What is PCB Assembly?
PCB assembly is the process of soldering or mounting electronic components onto a printed circuit board (PCB). It is a crucial step in the manufacturing of electronic devices, as it involves attaching various components such as resistors, capacitors, integrated circuits (ICs), and connectors to the PCB. The assembled PCB, also known as a printed circuit assembly (PCA), forms the backbone of the electronic device, enabling it to function as intended.
PCB assembly can be carried out through various methods, depending on the complexity of the design, the quantity of boards required, and the available resources. The two primary methods of PCB assembly are:
- Through-hole technology (THT)
- Surface mount technology (SMT)
Through-Hole Technology (THT)
Through-hole technology involves inserting component leads through drilled holes in the PCB and soldering them to pads on the opposite side of the board. This method is ideal for larger components or those that require greater mechanical stability. THT is also suitable for low-volume production runs or prototypes, as it can be performed manually or with semi-automatic equipment.
Advantages of THT:
– Stronger mechanical bonds
– Easier to inspect and repair
– Suitable for high-power applications
Disadvantages of THT:
– Larger footprint compared to SMT
– Slower assembly process
– Higher labor costs
Surface Mount Technology (SMT)
Surface mount technology involves placing components directly onto pads on the surface of the PCB and soldering them in place. SMT Components are typically smaller than their THT counterparts, allowing for higher component density and more compact designs. SMT assembly is often automated, using pick-and-place machines and reflow ovens, making it suitable for high-volume production.
Advantages of SMT:
– Smaller footprint and higher component density
– Faster assembly process
– Lower labor costs
– Better high-frequency performance
Disadvantages of SMT:
– Requires specialized equipment
– More difficult to inspect and repair
– Not suitable for high-power applications
PCB Assembly Process
The PCB assembly process typically involves the following steps:
- Solder Paste Application
- Component Placement
- Reflow Soldering
- Inspection and Testing
- Rework and Repair (if necessary)
1. Solder Paste Application
Solder paste, a mixture of tiny solder particles and flux, is applied to the PCB pads using a stencil or screen printing process. The stencil ensures that the solder paste is deposited accurately and consistently on the pads.
2. Component Placement
Components are placed onto the solder paste-covered pads using manual, semi-automatic, or fully automatic methods. For SMT assembly, pick-and-place machines are commonly used to accurately position components on the PCB.
3. Reflow Soldering
The PCB with components placed on it is then subjected to a reflow soldering process. The assembly is heated in a reflow oven, causing the solder paste to melt and form a permanent electrical and mechanical connection between the components and the PCB pads.
4. Inspection and Testing
After the reflow soldering process, the assembled PCB undergoes visual inspection and testing to ensure proper component placement, soldering quality, and functionality. Automated optical inspection (AOI) systems and X-ray inspection may be used to detect any defects or issues.
5. Rework and Repair
If any defects or issues are identified during the inspection and testing phase, the PCB may require rework or repair. This may involve replacing faulty components, resoldering joints, or making other necessary corrections.
PCB Assembly Considerations
When planning a PCB assembly project, several factors should be taken into account to ensure a successful outcome:
- Design for Manufacturing (DFM)
- Component Selection
- Assembly Method
- Quality Control
- Cost and Lead Time
1. Design for Manufacturing (DFM)
Design for Manufacturing (DFM) is the practice of designing PCBs with the manufacturing process in mind. This involves adhering to design guidelines that facilitate efficient and reliable assembly, such as:
- Ensuring adequate pad sizes and spacing
- Avoiding overly small or tightly packed components
- Providing clear silkscreen markings and labels
- Minimizing the number of unique parts
By following DFM principles, designers can reduce the likelihood of assembly issues and improve the overall quality of the final product.
2. Component Selection
Choosing the right components for a PCB assembly project is crucial for ensuring compatibility, reliability, and cost-effectiveness. Factors to consider when selecting components include:
- Functionality and performance requirements
- Availability and lead times
- Cost and minimum order quantities (MOQs)
- Package type (THT or SMT) and size
- Compliance with industry standards and regulations
3. Assembly Method
The choice between THT and SMT assembly methods depends on various factors, such as:
- Component types and sizes
- PCB complexity and layer count
- Production volume and scalability
- Available equipment and resources
- Cost and time constraints
In some cases, a combination of both THT and SMT methods may be used to accommodate different component types or design requirements.
