Introduction to RF PCB Design
Radio Frequency (RF) PCB design is a specialized area of printed circuit board design that focuses on the layout and construction of boards for high-frequency applications. RF PCBs are used in a wide range of applications, including wireless communication devices, radar systems, and medical equipment.
Designing an RF PCB requires a deep understanding of the unique challenges posed by high-frequency signals. These challenges include signal integrity, electromagnetic interference (EMI), and power dissipation. In this ultimate guide, we will explore the key concepts and best practices for RF PCB Design.
The Basics of RF PCB Design
What is RF PCB Design?
RF PCB design is the process of designing a printed circuit board that can effectively handle high-frequency signals. RF PCBs are used in applications where the signal frequency is typically above 100 MHz. At these high frequencies, the behavior of the signal becomes more complex, and the design of the PCB must take into account factors such as impedance matching, signal reflection, and crosstalk.
Why is RF PCB Design Important?
RF PCB design is critical for ensuring the proper functioning of high-frequency electronic devices. Poor RF PCB design can lead to a range of problems, including:
- Signal distortion and loss
- Electromagnetic interference (EMI)
- Reduced device performance and reliability
- Increased power consumption and heat generation
By following best practices for RF PCB design, engineers can minimize these issues and ensure that their devices perform optimally.
Key Considerations for RF PCB Design
Substrate Material Selection
The choice of substrate material is critical for RF PCB design. The substrate must have a low dielectric constant and low loss tangent to minimize signal loss and distortion. Common substrate materials for RF PCBs include:
- FR-4: A low-cost, widely used substrate material suitable for frequencies up to 2 GHz.
- Rogers: A high-performance substrate material with excellent electrical properties, suitable for frequencies up to 77 GHz.
- Teflon: A low-loss substrate material with a very low dielectric constant, suitable for frequencies up to 100 GHz.
Copper Weight and Thickness
The weight and thickness of the copper traces on an RF PCB can have a significant impact on signal integrity. Thicker copper traces have lower resistance and can carry more current, but they also have higher capacitance and can cause signal reflections. Thinner copper traces have higher resistance but lower capacitance.
The optimal copper weight and thickness will depend on the specific application and frequency range of the RF PCB. Common copper weights for RF PCBs include 0.5 oz, 1 oz, and 2 oz.
Trace Width and Spacing
The width and spacing of the traces on an RF PCB must be carefully designed to ensure proper impedance matching and minimize crosstalk. The characteristic impedance of a trace is determined by its width, thickness, and the dielectric constant of the substrate material.
To minimize crosstalk, traces should be spaced far enough apart to avoid coupling. The exact spacing required will depend on the frequency and power level of the signals.
Grounding and Shielding
Proper grounding and shielding are essential for minimizing EMI and ensuring signal integrity in RF PCBs. Ground planes should be used to provide a low-impedance return path for high-frequency currents. Shielding can be used to isolate sensitive circuits from external EMI sources.
There are several techniques for grounding and shielding in RF PCB design, including:
- Split ground planes: Separating the ground plane into multiple sections to isolate different parts of the circuit.
- Via stitching: Adding vias along the edges of the board to provide a low-impedance connection between the top and bottom ground planes.
- Faraday cages: Enclosing sensitive circuits in a metal shield to block external EMI.
