Introduction to PCB Development and Emerging Trends
Printed Circuit Board (PCB) development is a critical part of modern electronics manufacturing. PCBs provide the physical substrate and electrical interconnections for components that make up electronic devices we use every day, from smartphones and laptops to medical devices and automotive systems.
The PCB industry is constantly evolving to keep pace with advances in electronics. Smaller, faster, cheaper, and more power-efficient devices are always in demand, driving innovation in PCB design and manufacturing. In this article, we’ll explore some of the key trends shaping the future of PCB development that you may not be aware of.
Trend 1: HDI and Advanced Packaging Technologies
One of the biggest trends in PCB development is the adoption of high-density interconnect (HDI) PCBs and advanced packaging technologies. HDI PCBs feature finer lines and spaces, smaller vias, and higher connection pad density compared to traditional PCBs. This allows for smaller form factors and higher component density.
Some examples of HDI and advanced packaging PCB technologies include:
Technology | Description |
---|---|
Any-layer HDI | HDI with micro vias spanning any layer, not just adjacent layers |
Modified Semi-Additive Process (mSAP) | Involves depositing an ultra-thin layer of copper and using photolithography and laser etching to create finer features |
Embedded Component/Active PCBs | Components like ICs, resistors, and capacitors are embedded inside the PCB instead of mounted on the surface |
The benefits of these technologies include:
- Miniaturization and higher component density
- Improved signal integrity and lower noise
- Faster signal speeds
- Lower power consumption
- Cost reduction at volume production
Trend 2: 5G and mmWave-Capable PCBs
The rollout of 5G wireless networks is driving demand for PCBs that can operate at higher frequencies in the millimeter wave (mmWave) range, typically 28 GHz and higher. 5G promises dramatically faster speeds, lower latency, and the ability to connect more devices than previous generation networks.
However, operating at mmWave frequencies presents challenges for PCB design and manufacturing, such as:
- Signal loss and attenuation
- Sensitivity to PCB materials and surface finishes
- More complex multi-layer stack-ups
- Tighter tolerances and smaller feature sizes
To address these challenges, 5G PCBs are employing advanced materials like low-loss/high-frequency laminates, ultra-smooth copper, and innovative HDI structures like filled via-in-pad. Capabilities like 50 micron trace and space are becoming more common.
Examples of 5G applications driving PCB demand include:
- 5G smartphones and mobile devices
- Fixed wireless access points
- Cellular infrastructure equipment
- Automotive and V2X communication
- 5G IoT devices
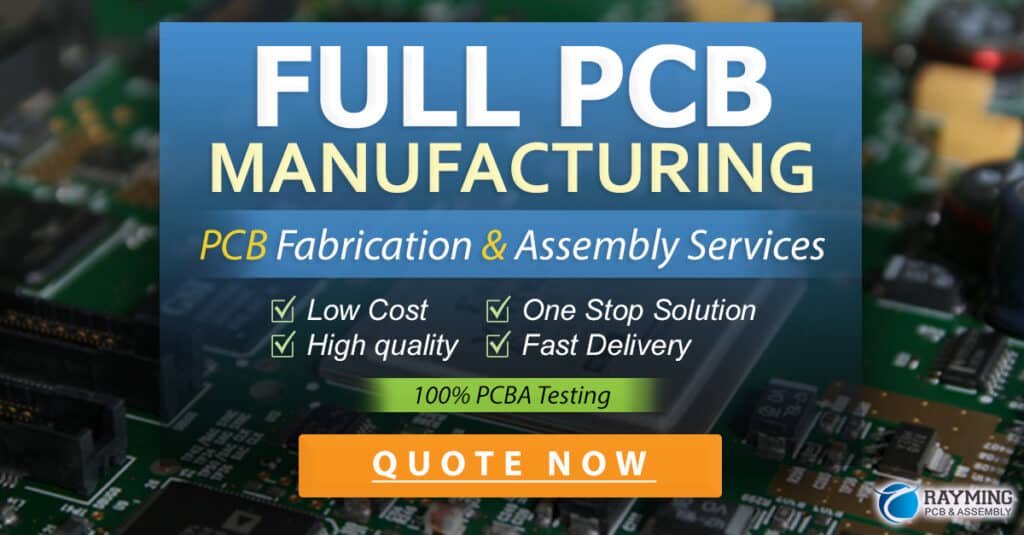
Trend 3: Rigid-Flex and Flex PCBs
Rigid-flex and flexible PCBs are seeing increased adoption due to the rise of wearable technology, foldable displays, and space-constrained electronic devices. Rigid-flex boards combine traditional rigid PCBs with flexible circuits, allowing the board to be bent and folded to fit into compact form factors.
Advantages of rigid-flex and flex PCBs include:
- Space and weight reduction
- Improved reliability, as flex circuits have no solder joints
- Dynamic flexing capability
- Design freedom and manufacturing simplicity
Applications well-suited for rigid-flex and flex PCBs include:
- Wearables like smart watches and AR/VR headsets
- Medical implantables
- Aerospace and defense electronics
- Automotive electronics
- Foldable smartphones and displays
However, designing rigid-flex and flex PCBs requires careful consideration of factors like bend radius, shielding, stiffeners, and stack-up construction. Panelization strategies are also important for manufacturing efficiency and cost.
