Introduction to Bill of Materials (BOM)
A Bill of Materials (BOM) is a comprehensive list of all the components, parts, raw materials, sub-assemblies, and associated quantities required to manufacture a product. It serves as a crucial document for product development, procurement, and production processes. The BOM provides a structured and hierarchical representation of the product, enabling effective communication among various departments involved in the product lifecycle.
In this article, we will explore the methods of designing a BOM type file, specifically focusing on box files. We will discuss the importance of BOMs, their key components, and best practices for creating and managing them effectively.
The Significance of Bill of Materials
Facilitating Product Development
A well-structured BOM plays a vital role in the product development process. It serves as a central repository of information, providing a clear and concise overview of all the components required to build a product. By defining the product structure and its constituent parts, the BOM enables cross-functional teams to collaborate effectively, identify potential issues, and make informed decisions throughout the development cycle.
Streamlining Procurement and Inventory Management
The BOM acts as a foundation for procurement and inventory management activities. It provides a detailed list of the components and their quantities, allowing procurement teams to plan and execute purchasing strategies efficiently. By accurately specifying the required materials, the BOM helps ensure that the right components are ordered in the correct quantities, minimizing excess inventory and reducing the risk of stockouts.
Enhancing Production Efficiency
In the manufacturing process, the BOM serves as a roadmap for production planning and execution. It provides a clear understanding of the assembly sequence, required tools, and production processes. By breaking down the product into its constituent parts and sub-assemblies, the BOM enables production teams to optimize their workflows, minimize errors, and improve overall efficiency.
Key Components of a Bill of Materials
Part Numbers and Descriptions
Each component or part in the BOM is assigned a unique part number and description. The part number serves as a standard identifier, allowing easy referencing and tracking throughout the product lifecycle. The description provides additional details about the part, such as its specifications, dimensions, or material composition. Clear and consistent part numbering and descriptions are essential for effective communication and collaboration among different teams.
Quantity and Unit of Measure
The BOM specifies the quantity of each component required to produce one unit of the final product. It is important to clearly indicate the unit of measure (UOM) for each quantity, such as pieces, kilograms, or meters. Accurate quantity information ensures that the right amount of materials is procured and allocated for production.
Revision and Change Control
As products evolve and undergo modifications, it is crucial to maintain version control and track changes in the BOM. Each revision of the BOM should be clearly identified with a unique revision number or code. This allows for traceability and ensures that all stakeholders are working with the most up-to-date information. Change control processes should be in place to manage and communicate any updates or modifications to the BOM.
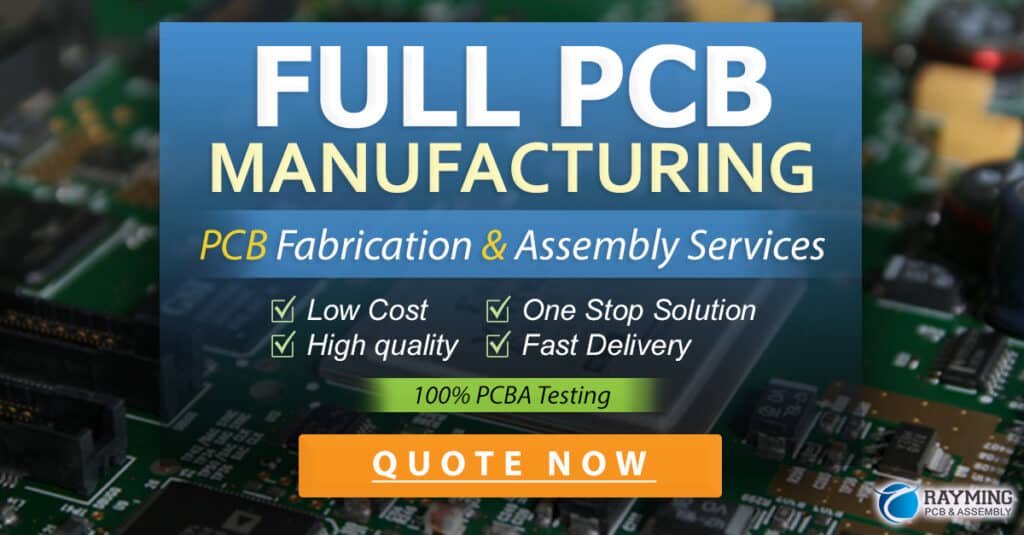
Designing a Box File BOM
Structuring the BOM Hierarchy
When designing a BOM for a box file, it is important to create a logical and hierarchical structure. The BOM hierarchy typically consists of multiple levels, representing the parent-child relationships between components and sub-assemblies. The top level represents the final product (the box file), while subsequent levels break down the product into its constituent parts and sub-assemblies.
Here’s an example of a simplified BOM hierarchy for a box file:
Level | Part Number | Description | Quantity | UOM |
---|---|---|---|---|
0 | BF-001 | Box File | 1 | EA |
1 | BF-001-01 | Box File Cover | 1 | EA |
2 | BF-001-01-01 | Cover Material (Cardboard) | 1 | SQM |
2 | BF-001-01-02 | Cover Printing | 1 | EA |
1 | BF-001-02 | Box File Base | 1 | EA |
2 | BF-001-02-01 | Base Material (Cardboard) | 1 | SQM |
2 | BF-001-02-02 | Base Reinforcement | 4 | EA |
1 | BF-001-03 | Box File Mechanism | 1 | EA |
2 | BF-001-03-01 | Lever Arch Mechanism | 1 | EA |
2 | BF-001-03-02 | Rivets | 2 | EA |
1 | BF-001-04 | Box File Label | 1 | EA |
2 | BF-001-04-01 | Label Material (Paper) | 1 | SQM |
2 | BF-001-04-02 | Label Printing | 1 | EA |
This hierarchical structure provides a clear understanding of how the box file is assembled and the relationships between its components.
