What is PCB Assembly?
PCB assembly is the process of assembling electronic components onto a printed circuit board to create a functional electronic device. The process involves several steps, including:
-
Solder Paste Application: Solder paste, a mixture of tiny solder particles and flux, is applied to the PCB’s pads using a stencil or screen printing process.
-
Component Placement: Electronic components, such as resistors, capacitors, and integrated circuits, are placed onto the solder paste-coated pads using automated pick-and-place machines or manual placement.
-
Reflow Soldering: The PCB with the placed components is heated in a reflow oven, melting the solder paste and creating a permanent electrical and mechanical connection between the components and the PCB.
-
Inspection and Testing: The assembled PCB undergoes visual inspection and electrical testing to ensure proper functionality and quality.
PCB assembly can be categorized into two main types:
- Through-Hole Assembly (THA): Components with long leads are inserted into drilled holes on the PCB and soldered on the opposite side.
- Surface Mount Assembly (SMT): Components are placed and soldered directly onto the surface of the PCB, allowing for smaller component sizes and higher component density.
Advantages of One-stop PCB Assembly Services
One-stop PCB assembly services offer numerous benefits to businesses looking to outsource their PCB assembly needs:
1. Time and Cost Savings
By partnering with a one-stop PCB assembly service provider, businesses can save time and money. These service providers have the necessary equipment, expertise, and resources to handle the entire PCB assembly process efficiently, reducing lead times and minimizing costs associated with in-house production.
2. Expertise and Quality Assurance
One-stop PCB assembly service providers employ experienced professionals who specialize in various aspects of PCB assembly, such as design, component selection, and quality control. They possess the knowledge and skills to ensure that the assembled PCBs meet the highest quality standards and are fully functional.
3. Access to Advanced Technology
One-stop PCB assembly service providers invest in state-of-the-art equipment and technology to stay competitive in the market. By outsourcing PCB assembly, businesses can leverage these advanced technologies without the need for significant capital investments.
4. Scalability and Flexibility
One-stop PCB assembly services offer scalability and flexibility to accommodate varying production volumes and project requirements. Whether a business needs prototypes, small batches, or large-scale production, these service providers can adapt their processes to meet specific needs.
5. Supply Chain Management
One-stop PCB assembly service providers often have established relationships with component suppliers and can manage the entire supply chain on behalf of their clients. This includes component procurement, inventory management, and logistics, allowing businesses to focus on their core competencies.
Choosing the Right One-stop PCB Assembly Service Provider
When selecting a one-stop PCB assembly service provider, consider the following factors:
-
Technical Capabilities: Ensure that the service provider has the necessary equipment, expertise, and experience to handle your specific PCB assembly requirements.
-
Quality Standards: Look for a service provider that adheres to strict quality control measures and holds relevant certifications, such as ISO 9001 and IPC standards.
-
Turnaround Time: Consider the service provider’s ability to meet your project deadlines and deliver assembled PCBs within the required timeframe.
-
Cost: Compare pricing from multiple service providers to ensure you are getting a competitive rate without compromising on quality.
-
Customer Support: Choose a service provider that offers responsive customer support and clear communication throughout the PCB assembly process.
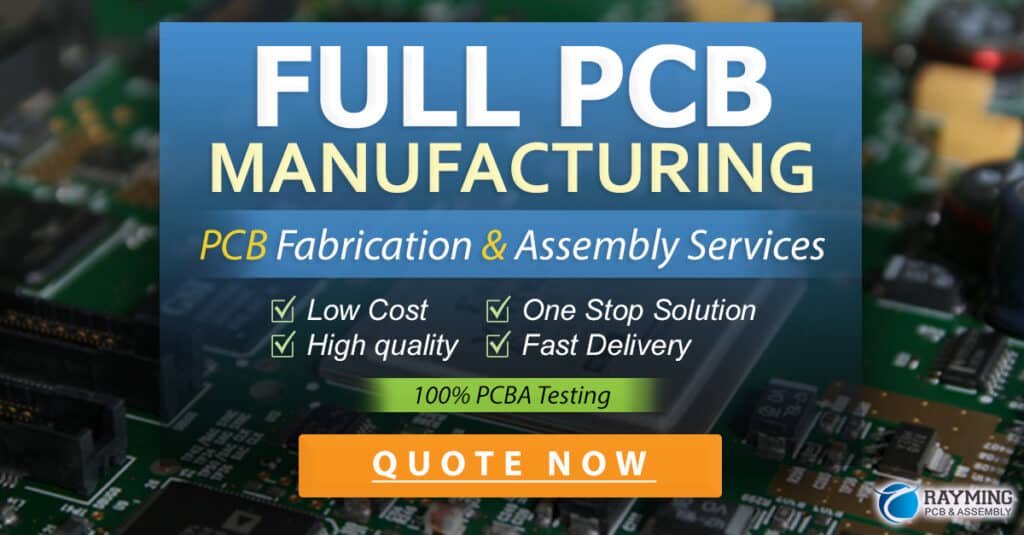
PCB Assembly Process Flow
The PCB assembly process typically follows these steps:
-
Design and Planning: The PCB design is finalized, and the assembly process is planned, including component selection and placement.