4. Quality Control
Implementing robust quality control measures throughout the PCB assembly process is essential for ensuring consistent and reliable results. This may involve:
- Conducting incoming inspection of components and materials
- Monitoring process parameters (e.g., solder paste application, reflow temperature profiles)
- Performing visual and automated inspection of assembLED PCBs
- Conducting functional testing and burn-in tests
- Maintaining detailed documentation and traceability records
5. Cost and Lead Time
Cost and lead time are important considerations in any PCB assembly project. Factors that can impact cost and lead time include:
- PCB complexity and layer count
- Component availability and pricing
- Assembly method and equipment requirements
- Production volume and minimum order quantities
- Shipping and logistics
To optimize cost and lead time, it is essential to work closely with the PCB assembly service provider and establish clear communication and expectations throughout the project.
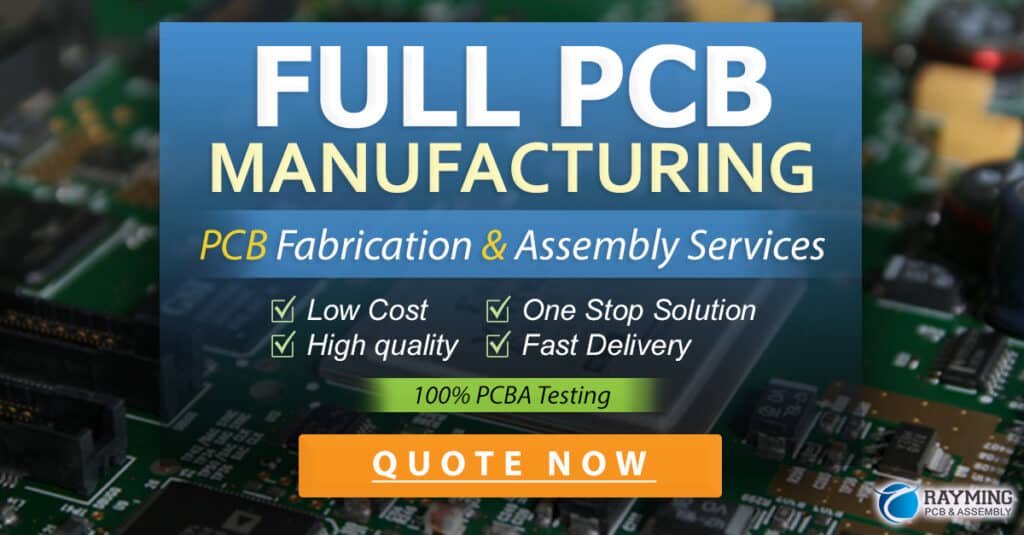
Choosing a PCB Assembly Service Provider
Selecting the right PCB assembly service provider is crucial for the success of your project. When evaluating potential partners, consider the following factors:
- Experience and Expertise
- Quality and Certifications
- Capabilities and Equipment
- Communication and Support
- Pricing and Lead Times
1. Experience and Expertise
Look for a PCB assembly service provider with a proven track record and expertise in the specific requirements of your project, such as:
- Experience with similar PCB designs and components
- Knowledge of industry standards and regulations
- Ability to handle complex or high-density designs
- Familiarity with your target market or application
2. Quality and Certifications
Ensure that the PCB assembly service provider has a robust quality management system and holds relevant certifications, such as:
- ISO 9001 (Quality Management Systems)
- IPC-A-610 (Acceptability of Electronic Assemblies)
- IPC J-STD-001 (Requirements for Soldered Electrical and Electronic Assemblies)
- UL or other safety certifications, if applicable
3. Capabilities and Equipment
Assess the PCB assembly service provider’s capabilities and equipment to ensure they can meet your project requirements, such as:
- SMT and THT assembly capabilities
- Automated optical inspection (AOI) and X-ray inspection
- Functional testing and programming
- Conformal coating and potting
- Box build and final assembly
4. Communication and Support
Choose a PCB assembly service provider that values open communication and provides responsive support throughout the project. Look for:
- Clear and timely communication channels
- Dedicated project management and technical support
- Regular progress updates and reporting
- Flexibility to accommodate changes or revisions
5. Pricing and Lead Times
Obtain quotes from multiple PCB assembly service providers and compare their pricing and lead times. However, keep in mind that the lowest price may not always be the best option, as quality, reliability, and support should also be considered. Look for a partner that offers a fair balance between cost, lead time, and overall value.