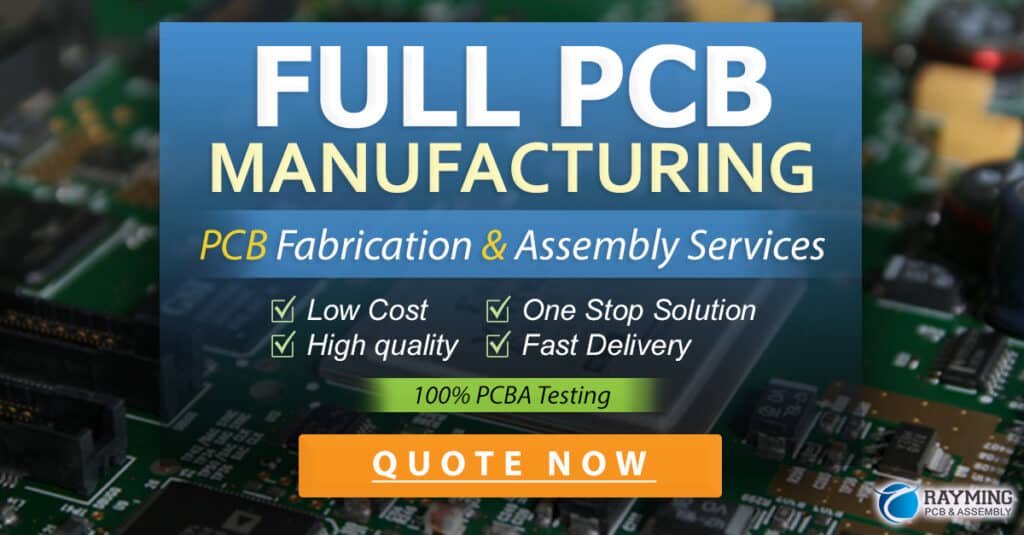
RF PCB Layout Techniques
Component Placement
The placement of components on an RF PCB is critical for minimizing signal reflections and ensuring proper impedance matching. Components should be placed as close together as possible to minimize trace lengths and reduce signal loss.
Passive components, such as resistors and capacitors, should be placed close to the active components they are associated with. Decoupling capacitors should be placed as close as possible to the power pins of active components to minimize power supply noise.
Trace Routing
The routing of traces on an RF PCB must be done carefully to minimize signal reflections and crosstalk. Traces should be kept as short and straight as possible, with minimal bends and corners. Bends should be made at 45-degree angles to minimize reflections.
Traces should also be routed away from each other to minimize crosstalk. The spacing between traces should be at least three times the trace width to ensure adequate isolation.
Impedance Matching
Impedance matching is critical for ensuring maximum power transfer and minimizing signal reflections in RF PCBs. The impedance of the source, transmission line, and load must all be matched to ensure efficient power transfer.
There are several techniques for impedance matching in RF PCB design, including:
- Stub matching: Adding a short trace (stub) to the transmission line to match the impedance.
- Tapered matching: Gradually changing the width of the trace to match the impedance.
- Resistive matching: Adding a resistor in series or parallel with the load to match the impedance.
Testing and Verification
S-Parameters
S-parameters are a set of measurements used to characterize the performance of an RF PCB. S-parameters measure the reflection and transmission of signals at the ports of the PCB.
The four S-parameters are:
- S11: Input reflection coefficient
- S12: Reverse transmission coefficient
- S21: Forward transmission coefficient
- S22: Output reflection coefficient
S-parameters can be measured using a vector network analyzer (VNA) and used to optimize the design of the RF PCB.
Time-Domain Reflectometry (TDR)
Time-domain reflectometry (TDR) is a technique used to measure the impedance of a transmission line as a function of time. TDR works by sending a short pulse down the transmission line and measuring the reflections that occur at impedance discontinuities.
TDR can be used to identify impedance mismatches and other issues in an RF PCB. By analyzing the TDR Measurements, engineers can optimize the design of the PCB to minimize reflections and ensure proper impedance matching.
Common RF PCB Design Mistakes to Avoid
Inadequate Grounding
Inadequate grounding is one of the most common mistakes in RF PCB design. Poor grounding can lead to signal integrity issues, EMI, and other problems.
To avoid grounding issues, designers should:
- Use a solid ground plane that covers the entire PCB.
- Connect all ground points to the ground plane using vias.
- Avoid splitting the ground plane unless absolutely necessary.
Incorrect Trace Impedance
Incorrect trace impedance is another common mistake in RF PCB design. If the impedance of the traces does not match the impedance of the source and load, signal reflections and power loss can occur.
To avoid impedance issues, designers should:
- Calculate the required trace width and spacing for the desired impedance.
- Use a controlled impedance process to ensure consistent trace impedance across the PCB.
- Verify the impedance of the traces using TDR measurements.
Inadequate Shielding
Inadequate shielding can lead to EMI issues and signal integrity problems in RF PCBs. Without proper shielding, external EMI sources can couple into the PCB and cause interference.
