Introduction to DIY PCB
DIY PCB, or Do-It-Yourself Printed Circuit Boards, have become increasingly popular among electronics enthusiasts, hobbyists, and even professionals. Creating your own circuit boards allows you to bring your electronic projects to life while providing a sense of accomplishment and customization. In this comprehensive guide, we will walk you through the key steps involved in building your own circuit boards, from designing the schematic to the final assembly.
Understanding the Basics of Circuit Boards
Before diving into the process of building a circuit board, it’s essential to understand the basics. A circuit board, also known as a printed circuit board (PCB), is a platform that mechanically supports and electrically connects electronic components using conductive tracks, pads, and other features etched from copper sheets laminated onto a non-conductive substrate.
Types of Circuit Boards
There are several types of circuit boards, each with its own characteristics and applications:
- Single-Layer PCB: These boards have conductive tracks on only one side of the substrate.
- Double-layer PCB: These boards have conductive tracks on both sides of the substrate, allowing for more complex designs and higher component density.
- Multi-layer PCB: These boards have multiple layers of conductive tracks separated by insulating layers, enabling even more complex designs and improved signal integrity.
- Flexible PCB: These boards are made from flexible materials, allowing them to bend and conform to various shapes.
PCB Materials
The choice of materials for your PCB depends on the specific requirements of your project, such as the operating environment, electrical properties, and cost. Some common PCB materials include:
- FR-4: A widely used substrate material made from fiberglass reinforced epoxy laminate.
- Polyimide: A flexible substrate material known for its high temperature resistance and durability.
- Aluminum: Used for PCBs that require excellent thermal dissipation properties.
Step 1: Designing the Schematic
The first step in building a circuit board is designing the schematic. A schematic is a graphical representation of the electronic circuit, showing the components and their interconnections. It serves as a blueprint for the PCB layout.
Choosing the Right Software
To create a schematic, you’ll need to use electronic design automation (EDA) software. Some popular options include:
- KiCad: A free and open-source EDA software suite that includes schematic capture and PCB layout tools.
- Eagle: A widely used EDA software with a user-friendly interface and extensive component libraries.
- Altium Designer: A professional-grade EDA software with advanced features and a steep learning curve.
Creating the Schematic
When creating the schematic, follow these guidelines:
- Use standard symbols: Utilize standardized symbols for components to ensure clarity and readability.
- Label components: Assign unique labels to each component for easy reference during the PCB layout process.
- Define net names: Assign meaningful names to the nets (connections) between components to aid in the PCB layout.
- Add power and ground symbols: Include power and ground symbols to clearly define the power supply connections.
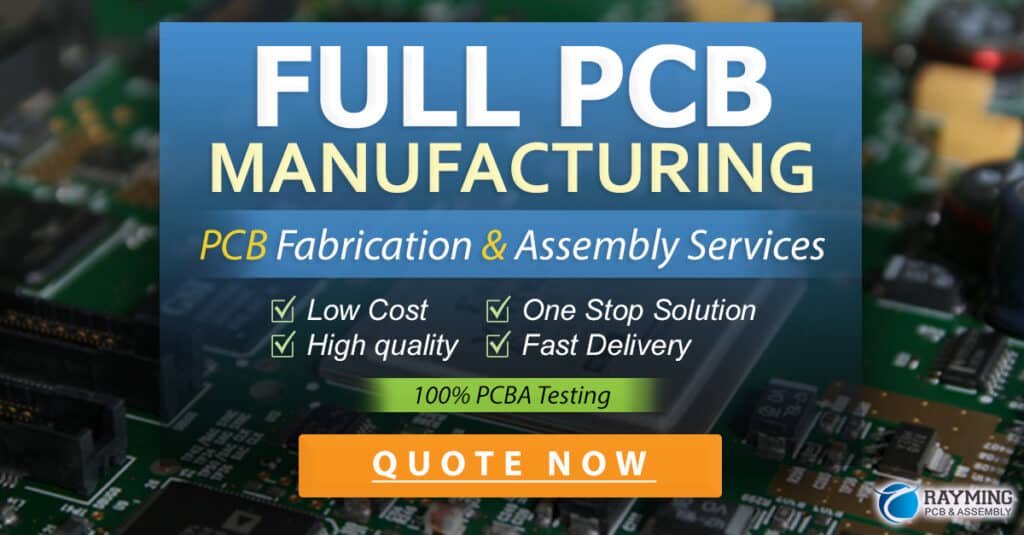
Step 2: Designing the PCB Layout
Once the schematic is complete, the next step is to design the PCB layout. The PCB layout determines the physical arrangement of components and the routing of conductive tracks on the board.
PCB Layout Considerations
When designing the PCB layout, keep the following considerations in mind:
- Component placement: Arrange components in a logical and efficient manner, considering factors such as signal flow, heat dissipation, and mechanical constraints.
- Track width: Select appropriate track widths based on the current carrying requirements and the PCB manufacturing capabilities.
- Clearance and spacing: Maintain sufficient clearance between components and tracks to avoid short circuits and ensure manufacturability.
- Via placement: Use vias (plated holes) to connect tracks between layers when necessary, minimizing their number and placing them strategically.
Routing Techniques
Routing is the process of creating conductive tracks to connect the components according to the schematic. Here are some common routing techniques:
- Manual routing: Manually place and route tracks using the EDA software’s tools.
- Autorouting: Utilize the EDA software’s autorouting feature to automatically route tracks based on predefined rules and constraints.
- Differential pair routing: Route differential signals (e.g., high-speed digital signals) as matched pairs to maintain signal integrity.
Step 3: PCB Fabrication
After finalizing the PCB layout, the next step is to fabricate the physical board. You have two options for PCB fabrication: in-house fabrication or outsourcing to a PCB manufacturing service.