-
PCB Fabrication: The bare PCB is manufactured based on the design specifications.
-
Solder Paste Application: Solder paste is applied to the PCB’s pads using a stencil or screen printing process.
-
Component Placement: Electronic components are placed onto the solder paste-coated pads using automated pick-and-place machines or manual placement.
-
Reflow Soldering: The PCB with the placed components is heated in a reflow oven, melting the solder paste and creating a permanent connection between the components and the PCB.
-
Inspection and Testing: The assembled PCB undergoes visual inspection and electrical testing to ensure proper functionality and quality.
-
Rework and Repair (if necessary): If any defects or issues are identified during inspection and testing, rework and repair processes are performed to rectify them.
-
Final Assembly and Packaging: The assembled PCB is integrated into the final product or enclosure and packaged for shipment.
Here’s a table summarizing the PCB assembly process flow:
Step | Process | Description |
---|---|---|
1 | Design and Planning | PCB design finalization and assembly process planning |
2 | PCB Fabrication | Manufacturing of the bare PCB |
3 | Solder Paste Application | Application of solder paste to PCB pads |
4 | Component Placement | Placement of electronic components onto the PCB |
5 | Reflow Soldering | Melting of solder paste to create permanent connections |
6 | Inspection and Testing | Visual inspection and electrical testing for quality assurance |
7 | Rework and Repair | Rectification of any identified defects or issues |
8 | Final Assembly and Packaging | Integration of the assembled PCB into the final product and packaging for shipment |
PCB Assembly Techniques
There are several PCB assembly techniques used in the industry, each with its own advantages and applications:
1. Through-Hole Assembly (THA)
Through-hole assembly involves inserting component leads into drilled holes on the PCB and soldering them on the opposite side. This technique is suitable for larger components and provides strong mechanical connections. However, it is less space-efficient compared to surface mount assembly.
2. Surface Mount Assembly (SMT)
Surface mount assembly involves placing and soldering components directly onto the surface of the PCB. SMT allows for smaller component sizes, higher component density, and faster assembly processes. It is widely used in modern electronic devices due to its space-saving and cost-effective nature.
3. Mixed Assembly
Mixed assembly combines both through-hole and surface mount techniques on a single PCB. This approach is used when certain components are only available in through-hole packages or when specific mechanical requirements need to be met.
4. Wave Soldering
Wave soldering is a process used for through-hole assembly, where the PCB is passed over a molten solder wave, allowing the solder to fill the through-holes and create connections. This technique is efficient for high-volume production but requires careful process control to avoid defects.
5. Selective Soldering
Selective soldering is a targeted soldering process used for specific components or areas on a PCB. It involves applying solder to selected locations using specialized nozzles or laser soldering techniques. Selective soldering is useful for rework, repair, or assemblies with heat-sensitive components.
PCB Assembly Materials
Various materials are used in the PCB assembly process, each serving specific purposes:
1. PCB Substrates
PCB substrates are the base material on which the electronic components are mounted. The most common PCB substrate materials include:
- FR-4: A glass-reinforced epoxy laminate, widely used for its good electrical insulation properties and mechanical strength.
- Polyimide: A high-temperature resistant material used in applications that require stability under extreme conditions.
- Metal Core: A PCB substrate with a metal core, used for improved heat dissipation in high-power applications.
2. Solder Paste
Solder paste is a mixture of tiny solder particles and flux used for surface mount assembly. It is applied to the PCB pads before component placement and melts during the reflow soldering process to create electrical and mechanical connections.
3. Solder Wire
Solder wire is used for manual soldering processes, such as through-hole assembly or rework. It consists of a core of flux surrounded by a solder alloy, typically a combination of tin, lead, and other metals.
