable for most PCB soldering. Higher wattage irons heat up faster but may be more difficult to control. Temperature adjustable irons offer more flexibility to work with different components and base materials.
Q3: How do I clean my soldering iron tip?
A3: Always keep the soldering iron tip clean by wiping it frequently on a damp sponge or brass wool during use. Tips can be cleaned with tip tinner or by heating and applying solder then wiping away the excess.
Q4: What can cause a Cold Solder Joint?
A4: Cold solder joints can be caused by insufficient heat, poor wetting of the solder, or contamination on the surfaces being soldered. Make sure to apply adequate heat and flux and keep the tip and pads clean to avoid cold joints.
Q5: How can I prevent solder bridges when soldering IC pins?
A5: To avoid solder bridging, use a fine tipped iron and apply solder sparingly. Drag the iron tip perpendicular to the pin row to remove excess solder. Solder bridges can be removed by wicking away the excess with solder wick braid.
Conclusion
Manual PCB soldering is a skill that takes practice to master but is an essential process for assembling and repairing circuit boards. By using the proper tools and techniques and following the tips in this guide, you’ll be able to confidently solder a variety of through-hole and surface mount components. Remember to always work safely, inspect your solder joints carefully, and don’t be afraid to desolder and rework any imperfect connections. With patience and experience, your hand soldering skills will improve to help you build and fix PCBs like a pro!
No responses yet