Introduction to Cold Solder Joints
A cold solder joint, also known as a dry solder joint or cracked solder joint, is a common problem in electronic assemblies caused by improper or incomplete soldering. Cold solder joints occur when the solder does not melt and flow properly, resulting in a weak, brittle, and unreliable connection between components and the printed circuit board (PCB). These faulty connections can lead to intermittent electrical failures, reduced performance, and even complete device malfunction.
The Importance of Addressing Cold Solder Joints
Identifying and addressing cold solder joints is crucial for ensuring the reliability and longevity of electronic devices. In this comprehensive article, we will explore the causes, characteristics, and prevention methods for cold solder joints, as well as techniques for identifying and repairing them.
Causes of Cold Solder Joints
Several factors can contribute to the formation of cold solder joints during the soldering process:
Insufficient Heat
One of the primary causes of cold solder joints is insufficient heat applied to the solder joint. When the soldering iron temperature is too low or the heat is not applied long enough, the solder may not melt completely or flow properly around the components and PCB pads. This incomplete melting and flowing of solder results in a weak, porous, and brittle connection.
Contamination
Contamination of the soldering surface or components can also lead to cold solder joints. Dirt, grease, oxidation, or other foreign materials on the PCB pads, component leads, or solder itself can prevent proper solder adhesion and flow. These contaminants act as barriers, hindering the formation of a strong metallic bond between the solder and the surfaces being joined.
Improper Soldering Technique
Poor soldering technique is another common cause of cold solder joints. Applying the soldering iron incorrectly, using too much or too little solder, or moving the components during the solidification process can all contribute to the formation of weak and unreliable solder connections.
Incorrect Solder Composition
Using solder with an incorrect composition or ratio of metals can also result in cold solder joints. Different solder alloys have specific melting temperatures and flow characteristics. If the wrong type of solder is used for a particular application, it may not melt and flow properly, leading to subpar solder joints.
Characteristics of Cold Solder Joints
Cold solder joints exhibit distinct visual and physical characteristics that can help identify them during inspection:
Visual Appearance
- Dull, grainy, or porous surface: Cold solder joints often have a matte, granular appearance instead of the smooth, shiny surface of a properly formed solder joint.
- Concave or cracked surface: The solder may appear sunken or concave, with visible cracks or fissures on the surface.
- Incomplete wetting: The solder may not fully cover or adhere to the PCB pads or component leads, leaving exposed metal surfaces.
Physical Characteristics
- Weak mechanical strength: Cold solder joints are brittle and prone to cracking or breaking under mechanical stress or vibration.
- High electrical resistance: Due to the poor metallic bond and presence of contaminants, cold solder joints exhibit higher electrical resistance compared to properly formed joints.
- Intermittent connectivity: Cold solder joints may cause intermittent electrical connections, leading to erratic device behavior or complete failure.
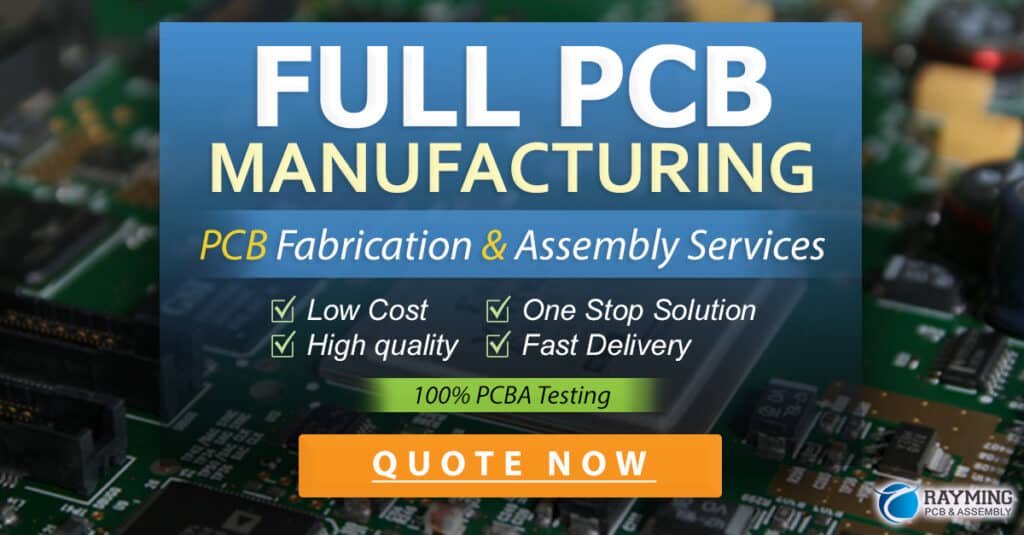
Preventing Cold Solder Joints
To minimize the occurrence of cold solder joints, follow these best practices during the soldering process:
Ensure Proper Soldering Temperature
Use a soldering iron with adjustable temperature control and set it to the appropriate temperature for the solder alloy being used. Consult the solder manufacturer’s specifications for recommended temperature ranges.