4. Flux
Flux is a chemical agent used to remove oxides and impurities from the surfaces to be soldered, promoting better solder wetting and adhesion. Flux can be categorized into three main types:
- Rosin Flux: A natural or synthetic resin-based flux, commonly used in electronics soldering.
- Water-Soluble Flux: A flux that can be cleaned using water after soldering, suitable for applications requiring high cleanliness.
- No-Clean Flux: A low-residue flux that does not require cleaning after soldering, minimizing the cleaning process.
PCB Assembly Quality Control
Ensuring the quality of assembled PCBs is crucial for the reliability and performance of electronic devices. One-stop PCB assembly service providers implement various quality control measures throughout the assembly process:
1. Incoming Inspection
Incoming materials, such as PCBs and components, are inspected to verify their quality and compliance with specifications before entering the assembly process.
2. Automated Optical Inspection (AOI)
AOI systems use high-resolution cameras and advanced image processing algorithms to detect assembly defects, such as missing components, incorrect component placement, or solder bridging.
3. X-Ray Inspection
X-ray inspection is used to examine solder joints and component connections that are not visible from the surface, such as ball grid array (BGA) packages or hidden vias.
4. In-Circuit Testing (ICT)
ICT involves using a bed-of-nails fixture to make electrical contact with specific points on the PCB, allowing for the testing of individual components and their interconnections.
5. Functional Testing
Functional testing verifies the overall performance and functionality of the assembled PCB, ensuring that it meets the design specifications and operates as intended.
6. Environmental Testing
Environmental testing exposes the assembled PCBs to various environmental conditions, such as temperature extremes, humidity, or vibration, to assess their durability and reliability.
Frequently Asked Questions (FAQ)
-
What is the difference between through-hole and surface mount assembly?
Through-hole assembly involves inserting component leads into drilled holes on the PCB and soldering them on the opposite side, while surface mount assembly involves placing and soldering components directly onto the surface of the PCB. Surface mount assembly allows for smaller component sizes and higher component density compared to through-hole assembly. -
How long does the PCB assembly process typically take?
The duration of the PCB assembly process depends on various factors, such as the complexity of the design, the number of components, and the chosen assembly techniques. Simple assemblies can be completed within a few days, while more complex projects may take several weeks. One-stop PCB assembly service providers can provide specific lead times based on the project requirements. -
What are the advantages of using a one-stop PCB assembly service?
One-stop PCB assembly services offer several advantages, including time and cost savings, access to expertise and advanced technology, quality assurance, scalability and flexibility, and supply chain management. By outsourcing PCB assembly to a one-stop service provider, businesses can focus on their core competencies while ensuring high-quality and efficient production. -
How can I ensure the quality of the assembled PCBs?
To ensure the quality of assembled PCBs, choose a reputable one-stop PCB assembly service provider that adheres to strict quality control measures and holds relevant certifications, such as ISO 9001 and IPC standards. The service provider should implement various quality control techniques, such as automated optical inspection, X-ray inspection, in-circuit testing, and functional testing, to identify and rectify any defects or issues. -
What information do I need to provide to a one-stop PCB assembly service provider?
To obtain a quote and initiate a PCB assembly project, you typically need to provide the following information to the service provider: - PCB design files (Gerber files, BOM, pick-and-place files)
- Bill of Materials (BOM) with component specifications and quantities
- Assembly instructions or drawings
- Quantity and delivery requirements
- Any special requirements or considerations
By providing comprehensive and accurate information, you can ensure a smooth and efficient PCB assembly process.
Conclusion
One-stop PCB assembly services have revolutionized the electronics manufacturing industry by offering businesses a comprehensive and efficient solution for their PCB assembly needs. From design to final product assembly, these service providers leverage their expertise, advanced technology, and quality control measures to deliver high-quality and reliable electronic devices.
By outsourcing PCB assembly to a one-stop service provider, businesses can benefit from time and cost savings, access to specialized knowledge and resources, and the ability to scale production according to their requirements. This allows companies to focus on their core competencies and bring innovative products to market faster.
When selecting a one-stop PCB assembly service provider, it is crucial to consider factors such as technical capabilities, quality standards, turnaround time, cost, and customer support. By partnering with a reputable and experienced service provider, businesses can ensure the success of their electronic products and maintain a competitive edge in the market.
As the electronics industry continues to evolve and demand for high-quality and efficient PCB assembly grows, one-stop PCB assembly services will play an increasingly vital role in supporting businesses of all sizes and industries. By leveraging these services, companies can navigate the complexities of PCB assembly with confidence and achieve their goals in the fast-paced world of electronics manufacturing.
No responses yet