Understanding the Requirements of PCB Enclosure Design
Before starting the enclosure design process, it is essential to understand the specific requirements of the PCBA and the end product. Some of the key factors to consider include:
Environmental Factors
The enclosure must be designed to protect the PCBA from environmental factors such as:
- Temperature: The enclosure should be able to withstand the expected temperature range of the product’s operating environment.
- Humidity: The enclosure should be designed to prevent moisture from entering and damaging the PCBA.
- Dust and Debris: The enclosure should be sealed to prevent dust and debris from accumulating on the PCBA.
Mechanical Factors
The enclosure must also be designed to withstand mechanical stresses such as:
- Vibration: The enclosure should be designed to minimize the impact of vibrations on the PCBA.
- Shock: The enclosure should be able to absorb shocks and impacts without damaging the PCBA.
- Pressure: The enclosure should be able to withstand the expected pressure levels of the product’s operating environment.
Electromagnetic Compatibility (EMC)
The enclosure must be designed to minimize electromagnetic interference (EMI) and ensure electromagnetic compatibility (EMC) with other electronic devices. This can be achieved through the use of shielding materials and proper grounding techniques.
Accessibility and Maintenance
The enclosure should be designed to allow for easy access to the PCBA for maintenance and repairs. This may include the use of removable panels or access ports.
Aesthetics and Branding
The enclosure should be designed to enhance the overall aesthetics of the product and incorporate any necessary branding elements such as logos or colors.
Selecting the Appropriate Material for PCB Enclosure Design
The choice of material for the enclosure is a critical decision that will impact the performance, durability, and cost of the final product. Some of the most common materials used for PCB enclosures include:
Plastic
Plastic is a popular choice for PCB enclosures due to its low cost, lightweight, and ease of manufacturing. Some of the most common types of plastic used for enclosures include:
- ABS (Acrylonitrile Butadiene Styrene)
- PC (Polycarbonate)
- PVC (Polyvinyl Chloride)
- Nylon
Metal
Metal enclosures offer superior strength, durability, and EMI Shielding compared to plastic enclosures. Some of the most common types of metal used for enclosures include:
- Aluminum
- Steel
- Stainless Steel
- Copper
Composite Materials
Composite materials such as carbon fiber and fiberglass offer a combination of strength, lightweight, and EMI shielding properties. However, they are generally more expensive than plastic or metal enclosures.
The choice of material will depend on the specific requirements of the product, such as the expected environmental conditions, mechanical stresses, and EMI shielding needs.
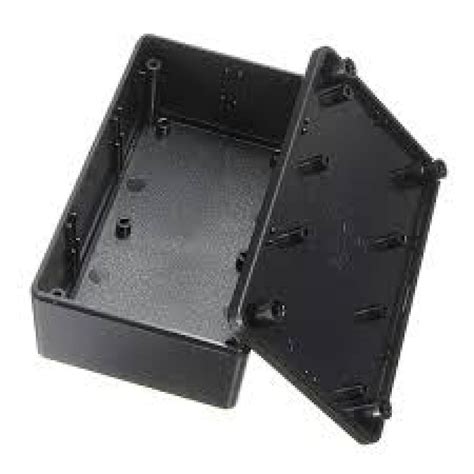
Designing the Enclosure for Manufacturing
Once the material has been selected, the next step is to design the enclosure for manufacturing. This involves creating detailed 3D models and 2D drawings of the enclosure using computer-aided design (CAD) software.
3D Modeling
3D modeling allows designers to create a virtual representation of the enclosure and test its fit and function before manufacturing. Some of the most common CAD Software used for 3D modeling include:
- SolidWorks
- Autodesk Fusion 360
- Creo
- CATIA
2D Drawings
2D drawings are used to communicate the design intent to the manufacturing team and ensure that the enclosure is produced to the correct specifications. The drawings should include:
- Dimensions
- Tolerances
- Material specifications
- Finishing requirements
- Assembly instructions
Design for Manufacturing (DFM)
When designing the enclosure, it is important to consider the manufacturing process and ensure that the design is optimized for production. This involves following Design for Manufacturing (DFM) principles such as:
- Minimizing the number of parts
- Avoiding undercuts and sharp corners
- Designing for ease of assembly
- Specifying standard components and materials
- Allowing for adequate draft angles and radii
By following DFM principles, designers can reduce manufacturing costs, improve production efficiency, and ensure the quality and reliability of the final product.