Trend 4: Additive Manufacturing and 3D Printed Electronics
Additive manufacturing, also known as 3D printing, is an emerging trend in PCB fabrication that offers advantages over traditional subtractive methods. In 3D printed electronics, conductive and insulating materials are selectively deposited to create PCB traces, vias, and other features.
Benefits of additive manufacturing for PCBs include:
- Rapid prototyping and faster time-to-market
- No need for masks or etching chemicals
- Ability to create complex, non-planar geometries
- Potential for embedding components and creating “smart structures”
Some examples of additive manufacturing technologies for PCBs are:
Technology | Description |
---|---|
Inkjet printing | Deposits conductive ink onto substrate using print heads |
Aerosol jet printing | Uses aerodynamic focusing to precisely deposit conductive inks |
Selective laser sintering (SLS) | Sinters powdered metals to form conductive traces |
Stereolithography (SLA) | Uses UV light to cure photopolymer resins layer by layer |
Challenges still remain in terms of conductivity, resolution, and scalability compared to traditional PCB manufacturing. However, advancements in materials and processes are closing the gap, making 3D printed electronics a trend to watch.
Trend 5: Sustainability and Green Manufacturing
Sustainability is becoming an increasingly important consideration in PCB development and manufacturing. Electronics companies are under pressure to reduce their environmental impact and comply with regulations like RoHS and REACH.
Some key aspects of sustainability in PCB manufacturing include:
- Elimination of hazardous substances like lead, cadmium, and certain flame retardants
- Adoption of recycled and biodegradable materials
- More efficient energy and water usage
- Waste reduction and recycling programs
Specific examples of sustainable PCB materials and processes include:
- Halogen-free and low-VOC (volatile organic compound) laminates
- Biodegradable dielectric materials like polylactic acid (PLA)
- Water-based and VOC-free soldermasks
- Recycled copper foils
- Ionic contamination testing and prevention
By embracing sustainable practices, PCB manufacturers can not only reduce their environmental footprint but also appeal to eco-conscious customers and stay ahead of regulatory requirements.
FAQ
What is the most important trend in PCB development?
It’s difficult to single out one trend as the most important, as different trends may be more relevant depending on the specific application and industry. However, the adoption of HDI and advanced packaging technologies is a key overarching trend that enables many of the other trends like 5G, rigid-flex, and miniaturization.
How will 5G impact the PCB industry?
5G is driving demand for PCBs that can operate at higher frequencies and support faster data speeds. This requires the use of advanced materials, tighter tolerances, and innovative structures like filled via-in-pad. PCB manufacturers that can meet the technical challenges of 5G stand to benefit from the growth of 5G devices and infrastructure.
Are 3D printed PCBs a viable alternative to traditional manufacturing?
Additive manufacturing of PCBs is still an emerging technology with some limitations in terms of conductivity, resolution, and scalability compared to traditional subtractive methods. However, it offers advantages in terms of rapid prototyping, design flexibility, and the potential for embedded electronics. As the technology advances, 3D printed PCBs could become a viable option for certain applications.
What are some challenges in Rigid-Flex PCB Design?
Designing rigid-flex PCBs requires careful consideration of factors like bend radius, shielding, stiffeners, and stack-up construction. The transition zone between rigid and flex sections is a critical area that needs to be designed and reinforced properly. Panelization strategies are also important for manufacturing efficiency and cost. Designers need to work closely with fabricators to ensure design for manufacturability (DFM).
How can PCB manufacturers improve sustainability?
There are several ways PCB manufacturers can improve sustainability, including using eco-friendly materials like halogen-free laminates and biodegradable dielectrics, adopting water-based and VOC-free processes, implementing waste reduction and recycling programs, and conducting ionic contamination testing. Compliance with environmental regulations and industry standards is also important. By prioritizing sustainability, manufacturers can reduce their environmental impact and appeal to environmentally conscious customers.
Conclusion
The PCB industry is constantly evolving to keep up with the demands of the electronics market. From HDI and advanced packaging to 5G and mmWave, rigid-flex and 3D printing to sustainability and green manufacturing, there are many exciting trends shaping the future of PCB development.
For PCB designers and engineers, staying on top of these trends is critical to creating innovative, high-performance products that meet customer needs and expectations. Understanding the capabilities and limitations of different technologies, materials, and processes is key to making informed design decisions.
At the same time, PCB manufacturers need to invest in the latest equipment, processes, and workforce skills to stay competitive in a rapidly changing industry. This may require significant capital expenditures and a willingness to embrace new technologies and business models.
Ultimately, the future of PCB development will be shaped by a combination of technological innovation, market demand, and regulatory pressures. By staying informed and adaptable, PCB professionals can navigate these challenges and opportunities to create the next generation of electronic devices that will transform our world.
No responses yet