Defining Part Attributes
In addition to the basic information such as part numbers, descriptions, quantities, and UOMs, it is important to include relevant attributes for each part in the BOM. These attributes provide additional details that are necessary for procurement, production, and quality control. Some common attributes include:
- Material specification
- Dimensions (length, width, height)
- Color
- Finish
- Supplier information
- Lead time
- Cost
By including these attributes, the BOM becomes a comprehensive source of information for all stakeholders involved in the product lifecycle.
Incorporating Visual Aids
Visual aids can greatly enhance the clarity and usability of a BOM. Consider including images, drawings, or CAD models of the components and sub-assemblies. These visual representations help in understanding the product structure, assembly sequence, and component relationships. They also facilitate communication between different teams, reducing the risk of misinterpretation or errors.
Ensuring Data Accuracy and Consistency
Maintaining data accuracy and consistency is crucial for an effective BOM. Implement data validation and error-checking mechanisms to ensure that the information entered into the BOM is accurate and complete. Establish standard naming conventions and formatting guidelines to maintain consistency across different BOMs and related documents.
Best Practices for Managing BOMs
Collaboration and Communication
Effective collaboration and communication are essential for successful BOM management. Ensure that all relevant stakeholders, including engineering, procurement, production, and quality teams, have access to the latest version of the BOM. Establish clear communication channels and processes for sharing updates, resolving discrepancies, and addressing any issues that arise.
Change Management
Implement a robust change management process to handle revisions and updates to the BOM. Any changes to the product design, component specifications, or quantities should be documented and communicated to all affected parties. Maintain a change history log to track the evolution of the BOM over time, allowing for traceability and auditing purposes.
Integration with Other Systems
Consider integrating the BOM with other enterprise systems, such as Enterprise Resource Planning (ERP), Product Lifecycle Management (PLM), or Manufacturing Execution System (MES). Integration enables seamless data flow, eliminates manual data entry, and ensures that the BOM information is consistent across different systems. This integration streamlines processes, improves efficiency, and reduces the risk of errors.
Regular Reviews and Audits
Conduct regular reviews and audits of the BOM to ensure its accuracy and completeness. Periodically verify that the BOM reflects the latest product design, component specifications, and production processes. Identify and address any discrepancies or inconsistencies promptly to maintain the integrity of the BOM.
Frequently Asked Questions (FAQ)
- What is the difference between an Engineering BOM (EBOM) and a Manufacturing BOM (MBOM)?
- An Engineering BOM (EBOM) represents the product structure from a design perspective, focusing on the functional relationships between components. It is created during the product development phase and is used by engineers for design and prototyping purposes.
-
A Manufacturing BOM (MBOM) represents the product structure from a production perspective, focusing on the assembly sequence and manufacturing processes. It is derived from the EBOM and includes additional information necessary for production, such as packaging materials and production instructions.
-
How often should a BOM be updated?
- A BOM should be updated whenever there are changes to the product design, component specifications, or production processes. It is important to maintain the BOM as a living document, reflecting the most up-to-date information.
-
The frequency of updates may vary depending on the nature of the product and the industry. In some cases, updates may be required on a daily or weekly basis, while in others, updates may be less frequent.
-
What is the role of a BOM in cost estimation and budgeting?
- The BOM provides a detailed breakdown of the components and their quantities required to produce a product. By assigning costs to each component, the BOM can be used to estimate the total cost of materials and production.
-
The BOM serves as a basis for budgeting and financial planning. It helps in determining the cost of goods sold (COGS), setting pricing strategies, and evaluating the financial viability of a product.
-
How can I ensure the security and confidentiality of BOM information?
- Implement appropriate access controls and permissions to restrict access to the BOM information. Only authorized personnel should have access to the BOM based on their roles and responsibilities.
- Use secure data storage and transmission methods to protect the confidentiality of the BOM information. Encrypt sensitive data and ensure that it is stored in a secure environment.
-
Establish clear policies and guidelines for handling and sharing BOM information, including non-disclosure agreements (NDAs) with external partners or suppliers.
-
What are some common challenges in managing BOMs?
- Maintaining data accuracy and consistency across different systems and departments can be challenging. Ensuring that all stakeholders are working with the most up-to-date information requires robust communication and change management processes.
- Managing complex product structures with multiple levels and a large number of components can be time-consuming and prone to errors. Implementing automated tools and processes can help streamline BOM management and reduce the risk of errors.
- Collaborating with external partners, such as suppliers or contract manufacturers, can introduce additional complexities in BOM management. Establishing clear communication channels, data exchange protocols, and version control mechanisms is essential for effective collaboration.
Conclusion
Designing and managing a Bill of Materials (BOM) type file for a box file requires a systematic approach and adherence to best practices. By creating a well-structured BOM hierarchy, defining part attributes, incorporating visual aids, and ensuring data accuracy and consistency, organizations can streamline their product development, procurement, and production processes.
Effective BOM management involves collaboration, communication, change management, and integration with other enterprise systems. Regular reviews and audits are essential to maintain the integrity and accuracy of the BOM over time.
By implementing the methods and best practices discussed in this article, organizations can enhance their BOM management capabilities, improve efficiency, and ultimately deliver high-quality products to their customers.
No responses yet