The Challenge of Component Obsolescence in Electronics Manufacturing
One of the biggest challenges faced by electronics manufacturers today is component obsolescence – when critical components used in PCB designs reach end-of-life (EOL) and are no longer available from suppliers. This can cause major disruptions to production, leading to costly redesigns, delays, and even the inability to continue manufacturing a product altogether.
Component obsolescence is an inevitable reality in the fast-paced world of electronics. As new technologies emerge and market demands shift, component manufacturers are constantly phasing out older parts to make way for newer, more advanced components. The typical lifecycle of an electronic component is only around 18-24 months before an updated version is released.
For OEMs and electronics manufacturers, managing component obsolescence is a never-ending battle. PCB designs often have lifespans of 5, 10 or even 20+ years, far exceeding the availability of many of the components used in the original design. When critical components become obsolete, manufacturers are faced with some difficult choices:
Option 1: Stockpile EOL Components
One approach is to purchase and stockpile a large quantity of the obsolete components before the EOL date. This allows production to continue uninterrupted in the short-term, but has some major drawbacks:
- High upfront costs to purchase EOL components in bulk
- Risk of unused inventory if demand changes
- Components degrade over time in storage
- Eventual obsolescence when stockpile runs out
Option 2: Redesign the PCB
The other main option is to redesign the PCB to use newer, available components. However, this comes with its own set of challenges:
- Costly engineering time and resources for redesign
- Requalification testing and certification
- Production delays during redesign process
- Difficulty finding pin-to-pin replacements
Neither of these options are ideal. Stockpiling EOL parts is a temporary Band-Aid solution at best, while PCB redesigns are highly disruptive and expensive. Many manufacturers end up doing a combination of both – redesigning their boards while stockpiling EOL parts to fill the gap until the new design is ready.
The High Costs of Component Obsolescence
The costs of managing obsolescence can be staggeringly high for electronics manufacturers. Some of the main obsolescence-related expenses include:
-
Redesign costs – Engineering time spent designing, prototyping, and testing replacement PCBs. Can be $50k-$200k per redesign.
-
Requalification costs – Replacement components and PCBs often need to be requalified and certified, adding more time and expense.
-
Production downtime – Delays caused by redesigns and waiting for replacement parts can halt production for weeks or months.
-
Excess and obsolete (E&O) inventory – Unusable EOL components already purchased and in stock become expensive dead weight.
-
Counterfeit part risk – Desperate manufacturers may turn to risky gray market sources for obsolete parts.
-
Diminished product quality – Substitute components may not perform as well as the original, compromising quality and reliability.
According to a study by the Ponemon Institute, the average cost of an obsolescence-related production delay is a staggering $3.6 million. For large manufacturers with multiple products, the total annual costs can easily be in the tens of millions of dollars.
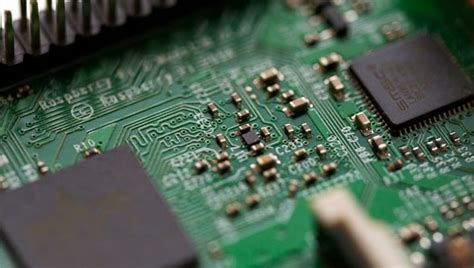
Proactive Obsolescence Management with Altium and IHS Markit
To help manufacturers get ahead of component obsolescence issues, Altium, a leading PCB design software company, has partnered with IHS Markit, a global data and analytics provider, to integrate real-time component lifecycle data into Altium Designer.
The new partnership allows PCB designers to make more informed component selections during the design process based on actual product change notifications (PCNs) and predicted obsolescence dates from over 100 leading component manufacturers.
Real-Time Component Lifecycle Data in Altium Designer
Within the Altium Designer environment, designers now have access to component lifecycle data from IHS Markit’s extensive parts database. This includes:
-
Years to End-of-Life (YTEOL) – Predicted number of years until the component will be discontinued by the manufacturer based on historical lifecycle data.
-
Product Change Notifications (PCNs) – Official notices from manufacturers about component changes, discontinuations, and estimated last time buy dates.
-
Availability – Current availability of the component from authorized distributors.
-
Alternatives – Suggested alternative components that are pin-compatible and actively stocked.
With this data integrated directly into the design environment, engineers can easily see potential long-term obsolescence risks and make design decisions to mitigate them early in the process.
Obsolescence Risk Scoring and Alerts
In addition to providing raw lifecycle data, the Altium IHS Markit integration also offers tools to help proactively manage obsolescence, including:
-
Obsolescence Risk Scoring – Each component is assigned an Obsolescence Risk Score based on its YTEOL, lifecycle stage, and other factors. High risk components are flagged.
-
BOM Risk Assessment – Entire bills of materials can be assessed for overall obsolescence risk and flagged if they contain high-risk parts.
-
Alerts and Notifications – PCB designers can sign up for email alerts when components they have used in designs have new PCNs issued or are flagged as high-risk.
By utilizing these tools, electronics manufacturers can take a much more proactive approach to obsolescence management. Catching high-risk components early in the design phase can save millions in avoided redesign costs and production delays down the road.
