Understanding BOM Resilience
BOM resilience refers to the ability of your Bill of Materials to withstand and adapt to various challenges and disruptions throughout the product lifecycle. A resilient BOM is characterized by its robustness, flexibility, and adaptability in the face of supply chain uncertainties, Component Obsolescence, and design changes.
The Importance of BOM Resilience
In today’s competitive and fast-paced market, having a resilient BOM is essential for several reasons:
-
Mitigating Supply Chain Risks: A resilient BOM helps mitigate the risks associated with supply chain disruptions, such as Component Shortages, lead time variations, and supplier issues. By incorporating alternative components and sourcing strategies, you can ensure a more stable and reliable supply chain.
-
Addressing Component Obsolescence: Electronic components have limited lifecycles, and obsolescence is a common challenge faced by designers and manufacturers. A resilient BOM proactively addresses obsolescence by identifying potential end-of-life components and incorporating suitable alternatives or redesign strategies.
-
Facilitating Design Changes: Throughout the product development process, design changes are inevitable. A resilient BOM allows for smoother incorporation of design changes by considering the impact on component selection, availability, and compatibility.
-
Ensuring Product Longevity: A resilient BOM contributes to the longevity and sustainability of your product. By selecting components with longer lifecycles, considering future upgrades, and planning for maintenance and repairs, you can extend the lifespan of your product and reduce the need for costly redesigns.
Strategies for Achieving BOM Resilience
Alex Sapp highlighted several key strategies for achieving BOM resilience during his AltiumLive 2022 presentation. Let’s explore these strategies in detail:
1. Thorough Component Selection
The foundation of a resilient BOM lies in thorough component selection. When choosing components for your design, consider the following factors:
-
Lifecycle Status: Select components with a longer lifecycle to minimize the risk of obsolescence. Avoid using components that are approaching end-of-life or have limited availability.
-
Multiple Sourcing: Identify components that can be sourced from multiple suppliers to reduce dependence on a single source and mitigate supply chain risks.
-
Performance and Quality: Ensure that the selected components meet the required performance and quality standards for your application. Consider factors such as temperature range, reliability, and certifications.
-
Cost and Availability: Balance cost considerations with component availability and lead times. While cost optimization is important, prioritize components with stable pricing and reliable availability.
2. Proactive Obsolescence management
Proactive obsolescence management is crucial for maintaining a resilient BOM. Implement the following practices:
-
Lifecycle Monitoring: Regularly monitor the lifecycle status of components in your BOM. Stay updated on manufacturer notifications, product change notices (PCNs), and end-of-life (EOL) announcements.
-
Obsolescence Risk Assessment: Conduct periodic risk assessments to identify components that are at high risk of obsolescence. Evaluate factors such as the manufacturer’s history, market trends, and technology advancements.
-
Proactive Mitigation: Develop proactive mitigation strategies for components identified as high-risk. This may involve securing long-term supply agreements, designing in alternative components, or initiating redesign efforts.
3. Design for Manufacturing (DFM)
Incorporating Design for Manufacturing (DFM) principles into your BOM enhances its resilience. Consider the following DFM practices:
-
Standardization: Standardize components and design practices across your product portfolio to improve manufacturing efficiency and reduce supply chain complexity.
-
Modular Design: Adopt a modular design approach to facilitate easier component replacements and upgrades. Modular designs allow for flexibility in component selection and sourcing.
-
Manufacturing Process Considerations: Collaborate with your manufacturing partners to ensure that your BOM aligns with their capabilities and processes. Consider factors such as component packaging, assembly techniques, and test requirements.
4. Supply Chain Collaboration
Effective collaboration with your supply chain partners is essential for maintaining a resilient BOM. Engage in the following practices:
-
Supplier Relationship Management: Establish strong relationships with your suppliers through regular communication, information sharing, and performance monitoring. Foster a collaborative approach to address supply chain challenges and opportunities.
-
Inventory Management: Implement robust inventory management practices to ensure an adequate supply of critical components. Consider safety stock levels, lead time variability, and demand forecasting to optimize inventory levels and mitigate supply chain risks.
-
Supplier Diversification: Diversify your supplier base to reduce dependence on a single source and mitigate geographical or geopolitical risks. Explore alternative suppliers and establish backup sources for critical components.
5. Continuous Monitoring and Improvement
Achieving BOM resilience is an ongoing process that requires continuous monitoring and improvement. Implement the following practices:
-
Regular BOM Reviews: Conduct regular BOM reviews to assess component status, identify potential risks, and evaluate the effectiveness of mitigation strategies. Involve cross-functional teams, including engineering, procurement, and manufacturing, in these reviews.
-
Performance Metrics: Establish key performance indicators (KPIs) to measure the resilience of your BOM. Track metrics such as component availability, lead time variability, and obsolescence risk to monitor the health of your BOM over time.
-
Continuous Improvement: Embrace a culture of continuous improvement by actively seeking feedback from stakeholders, implementing lessons learned, and adopting best practices. Regularly assess and refine your BOM resilience strategies based on changing market conditions and technological advancements.
