What is Design for Manufacturability (DFM)?
Design for Manufacturability (DFM) is a design approach that focuses on creating products that are easy to manufacture, assemble, and test. The primary goal of DFM is to minimize production costs, improve product quality, and reduce time-to-market by identifying and addressing potential manufacturing issues early in the design process. By considering manufacturing constraints and requirements during the design phase, engineers can create designs that are optimized for production, resulting in fewer manufacturing defects, reduced material waste, and improved overall efficiency.
The Importance of DFM Tools
DFM tools are software applications that help engineers and designers analyze and optimize their designs for manufacturability. These tools provide a range of features and functionalities that enable users to identify potential manufacturing issues, evaluate design alternatives, and make informed decisions to improve the manufacturability of their products. Some of the key benefits of using DFM tools include:
- Early identification of manufacturing issues
- Reduced production costs
- Improved product quality
- Faster time-to-market
- Enhanced collaboration between design and manufacturing teams
By leveraging DFM tools, companies can streamline their product development process, minimize the risk of manufacturing defects, and ultimately deliver high-quality products to their customers more efficiently.
Types of DFM Tools
There are various types of DFM tools available in the market, each designed to address specific aspects of the product design and manufacturing process. Some of the most common types of DFM tools include:
1. CAD-Integrated DFM Tools
CAD-integrated DFM tools are software applications that are integrated with popular computer-aided design (CAD) platforms, such as SolidWorks, Autodesk Inventor, and PTC Creo. These tools allow engineers to analyze their designs directly within the CAD environment, providing real-time feedback on potential manufacturing issues. CAD-integrated DFM tools typically offer features such as:
- Design rule checks
- Material selection guidance
- Tolerance analysis
- Moldflow analysis
- Cost estimation
Examples of CAD-integrated DFM tools include:
- SolidWorks DFMXpress
- Autodesk DFM Advisor
- PTC Creo DFM Advisor
2. Standalone DFM Tools
Standalone DFM tools are independent software applications that are not integrated with specific CAD platforms. These tools offer a more comprehensive set of features and functionalities compared to CAD-integrated tools, and can often handle a wider range of file formats. Standalone DFM tools are particularly useful for companies that work with multiple CAD platforms or need to analyze designs created by external partners or suppliers. Key features of standalone DFM tools include:
- Design rule checks
- Manufacturability analysis
- Assembly analysis
- Cost estimation
- Reporting and collaboration
Examples of standalone DFM tools include:
- DFMPro
- DFMA Software
- Geometric DFMPro
3. Cloud-Based DFM Tools
Cloud-based DFM tools are web-based applications that allow users to access DFM functionality through a web browser, without the need for local software installation. These tools offer the benefits of scalability, accessibility, and collaboration, as multiple users can access and work on the same project simultaneously from different locations. Cloud-based DFM tools often provide features such as:
- Design rule checks
- Manufacturability analysis
- Cost estimation
- Real-time collaboration
- Version control
Examples of cloud-based DFM tools include:
- 3DX DFM
- Quotient DesignRule
- CASTOR
4. Specialty DFM Tools
Specialty DFM tools are software applications designed to address specific manufacturing processes or industries. These tools offer tailored features and functionalities that cater to the unique requirements of particular manufacturing methods or product types. Examples of specialty DFM tools include:
- DFM tools for injection molding
- DFM tools for Sheet Metal Fabrication
- DFM tools for PCB Design
- DFM tools for additive manufacturing
Examples of specialty DFM tools include:
- Moldex3D
- AutoForm
- Valor NPI
- Materialise Magics
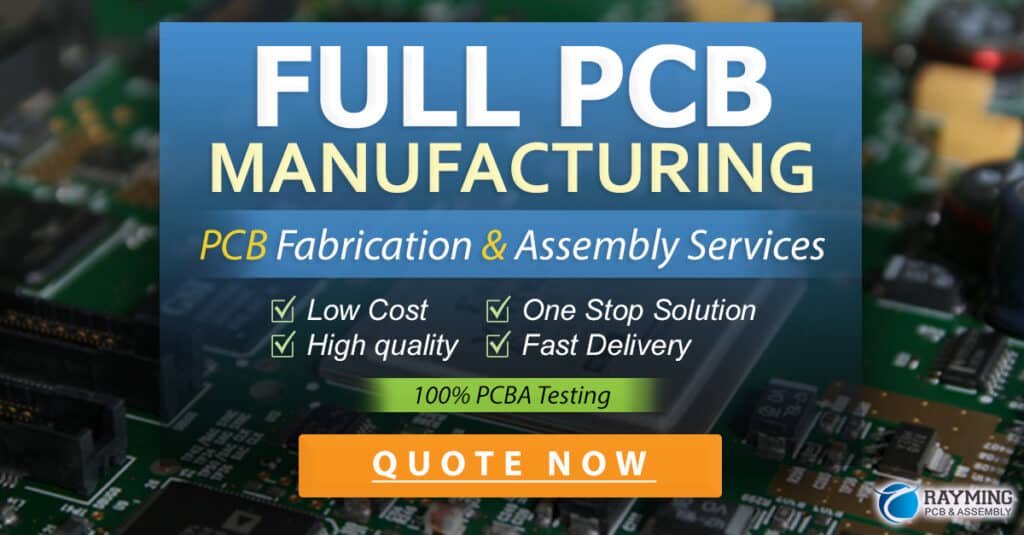
Comparing DFM Tools
When selecting a DFM tool for your product design and manufacturing needs, it’s important to consider factors such as:
- Compatibility with your existing CAD platform
- Ease of use and learning curve
- Range of features and functionalities
- Integration with other software tools
- Cost and licensing options
- Customer support and training resources
To help you compare the various DFM tools available, we’ve created a table that highlights some of the key features and characteristics of popular DFM tools:
DFM Tool | Type | Key Features | CAD Compatibility | Cost |
---|---|---|---|---|
SolidWorks DFMXpress | CAD-Integrated | Design rule checks, material selection, cost estimation | SolidWorks | Included with SolidWorks Professional and Premium |
Autodesk DFM Advisor | CAD-Integrated | Design rule checks, manufacturability analysis, cost estimation | Autodesk Inventor, AutoCAD | Subscription-based |