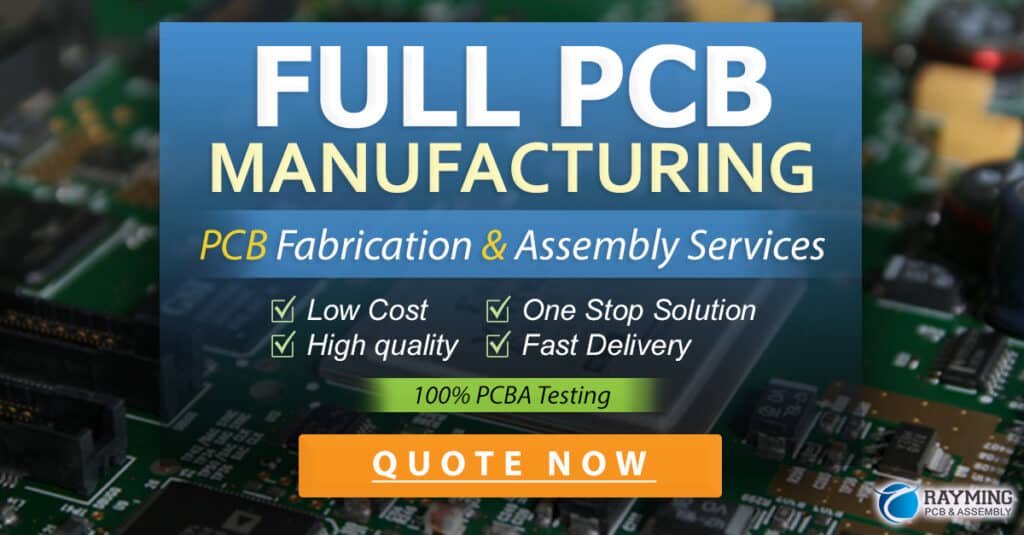
Best Practices for Proactive Obsolescence Management
In addition to using intelligent tools like those offered by Altium and IHS Markit, there are also best practices that manufacturers can adopt to minimize obsolescence disruptions:
1. Design for Obsolescence
Designing for obsolescence means making design choices that minimize the impact of component EOL events, such as:
- Using components with longer lifecycles or that are less likely to obsolete
- Choosing components that have multiple manufacturer sources
- Designing in pin-compatible alternative components from the start
- Making designs modular to allow for partial redesigns as needed
2. Monitor and Forecast Obsolescence
Actively monitoring the supply chain for PCNs and proactively forecasting component obsolescence is critical. This requires:
- Subscribing to and reviewing PCNs from component manufacturers
- Utilizing obsolescence forecasting data and tools
- Regularly assessing designs and BOMs for obsolescence risks
3. Plan and Budget for Obsolescence
Obsolescence is inevitable, so it’s important to have a plan and budget in place to deal with it when it happens. This includes:
- Allocating annual budget for obsolescence-related expenses
- Having a formal obsolescence management plan for each product
- Planning bridge buys of EOL components when necessary
- Having a PCB redesign process ready to execute
4. Work with Suppliers to Manage Obsolescence
Manufacturers should work closely with their component suppliers and distributors to manage obsolescence issues collaboratively. This can include:
- Getting early notification of EOL events from suppliers
- Working with suppliers to identify alternative components
- Negotiating last-time buys (LTBs) of EOL components
- Participating in supplier-managed inventory programs
By adopting these best practices and utilizing tools like those offered by Altium and IHS Markit, manufacturers can significantly reduce the costs and disruptions caused by component obsolescence.
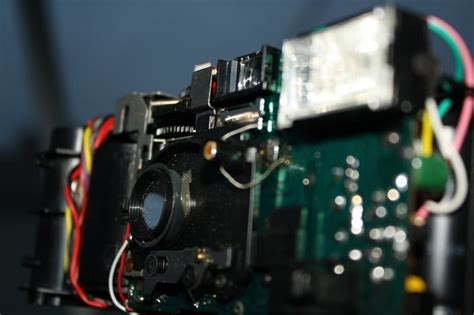
Conclusion
Component obsolescence is an unavoidable challenge in electronics manufacturing, but it doesn’t have to be a devastating one. By taking a proactive approach to obsolescence management, utilizing intelligent tools, and adopting best practices, manufacturers can minimize the impact of EOL events on their production and bottom line.
The partnership between Altium and IHS Markit to integrate real-time component lifecycle data into the PCB design process is a major step forward in the fight against obsolescence. By empowering engineers to make informed decisions and avoid high-risk components from the start, this integration can help manufacturers avoid millions in redesign costs and delays.
As the electronics industry continues to evolve at a rapid pace, effective obsolescence management will only become more important. Manufacturers that prioritize and invest in proactive obsolescence management will be well-positioned to navigate these challenges and thrive in the years to come.
Frequently Asked Questions
What is component obsolescence?
Component obsolescence is when a component used in a PCB design reaches its end-of-life (EOL) and is no longer being manufactured or sold by suppliers. This can happen when manufacturers discontinue older components to focus on newer technologies.
Why is component obsolescence such a big problem in electronics manufacturing?
Obsolescence is a major problem because the lifespan of a typical electronic component (18-24 months) is much shorter than the lifespan of the products they are used in (5-20+ years). When critical components become obsolete, manufacturers are forced to either stockpile the EOL parts or redesign their products, both of which are costly and disruptive.
How does the Altium IHS Markit partnership help with obsolescence?
The partnership integrates real-time component lifecycle data from IHS Markit into the Altium Designer PCB design environment. This allows engineers to see obsolescence risk scores, predicted years to EOL, and PCN alerts for components during the design process. They can then make informed decisions to avoid high-risk components and design for obsolescence.
What are some best practices for managing component obsolescence?
Some best practices include designing for obsolescence by choosing lower risk components, actively monitoring and forecasting obsolescence, planning and budgeting for obsolescence-related costs, and working closely with component suppliers to manage EOL events.
How much can component obsolescence cost manufacturers?
The costs of obsolescence can be very high, including expenses for PCB redesigns, requalification, production downtime, excess and obsolete inventory, and more. According to one study, the average cost of an obsolescence-related production delay is $3.6 million. For large manufacturers, the annual costs can easily reach tens of millions of dollars.
No responses yet