To avoid shielding issues, designers should:
- Use shielding cans or Faraday cages to enclose sensitive circuits.
- Use via stitching along the edges of the PCB to provide a low-impedance connection between the top and bottom ground planes.
- Use shielded connectors and cables to prevent EMI from entering or leaving the PCB.
RF PCB Design Tools
There are several tools available for RF PCB design, ranging from simple schematic capture and layout tools to advanced electromagnetic simulation software. Some of the most popular RF PCB design tools include:
- Altium Designer: A comprehensive PCB design tool that includes schematic capture, layout, and simulation capabilities.
- Ansys HFSS: A high-frequency electromagnetic simulation tool used for analyzing the performance of RF and microwave devices.
- Cadence AWR: A suite of tools for designing and simulating RF and microwave circuits, including schematic capture, layout, and electromagnetic simulation.
- Mentor Graphics HyperLynx: A signal integrity analysis tool used for simulating the performance of high-speed digital and RF circuits.
Tool | Schematic Capture | Layout | Simulation |
---|---|---|---|
Altium Designer | Yes | Yes | Yes |
Ansys HFSS | No | No | Yes |
Cadence AWR | Yes | Yes | Yes |
Mentor Graphics HyperLynx | No | No | Yes |
Frequently Asked Questions (FAQ)
What is the difference between RF PCB design and regular PCB design?
RF PCB design is a specialized area of PCB design that focuses on the layout and construction of boards for high-frequency applications. RF PCBs must be designed to handle the unique challenges posed by high-frequency signals, such as signal integrity, EMI, and power dissipation. Regular PCB design, on the other hand, focuses on the layout and construction of boards for low-frequency applications.
What is the best substrate material for RF PCBs?
The best substrate material for RF PCBs depends on the specific application and frequency range. For frequencies up to 2 GHz, FR-4 is a low-cost, widely used substrate material. For frequencies up to 77 GHz, Rogers is a high-performance substrate material with excellent electrical properties. For frequencies up to 100 GHz, Teflon is a low-loss substrate material with a very low dielectric constant.
How can I minimize EMI in my RF PCB design?
There are several techniques for minimizing EMI in RF PCB design, including:
- Using a solid ground plane that covers the entire PCB.
- Using via stitching along the edges of the PCB to provide a low-impedance connection between the top and bottom ground planes.
- Using shielding cans or Faraday cages to enclose sensitive circuits.
- Using shielded connectors and cables to prevent EMI from entering or leaving the PCB.
What is the purpose of impedance matching in RF PCB design?
Impedance matching is critical for ensuring maximum power transfer and minimizing signal reflections in RF PCBs. If the impedance of the source, transmission line, and load are not matched, signal reflections and power loss can occur. By matching the impedance of the traces to the impedance of the source and load, designers can ensure efficient power transfer and minimize signal distortion.
What are some common mistakes to avoid in RF PCB design?
Some common mistakes to avoid in RF PCB design include:
- Inadequate grounding, which can lead to signal integrity issues and EMI.
- Incorrect trace impedance, which can cause signal reflections and power loss.
- Inadequate shielding, which can allow external EMI sources to couple into the PCB and cause interference.
- Poor component placement, which can lead to signal reflections and crosstalk.
- Incorrect trace routing, which can cause signal distortion and loss.
Conclusion
RF PCB design is a complex and challenging area of PCB design that requires a deep understanding of the unique challenges posed by high-frequency signals. By following best practices for RF PCB design, such as proper substrate material selection, trace impedance matching, and adequate grounding and shielding, designers can ensure that their boards perform optimally and meet the requirements of their specific application.
While RF PCB design can be intimidating for those new to the field, there are many resources available to help designers get started. From online tutorials and courses to advanced simulation tools and professional design services, there are many ways to learn and apply the principles of RF PCB design.
Ultimately, the key to successful RF PCB design is a combination of technical knowledge, practical experience, and attention to detail. By understanding the fundamentals of RF PCB design and applying them carefully and systematically, designers can create high-performance, reliable PCBs that meet the demands of even the most challenging high-frequency applications.
No responses yet