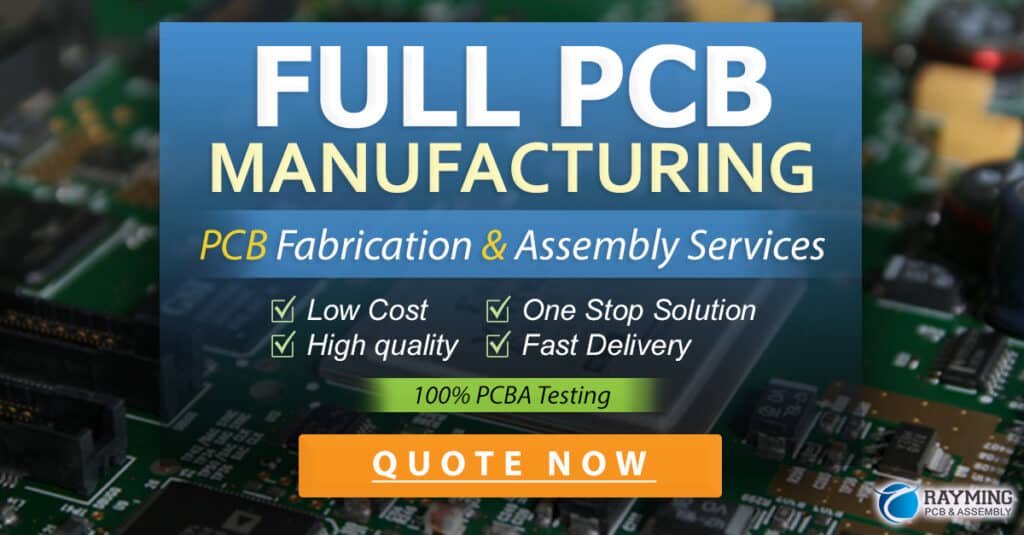
Prototyping and Testing
Before mass production, it is important to create prototypes of the enclosure and test them to ensure that they meet the required specifications and performance criteria. Prototyping allows designers to:
- Verify the fit and function of the enclosure
- Test the mechanical and environmental performance
- Evaluate the aesthetics and ergonomics
- Identify and correct any design flaws
There are several methods for creating prototypes, including:
3D Printing
3D printing is a Rapid prototyping technique that allows designers to create physical models of the enclosure directly from the 3D CAD model. This method is fast and relatively low cost, making it ideal for early-stage prototyping and design validation.
CNC Machining
CNC machining is a subtractive manufacturing process that involves cutting away material from a solid block to create the desired shape. This method is more expensive and time-consuming than 3D printing but offers higher precision and better material properties.
Injection Molding
Injection molding is a manufacturing process that involves injecting molten plastic into a mold cavity to create the desired shape. This method is suitable for high-volume production and offers excellent dimensional accuracy and surface finish.
Once the prototypes have been created, they should be subjected to various tests to ensure that they meet the required performance criteria. Some of the common tests include:
- Environmental testing (temperature, humidity, dust)
- Mechanical testing (vibration, shock, pressure)
- EMC testing (electromagnetic interference, electromagnetic compatibility)
- Functional testing (fit, assembly, accessibility)
Based on the test results, designers may need to make modifications to the enclosure design to improve its performance and reliability.
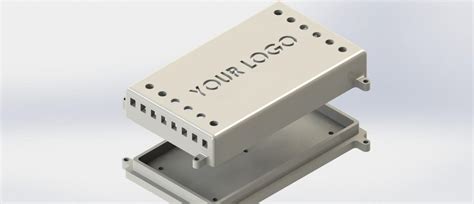
Best Practices for PCB Enclosure Design
To ensure the success of the PCB enclosure design, it is important to follow some best practices:
Collaborate with the PCBA Design Team
The enclosure design should be developed in close collaboration with the PCBA design team to ensure that the enclosure is optimized for the specific requirements of the PCBA. This includes considerations such as component placement, heat dissipation, and Signal Integrity.
Use Standardized Components and Materials
Using standardized components and materials can help reduce manufacturing costs, improve production efficiency, and ensure the availability of replacement parts. This includes considerations such as fasteners, connectors, and sheet metal gauges.
Allow for Future Upgrades and Expansions
The enclosure should be designed with future upgrades and expansions in mind. This may include leaving extra space for additional components or designing the enclosure to be modular and easily reconfigurable.
Consider the User Experience
The enclosure should be designed with the user experience in mind, including considerations such as ergonomics, accessibility, and aesthetics. This may involve conducting user research and usability testing to ensure that the enclosure meets the needs and preferences of the target audience.
Document the Design Process
It is important to document the entire design process, including the requirements, design decisions, and test results. This documentation can serve as a reference for future projects and help ensure the consistency and quality of the final product.
Frequently Asked Questions (FAQ)
-
What is the difference between a PCB and a PCBA?
A: A PCB (Printed Circuit Board) is the bare board without any components attached, while a PCBA (Printed Circuit Board Assembly) is the PCB with all the components soldered onto it. -
What are the most common materials used for PCB enclosures?
A: The most common materials used for PCB enclosures are plastic (ABS, PC, PVC, Nylon), metal (aluminum, steel, stainless steel, copper), and composite materials (carbon fiber, fiberglass). -
What is EMI shielding and why is it important for PCB enclosures?
A: EMI (Electromagnetic Interference) shielding is the practice of using conductive materials to prevent electromagnetic radiation from entering or leaving the enclosure. It is important for ensuring the electromagnetic compatibility (EMC) of the product and preventing interference with other electronic devices. -
What is Design for Manufacturing (DFM) and why is it important for PCB enclosure design?
A: Design for Manufacturing (DFM) is the practice of designing products with the manufacturing process in mind, in order to reduce costs, improve efficiency, and ensure quality. It is important for PCB enclosure design because it helps ensure that the enclosure can be manufactured reliably and cost-effectively. -
What are some common tests performed on PCB enclosure prototypes?
A: Some common tests performed on PCB enclosure prototypes include environmental testing (temperature, humidity, dust), mechanical testing (vibration, shock, pressure), EMC testing (electromagnetic interference, electromagnetic compatibility), and functional testing (fit, assembly, accessibility).
In conclusion, designing an enclosure for a Printed Circuit Board Assembly (PCBA) is a complex process that requires careful consideration of various factors such as environmental conditions, mechanical stresses, electromagnetic compatibility, accessibility, aesthetics, and manufacturing feasibility. By following best practices such as collaborating with the PCBA design team, using standardized components and materials, allowing for future upgrades and expansions, considering the user experience, and documenting the design process, designers can create enclosures that are optimized for performance, reliability, and cost-effectiveness. With the right approach and attention to detail, a well-designed PCB enclosure can help ensure the success and longevity of the final product.
No responses yet