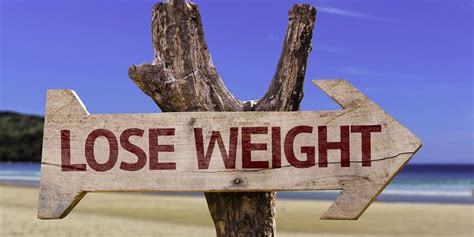
Frequently Asked Questions (FAQ)
-
Q: What are the main benefits of having a resilient BOM?
A: The main benefits of having a resilient BOM include mitigating supply chain risks, addressing component obsolescence, facilitating design changes, and ensuring product longevity. -
Q: How can I identify components at high risk of obsolescence?
A: To identify components at high risk of obsolescence, conduct regular lifecycle monitoring, stay updated on manufacturer notifications and EOL announcements, and assess factors such as the manufacturer’s history, market trends, and technology advancements. -
Q: What is the role of supply chain collaboration in achieving BOM resilience?
A: Effective supply chain collaboration is crucial for maintaining a resilient BOM. It involves establishing strong relationships with suppliers, implementing robust inventory management practices, and diversifying the supplier base to mitigate risks and ensure a stable supply of components. -
Q: How can Design for Manufacturing (DFM) principles enhance BOM resilience?
A: Incorporating DFM principles such as standardization, modular design, and manufacturing process considerations can enhance BOM resilience by improving manufacturing efficiency, facilitating component replacements and upgrades, and aligning the BOM with manufacturing capabilities. -
Q: What are some key performance indicators (KPIs) for measuring BOM resilience?
A: Key performance indicators for measuring BOM resilience include component availability, lead time variability, obsolescence risk, and supply chain disruption frequency. Tracking these metrics helps monitor the health of your BOM and identify areas for improvement.
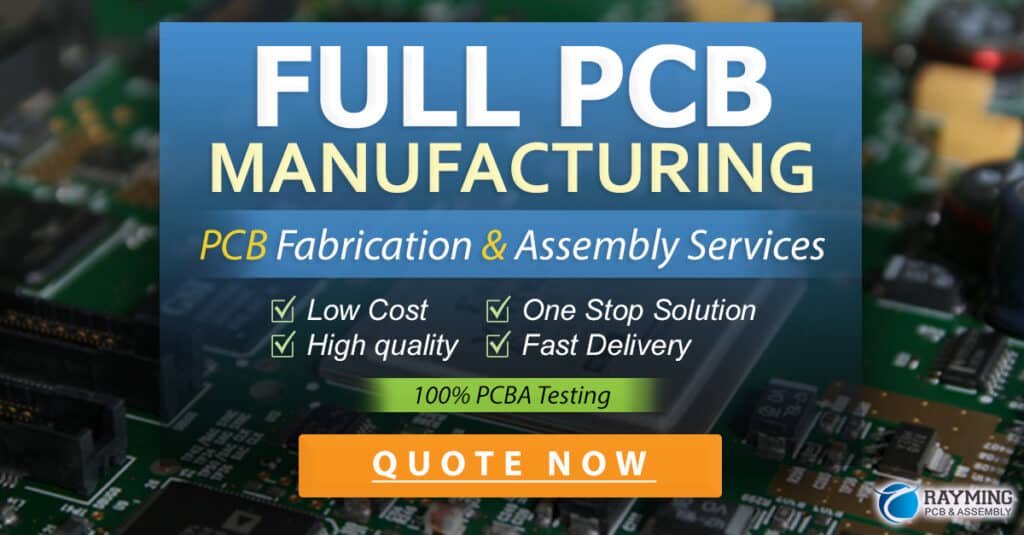
Conclusion
Achieving BOM resilience is a critical aspect of successful electronic product development and manufacturing. As highlighted by Alex Sapp at AltiumLive 2022, a resilient BOM enables you to navigate the challenges of supply chain disruptions, component obsolescence, and design changes while ensuring product longevity and sustainability.
By implementing strategies such as thorough component selection, proactive obsolescence management, Design for Manufacturing (DFM), supply chain collaboration, and continuous monitoring and improvement, you can build a robust and adaptable BOM that withstands the test of time.
Remember, BOM resilience is an ongoing journey that requires commitment, collaboration, and a proactive mindset. By embracing the insights shared by Alex Sapp and adopting industry best practices, you can position your electronic products for long-term success in an ever-changing market landscape.
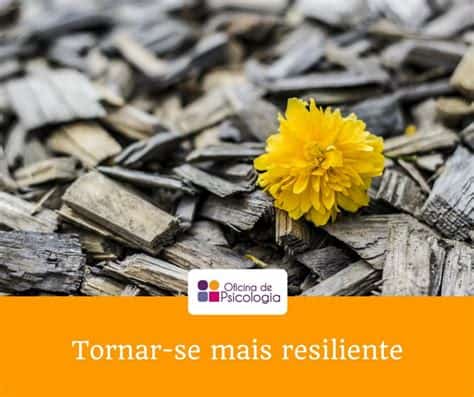
No responses yet