Solder Alloy | Melting Temperature Range |
---|---|
Tin-Lead (63/37) | 183°C – 190°C |
Lead-Free (Sn96.5/Ag3.0/Cu0.5) | 217°C – 220°C |
Lead-Free (Sn99.3/Cu0.7) | 227°C – 230°C |
Clean and Prepare Surfaces
Before soldering, thoroughly clean the PCB pads, component leads, and soldering iron tip to remove any dirt, grease, or oxidation. Use isopropyl alcohol or a commercial PCB cleaner to ensure a clean and contamination-free surface.
Use Appropriate Solder and Flux
Choose a solder alloy and flux that are suitable for the specific application and components being soldered. Use solder with the correct diameter and composition, and apply an appropriate amount of flux to promote solder flow and prevent oxidation.
Employ Proper Soldering Technique
Follow proper soldering techniques to ensure the formation of reliable solder joints:
- Preheat the PCB pads and component leads with the soldering iron before applying solder.
- Apply the solder to the joint while maintaining contact between the soldering iron, component lead, and PCB pad.
- Allow the solder to melt and flow around the joint, creating a concave fillet.
- Remove the soldering iron and allow the joint to cool and solidify without disturbing the components.
Implement Quality Control Measures
Establish quality control procedures to inspect and test the soldered assemblies for the presence of cold solder joints. Visual inspection using magnification tools and electrical continuity testing can help identify problematic joints early in the manufacturing process.
Identifying Cold Solder Joints
Identifying cold solder joints is essential for troubleshooting and repairing electronic assemblies. Here are some methods for detecting cold solder joints:
Visual Inspection
Perform a visual examination of the solder joints using magnification tools such as a microscope or magnifying glass. Look for the characteristic visual signs of cold solder joints, such as a dull, grainy, or cracked surface, incomplete wetting, or excessive solder.
Mechanical Testing
Apply gentle pressure or wiggle the components to check for mechanical weakness or looseness in the solder joints. Cold solder joints may break or come loose under minimal stress.
Electrical Testing
Use a multimeter or continuity tester to measure the electrical resistance across the solder joints. Cold solder joints typically exhibit higher resistance compared to properly formed joints. Perform continuity tests to identify any intermittent or open connections.
X-Ray Inspection
For complex or multi-layered PCBs, X-ray inspection can provide a non-destructive way to examine the internal structure of solder joints. X-ray images can reveal voids, cracks, or incomplete solder flow that may not be visible from the surface.
Repairing Cold Solder Joints
If cold solder joints are identified, they must be repaired to restore the reliability and functionality of the electronic assembly. Follow these steps to repair cold solder joints:
- Desolder the affected joint using a desoldering tool, such as a desoldering pump or solder wick, to remove the faulty solder.
- Clean the PCB pads and component leads thoroughly to remove any residual solder or contamination.
- Apply fresh solder to the joint, ensuring proper heat application and solder flow.
- Inspect the repaired joint visually and test it electrically to confirm the integrity of the connection.
Frequently Asked Questions (FAQ)
-
What is the main cause of cold solder joints?
The main cause of cold solder joints is insufficient heat applied to the solder joint during the soldering process. This can be due to a low soldering iron temperature, inadequate heat transfer, or improper soldering technique. -
How can I identify a cold solder joint visually?
Cold solder joints often have a dull, grainy, or porous surface appearance, unlike the smooth and shiny surface of a properly formed solder joint. They may also exhibit cracks, incomplete wetting, or excessive solder buildup. -
Can cold solder joints cause intermittent device failures?
Yes, cold solder joints can cause intermittent electrical connections, leading to erratic device behavior or complete failure. The weak and brittle nature of cold solder joints makes them susceptible to breaking or losing contact under mechanical stress or vibration. -
What are some preventive measures to avoid cold solder joints?
To prevent cold solder joints, ensure proper soldering temperature, clean and prepare the surfaces thoroughly, use appropriate solder and flux, employ proper soldering techniques, and implement quality control measures to inspect and test the soldered assemblies. -
Can cold solder joints be repaired, or do they require complete replacement?
Cold solder joints can often be repaired by desoldering the affected joint, cleaning the surfaces, and applying fresh solder using proper techniques. However, in some cases, if the PCB pads or component leads are severely damaged, complete replacement of the component may be necessary.
Conclusion
Cold solder joints are a common problem in electronic assemblies that can lead to unreliable connections, intermittent failures, and device malfunction. Understanding the causes, characteristics, and prevention methods for cold solder joints is crucial for ensuring the quality and reliability of soldered assemblies.
By following best practices such as ensuring proper soldering temperature, cleaning and preparing surfaces, using appropriate solder and flux, employing proper soldering techniques, and implementing quality control measures, the occurrence of cold solder joints can be minimized.
Regularly inspecting and testing electronic assemblies for the presence of cold solder joints using visual examination, mechanical testing, electrical testing, and X-ray inspection can help identify and address these issues promptly.
When cold solder joints are detected, they can often be repaired by desoldering the affected joint, cleaning the surfaces, and applying fresh solder using correct techniques. In some cases, complete replacement of the component may be necessary if the PCB pads or component leads are severely damaged.
By understanding and addressing the challenges posed by cold solder joints, manufacturers and technicians can improve the reliability, performance, and longevity of electronic devices, ultimately leading to enhanced customer satisfaction and reduced warranty claims.
No responses yet