In-House Fabrication
If you have access to the necessary equipment and materials, you can fabricate the PCB in-house. The process typically involves the following steps:
- Printing the PCB artwork: Print the PCB layout onto a transparent film or photosensitive paper.
- Exposing the photoresist: Transfer the PCB artwork onto a copper-clad board coated with photoresist using UV light exposure.
- Developing the photoresist: Remove the exposed photoresist using a developer solution.
- Etching the copper: Immerse the board in an etching solution to remove the unwanted copper, leaving only the desired tracks.
- Drilling holes: Drill holes for through-hole components and vias using a drill press or a CNC machine.
Outsourcing to a PCB Manufacturing Service
Outsourcing PCB fabrication to a professional manufacturing service is often more convenient and cost-effective, especially for complex designs or large quantities. To outsource PCB fabrication:
- Generate manufacturing files: Export the necessary manufacturing files (e.g., Gerber files, drill files) from your EDA software.
- Choose a PCB manufacturer: Research and select a reputable PCB manufacturing service that meets your requirements (e.g., lead time, cost, quality).
- Submit files and place an order: Upload the manufacturing files and place an order with the chosen PCB manufacturer.
Step 4: PCB Assembly
Once the PCB is fabricated, the final step is to assemble the components onto the board. PCB assembly can be done manually or using automated assembly techniques.
Manual Assembly
For manual assembly, follow these steps:
- Gather components: Collect all the necessary components for your PCB based on the bill of materials (BOM).
- Solder components: Use a soldering iron and solder to attach the components to the PCB. Start with the smallest components and work your way up to the larger ones.
- Inspect and clean: Visually inspect the soldered joints for any defects or short circuits. Clean the PCB using isopropyl alcohol to remove flux residue.
Automated Assembly
For larger quantities or complex designs, automated assembly techniques such as surface mount technology (SMT) and wave soldering are used. These techniques require specialized equipment and are typically outsourced to professional assembly services.
Testing and Debugging
After assembling the PCB, it’s crucial to test and debug the board to ensure its functionality and reliability. Here are some steps to follow:
- Visual inspection: Conduct a thorough visual inspection of the assembled PCB, checking for any visible defects, short circuits, or missing components.
- Continuity testing: Use a multimeter to test for continuity between various points on the PCB, ensuring that the connections are intact and there are no short circuits.
- Power-on testing: Apply power to the PCB and verify that it functions as expected. Check for any unusual behavior, such as overheating or unexpected voltage levels.
- Functional testing: Test the PCB’s functionality by applying input signals and measuring the output response. Compare the results with the expected behavior based on the schematic.
- Debugging: If any issues are found during testing, use debugging techniques such as probing with an oscilloscope or logic analyzer to identify the root cause and make necessary corrections.
Tips and Best Practices
Here are some tips and best practices to keep in mind when building DIY circuit boards:
- Start with a simple design: If you’re new to PCB design, start with a simple project to gain familiarity with the process before moving on to more complex designs.
- Use a modular approach: Break down your design into smaller, modular sections to make it easier to design, debug, and modify.
- Follow design guidelines: Adhere to the design guidelines provided by your chosen PCB manufacturer to ensure manufacturability and reliability.
- Use version control: Implement version control for your schematic and PCB layout files to track changes and collaborate with others effectively.
- Document your work: Maintain clear documentation of your design, including schematics, BOMs, and assembly instructions, to facilitate future modifications and troubleshooting.
Frequently Asked Questions (FAQ)
-
What is the difference between a breadboard and a PCB?
A breadboard is a prototyping tool used for temporarily connecting electronic components, while a PCB is a permanent and more reliable solution for interconnecting components. -
Can I design a PCB without using EDA software?
While it is technically possible to design a PCB manually, using EDA software significantly simplifies the process and helps avoid errors. EDA software provides tools for schematic capture, PCB layout, and design rule checking. -
How do I choose the right PCB Thickness for my project?
The choice of PCB thickness depends on factors such as the component sizes, mechanical requirements, and the intended application. Common PCB thicknesses range from 0.8mm to 1.6mm, with 1.6mm being the most widely used. -
What is the difference between through-hole and surface mount components?
Through-hole components have leads that are inserted into holes drilled in the PCB and soldered on the opposite side. Surface mount components are placed directly on the surface of the PCB and soldered in place. Surface mount components are generally smaller and allow for higher component density. -
How can I reduce electromagnetic interference (EMI) in my PCB design?
To reduce EMI in your PCB design, consider techniques such as proper grounding, use of ground planes, minimizing loop areas, and separating sensitive signals from noisy ones. Additionally, using shielding techniques and filters can help mitigate EMI.
Conclusion
Building your own circuit boards can be a rewarding and educational experience. By following the key steps outlined in this guide, from designing the schematic to assembling the PCB, you can bring your electronic projects to life. Remember to start with simple designs, adhere to best practices, and continuously learn from your experiences. With practice and perseverance, you’ll be able to create increasingly complex and sophisticated PCBs for your DIY projects.
Resources and Further Reading
Here are some resources and further reading materials to help you deepen your understanding of DIY PCB design and fabrication:
- “Make Your Own PCBs with EAGLE: From Schematic Designs to Finished Boards” by Simon Monk
- “KiCad Like a Pro” by Peter Dalmaris
- “PCB Design for Real-World EMI Control” by Bruce R. Archambeault and James Drewniak
- Sparkfun Electronics PCB Basics Tutorial: https://learn.sparkfun.com/tutorials/pcb-basics
- EEVblog PCB Design Tutorial Series: https://www.youtube.com/playlist?list=PLy2022BX6Eso532xqrUxDT1u2p4VVsg-q
Happy PCB designing and building!
No responses yet