PCB Assembly FAQs
1. What is the difference between PCB assembly and PCB fabrication?
PCB fabrication is the process of manufacturing the bare printed circuit board, which includes designing the circuit layout, printing the copper traces, drilling holes, and applying the soldermask and silkscreen. PCB assembly, on the other hand, involves soldering or mounting electronic components onto the fabricated PCB to create a functional printed circuit assembly (PCA).
2. How do I choose between THT and SMT assembly methods?
The choice between THT and SMT assembly methods depends on factors such as the types and sizes of components used, the complexity of the PCB design, the required production volume, and the available budget. SMT is generally more suitable for smaller components and high-volume production, while THT is often used for larger components or low-volume runs. In some cases, a combination of both methods may be used to accommodate different component types or design requirements.
3. What information do I need to provide to a PCB assembly service provider?
When engaging a PCB assembly service provider, you should provide the following information:
- Gerber files for the PCB design
- Bill of Materials (BOM) listing all components and their quantities
- Assembly drawings or instructions
- Any special requirements or specifications (e.g., testing, packaging)
- Target quantities and delivery dates
Providing clear and complete information upfront can help streamline the quoting and assembly process and avoid potential delays or issues.
4. How long does PCB assembly typically take?
The lead time for PCB assembly depends on various factors, such as the complexity of the design, the availability of components, the production volume, and the workload of the assembly service provider. Simple designs with readily available components may be assembled within a few days, while more complex projects or those with custom or hard-to-find components may take several weeks. It is essential to discuss your specific requirements and timeline with the assembly service provider to ensure they can meet your needs.
5. What quality control measures should I expect from a PCB assembly service provider?
A reputable PCB assembly service provider should have a robust quality management system in place, which may include:
- Incoming inspection of components and materials
- Process control and monitoring (e.g., solder paste application, reflow temperature profiles)
- Visual and automated inspection of assembled PCBs (e.g., AOI, X-ray)
- Functional testing and burn-in tests
- Detailed documentation and traceability records
When selecting a PCB assembly service provider, inquire about their quality control processes and certifications to ensure they can consistently deliver high-quality results.
Conclusion
PCB assembly is a critical process in the production of electronic devices, involving the soldering or mounting of components onto a printed circuit board. Choosing the right assembly method, components, and service provider is essential for ensuring a successful outcome. By understanding the various aspects of PCB assembly, from design considerations to quality control measures, you can make informed decisions and work effectively with your chosen assembly partner to bring your electronic product to life.
When selecting a PCB assembly service provider, such as PCB Proto, look for a partner with the experience, capabilities, and commitment to quality that aligns with your project requirements. By fostering open communication, setting clear expectations, and maintaining a focus on reliability and customer satisfaction, you can build a strong partnership that will support your PCB assembly needs now and in the future.
Assembly Method | Advantages | Disadvantages |
---|---|---|
Through-Hole Technology (THT) | – Stronger mechanical bonds – Easier to inspect and repair – Suitable for high-power applications |
– Larger footprint compared to SMT – Slower assembly process – Higher labor costs |
Surface Mount Technology (SMT) | – Smaller footprint and higher component density – Faster assembly process – Lower labor costs – Better high-frequency performance |
– Requires specialized equipment – More difficult to inspect and repair – Not suitable for high-power applications |
This article provides a comprehensive overview of PCB assembly, covering key topics such as assembly methods, process steps, design considerations, and tips for choosing the right assembly service provider. By understanding these aspects and partnering with a reliable PCB assembly company, you can ensure the successful production of your electronic devices.
No responses yet