PTC Creo DFM Advisor | CAD-Integrated | Design rule checks, tolerance analysis, moldflow analysis | PTC Creo | Included with PTC Creo Advanced Assembly Extension |
DFMPro | Standalone | Design rule checks, manufacturability analysis, cost estimation | Multiple CAD formats | Perpetual license or subscription-based |
DFMA Software | Standalone | Design for assembly, design for manufacturing, cost estimation | Multiple CAD formats | Perpetual license |
3DX DFM | Cloud-Based | Design rule checks, manufacturability analysis, real-time collaboration | Multiple CAD formats | Subscription-based |
Moldex3D | Specialty (Injection Molding) | Moldflow analysis, warpage prediction, cooling optimization | Multiple CAD formats | Perpetual license or subscription-based |
Implementing DFM Tools in Your Product Development Process
To effectively implement DFM tools in your product development process, consider the following best practices:
- Identify your specific DFM requirements based on your product types, manufacturing processes, and design challenges.
- Evaluate multiple DFM tools to find the best fit for your needs, considering factors such as compatibility, features, ease of use, and cost.
- Provide adequate training and support for your design and manufacturing teams to ensure they can effectively use the selected DFM tools.
- Integrate DFM analysis into your product development workflow, ideally starting from the early design stages.
- Establish clear guidelines and standards for DFM analysis, including design rules, material selection, and tolerancing.
- Encourage collaboration between design and manufacturing teams to ensure that DFM insights are effectively communicated and incorporated into the final product design.
- Continuously monitor and evaluate the effectiveness of your DFM tools and processes, and make adjustments as needed to optimize results.
By following these best practices and leveraging the right DFM tools for your needs, you can significantly improve the manufacturability, quality, and cost-effectiveness of your products.
Frequently Asked Questions (FAQ)
-
What is the difference between CAD-integrated and standalone DFM tools?
CAD-integrated DFM tools are software applications that are built into specific CAD platforms, allowing engineers to analyze their designs directly within the CAD environment. Standalone DFM tools, on the other hand, are independent software applications that can work with multiple CAD formats and offer a more comprehensive set of features and functionalities. -
How can DFM tools help reduce production costs?
DFM tools help reduce production costs by identifying potential manufacturing issues early in the design process, allowing engineers to make necessary design changes before committing to expensive tooling and production. By optimizing designs for manufacturability, DFM tools can also help minimize material waste, reduce assembly time, and improve overall production efficiency. -
Are cloud-based DFM tools secure?
Cloud-based DFM tool providers typically employ robust security measures to protect user data, such as encrypted data storage, secure data transmission, and regular security audits. However, it’s important to carefully review the security policies and practices of any cloud-based DFM tool provider before entrusting them with sensitive design data. -
Can DFM tools be used for additive manufacturing (3D printing)?
Yes, there are specialty DFM tools designed specifically for additive manufacturing processes. These tools help engineers optimize their designs for 3D printing, taking into account factors such as material properties, support structures, and print orientation to ensure high-quality, cost-effective parts. -
How do I choose the right DFM tool for my company?
When choosing a DFM tool for your company, consider factors such as compatibility with your existing CAD platform, the specific manufacturing processes and product types you work with, the ease of use and learning curve for your team, and the cost and licensing options. It’s also a good idea to evaluate multiple DFM tools through free trials or demos to determine which one best meets your needs.
Conclusion
DFM tools are essential for optimizing product designs, reducing manufacturing costs, and improving overall production efficiency. With a wide range of DFM tools available, from CAD-integrated and standalone applications to cloud-based and specialty tools, companies have the flexibility to choose the best solution for their specific needs. By implementing DFM tools and best practices in their product development process, businesses can create high-quality, cost-effective products that meet the demands of today’s competitive market.
To make the most of DFM tools, it’s important to carefully evaluate your options, provide adequate training and support for your team, and continuously monitor and refine your DFM processes. By embracing DFM as an integral part of your product development strategy, you can drive innovation, reduce time-to-market, and ultimately achieve greater success in your industry.
No responses yet